In the rapidly evolving world of manufacturing, electric press brake manufacturers are at the forefront of innovation, delivering precision and efficiency like never before. As we look ahead to 2024, it's essential to stay informed about the leading companies in this sector. These manufacturers are not only revolutionizing the industry with advanced technology but also setting new standards for quality and performance. Whether you’re upgrading your current equipment or starting a new venture, knowing the top electric press brake manufacturers can help you make informed decisions and stay competitive in the market.
Background of the Birth of Electric Bending Machines
The birth of electric bending machines, also known as electric press brakes, marked a significant milestone in the evolution of manufacturing technology. Historically, metal forming and bending were labor-intensive processes, primarily carried out using mechanical and hydraulic press brakes. These traditional machines, while effective, had several limitations including slower operation speeds, higher energy consumption, and less precision.
The development of electric bending machines was driven by the need for more efficient, precise, and environmentally friendly manufacturing solutions. Key advancements in servo motor technology and control systems in the late 20th and early 21st centuries paved the way for the creation of electric press brakes. Unlike their hydraulic counterparts, electric press brakes utilize electric servo motors to drive the bending process. This innovation offers several advantages:
Precision and Control: Electric press brakes provide exceptional precision in the bending process. The use of servo motors allows for accurate control of the ram position, ensuring consistent and high-quality bends.
Energy Efficiency: Electric press brakes consume significantly less energy compared to hydraulic systems. They only use power during the actual bending process, reducing overall energy consumption and operational costs.
Speed and Productivity: The rapid response of electric servo motors enables faster cycle times, enhancing productivity. This speed is particularly beneficial in high-volume production environments.
Safety and Maintenance: Electric press brakes are designed with advanced safety features, reducing the risk of accidents. Additionally, they require less maintenance as they do not rely on hydraulic fluids and complex hydraulic systems, resulting in lower downtime and maintenance costs.
Environmental Impact: By eliminating the need for hydraulic oil and reducing energy consumption, electric press brakes present a more environmentally friendly option, aligning with the growing emphasis on sustainable manufacturing practices.
The first electric press brakes began to appear in the market in the early 2000s, introduced by innovative manufacturers who recognized the potential of electric technology in metal forming. These early models demonstrated the feasibility and advantages of electric actuation, leading to wider adoption and continuous improvements in the technology.
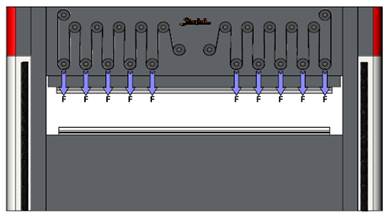
Today, electric press brakes are a staple in modern manufacturing facilities, offering unparalleled efficiency, accuracy, and sustainability. Their development and adoption represent a significant leap forward in the quest for advanced manufacturing solutions, meeting the demands of a competitive and evolving industry.
Why Electric Press Brakes Are Worth Investing In
Electric press brakes represent a significant advancement in metal forming technology, offering numerous benefits that make them a valuable investment for manufacturing businesses. Here are key reasons why investing in an electric press brake is worthwhile:
Enhanced Precision and Accuracy
- Electric press brakes use servo motors that provide exceptional control over the bending process. This results in highly accurate and consistent bends, reducing material waste and ensuring high-quality output.
Energy Efficiency
- Unlike hydraulic press brakes, electric models consume power only when in operation, leading to significant energy savings. This reduced energy consumption not only lowers operational costs but also contributes to a smaller carbon footprint.
Increased Productivity
- The rapid response of electric servo motors enables faster cycle times compared to hydraulic systems. This speed translates to higher throughput and improved productivity, allowing manufacturers to meet tight deadlines and increase their production capacity.
Lower Maintenance Costs
- Electric press brakes have fewer moving parts and do not rely on hydraulic fluids, reducing the need for regular maintenance. This simplicity in design leads to lower maintenance costs and less downtime, enhancing overall operational efficiency.
Improved Safety
- Electric press brakes come equipped with advanced safety features, such as automatic ram stopping in case of obstruction and precise control over ram movement. These safety mechanisms reduce the risk of workplace accidents and enhance operator safety.
Environmental Benefits
- The elimination of hydraulic oil and reduced energy consumption make electric press brakes a more environmentally friendly option. This aligns with the increasing emphasis on sustainable manufacturing practices and regulatory compliance.
