In the world of metalworking, precision and efficiency are paramount. With various machines available for bending and shaping metal, understanding the differences between them can be crucial. Two commonly confused terms are press brake vs brake press. This article aims to clarify the distinction between these terms, helping you make informed decisions for your manufacturing needs.
Press Brake vs Brake Press: How To Distinguish
Press brakes are machines used to bend sheet and plate material, primarily sheet metal, by clamping the workpiece between a matching punch and die. The customization of the punch and die setup allows for a wide range of bends to be executed, making the press brake a versatile tool in the metalworking industry. They are known for their accuracy and ability to produce repetitive, high-precision bends.
Brake presses, on the other hand, may refer to the same press brake equipment or, in some contexts, to simpler, manual brake machines that are operated by hand. These manual machines are typically less complex and are used for straightforward bending operations where precision is important but does not need to be at the same high level as what is achievable with a powered press brake.
What Is A Press Brake
A press brake is a machine used for bending sheet and plate material, most commonly sheet metal. It forms predetermined bends by clamping the workpiece between a matching punch and die. Press brakes are essential in various industries, including automotive, aerospace, and construction, due to their ability to create precise bends and angles.
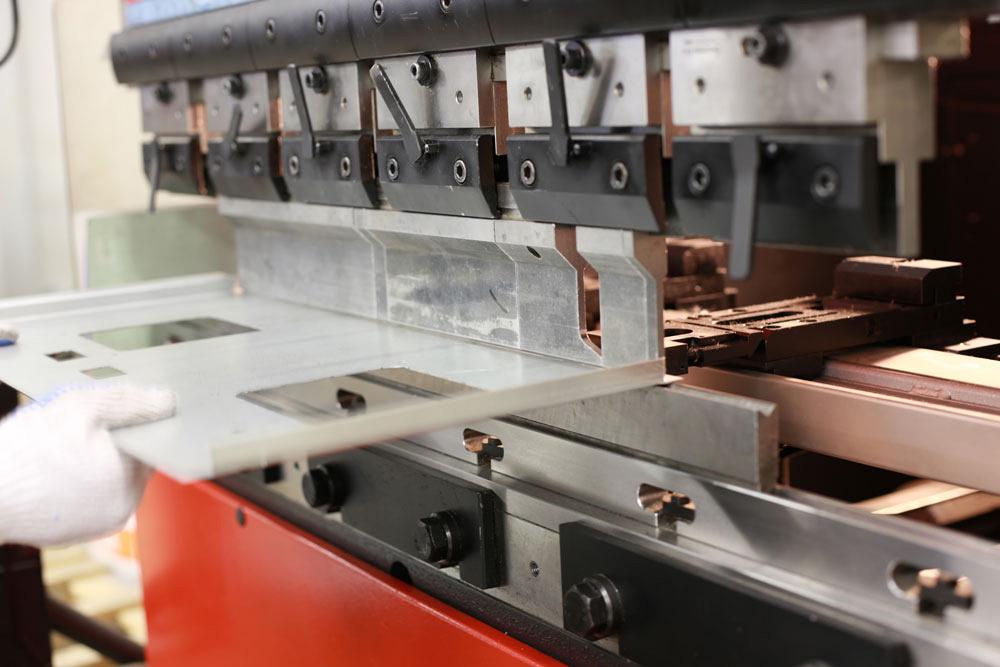
What Is A Brake Press
A brake press, often used interchangeably with press brake, refers to the same type of machine. However, in some contexts, "brake press" may emphasize different aspects or functionalities of the machine. Essentially, both terms describe a device designed to bend metal, though nuances in regional usage or specific applications might exist.
Key Differences: Press Brake vs Brake Press
1.Terminology and Usage
While "press brake" and "brake press" can be used interchangeably, regional preferences or industry-specific jargon might influence their usage. In some regions, "press brake" is the preferred term, while "brake press" might be more common in others. Understanding these nuances can help in effective communication within the industry.
