When it comes to sheet metal bending, accuracy and precision are key. The finger press brake is specifically designed to meet these requirements, offering a level of control that is unmatched by other bending methods. With its adjustable fingers, you can easily create bends of various angles and lengths, allowing for a wide range of applications. From HVAC ductwork to electrical enclosures, the finger press brake is a versatile tool that can handle it all.
What Is Finer Press Brake
A finger press brake is a small, portable machine designed for bending sheet metal with precision and accuracy. Its versatility enables users to create different angles and lengths, making it an invaluable tool for both professionals and DIY enthusiasts working on metal fabrication projects.
The finger press brake delivers exceptional control and precision in metal bending. Its distinctive design features adjustable fingers or dies, allowing for the creation of bends at various angles and lengths, ensuring consistent and accurate results with every use.
A major advantage of the finger press brake is its portability. Unlike larger, bulkier machines, this compact and lightweight tool is easy to transport and store, making it ideal for use in tight workspaces or on-the-go projects.
User-friendly and intuitive, the finger press brake is accessible to both professionals and beginners. With minimal adjustments and the application of pressure, it efficiently produces precise bends in sheet metal with ease.
Investing in a finger press brake is a practical choice for anyone working with sheet metal. It streamlines the bending process, saves time and effort, and guarantees accurate results, making it a valuable addition to any metalworking toolkit, whether for professional use or DIY projects.
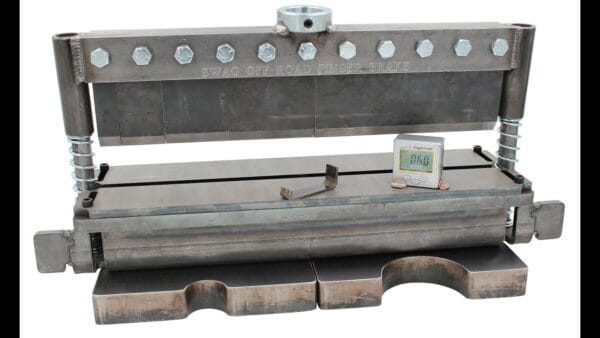
Types of Finger Press Brakes
Finger press brakes come in various types, each offering distinct features and capabilities to meet different project requirements. Below are the common types of finger press brakes available:
- Manual Finger Press Brake: Operated by hand, the manual finger press brake is ideal for small-scale projects and DIY enthusiasts. It’s easy to use, requires minimal setup, and provides precise bending for smaller jobs without the need for power assistance.
- Hydraulic Finger Press Brake: Powered by hydraulic cylinders, this type delivers more force and control, making it suitable for larger, more demanding projects. Hydraulic finger press brakes offer enhanced precision and can handle a wider range of materials and thicknesses.
- Electric Finger Press Brake: Powered by electricity, electric finger press brakes provide convenience and efficiency by eliminating manual effort. Often equipped with advanced features such as programmable controls and digital displays, they enable precise and repeatable bends with minimal operator input.
- CNC Finger Press Brake: The CNC (Computer Numerical Control) finger press brake is the most advanced option, utilizing computer software to automate bending operations. Known for high accuracy and repeatability, CNC finger press brakes are ideal for large-scale production and complex bends.
- Portable Finger Press Brake: Lightweight and easy to transport, portable finger press brakes offer flexibility for professionals who need to work at multiple job sites. Despite their compact design, they still provide the same precision and accuracy as larger models, making them a convenient solution for on-the-go projects.
Each type of finger press brake offers unique benefits, whether you need a manual, hydraulic, electric, CNC, or portable version. Regardless of the type, these machines ensure precise bends and efficient sheet metal processing tailored to your needs.
Benefits of Finger Press Brake
Precision and Accuracy: A finger press brake allows for highly precise bends in sheet metal, making it ideal for projects requiring exact angles and lengths. The adjustable fingers or dies ensure consistent, repeatable results.
Versatility: With adjustable fingers, this tool can handle various bending tasks, from simple to complex shapes, making it suitable for a wide range of sheet metal applications.
Portability: Its compact and lightweight design makes the finger press brake easy to transport and store. This portability is especially useful for those working in tight spaces or needing to move the machine between job sites.