Advanced Technology Integration
- Electric press brakes often incorporate the latest technological advancements, including CNC controls, automated tooling, and real-time monitoring. These features facilitate easier setup, better process control, and the ability to handle complex bending tasks with ease.
Versatility and Flexibility
- The precision and control offered by electric press brakes make them suitable for a wide range of applications, from simple bends to complex, multi-bend components. This versatility makes them an excellent investment for manufacturers handling diverse production requirements.
Return on Investment (ROI)
- While the initial cost of electric press brakes may be higher than that of hydraulic models, the long-term savings in energy, maintenance, and operational efficiency can result in a faster return on investment. Enhanced productivity and reduced downtime further contribute to the financial benefits.
Future-Proofing Manufacturing Operations
- Investing in electric press brakes positions manufacturers at the forefront of industry advancements. As the industry continues to move towards smarter, more efficient production methods, having cutting-edge equipment ensures that businesses remain competitive and capable of meeting future demands.
In conclusion, the numerous advantages of electric press brakes, including their precision, energy efficiency, lower maintenance requirements, and enhanced safety, make them a compelling investment for modern manufacturing operations. By adopting this advanced technology, manufacturers can achieve significant improvements in productivity, cost savings, and environmental sustainability.
Key Technical Parameters to Consider When Purchasing an Electric Press Brake
When purchasing an electric press brake, understanding the technical parameters is crucial to ensure that the machine meets your production requirements. Here are the key technical parameters you should consider:
1. Bending Capacity
Maximum Bending Length: The maximum length of the metal sheet that the press brake can bend, crucial for handling large workpieces efficiently.
Maximum Bending Thickness: The maximum thickness of the metal sheet or plate that the press brake can bend, determining its capability to handle various materials.
Minimum Bending Radius: The smallest radius that can be achieved without causing material deformation, important for precision bending applications.
2. Tonnage
Maximum Tonnage: The maximum force the press brake can apply during bending, ensuring it can handle heavy-duty materials and thick plates.
Minimum Tonnage: The lowest force setting of the press brake, which affects its versatility for bending various materials, from thin sheets to thicker plates.
3. Back Gauge Range
Maximum Back Gauge Travel: The maximum distance the back gauge can move, determining the maximum depth of the bend and accommodating complex bending sequences.
Minimum Back Gauge Position: The closest distance the back gauge can move to the bending edge, ensuring flexibility for handling small parts or tight bending setups.
4. Speed and Accuracy
Bending Speed: The speed at which the ram descends and ascends during bending operations, impacting productivity and turnaround time for jobs.
Positioning Accuracy: The precision with which the ram can be positioned for bending, critical for achieving accurate bends, especially in intricate designs.
5. Control System
Type of Control: Whether the press brake uses a manual, semi-automatic, or CNC control system, affecting ease of use and automation capabilities.
Control Interface: The user interface for setting bending parameters, often including touchscreen displays or software interfaces for intuitive operation.
Programmable Features: Ability to store and recall bending programs for different jobs, allowing for efficient setup and repeatability.
6. Drive System
Servo Motor Type: Details about the servo motors used for driving the ram and back gauge, providing precise control and high-speed operation.
Drive Mechanism: Information about the drive mechanism, such as ball screw or belt drive, affecting precision, speed, and reliability.
7. Tooling Compatibility
Tooling Type: Compatibility with standard or custom tooling systems, including punch and die sizes, enabling versatility for various bending tasks.
Tooling Setup: Ease of tooling setup and changeover for different bending tasks, reducing downtime and increasing efficiency.
8. Safety Features
Light Curtains: Presence of light curtains to detect operator presence and prevent accidents, ensuring a safe working environment.
Safety Interlocks: Mechanisms to ensure safe operation, such as interlocks on guards and doors, minimizing the risk of injuries.
Emergency Stop: Ability to quickly stop machine operation in case of emergencies, prioritizing operator safety.
9. Energy Efficiency
Power Consumption: Information about energy consumption during operation, helping to optimize energy usage and reduce operational costs.
Energy-saving Features: Presence of features like regenerative braking or standby modes to reduce energy usage, promoting sustainability and cost savings.
10. Machine Dimensions and Weight
Overall Dimensions: Understanding the size of the machine is crucial to ensure it fits comfortably within your workspace. Consider the overall dimensions to plan for placement and workflow efficiency.
Weight: The weight of the machine is important for installation considerations and determining floor load capacity. Knowing the weight helps ensure proper support and stability for the press brake within your facility.