2.Technical Differences
Technically, the differences might be minimal, but the focus can vary:
- Force and Pressure Capabilities: Both machines use considerable force to bend metal, but specific models might offer different pressure ranges.
- Precision and Accuracy: Modern press brakes, especially CNC versions, offer high precision and repeatability, which might be a distinguishing feature when someone refers to a "press brake" versus a "brake press."
- Material Handling: Both machines are capable of handling a variety of materials, but certain models might be optimized for specific types of metal or thicknesses.
3.Design and Structure
Design features can vary slightly:
- Frame Structure: Differences in frame design can impact stability and capacity.
- Tooling Options: Flexibility in tooling can vary, with some machines offering more customization options.
- Control Systems: Manual vs. CNC controls can be a distinguishing factor, with CNC press brakes offering enhanced automation and precision.
Similarities Between Press Brake vs Brake Press
While the terms "press brake" and "brake press" are often used interchangeably, understanding their similarities can provide clarity and reinforce why they are considered essentially the same machine in many contexts. Here are the key similarities:
1. Functionality
Both press brakes vs brake presses are designed to perform the same fundamental task: bending and shaping sheet metal. They use a combination of force and precise control to create bends, angles, and folds in metal sheets.
2. Components
The primary components of press brakes and brake presses are virtually identical. Both types of machines consist of:
- Ram: The upper part that moves down to press the metal.
- Bed: The lower stationary part that holds the die.
- Punch and Die: Tools that determine the shape and angle of the bend.
3. Operation Mechanism
Both machines operate using similar mechanisms:
- Hydraulic or Mechanical Systems: Both can utilize hydraulic systems for smooth, powerful operation, or mechanical systems for precise, repetitive movements.
- Manual or CNC Control: Both can be operated manually for simple tasks or controlled by CNC (Computer Numerical Control) systems for more complex, automated operations.
4. Applications
Press brakes and brake presses are used in similar applications across various industries, such as:
- Automotive Manufacturing: Creating parts for vehicles.
- Aerospace: Forming components for aircraft.
- Construction: Producing metal parts for buildings and infrastructure.
- Industrial Equipment: Manufacturing parts for machinery and equipment.
5. Material Handling
Both machines are capable of handling a wide range of materials, including:
- Steel: Both machines can bend different grades of steel.
- Aluminum: They can handle lightweight yet strong aluminum sheets.
- Stainless Steel: Suitable for bending corrosion-resistant stainless steel.
6. Bending Capabilities
Both press brakes and brake presses offer similar bending capabilities:
- Angle Bending: Creating precise angles in metal sheets.
- Radius Bending: Forming curves with a specified radius.
- Box and Pan Bending: Making box shapes and complex forms.
7. Customization and Tooling
Both types of machines allow for customization through different tooling options:
- Standard Tools: Basic punch and die sets for common bends.
- Specialized Tools: Custom-designed tools for unique or complex bending tasks.
8. Maintenance Requirements
Maintenance for both press brakes and brake presses involves similar tasks:
- Regular Inspection: Checking for wear and tear on moving parts.
- Lubrication: Ensuring all moving components are properly lubricated.
- Calibration: Regularly calibrating the machine to maintain precision.
Applications and Use Cases
Common Applications of Press Brakes
Press brakes are used in various applications such as:
- Automotive Manufacturing: Creating car body panels and structural components.
- Aerospace: Forming lightweight, high-strength metal parts.
- Construction: Bending metal beams and sheets for building structures.
Common Applications of Brake Presses
Similarly, brake presses are utilized in:
- Home Appliances: Fabricating metal housings and components.
- Furniture Manufacturing: Bending metal frames and supports.
- Industrial Equipment: Producing parts for machinery and equipment.
Advantages and Disadvantages
Advantages of Press Brakes
- High Precision: Especially CNC press brakes offer unmatched precision.
- Versatility: Capable of handling various materials and complex bends.