User-Friendly Operation: The simple and intuitive design of the finger press brake makes it accessible to both professionals and beginners, allowing for quick setup and easy operation.
Efficiency: By eliminating the need for manual bending methods, a finger press brake saves time and effort, enabling faster production of bent metal parts with minimal physical strain.
Cost-Effective: Compared to larger bending machines, finger press brakes are generally more affordable, making them an economical option for small workshops, DIY enthusiasts, or professionals working on smaller-scale projects.
Customization: The adjustable nature of the fingers allows for greater flexibility in creating custom bends and shapes, accommodating a wide range of metalworking needs.
Space-Saving: Its compact size makes it an ideal choice for small workshops or areas with limited space, providing powerful bending capabilities without taking up too much room.
Factors to Consider When Choosing a Finger Press Brake
Selecting the right finger press brake is essential for achieving optimal performance and meeting your specific needs. Here are key factors to consider:
Bending Capacity: One of the most important considerations is the machine's bending capacity, which refers to the maximum thickness and length of sheet metal it can handle. Choose a press brake that can accommodate the size and thickness of the materials you typically work with.
Power Source: Finger press brakes are available in various power types, including manual, hydraulic, electric, and CNC. Each has its own benefits and limitations. Evaluate your specific requirements and preferences to determine which power source best suits your applications.
Precision and Accuracy: High precision is essential for producing consistent, quality bends. Ensure the press brake offers fine-tuned control to achieve the desired angles and dimensions with minimal error.
Ease of Use: User-friendliness is important, especially for beginners or when training others. Look for a machine that is easy to operate, with intuitive controls and clear instructions to streamline the bending process.
Durability and Reliability: A press brake should be durable and reliable to withstand long-term use. Consider the build quality, materials, and reputation of the manufacturer to ensure you invest in a machine that delivers consistent performance over time.
By considering these factors, you can confidently choose a finger press brake that enhances your sheet metal bending capabilities, offering precise and professional results tailored to your specific needs.
Tips for Using a Finger Press Brake Safely
Operating a finger press brake requires attention to safety and proper technique to ensure both your safety and the quality of your work. Here are some key tips to follow:
- Wear Protective Gear: Always wear appropriate safety equipment such as safety glasses, gloves, and ear protection. This will help protect you from potential hazards and injuries during operation.
- Read the Manual: Before using the machine, thoroughly read the user manual provided by the manufacturer. This will help you understand the machine’s capabilities, operating procedures, and safety precautions.
- Inspect the Machine: Before each use, inspect the finger press brake to ensure it is in good working condition. Check for any loose or damaged parts, and make sure all safety features and guards are securely in place.
- Position the Material Correctly: Ensure the sheet metal is properly positioned on the machine’s bed and securely held in place to prevent any movement or slippage during the bending process.
- Adjust the Fingers Properly: Set the adjustable fingers or dies to the required angle and length for the bend, making sure they are securely tightened to avoid any shifting during operation.
- Use Proper Technique: Apply steady, even pressure on the material when operating the machine. Avoid using excessive force or sudden movements, as these can cause accidents or damage the machine.
- Take Breaks: If you are working on multiple pieces or a large project, take regular breaks to rest and avoid fatigue. Staying focused is essential for maintaining safe operation.
Safety should always be your top priority when using any machinery. By following these guidelines and taking necessary precautions, you can safely operate a finger press brake and achieve accurate, professional results.
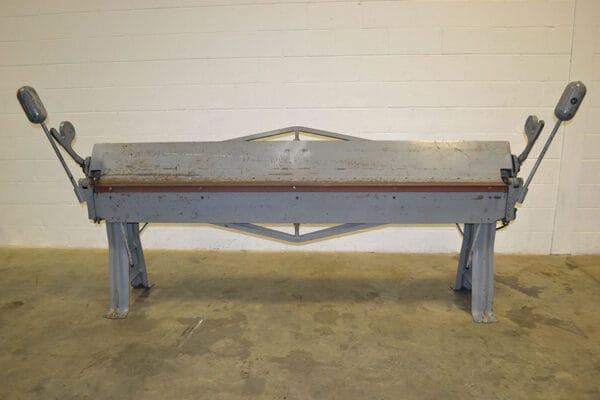
How to Maintain a Finger Press Brake
Proper maintenance of a finger press brake is essential for ensuring its longevity, performance, and safety. Here are some key steps to follow for maintaining your finger press brake:
- Regular Cleaning: Keep the machine clean by removing dust, debris, and metal shavings after each use. This prevents buildup that can affect performance and damage moving parts.