11. Manufacturer Support
Warranty Coverage: Ensure you understand the warranty terms, including coverage and duration, provided by the manufacturer. A comprehensive warranty can offer peace of mind regarding potential maintenance or repair costs.
Technical Support and Training: Look for manufacturers like KRRASS who offer extensive technical support, including assistance with machine setup, troubleshooting, and training for operators. Access to expert guidance ensures smooth operation and maximizes productivity.
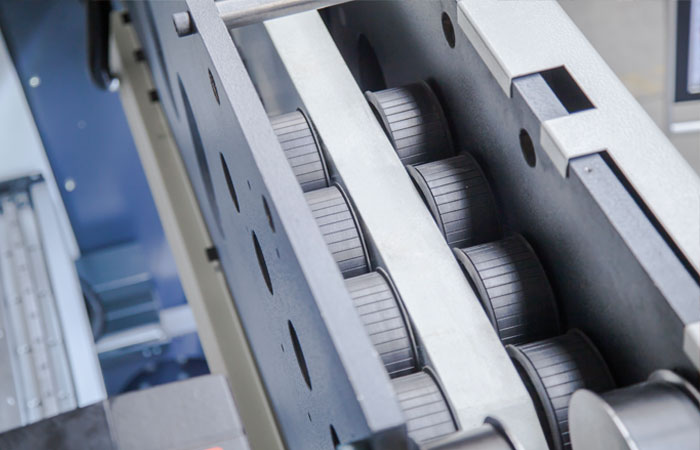
Criteria for Selecting Top Electric Press Brake Manufacturers
Selecting the right manufacturer for your electric press brake is essential to ensure you get a machine that meets your needs and provides long-term value. Here are the key criteria to consider:
Quality and Reliability of Products
- Build Quality: Look for manufacturers known for high-quality construction materials and robust engineering. The durability of the machine is crucial for long-term performance.
- Performance Consistency: Choose manufacturers whose products are consistently reliable and perform well under various operating conditions.
Technological Innovations and Advancements
- Cutting-Edge Technology: Opt for manufacturers that integrate the latest technological advancements, such as advanced CNC controls, automated systems, and precision servo motors.
- R&D Investment: Consider manufacturers that invest heavily in research and development to continuously improve their products and introduce innovative features.
Customer Service and Support
- Technical Support: Ensure the manufacturer offers comprehensive technical support, including troubleshooting, maintenance, and repair services.
- Training and Resources: Look for manufacturers that provide extensive training programs and resources to help you and your team operate the machine efficiently.
- After-Sales Service: Reliable after-sales support is crucial for addressing any issues that may arise post-purchase and ensuring minimal downtime.
Industry Reputation and Reviews
- Customer Feedback: Check reviews and testimonials from other users in the industry to gauge the manufacturer’s reputation. Positive feedback indicates reliability and customer satisfaction.
- Industry Awards and Recognitions: Manufacturers recognized by industry awards and certifications often demonstrate excellence in their field.
Cost-Effectiveness and Return on Investment
- Initial Cost vs. Long-Term Value: Evaluate the balance between the initial purchase cost and the long-term benefits, such as lower maintenance costs, energy savings, and increased productivity.
- ROI Analysis: Consider how quickly the machine will pay for itself through improved efficiency and reduced operational costs. A high-quality machine might have a higher upfront cost but offer significant savings over time.
By considering these criteria, you can select a top electric press brake manufacturer that delivers high-quality, reliable products backed by excellent customer support and technological innovation, ensuring a valuable return on your investment.
Top Electric Press Brake Manufacturers in 2024
Krrass Machinery
Krrass Manufacture, established in 1998, is a prominent metalworking machinery company situated on a sprawling 30,000 square meter facility. With a team of over 150 dedicated employees, the company excels in the design and production of a wide range of metalworking machines, including press brakes, shearing machines, and electric bending machines.
Krrass has earned a stellar reputation in the global market, exporting its products to numerous countries around the world. A notable strength of the company is its exceptional after-sales service team, which is fluent in English and has consistently received positive feedback from customers both domestically and internationally.
The company is proud of its factory-direct sales model. Its product lineup includes the WE67K series CNC electro-hydraulic press brakes, the WC67K series NC hydraulic press brakes, the QC11K series CNC guillotine hydraulic shearing machines, the QC12K series swing beam hydraulic shearing machines, the HSL series CNC gantry V grooving machines, the HSDV series CNC vertical V grooving machines, and the Q35Y series hydraulic ironworkers. Additionally, Krrass offers advanced electric bending machines that provide high precision and efficiency, catering to the evolving needs of the metalworking industry.