- Automation: Modern machines reduce manual labor and increase efficiency.
Advantages of Brake Presses
- Cost-Effective: Manual brake presses can be more affordable for small shops.
- Flexibility: Suitable for both small-scale and large-scale production.
- Ease of Use: Simple designs can be easier to operate for basic tasks.
Disadvantages and Limitations
- Press Brakes: Higher initial cost and maintenance for advanced models.
- Brake Presses: Manual versions may lack the precision and speed of CNC models.
- Situational considerations where one might be preferred over the other depend on specific project requirements and budget constraints.
Therefore, are press brakes and brake presses the same? The answer is: Yes. They refer to the same type of machine, just regional or contextual differences might apply. Whether referred to as a press brake or brake press, these machines are indispensable tools in the metalworking industry, offering flexibility, precision, and versatility. Next, let's explore more about press brake, also called brake press.
Origin and Evolution Of Press Brakes
As one of the more traditional methods for processing metal materials, the press brake, also commonly known as a brake press, has been around for over a hundred years. In fact, did you know the first brake was patented in 1882?
Known as the cornice brake, this nineteenth-century machine was made out of custom cast iron parts attached to finished pieces of oak and used a manually operated leaf that forced a clamped piece of sheet metal to be bent in a straight line - talk about some pressing labor! You can learn more about the origins of the press brake here.
Fast forward to today, and press brakes have evolved into highly-advanced machines powered by hydraulic systems and computer technology. These modern brakes easily bend sheet and plate metal, supplying various industries with simple and complex parts.
Understanding Press Brakes
In metalworking, a press brake is a machine tool designed to form predetermined bends by clamping the workpiece between a matching punch and die. The fabrication and sheet metal industries commonly utilize this versatile piece of equipment for bending sheet and plate material, most often sheet metal.
Types of Press Brakes
The primary classification of press brakes is by their method of applying force — hydraulic, mechanical, servo, and pneumatic.
Hydraulic press brakes have become the most common press brake in use since the 1970s. They are designed for both specialized sheet metal work and continuous industrial production jobs from single-cycle operations to automated cell components. Driven by two synchronized hydraulic cylinders, hydraulic press brakes are safer and less expensive than mechanical press brakes and offer advantages such as variable speed control, quick retraction, and the capability to reverse the stroke at any time.
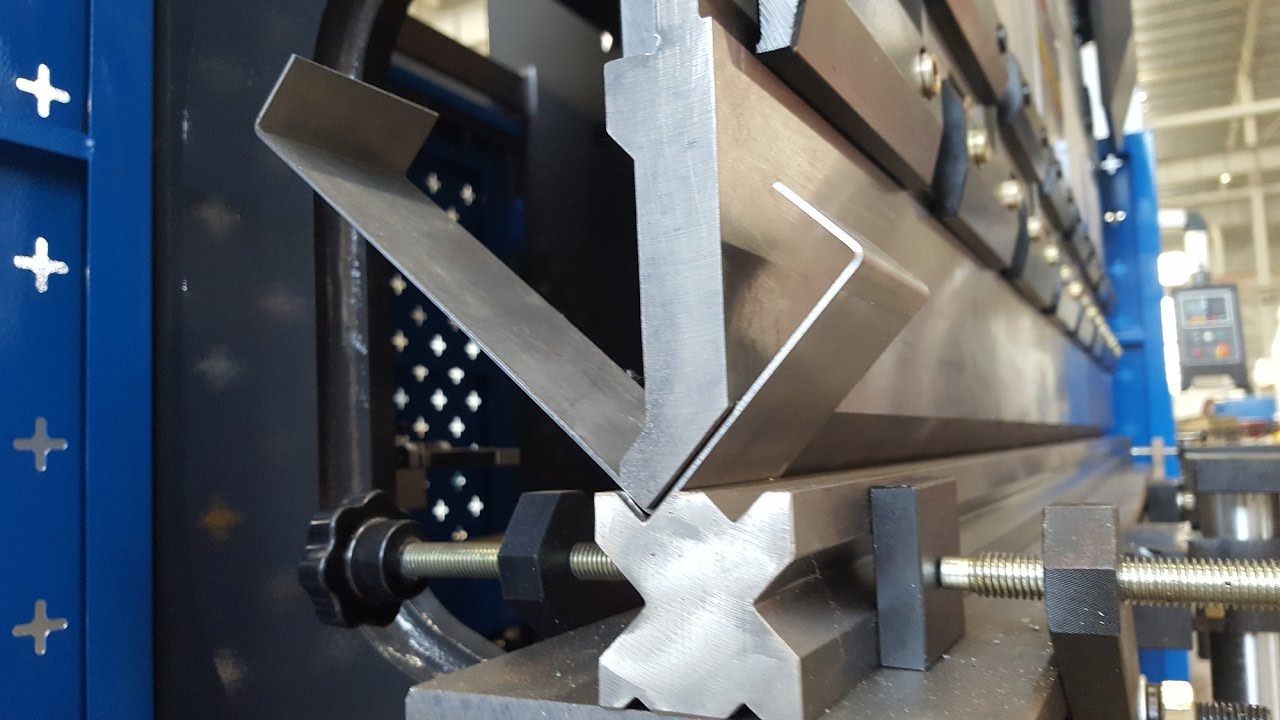