- Lubricate Moving Parts: Regularly lubricate the moving components such as the hinges, joints, and fingers to reduce friction and wear. Follow the manufacturer’s recommendations for the type of lubricant to use.
- Inspect for Wear and Tear: Routinely check for any signs of wear or damage, especially on critical parts such as the fingers, dies, and clamps. Replace any worn or damaged components immediately to avoid compromising the machine's performance.
- Check Alignment: Ensure that the press brake’s fingers and dies are properly aligned. Misalignment can lead to inaccurate bends and cause undue stress on the machine.
- Tighten Loose Parts: Periodically check for loose bolts, nuts, or other fasteners and tighten them as needed to maintain the stability and integrity of the machine.
- Test Safety Features: Regularly inspect and test safety guards, sensors, and other protective features to ensure they are functioning correctly.
- Hydraulic and Electric System Checks: For hydraulic or electric models, check the hydraulic fluid levels and electrical connections. Replace hydraulic fluid according to the manufacturer’s guidelines and inspect hoses for any leaks or signs of wear.
- Calibrate as Needed: Over time, the accuracy of the machine may decrease. Regularly calibrate the press brake to ensure that it continues to perform precise bends.
- Store Properly: When not in use, store the finger press brake in a dry, clean environment to prevent rust and damage from exposure to moisture or dust.
- Follow Manufacturer’s Maintenance Schedule: Adhere to the maintenance schedule provided in the user manual for regular servicing and parts replacement to keep the machine in optimal condition.
By performing these maintenance tasks consistently, you can extend the lifespan of your finger press brake, ensure its reliability, and maintain the quality of your bending operations.
Press Brake vs Finger Brake: What Are the Differences
1. Functions
Finger Press Brake
The finger brake is predominantly utilized for creating boxes, pans, channels, angles, and other similar objects of varying depths and sizes. It also has the capability of creating hemming, processing both open and closed hems and even lighter gauge hems.
The sheet metal finger brake bends the metal to over 130 degrees and then flattens the hem using the apron and presses it firmly against the top of the clamping rod. It is mainly utilized for bending simple workpieces or for prototype design and production.
This sheet metal brake can also be utilized for one-time sheet metal forming for automobile bodies and for HVAC workpieces, as it is capable of performing small, complex angle bends quickly.
Press Brake
In comparison to a finger brake, the press brake offers a wider range of advanced functions. Different types of press brakes all share common components, including a frame, workbench, ram, tooling, and driving device.
The driving mechanism of a press brake can be manual, mechanical, hydraulic, servo motor, or pneumatic, each producing different levels of bending force on the workpiece. As a result, press brakes come in various tonnage capacities, typically ranging from 40 tons to 1,000 tons.
This capacity to exert varying forces allows the press brake to bend plates of different thicknesses without causing damage to the machine. The length of the press brake's worktable determines the maximum length of the sheet metal that can be bent.
Smaller press brakes are suited for bending shorter plates, whereas tandem press brakes are designed for larger workpieces. The tooling of a press brake includes a variety of dies with different shapes and angles, such as punches (right angle, acute angle, obtuse angle, gooseneck) and dies (U-shaped, V-shaped, single-mode, double-mode).
CNC press brakes come with controllers that offer precise real-time control over bending angles and operations. The backgauge system, which features multiple axes, ensures a high level of accuracy for each bend. This advanced functionality allows the press brake to produce workpieces with complex and diverse shapes.
2. Structures and Working Principles
Finger Brake
The finger brake is mainly composed of a frame, a forming rod, and a clamping mechanism and is manually operated. The body is made of heavy steel and the steel plate structure ensures that the bending angle will not be affected, even under full load.
The machine also features super-heavy truss rods and supports for minimal deflection and powerful operation. The finger brake is equipped with an extended handle and an apron stop for repeated bending and a replaceable bushing to mitigate wear.
