Hydraulic shearing machine for metal play a crucial role in modern fabrication workshops, offering precision and efficiency in cutting various types of metal sheets. These machines are widely used due to their ability to handle large-scale production with minimal waste and high-quality results. In this article, we’ll explore the key features that make hydraulic shearing machines essential for metalworking, along with the numerous benefits they provide to fabricators.
What Is Hydraulic Shearing Machine for Metal
A hydraulic shearing machine for metal is used to cut sheet metal, bars, and plates by applying shear stress using a die and a punch, which is very similar to punching paper. The die and punch can have different shapes, such as circular or straight blades that resemble scissors. Shearing machines include punching machines for small discs, blanking machines for washer production, etc. Usually, shearing operations are used to split metals into sheets or strips. The type of blade used for shearing—a straight or rotatory edge determines the process of shearing a plate, sheet, or strip.
What is the Purpose of Metal Shearing?
Keeping chips from forming and eliminating burning or melting that can negatively impact metal die quality is the purpose of metal shearing. It’s excellent for suppliers of bronze and brass that work with sheets or plates, like Rotax Metals. It makes precise cuts without compromising the quality of the metal.
Classification of Shearing Machine
Shearing machines, along with other associated equipment, are utilized during the initial stage of metal sheet manufacturing, where they are responsible for cutting the metal sheets to the required size. These machines are highly versatile tools, capable of cutting through sheet metal and various alloys. Some shearing machines operate similarly to scissor blades, using angular shear motion to slice the metal into strips or sheets. In contrast, larger machines may employ straight shear action, where the blades are set at a fixed angle opposing the angular movement.
Typically, shearing involves two blades: one is stationary on the shear bed, while the other moves vertically with minimal clearance. The shearing handle moves gradually across the material from one side to the other. The term "rake" describes the angular arrangement of the blades, and both the clearance and rake are determined by the thickness and type of material being cut. In press-type shears, the angle between the upper and lower blades ranges from 0.5 to 2.5 degrees. In shearing machines, one of the blades is generally mounted on a fixed bed, with the workpiece secured in place by a series of hold-down pins. The cutting process is facilitated by a vertically moving crosshead.
How Shearing Is Performed
Shearing is performed by slicing through sheet metal with a blade-affixed machine or tool. Sheet metal is first secured between the tool’s or machine’s blades. Most shearing tools and machines have a squaring arm to control the location of the cut. After placing the sheet metal in the proper position with the squaring arm, the top blade drops to slice through the sheet metal. As the top blade comes down, the bottom of the sheet metal is pressed into a lower blade.
There are several types of shearing tools and machines, one of the most common being a bench shear. Also known as a lever shear, a bench shear is a cutting tool that’s mounted to a working surface, such as a workbench. It’s small, lightweight and easy to use, though it requires the use of a stable and secure surface for mounting.
Guillotine machines are also used to perform shearing. Also known as a power shear, it’s a more complex shearing machine that’s powered either mechanically or hydraulically. The powered blade allows guillotine machines to slice through sheet metal faster and more effectively than a bench shear.
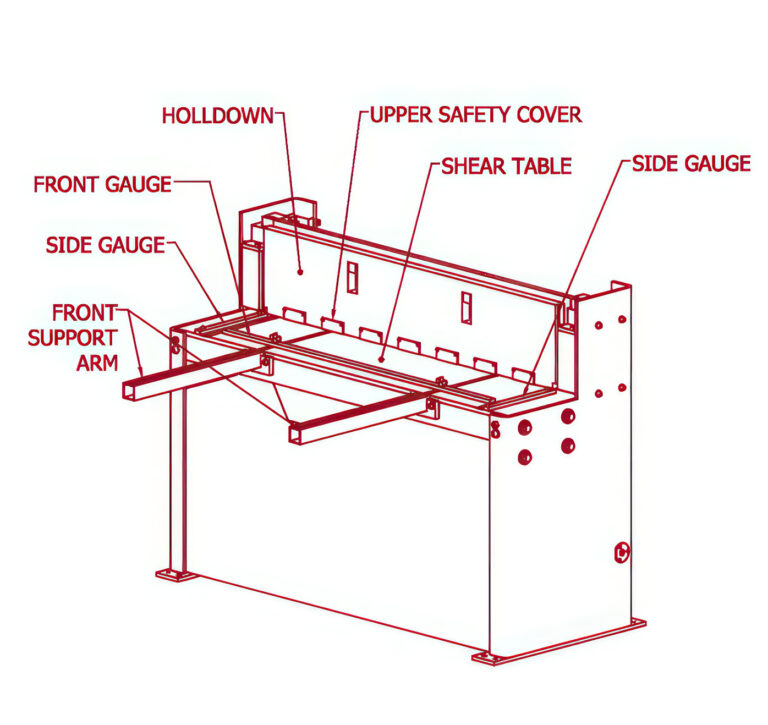
Diagram of Hydraulic Shearing Machine for Metal
The most popular shearing machine operation, punching, is used to scrap sheared slug. Shearing also takes place between a punch and a die. Punching, Cutting, blanking, Piercing, notching, Perforating, and nibbling are all part of the shearing operation.