Mechanical press brakes use an electric motor to power a flywheel that stores kinetic energy and releases it through one of several different drive transmission configurations. Mechanical presses are accurate, high-speed machines with relatively low maintenance costs.
Servo press brakes, also referred to as CNC press brakes, supply the pressing force via two synchronized servomotors used to power a belt and pulley mechanism. The servomotor replaces the flywheel and clutch in mechanical press brakes. Servo-driven presses are highly flexible machines due to the ability to precisely control the stroke and speed of the ram with the servomotors. Mechanical press brakes are still a better option for high-volume applications, while servo presses are better for low-volume specialty or custom applications.
Pneumatic press brakes deliver the pressing action from a compressed air pressure source. Applications for pneumatic presses include bending, shearing, punching, forming, drawing, extruding, and assembly. Pneumatic presses cannot supply the same force as hydraulic press brakes, but they do provide a fast, clean operation.
Characteristics of Press Brakes
Press brakes are essential machines in metalworking and manufacturing industries, known for their precision and versatility in bending sheet metal. Here are the key characteristics of press brakes that define their functionality and applications:
1. Bending Capacity
- Tonnage: The force a press brake can exert, measured in tons. Higher tonnage allows for bending thicker and stronger materials.
- Bending Length: The maximum length of metal that can be bent. This is determined by the length of the machine’s bed and ram.
2. Accuracy and Precision
- Repeatability: The ability of the press brake to produce consistent results across multiple operations. High-precision machines often have repeatability within ±0.0004 inches (±0.01 mm).
- Back Gauge Accuracy: The back gauge system ensures precise positioning of the metal sheet for accurate bends. Advanced back gauges can move in multiple axes for complex bends.
3. Control Systems
- Manual Control: Basic press brakes might use manual controls, suitable for simple and less demanding tasks.
- CNC Control: Computer Numerical Control (CNC) press brakes use computer systems for precise control of bending operations. They can store multiple programs and handle complex bends with high accuracy.
- Hydraulic Systems: Provide smoother and more controlled movement compared to mechanical systems, especially for high-tonnage press brakes.
4. Tooling
- Punches and Dies: The tools used to create bends. Various shapes and sizes are available to accommodate different bending requirements.
- Quick-Change Tooling: Systems that allow for fast and easy changing of tools, minimizing downtime and increasing efficiency.
5. Material Handling
- Thickness: The thickness of the metal sheet that can be bent, typically ranging from thin sheets to thick plates.
- Material Types: Press brakes can handle a variety of materials including steel, aluminum, brass, copper, and other metals.