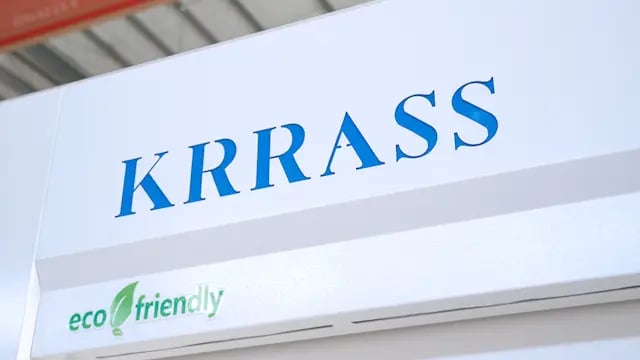
Boschert USA
Boschert USA is a renowned company that specializes in manufacturing high-quality sheet metal fabrication equipment. The company offers a wide range of machinery and tools, with a particular focus on electric press brakes. Boschert USA’s electric press brake machines are known for their cutting-edge technology and numerous features, making them suitable for various industries and applications.
In summary, Boschert USA’s electric press brake machines are known for their precision, flexibility, and productivity-enhancing features. They are well-suited to various industries that require the bending and shaping of sheet metal components with high levels of accuracy and efficiency.
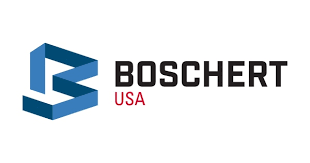
Euromac
Euromac is a globally recognized company that specializes in supplying advanced machinery for sheet metal working. Their product range encompasses CNC punching machines, bending machines, and notching machines, all of which incorporate cutting-edge technologies. These machines have been continuously refined and improved by Euromac’s team of skilled design engineers to meet the ever-evolving demands of the market, particularly in terms of flexibility and precision.
One of the key distinguishing features of Euromac is its proud Italian heritage. It’s an Italian company that carries a legacy of craftsmanship and innovation. Despite its Italian roots, Euromac has a strong and extensive global presence within the sheet metal industry.
Their commitment to excellence and their ability to provide state-of-the-art solutions have made them a trusted name worldwide, serving a diverse clientele that relies on their machinery for various sheet metal processing needs. Euromac’s dedication to staying at the forefront of technological advancements in the sheet metal industry underscores their commitment to delivering quality and reliability to their customers on a global scale.

MC Machinery System
MC Machinery Systems, as part of the global Mitsubishi Corporation, benefits from extensive worldwide support and access to innovative resources. Headquartered near Chicago in Elk Grove Village, Illinois, MC Machinery is a subsidiary of the Mitsubishi Corporation. The company also operates technology centers in various strategic locations, including Concord, North Carolina; Cypress, California; Pine Brook, New Jersey; Dallas, Texas; Querétaro, Mexico; and Richmond Hill in Ontario, Canada.
Established in 1978, MC Machinery has grown to employ more than 430 dedicated professionals in North America. With a focus on serving a diverse range of industries, including aerospace, automotive, mold and die, job shops, medical, and energy, the company offers a substantial, regionally-focused service network. Additionally, MC Machinery boasts an experienced application support team that is committed to assisting its customers in various applications and processes.
Notably, MC Machinery holds the distinction of being the exclusive North American supplier and servicer of Mitsubishi lasers and Electrical Discharge Machining (EDM) equipment.
Automec
Automec Inc., headquartered in Waltham, Massachusetts, has a rich history dating back to its founding in 1969, and it officially incorporated in 1971. The company specializes in the manufacturing and distribution of computerized gauging systems, with a primary focus on serving the Metal Fabrication Industry. Furthermore, Automec has extended its expertise to cater to the Wood and Fenestration Industries as well.
Automec’s innovative gauging systems are designed to seamlessly integrate with key fabricating machines, such as press brakes, shears, saws, and punches. By doing so, these systems enhance operator productivity and efficiency, streamlining various manufacturing processes.
Recognizing the growing significance of Servo-electric press brakes in the evolving landscape of press brake technology, Automec made a significant move by becoming a Certified USA Dealer of CoastOne servo-electric press brakes in 2017. This strategic partnership marked a pivotal moment in the company’s history. CoastOne, a private company based in Finland, joined forces with Automec to offer their servo-electric press brakes to the American Market.