1. Punching or Blanking:
Using a punch to remove material from a strip of sheet metal or a more significant piece is known as blanking or punching. Punching means removing small pieces; blanking means removing small scrap parts and the remaining helpful portion.
2. Cutting:
Very little excess metal is spread on the parting plane during drop forging or die-casting parts production. The extra metal, referred to as flash, is removed from the part during the trimming process before it is used. Blanking and trimming are similar processes, and the dies used in each process are similar.
3. Piercing
Piercing is the definition of tearing a hole in metal. Because slug is not generated during piercing, it differs from punching. A drilled hole resembles a bullet hole in a metal sheet rather closely.
4. Nibbling
Nibbling is a particular notching where the metal is sliced with overlapping notches. Nibbling is used to create any desired shape, such as flanges or collars.
5. Perforating
The process of creating a uniform spacing of holes in a metal sheet that can be any size or shape and cover the entire sheet is known as this.
6. Making a notch
Cutting a small amount of metal from a blank is known as notching. Because the cutting line of the slug touches one edge of the strip or blank during notching, it differs from punching. Any shape can be used for notches.
How Does a Hydraulic Shearing Machine for Metal Work?
Two essential parts make a metal shear work:
- The moving blade known as the punch
- The fixed blade referred to as the die
When activated, the punch pushes against the workpiece until clearance is achieved. This clearance typically ranges from 5% to 40% of the metal’s thickness.
The importance of clearance should not be underestimated—it directly influences cut quality and energy efficiency. If insufficient, there may still be some attachment between stock parts that require manual separation through prying. In contrast, excessive clearance can result in problems like rollover or heavy burring that damage delicate metals.
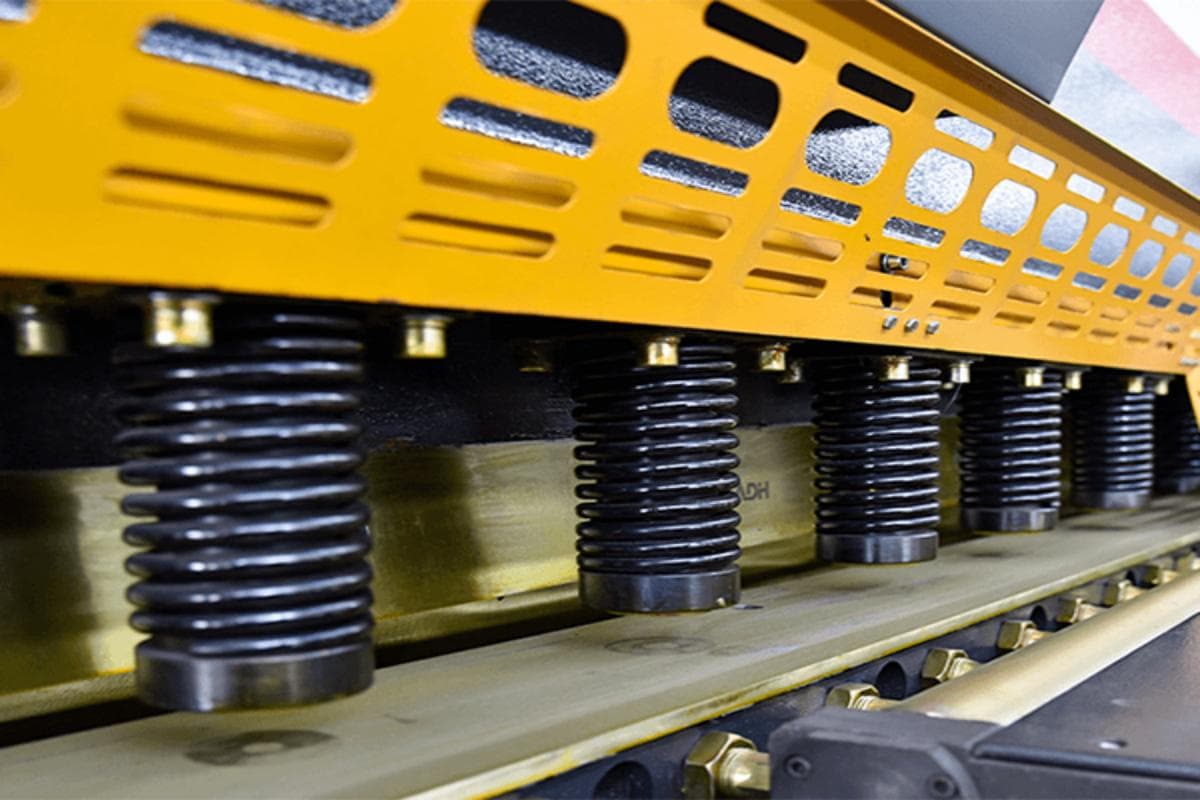
All Types of Hydraulic Shearing Machine for Metal
If you’ve ever wondered about the diverse world of metal shears, buckle up for a riveting exploration into the machinery that precisely shapes metal. Let’s dive into different types of shears used to cut metals, shedding light on each unique type and its distinctive strengths.
- Alligator Shear
Let’s kickstart our metal shearing expedition with the mighty alligator shear. Its hinged jaw resembling a powerful reptile makes this hydraulic marvel ideal for cutting l-beams, angle iron, and rebar. Powered by a hydraulic cylinder, the cutting motion is initiated by a piston extending to close the upper jaw alongside the bed gradually.