6. Safety Features
- Guarding Systems: Safety guards and barriers to protect operators from moving parts.
- Light Curtains: Safety devices that use light beams to detect if an operator’s hand or another object is in the danger zone, automatically stopping the machine.
7. Flexibility and Versatility
- Multi-Axis Capability: Advanced press brakes can operate on multiple axes (X, Y, Z) allowing for more complex and precise bending operations.
- Bending Radius: Ability to create different bending radii by adjusting the punch and die setup.
8. Energy Efficiency
- Servo-Electric Systems: Use electric motors instead of hydraulic systems, providing precise control and energy efficiency.
- Energy-Saving Features: Modern press brakes often come with features that reduce energy consumption during idle times.
9. Durability and Build Quality
- Frame Construction: The robustness of the machine frame, usually made from high-quality steel to withstand the forces during bending.
- Component Quality: High-quality hydraulic components, electronic controls, and mechanical parts ensure longevity and reduce maintenance needs.
Techniques of Press Brakes
Bottoming refers to the point during bending where the tooling bottoms out and the punch, material and die come together with no air gap separating them. Bottoming does not produce accurate bends, as the metal attempts to spring back to its original shape when the tooling withdraws and the force is removed.
Bottoming with penetration, also referred to as coining, is a method used to compensate for material springback. During bottoming with penetration, the tool bottoms out and then the nose penetrates the material. This creates a high enough stress to create plastic material flow, eliminating the results of springback. The drawback to this method is that the forces required are much higher than needed for bottoming, which is taxing on the tooling.
General-purpose air bending is the process of bending in air, where there are only three points of contact between the punch, material and die — two points with the die and one with the tip of the tool. The air bending process is used for material of thickness gauges 10 gauges and higher. General-purpose air bending does not produce precise bends and is used in applications that can tolerate angle variations of 1 to 2 degrees.
Precision air bending is used in applications needing tighter tolerances, however, a CNC press brake and precision-ground tooling are required. Precision air bending can produce bends with accuracy within +/- ½ degree.
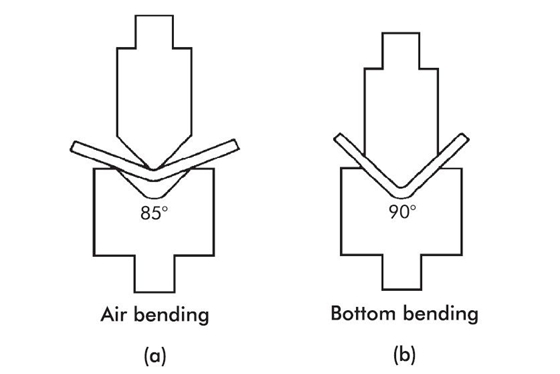
Advancements in Press Brake and Brake Press Technologies
The field of metalworking continues to evolve with technological advancements that enhance the capabilities and efficiency of press brakes and brake presses. Here are some of the most significant advancements in these machines:
1. CNC Integration
Computer Numerical Control (CNC) has revolutionized press brakes and brake presses by enabling precise, automated operations. CNC systems allow for:
- High Precision and Repeatability: CNC controls ensure that each bend is consistent and accurate, reducing errors and waste.
- Complex Bending Sequences: CNC technology can handle intricate bending sequences with ease, making it possible to produce complex parts with multiple bends.
- Ease of Use: User-friendly interfaces and programming capabilities make it easier for operators to set up and run complex jobs.
2. Automated Tool Changing
Automated Tool Changers (ATC) have significantly improved the efficiency and flexibility of press brakes:
- Reduced Downtime: Automated tool changers can quickly switch between different punch and die sets, minimizing downtime between jobs.
- Increased Flexibility: With the ability to change tools automatically, manufacturers can handle a wider variety of jobs with a single machine.
- Enhanced Safety: Automation reduces the need for manual handling of heavy tools, improving operator safety.
