A 100 ton press brake is a powerful and versatile machine widely used in metalworking industries for bending and shaping metal sheets. Understanding its bending limits is crucial for achieving precision, efficiency, and safety in various applications. This guide will explore the factors influencing these limits, methods to calculate them, and practical considerations for optimal performance. Whether you're a seasoned professional or new to press brake operations, knowing the bending capabilities and constraints of a 100 ton press brake can significantly enhance your workflow and prevent costly mistakes.
100 Ton Press Brake Basics
The hydraulic 100 ton press brake is an invaluable piece of industrial machinery for various metal forming applications. It is designed to bend and shape sheet metal, steel, aluminum, and other metals into complex configurations. By applying pressure from the press ram to a workpiece, the machine bends it into the desired shape with precision.
This particular press brake features a heavy-duty frame construction with high-grade steel welding, ensuring stability and durability during operation. It includes an adjustable work table that can easily be modified to accommodate different material sizes. The machine is equipped with a two-speed motor for smooth operation and precise control over the bending process. Additionally, it boasts multiple safety features, such as overload protection and emergency stop buttons, to ensure safe operation at all times.
Powered by an electric motor, the hydraulic system includes two cylinders that generate up to 100 tons of force, allowing a wide range of materials to be bent without excessive strain on the machine. The hydraulic system offers variable speed settings for enhanced control over the bending process.
Furthermore, the press brake comes with a digital display providing accurate readings of the bend angle, pressure, and other parameters, enabling precise control over each bend. Quick die change technology also allows operators to switch between different dies swiftly and easily without manual adjustments.
This 100 ton hydraulic press brake is ideal for industrial applications such as automotive manufacturing, aerospace engineering, electronics manufacturing, and metal fabrication, offering high-performance capabilities and advanced safety features for reliable results in any metal forming project.
Why Use a 100 Ton Press Brake
A 100 Ton Hydraulic Press Brake is an essential tool for metalworking professionals, offering numerous benefits over traditional press brakes. This machine employs a hydraulic system to generate 100 tons of force, enabling it to bend, shape, and form metal with exceptional accuracy and precision. This capability makes it perfect for producing complex parts with intricate designs that are difficult or impossible to achieve manually.
The hydraulic system ensures smooth operation by providing consistent power throughout the entire bending process. This consistency helps prevent warping or distortion that can occur with manual press brakes due to uneven force application. Furthermore, the 100 Ton Hydraulic Press Brake can perform multiple bends in a single cycle, saving time and boosting productivity.
How Does Efficiency Increase with 100 Ton Press Brake
The most notable benefit of using a 100 ton hydraulic press brake is its tremendous power and capacity. With a maximum pressure rating of up to 100 tons, this machine can effortlessly bend and shape heavy-duty materials. Furthermore, it features an adjustable bed length and stroke depth, allowing for precision bending without requiring multiple operations. This reduces the time spent on each job and enhances overall productivity.
The accuracy provided by a 100 ton hydraulic press brake significantly boosts efficiency. The machine's control system ensures repeatable bends within tight tolerances, eliminating the need for manual adjustments or resets each time. This results in quick turnaround times between jobs and fewer scrap pieces due to inaccurate bending operations.
In addition to speed and accuracy, a 100 ton hydraulic press brake also enhances safety compared to other bending machines. Its hydraulically powered system requires minimal operator intervention, and it includes various safety mechanisms such as emergency stops and interlocks to prevent accidents during operation.
How Tonnage Impacts Press Brake Bending
Selecting the correct tonnage for press brake bending is crucial to ensuring both high-quality production and cost-efficiency. Incorrect tonnage not only affects the quality of the finished part but can also lead to significant risks for tooling, machinery, and operators. Using more tonnage than the press brake's maximum capacity for any application can result in severe damage to the machine, breakage of tooling, and pose serious safety hazards to operators. Overloading a press brake can cause deformation of the ram and bed, often leading to damage that cannot be repaired. Properly choosing the right tonnage for each bending task is essential to avoid such irreversible damage and to maintain operator safety.
Understanding Maximum Tonnage
Maximum tonnage refers to the highest amount of force that a press brake can apply to shape sheet metal. It is commonly measured in tons per foot (tons/ft) or kilonewtons per meter (kN/m). Each press brake machine has a specific maximum tonnage rating that dictates the amount of force it can safely generate. Additionally, tooling, holders, and adapters each have their own tonnage limits. Operators must be aware of these limits to effectively and safely utilize the full range of applications for their press brake.
How to Determine the Required Tonnage
How much tonnage is necessary for a bending application? Several factors influence the tonnage needed, including:
- Material Thickness
- Material Type
- Material Length
- Bending Method
- Tooling Selection
Generally, thicker materials require more tonnage to form. The material type significantly affects this requirement, as different materials have varying yield strengths. For instance, bending soft brass or copper demands less tonnage compared to mild steel of the same thickness, while stainless steel requires even more force than mild steel.
Tonnage ratings also factor in the length of the material being bent. For example, a press brake with a rating of 30 tons per foot translates to 2.5 tons per inch. If a bending task requires 50 tons of force over a 10-inch length, it translates to 5 tons per inch or 60 tons per foot. Some applications necessitate concentrating a large amount of tonnage in a small area, known as isolated tonnage. In such cases, it is crucial to ensure that the tooling and holders can handle the required tonnage.