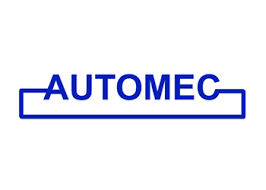
Trading Company or Factory, How to Choose Purchasing Channels?
Choosing the right purchasing channel for electric press brakes is crucial for ensuring the best value, quality, and support for your investment. Here are key considerations when deciding between a trading company and a factory:
Trading Company
Advantages:
- Wide Range of Products:
- Trading companies often represent multiple manufacturers, giving you access to a broader range of products and technologies.
- They can provide comprehensive solutions by combining products from different suppliers.
- Convenience:
- Trading companies handle import/export logistics, documentation, and compliance, simplifying the purchasing process.
- They can offer turnkey solutions, including installation, training, and after-sales service.
- Market Expertise:
- Trading companies usually have extensive knowledge of the market and can provide insights and recommendations based on your specific needs.
- They can negotiate better terms and prices due to their purchasing volumes and relationships with manufacturers.
- Customer Support:
- Trading companies often have dedicated customer service teams to handle inquiries, orders, and support, providing a single point of contact.
Disadvantages:
- Higher Costs:
- Trading companies add a markup to the manufacturer's price, potentially increasing the overall cost.
- Additional layers in the supply chain can lead to higher prices compared to direct factory purchases.
- Less Direct Control:
- You may have less direct control over the production process and quality assurance since you are not dealing directly with the manufacturer.
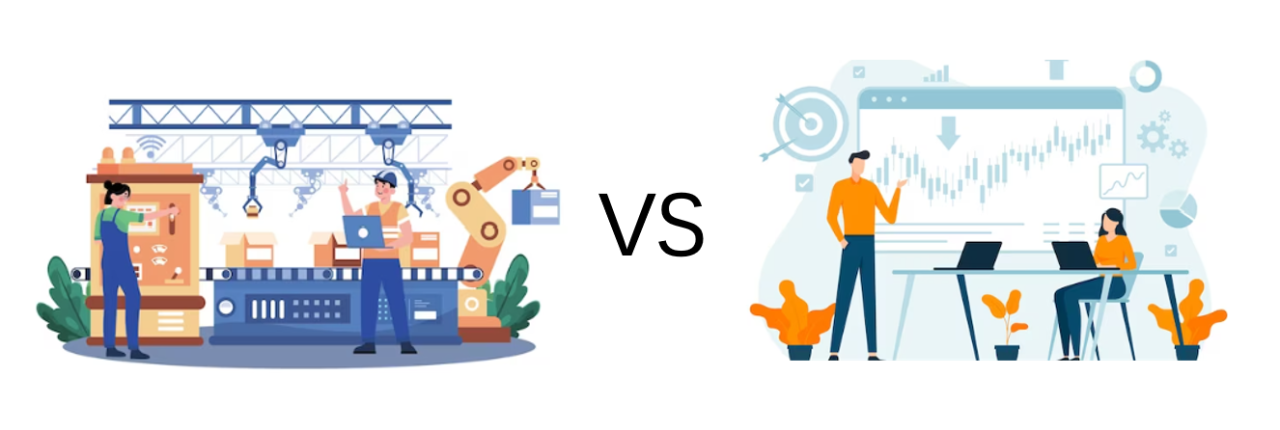
Factory
Advantages:
- Lower Costs:
- Purchasing directly from the factory eliminates intermediaries, potentially reducing costs.
- Direct negotiation with manufacturers can lead to better pricing and customized solutions.
- Direct Communication:
- Direct interaction with the factory allows for clearer communication regarding specifications, customizations, and production schedules.
- You can ensure that your specific requirements are met more accurately.
- Quality Control:
- Direct access to the factory enables better monitoring of the production process and quality control measures.
- Factories may offer factory tours, allowing you to inspect production facilities and processes firsthand.
- Customization:
- Factories are more likely to accommodate special requests and customizations tailored to your specific needs.
- They can provide more technical support and detailed product knowledge.
Disadvantages:
- Limited Product Range:
- Factories typically specialize in specific product lines, offering a narrower range compared to trading companies.
- You may need to work with multiple factories to fulfill all your equipment needs.
- Complex Logistics:
- Handling import/export logistics, customs clearance, and international shipping can be more complex and time-consuming when dealing directly with factories.
- You may need to manage multiple suppliers and coordinate shipments yourself.
- After-Sales Support:
- Factories may have limited local presence or after-sales support in your region.