3. Improved Hydraulic Systems
Modern Hydraulic Systems have become more efficient and reliable:
- Energy Efficiency: New hydraulic systems are designed to consume less energy while providing the same or greater force, reducing operational costs.
- Precision Control: Advances in hydraulic technology allow for more precise control of the ram movement, improving the accuracy of bends.
- Lower Maintenance: Modern hydraulic components are built to last longer and require less maintenance, increasing machine uptime.
4. Advanced Safety Features
Safety is a paramount concern in metalworking, and new advancements have made press brakes and brake presses safer to operate:
- Laser Safety Systems: These systems use lasers to detect any objects (like hands or fingers) in the path of the machine, stopping the press if an obstruction is detected.
- Light Curtains: Light curtains create an invisible barrier around the machine, stopping operation if the barrier is breached.
- Safety Controls and Interlocks: Advanced safety controls and interlocks ensure that the machine operates only when all safety conditions are met.
5. Smart Manufacturing and Industry 4.0
The integration of Smart Manufacturing principles and Industry 4.0 technologies has brought significant benefits:
- Real-Time Monitoring: Sensors and IoT (Internet of Things) devices can monitor machine performance in real-time, providing data on machine health and operation.
- Predictive Maintenance: By analyzing data from sensors, predictive maintenance systems can identify potential issues before they lead to machine failure, reducing downtime.
- Remote Diagnostics and Support: Manufacturers can access machine diagnostics and provide support remotely, minimizing the need for on-site visits and speeding up troubleshooting.
6. Servo-Electric Press Brakes
Servo-Electric Press Brakes offer several advantages over traditional hydraulic models:
- Energy Efficiency: Servo-electric systems use significantly less energy, as they only consume power during the bending process.
- Precision and Speed: These systems provide highly precise control of the ram, allowing for faster and more accurate bends.
- Quiet Operation: Servo-electric press brakes operate more quietly than hydraulic models, improving the working environment.
7. Enhanced User Interfaces
The development of more intuitive and user-friendly interfaces has made it easier for operators to use advanced features:
- Touchscreen Controls: Modern press brakes often feature touchscreen controls that simplify programming and operation.
- 3D Simulation: Advanced software can simulate the bending process in 3D, allowing operators to visualize the finished part and identify potential issues before bending begins.
- Offline Programming: Operators can program jobs offline on a computer and then upload them to the machine, reducing setup time and increasing productivity.
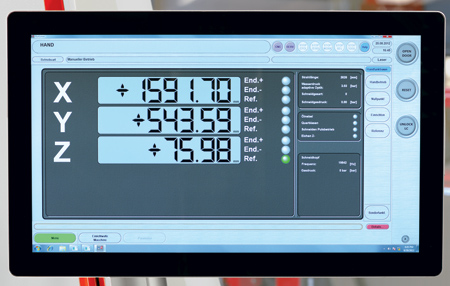
Press Brake vs Brake Press: How To Choose Right Equipment
Selecting the right press brake for your metalworking needs involves considering various factors to ensure that the machine meets your specific requirements. Here are the key aspects to consider:
1. Define Your Requirements
Understanding your specific needs is the first step in choosing the right press brake. Consider the following:
- Material Type: What types of materials will you be bending (e.g., steel, aluminum, stainless steel)?
- Material Thickness: What is the range of thicknesses you need to work with?
- Part Size and Complexity: What are the dimensions and complexity of the parts you need to produce?
2. Determine the Tonnage
The tonnage requirement is a critical factor in selecting a press brake:
- Material and Thickness: Calculate the tonnage based on the thickest and hardest material you will be bending. Most manufacturers provide tonnage charts to help with this calculation.
- Bending Length: Ensure the press brake has sufficient length to accommodate the widest material you will be working with.
3. Choose Between Hydraulic, Mechanical, and Electric
Different press brake types offer various advantages:
- Hydraulic Press Brakes: Known for their versatility and high capacity. They are suitable for a wide range of materials and thicknesses and offer precise control over the bending process.