The bending method used also affects the tonnage requirements. Air bending typically requires the least force, followed by bottom bending, with coining demanding the most. Bottom bending generally needs at least twice the tonnage of air bending, while coining may require 5 to 10 times more force than air bending. Each method has its own advantages and limitations, but understanding these differences is essential for selecting the appropriate tonnage.
Understanding Force Charts
To help calculate the required tonnage for press brake operations, we use air-bending force charts. These charts provide estimates for the tonnage needed to air bend a specific thickness of mild steel given a particular V-opening. The values in the white and gray boxes, which run diagonally from the top left to the bottom right of each chart, indicate the required tons per foot (tons/ft) for achieving a certain bend.
Important Note: The figures on these charts are based on mild steel with a tensile strength of approximately 60,000 psi.
To use the chart, start by locating the material thickness on the left side of the chart. Follow the row horizontally to find the corresponding tonnage values. You'll notice that tonnage requirements decrease as the V-opening size increases for the same material thickness. A shaded box on the chart shows the recommended V-opening for each material thickness. Conversely, a red-shaded box indicates that the V-opening is too small for the given material thickness.
If the tonnage limitations suggest that a larger V-opening might be needed, it’s essential to evaluate the implications on the final part. Consider whether the larger V-opening will affect the flange length or alter the inside radius of the bend. Additionally, changes in the V-opening may impact the flat pattern or blank development, so these factors should be taken into account before making adjustments.
Steps to Calculate Press Brake Tonnage Bending Limits
Determine Material Properties
Material Type: Identify the material you are working with (e.g., mild steel, stainless steel, aluminum).
Yield Strength: Obtain the yield strength of the material, usually provided in pounds per square inch (psi) or megapascals (MPa).
Measure Material Dimensions
Material Thickness: Measure the thickness of the sheet metal.
Material Length: Measure the length of the section being bent.
Select Bending Method
Identify the bending method you will use (e.g., air bending, bottom bending, coining), as each method requires different amounts of force.
Calculate Required Tonnage
Use the following formula to estimate the required tonnage:
Material Length: Length of the part being bent.
Material Thickness: Thickness of the sheet metal.
Yield Strength: Yield strength of the material.
Bending Constant: A constant factor depending on the bending method, typically ranging from 1.0 to 1.8. For air bending, use 1.0; for bottom bending, use 1.6; for coining, use 1.8.
What's the 100 Ton Press Brake Bending Limitis
A 100 ton press brake has specific bending limits that depend on various factors including material properties, dimensions, and bending methods. Here’s an overview of what influences these limits:
Material Thickness
The maximum thickness of the material that can be bent with a 100 ton press brake depends on the material’s yield strength. Generally, a 100 ton press brake can handle materials up to around 1/4 inch (6.35 mm) thick for mild steel. Thicker materials may require adjustments or different machinery.
Material Type
Mild Steel: A 100 ton press brake can handle relatively thick sections, typically up to 1/4 inch (6.35 mm) or slightly more.
Stainless Steel: Due to its higher yield strength, the thickness limit is usually lower, around 3/16 inch (4.76 mm).
Aluminum: This material is easier to bend and can be handled in greater thicknesses, sometimes up to 3/8 inch (9.53 mm) or more, depending on its specific alloy and temper.
Bend Length
The length of the material being bent also affects the bending limits. A 100 ton press brake typically has a maximum bending length of about 4 to 6 feet (1.2 to 1.8 meters). The tonnage rating is distributed across this length, so longer bends may require adjustments in the setup.
Bending Method
Air Bending: Requires less tonnage compared to other methods. For a 100 ton press brake, this method allows for a broader range of material thicknesses and bend lengths.
Bottom Bending: Requires more tonnage than air bending. It typically limits the maximum thickness to around 1/4 inch (6.35 mm) for mild steel, depending on the machine’s design.
Coining: Demands the highest tonnage. A 100 ton press brake might be limited to thinner materials with this method, as it applies more concentrated force.
Write at the End
A 100 ton press brake, offers numerous advantages for manufacturing operations. It ensures increased accuracy and repeatability in bending and forming tasks, enhances safety, and accelerates production. The KRRASS 100 ton press brake is an ideal choice for any shop requiring precise and efficient metal forming. With its ability to accurately produce complex shapes quickly and safely, this press brake is a valuable asset for maximizing both efficiency and productivity.
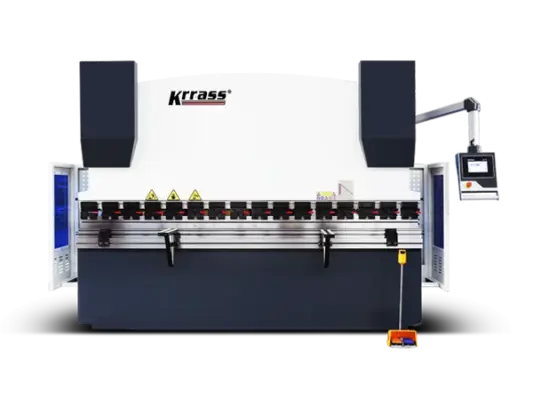