- You might face challenges in getting timely service, spare parts, or technical support.
Factors to Consider
- Budget:
- If cost is a primary concern, direct factory purchases may offer better pricing.
- Consider the total cost of ownership, including shipping, taxes, and potential after-sales support.
- Product Requirements:
- Evaluate your need for a wide range of products versus specialized, customized solutions.
- Ensure the chosen supplier can meet your technical and quality standards.
- Logistics and Support:
- Consider the complexity of logistics and the level of after-sales support you require.
- Trading companies may provide more convenience and support, while factories offer direct control and potentially lower costs.
- Market Knowledge:
- Trading companies often have better market knowledge and can offer insights and recommendations.
- Factories provide in-depth technical knowledge and direct product expertise.
- Risk Management:
- Trading companies can mitigate risks associated with international trade, such as currency fluctuations and regulatory changes.
- Factories might offer more stability and direct accountability for product quality and delivery.
Electric Press Press Brake From Krrass Manufacture
The ePP-Electric Press Brake from KRRASS offers notable advantages, including swift acceleration and deceleration, along with a rapid response time, thanks to its ball screw servo drive system. Additionally, it eliminates the need for hydraulic oil, resulting in a 50% reduction in energy consumption.
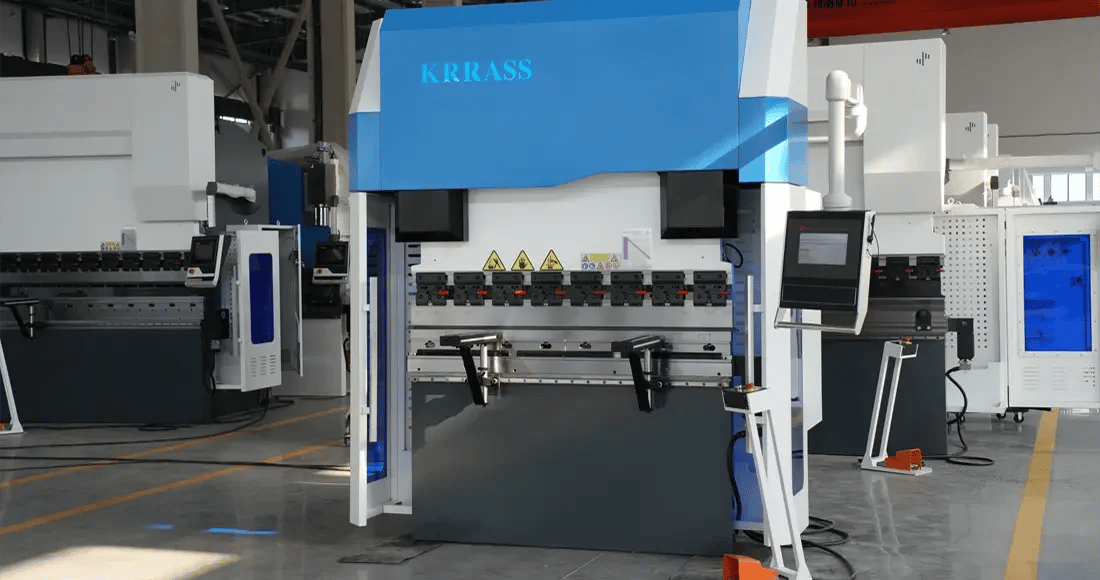
Complete Process Control
The EPP Series hybrid CNC press brake is designed with a user-friendly control interface, advanced features, and a step-by-step guide to accommodate operators of all skill levels. This ensures fast and efficient job loading, programming, and editing.
The cutting-edge multi-touch control is ergonomically mounted on a moveable arm, allowing for easy access and positioning at various points around the machine according to the operator's needs.
Direct-Drive Technology for All-Electric Operation
The hybrid CNC press brake features a patented Direct Drive Electric Motor that maximizes efficiency, repeatability, and reliability. This design directly connects the ball screw with the torque motor, ensuring seamless synchronization.
In addition to significantly reducing maintenance costs, the absence of gearboxes eliminates backlash, enhancing the overall performance and durability of the machine.
Conclusion
As the metalworking industry continues to evolve, electric press brake manufacturers like Krrass Manufacture are at the forefront of technological advancements. The development trend in electric press brakes is characterized by increased automation, higher precision, and greater energy efficiency. Manufacturers are investing in smart technology integration, such as IoT and AI, to enhance machine performance and provide real-time data monitoring and diagnostics.