The price of a CNC press brake is often a significant consideration for businesses looking to invest in metal fabrication equipment. From small workshops to large manufacturing plants, understanding why CNC press brake prices tend to be higher compared to conventional press brakes is essential for making informed purchasing decisions.
https://www.youtube.com/watch?v=huajhtWq3iE&t=263s
Understanding CNC Press Brake
A CNC press brake machine is a common press brake that incorporates a CNC (Computer Numerically Controlled) system. The CNC system enables the machine to bend and handle metal sheets as short as a few millimetres and as long as a few metres.
A CNC press brake machine’s structure might be of two varieties. They are as follows:
Type 1 (Down Forming): It is made up of a fixed bed (bottom) with a v-shaped tool attached to it. The impact is received by a top beam (also v-shaped), which presses the metal against the v-shaped tool.
Type 2 (Up Forming): This CNC press brake has the same components as type 1. However, in this case, the top piece is fixed, whereas the lower portion moves.
Whatever the type, the final effect will be the same, with no constraints on the shape and design. Now that we’ve defined what a CNC press brake machine is, we’ll look at how it works.
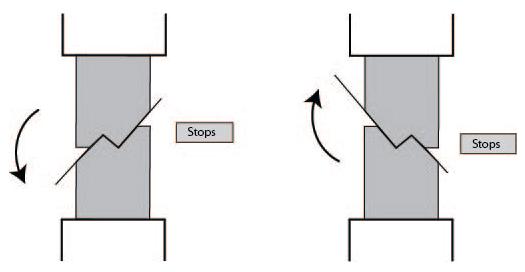
How Does CNC Press Brake Work
A CNC press brake operates through the utilization of a hydraulic or electrical system, enhanced with AI programming, facilitating precise and accurate bending of raw materials. Its operation follows a standardized procedure.
Initiating the process involves inputting detailed product specifications into the CNC press brake machine, ensuring precise bend angles and other necessary parameters. Once the instructions are analyzed and comprehended, the computer takes charge, orchestrating the machine's operations.
Depending on whether the press brake is hydraulic or electric, it harnesses hydraulic or electric force to exert pressure on the appropriate moving part, tailored to its specific type (type 1 or type 2). This action enables the moving component to apply force to the metal sheet, causing it to bend against the fixed component, achieving the desired result.
In the case of CNC machines, the metal sheet is manipulated in accordance with the computer's instructions, ensuring meticulous execution and reliability in the final product.
To accommodate diverse shapes, operators have the flexibility to alternate between a V-shaped tool, known as a die (affixed to the fixed part), and a blade (attached to the moving part). Various tool sets are available in the market to cater to this requirement.
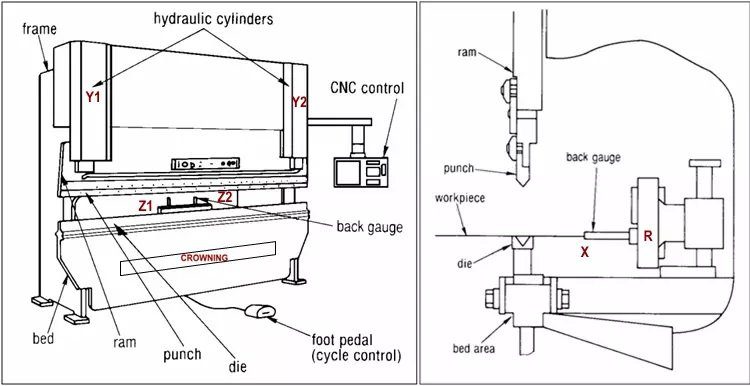
Advantages of Using A CNC Press Brake
As technology advances, ancient tools are evolving into powerful and reliable assets tailored for the modern era, and CNC Press Brake Machines are a prime example. The superiority of modern CNC Press Brake Machines over traditional ones stems from various reasons, a few of which are highlighted below:
Enhanced Efficiency and Precision
Unlike their manual predecessors, traditional CNC Press Brake Machines operated with room for errors. However, CNC Press Brake Machines leave no margin for error. Fully automated, they eliminate the need for human intervention, ensuring smoother operations and a streamlined workflow, thus boosting efficiency and productivity.