The key difference between the finger brake and the press brake is that its clamping rod is equipped with removable fingers. These fingers can be disassembled or rearranged to bend a metal plate or modify a part of the formed workpiece.
The finger brake is manually operated by the operator and can be operated by one or two operators, depending on the size of the workpiece. To complete the forming of boxes, pans, and other objects, the workpiece can be fixed using screws, rivets, welding, or other fixing processes.
To bend a sheet of metal, the clamping rod is opened by pushing the clamp handle to the back of the machine. The metal sheet is placed in the opening between the clamp finger and the work table, and the grip handle is pulled forward to fix the material in place. The baffle is then pulled up and the metal sheet is bent to the desired angle.
Press Brake
While there are various types of press brakes, their basic structures are largely the same, consisting of a frame, worktable, ram, tooling, electrical control box, and power system. CNC press brakes come with additional components, such as a controller, backgauge, light curtain protection, and a crowning device.
To operate a press brake, the sheet metal is positioned on the worktable and secured in place, after which the machine is activated. The upper die, driven by the ram, presses the metal sheet onto the lower die, then returns to its original position, completing one stroke.
The press brake functions through the combined operation of the controller and the operator, performing repeated bends. By interchanging various toolings, it can produce workpieces in different shapes and designs.
3. Press Brake vs. Finger Brake Comparison Table
Feature | Press Brake | Finger Brake |
Maximum Bending Force | Up to 3000 tons | Up to 50 tons |
Working Table Length | 4 feet to 40 feet | 2 feet to 12 feet |
Maximum Sheet Thickness | Up to 1 inch (25.4 mm) | Up to 0.25 inch (6.35 mm) |
Bending Angle Range | 0° to 180° | 0° to 135° |
Material Compatibility | Steel, Aluminum, Stainless Steel,etc. | Steel, Aluminum, Copper, etc. |
Control System | CNC, Manual, Hydraulic | Manual, Pneumatic |
Accuracy | ±0.01mm | ±0.1 mm |
Speed | Up to 20 bends per minute | Up to 10 bends per minute |
Tooling Options | Wide range of dies and punches | Adjustable fingers for custom bends |
Power Requirement | 220V/380V,3-phase | 110V/220V, single-phase |
Weight | 1 ton to 50 tons | 200 kg to 2 tons |
Application Scenarios | Large-scale manufacturing, automotive parts, heavy machinery components | Custom metal fabrication, small batch production, repair shops |
Cost | Higher initial investment and maintenance costs | Lower initial investment and maintenance costs |
Flexibility | High, suitable for complex and high-precision bending | High, suitable for frequent setup changes and custom bends |
Portability | Heavier, usually fixed installation | Lighter, easier to move and set up |
4. Performance Comparison Between Press Brake and Finger Brake
When comparing the performance of a press brake to that of a finger brake, several factors come into play, such as bending capabilities, precision, force, and versatility. Here's how these two machines differ in key areas:
- Bending Capacity:
- Press Brake: Capable of handling heavy-duty tasks, press brakes can bend thicker and longer sheets of metal. With tonnage ranging from 40 tons to 1,000 tons, they are designed to accommodate a wide range of materials, including steel and aluminum.
- Finger Brake: Generally suited for lighter tasks, finger brakes are used for smaller-scale projects. They are ideal for bending thinner sheets of metal, offering a more limited bending capacity compared to press brakes.
- Precision and Versatility:
- Press Brake: Equipped with CNC controls, press brakes allow for precise, repeatable bending and the creation of complex shapes. They can be used with various interchangeable dies and punches, enabling highly customizable and intricate bending operations.
- Finger Brake: While still accurate, finger brakes are more suited for simpler bends. The adjustability of the fingers makes it versatile for creating different lengths and angles, but it lacks the advanced control features of a CNC press brake.
- Force and Power:
- Press Brake: Press brakes, particularly those driven by hydraulic, mechanical, or electric power, generate significant force. This enables them to bend thicker materials and apply consistent pressure, making them more efficient for heavy-duty applications.
- Finger Brake: Typically manually operated, finger brakes rely on the user’s strength for applying pressure, making them less powerful. While they are suitable for small-scale projects, they cannot match the force generated by press brakes.