- Mechanical Press Brakes: Often faster and more efficient for repetitive, high-volume tasks. However, they are less flexible than hydraulic models.
- Servo-Electric Press Brakes: These are energy-efficient and provide high precision. They are ideal for lighter materials and applications requiring extreme accuracy.
4. Consider Automation and CNC Controls
The level of automation and control can significantly impact productivity and ease of use:
- Manual Press Brakes: Suitable for simple, low-volume tasks and small shops with limited budgets.
- CNC Press Brakes: Provide automated control for complex bending sequences, higher precision, and repeatability. They are ideal for high-volume production and complex parts.
5. Evaluate Tooling Options
The right tooling is essential for achieving the desired bends:
- Standard Tooling: Suitable for common bending tasks.
- Specialized Tooling: Required for unique or complex bends. Consider a press brake that allows for easy tool changes to maximize flexibility.
6. Assess Machine Features
Modern press brakes come with various features that can enhance performance:
- Backgauges: Ensure accurate positioning of the material for consistent bends. Look for multi-axis backgauges for more complex bending tasks.
- Crowning Systems: Compensate for deflection in the machine during bending, ensuring uniform bends across the entire length of the material.
- Safety Features: Laser safety systems, light curtains, and other safety mechanisms protect operators and ensure safe operation.
7. Review Software Capabilities
Software plays a crucial role in the operation of CNC press brakes:
- User Interface: Look for intuitive and user-friendly interfaces that simplify programming and operation.
- 3D Simulation: Software that provides 3D simulations can help visualize the bending process and identify potential issues before production.
- Offline Programming: Allows for job setup and programming outside of the production environment, reducing machine downtime.
8. Consider the Manufacturer and Support
The reputation of the manufacturer and the support they offer are important factors:
- Reliability and Quality: Choose a manufacturer known for producing reliable and high-quality machines.
- Technical Support and Service: Ensure that the manufacturer provides good technical support, training, and readily available spare parts.
- Warranty and Maintenance: Check the warranty offered and the maintenance services provided by the manufacturer.
9. Budget and Return on Investment (ROI)
While budget constraints are important, consider the long-term ROI:
- Initial Cost: Compare the upfront cost of different machines, but also consider the features and capabilities offered.
- Operating Costs: Factor in energy consumption, maintenance, and tooling costs.
- Productivity Gains: Assess how the machine will improve productivity and quality, potentially leading to cost savings and increased revenue.
Conclusion
Press brake and brake press are two commonly confused terms in the world of metalworking equipment. A press brake refers to a machine used for bending metal sheets into desired shapes, while "brake press" is a misnomer for press brake. Therefore, the key to understanding the difference between these two lies in the correct usage of terminology. Press brakes play a crucial role in metal fabrication, enabling high precision and efficiency in metal shaping, making them essential equipment in manufacturing industries.
With a commitment to quality and performance, Krrass Press Brake offers unparalleled accuracy and efficiency in metal bending processes. Its robust construction and advanced features make it suitable for a wide range of applications across diverse industries, from automotive to aerospace.
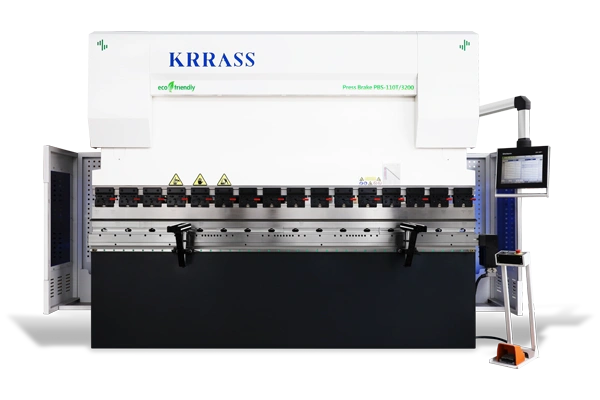