Moreover, CNC systems deliver exceptionally precise results compared to older models, yielding faster outcomes, double the precision, and superior quality work. This advancement significantly enhances both efficiency and precision. Additionally, the operation and control of CNC Press Brake Machines are remarkably user-friendly.
Cost-Effectiveness
Traditional press brake machines incurred various expenses, contributing to higher overall costs. For instance, they often ran continuously throughout the day, regardless of actual usage, leading to unnecessary energy consumption. Moreover, the maintenance and upkeep of traditional press brake machines were considerably costlier.
In contrast, CNC Press Brake Machines offer a more economical solution. They require minimal maintenance, generate less waste, and are equipped with high-quality components and readily available parts in case of breakdowns. This cost-effective nature makes CNC Press Brake Machines a preferred choice for modern manufacturing operations.
Versatility and Wide Range of Use
One of the most significant advantages of press brakes is their versatility. They can be used to create a wide range of bends, angles, and shapes in sheet metal, from simple bends to complex geometries. This makes them an excellent choice for a variety of applications, from metalworking to manufacturing. And can be applied into diverse scenes.
Meeting Diverse Standards: Precision and Accuracy Requirements
- Advanced CNC Controls for High Precision
These machines are equipped with cutting-edge Computer Numerical Control (CNC) systems, offering exceptional precision and accuracy in bending operations. CNC controls allow for intricate programming and highly detailed adjustments, ensuring consistent and precise bends even on complex workpieces. They are well-suited for industries or tasks that demand extremely tight tolerances and exacting specifications, such as aerospace or specialized engineering projects.
- Moderate Precision for General Manufacturing
These press brakes cater to general manufacturing needs where a high level of precision isn’t a critical requirement. While they still maintain a reasonable level of accuracy, they might lack the advanced features and intricate control offered by CNC systems. These machines are suitable for applications in industries where exacting precision isn’t as crucial, such as certain types of fabrication, automotive manufacturing, or general metalworking tasks.
Industry Application
Automotive Industry
Hydraulic press brakes are extensively utilized in the automotive sector for bending and shaping metal sheets and plates to create various vehicle components. These machines play a pivotal role in manufacturing car body parts, chassis structures, doors, hoods, and more, ensuring metal parts conform to specific shapes and size requirements.
Aerospace Industry
In the aerospace field, hydraulic press brakes are employed to fabricate aircraft components such as fuselages, wings, and other structural elements. These machines require high precision and control to meet the stringent requirements of aerospace engineering, ensuring the quality and performance of aircraft components..
Shipbuilding
Within shipbuilding, hydraulic press brakes are used to bend and shape metal sheets for constructing ship hulls. These machines handle large-sized and thick metal plates, manufacturing components and structures to ensure the strength and stability of ships.
Architectural Metalwork
In the construction industry, hydraulic press brakes are utilized to produce metal components for building structures and decorative elements such as beams, columns, handrails, balustrades, and more. They provide specific shapes and design requirements for architectural metalwork.
General Manufacturing
Hydraulic press brakes find wide application across various general manufacturing sectors for producing an array of metal parts and components. This includes the production of household appliances, electronic devices, mechanical parts, and other products requiring metal fabrication processes.
Reasons Why CNC Press Brake Is Higher
EfficiencyCNC press brakes can create around 900 bends per hour, compared to 600 bends per hour for older machines.Setup timeCNC press brakes have faster setup times because the controller calculates the ram and backgage, checks for mistakes, and determines the correct bend sequence.AccuracyCNC press brakes can achieve positioning accuracies within a few thousandths of an inch, and repeatability can also be very high.AutomationCNC press brakes automate the process by feeding orders into a program, with little human intervention required.SimplicityCNC press brakes are simpler to install and use, which speeds up manufacturing.