- Tooling Options:
- Press Brake: Press brakes offer a wide range of tooling, including V-dies, U-dies, and custom shapes, allowing for complex and diverse bending operations. The variety of available tools makes them adaptable to different tasks.
- Finger Brake: Finger brakes use simple tooling configurations, with adjustable fingers for creating standard bends. While versatile for basic operations, they don’t offer the same range of tooling options as a press brake.
- Automation and Efficiency:
- Press Brake: CNC press brakes are highly automated, offering advanced features like programmable controls, backgauges, and real-time bending adjustments. This automation improves both efficiency and accuracy, especially in large-scale production environments.
- Finger Brake: Finger brakes are typically manually operated, which makes them slower and more labor-intensive. While they are effective for custom, small-scale projects, they lack the automation and speed of press brakes.
- Portability:
- Press Brake: Press brakes are large and heavy machines, usually stationary in industrial workshops. Tandem press brakes are used for larger workpieces, but their size makes them less portable.
- Finger Brake: Finger brakes are compact and portable, allowing for easier transport and storage. This makes them ideal for contractors and professionals who work at various job sites or in limited spaces.
Conclusion:
Press brakes are better suited for industrial applications requiring high force, precision, and automation, especially when working with thick materials and large workpieces. On the other hand, finger brakes are more appropriate for small-scale, custom projects where portability and basic bending operations are the primary focus.
Applications of Finger Press Brake
Finger press brakes are versatile tools used in various metalworking applications. Their ability to provide precise and accurate bends makes them suitable for numerous tasks. Here are some common applications:
- Sheet Metal Fabrication:
- Finger press brakes are frequently used in sheet metal fabrication for creating custom parts and components. They are ideal for bending thin sheets of metal to form angles, edges, and other shapes required in metalworking projects.
- Prototype Development:
- In prototype development, finger press brakes are valuable for creating small batches of metal parts. Their precision allows designers and engineers to test and refine prototypes before moving on to larger production runs.
- Repair and Maintenance:
- For repair and maintenance tasks, finger press brakes are used to fabricate replacement parts or modify existing components. Their portability makes them suitable for on-site repairs or adjustments.
- Custom Metalworking Projects:
- Hobbyists and DIY enthusiasts use finger press brakes for custom metalworking projects. Whether building custom furniture, decorative items, or other metal objects, these brakes offer the precision needed for intricate designs.
- Architectural Metalwork:
- In architectural metalwork, finger press brakes are employed to create custom metal components for buildings and structures. This includes bending metal for decorative elements, structural supports, and architectural details.
- Automotive and Aerospace Industries:
- In the automotive and aerospace industries, finger press brakes are used for producing small metal parts and components. They are especially useful for creating precision parts for prototypes or limited-production runs.
- Signage and Displays:
- For creating metal signage and display structures, finger press brakes provide the ability to produce accurately bent and shaped metal components. This includes bending metal for letters, frames, and supports.
- Small-Batch Production:
- Finger press brakes are ideal for small-batch production where flexibility and precision are required. They allow manufacturers to produce various metal parts in limited quantities without the need for large, industrial machines.
- Art and Sculpture:
- Artists and sculptors use finger press brakes to shape metal into artistic forms and sculptures. The ability to make precise bends and adjustments is crucial for creating detailed and intricate metal art.
In summary, finger press brakes are a valuable tool for applications requiring precision bending of thin metal sheets. Their versatility makes them suitable for a range of tasks from prototyping and custom metalworking to architectural and artistic projects.
Which Is Better? Press Brake or Finger Press Brake?
Firstly, the press brake technology is more advanced compared to that of the finger brake. The finger press brake is primarily used for forming boxes, pans, and similar objects. Meanwhile, the press brake has multiple functions and is capable of performing various complex bending operations.
However, the cost of a press brake is significantly higher than that of a finger brake. If simple bending is all that is needed, there's no need to invest a large budget in a press brake. On the other hand, for complex and multi-functional batch bending operations, the press brake is the ideal machine.
The finger brake has a simpler operation compared to the press brake as it has fewer components and a straightforward design. However, its safety is lower than that of the press brake, so extra caution must be taken when using it.
Reviewed by 1 user
About the manual press brake very suitable for our small workhouse