Advantages of CNC press brake Over NC press brake
The main differences between CNC Press Brake and NC Press Brake are controllers, control methods and the number of control axes.Above points result in different functionality and final angular accuracy during the bending process.
CNC Press Brake Machines have more advanced controllers that allow for complex bending and more functionality.
CNC control is by proportional valve directly control the oil cylinders, By the grating ruler positioning, can be closed loop control, NC by AC motor or Servo motor control cylinder, limit switch set up and down stop.
CNC can control more axes, NC can control fewer axes.
So it is not difficult to understand why the price of CNC press brake is higher. CNC Press Brake is characterized by complex and efficient bending, which requires workers with certain operating experience.
CNC Press Brake is a sheet bending machine with more advanced functions. It includes WE67K, WF67K, MB8 series.
CNC Press Brake is based on proportional valve and grating ruler to built closed-loop control method.
The machine runs stably, the repetition positioning accuracy is within 0.02mm, excellent synchronization performance and bending accuracy;
CNC controller realizes 2D and 3D simulation to ensure that complex shapes of bending are fully taken into account, providing the most optimal programming solution, greatly improving production efficiency and workpiece quality.
CNC Press Brake analyzes the machine's operating status thanks to the control system's powerful algorithms, allowing precise adjustment of each machine parameter, leaving room for improvement in the bending machine's performance.
The continuous innovation in CNC system technology has also allowed the CNC Press Brake to be used for a wide range of applications, such as bending cell centers, which can be coordinated with robots.
Advanced CNC system also provides safety, Laser Protection, Light Curtain; Angle Check, Laser Check; sheet follow devices, etc.
The CNC controllers offer multiple languages and DXF file input with a high degree of intelligence.
These features will play an important role in the real working and really help the sheet metal bending work.
How To Choose A Right CNC Press Brake
When most users purchase a bending machine, the first thing they consider is the price. Price is very important, but it does not mean that the more expensive it is, the better it is, and that cheaper is bad. In addition to price, you also need to consider the following aspects:
Define your requirements: Determine the types of materials you will be bending, the thicknesses of those materials, the required bending length, and the complexity of the bends. This will help you identify the necessary tonnage capacity, bending length, and tooling requirements for the press brake.
Consider accuracy and precision: Evaluate the accuracy and repeatability of the CNC press brake, as well as its control system. Look for features such as advanced back gauge systems, crowning systems for maintaining bend accuracy across the length of the machine, and user-friendly CNC controls for precise programming and operation.
Assess the machine's speed: Consider the production requirements of your operation and choose a press brake with a bending speed that aligns with your needs. Faster bending speeds can improve productivity, but be sure to balance speed with accuracy and quality.
Evaluate tooling options: Look for a press brake that offers a wide range of tooling options to accommodate different bending applications. Consider the availability and cost of tooling, as well as the ease of tool changes and setup.
Consider the machine's footprint: Evaluate the available space in your facility and choose a press brake that fits within your layout constraints. Consider the layout of your production area, material flow, and access for maintenance and tooling changes.
Assess the reliability and support: Research the reputation of the manufacturer and the reliability of the CNC press brake. Look for a manufacturer with a track record of producing high-quality, reliable machines and providing excellent customer support, including training, service, and spare parts availability.
Think about future needs: Anticipate any future changes in your production requirements and choose a CNC press brake that can adapt to evolving needs. Consider factors such as scalability, upgradeability, and compatibility with other equipment or software in your operation.
Conclusion
In conclusion, while the initial price of a CNC press brake may be higher compared to manual or non-CNC alternatives, the investment is often well worth it for several reasons. CNC press brakes offer unparalleled accuracy, precision, and repeatability, leading to higher quality finished products and reduced scrap rates. Their advanced control systems and automation capabilities improve productivity and efficiency, allowing for faster setup times and increased throughput.
Additionally, CNC press brakes require less operator skill and experience, reducing the risk of errors and ensuring consistent results even with complex bending operations. When considering the long-term benefits of improved quality, productivity, and operational flexibility, the CNC press brake becomes justified as a smart investment in the future success of your manufacturing operation.