The alligator shear boasts cost-effectiveness, strength, and durability, making it a go-to choice for preparing scrap metal for shredding. However, its Achilles’ heel lies in occasional inaccuracy and a rugged finish. Despite these trade-offs, the alligator shear stands tall as a robust contender in metal cutting.
- Bench Shear
Mounted for mechanical advantage through a compound mechanism, bench shear is a craftsman’s delight. Ideal for shaping rough forms from medium-sized sheet metal, the bench shear flexes its muscles in various applications, from 90-degree angle cuts to T-sections. Besides, it effortlessly slices through both round and square bars.
The strength of a bench shear scales with its size, capable of withstanding the highest stresses. Broadly speaking, its efficiency and knack for producing clean cuts free of burrs make it an invaluable asset in metal shearing.
- Power Shear
The power shear takes center stage in the realm of blanking large pieces of sheet metal. It’s powered either electrically or pneumatically and operated by hand. This tool works magic with an upper blade moving towards a lower fixed blade, exerting tension on the cutting material. Its prowess lies in cutting straight lines or large-radius curves.
Flexibility, efficiency, accuracy, durability, and a top-notch quality finish are the key advantages that set power shears apart. Imagine the ease of maneuvering through curves, the efficiency of accurate cuts, and the durability to withstand metal fabrication demands.
- Throatless Shear
The throatless shear is perfect for crafting straight, intricately curved, or irregular cuts. It introduces a design innovation that allows free movement of the cutting material. Diverging from traditional models, this shear adds a layer of versatility to metal shearing tasks. Picture the freedom to move the material around, enabling precision in creating intricate shapes and cuts.
- Metal Guillotine
To talk about guillotines, we need to first understand how it’s set up. A guillotine comprises of:
- Shear table
- Work-holding device
- Gauging device
- Upper and lower shears
With a ram and blade, the metal guillotine clamps metal and cuts with precision. It can operate mechanically, hydraulically, or by footpower. Its strengths lie in speed and cost-effectiveness, making it ideal for high-volume production.
However, its biggest trade-off is that it has a tendency to produce a rough edge. These machines find their sweet spot in processing parts where aesthetics take a back seat or where the metal undergoes further refinement through welding. Safety measures are paramount when operating a metal guillotine, ensuring a smooth and secure metal-cutting process.
- Snips
Switching gears to precision in the palm of your hand, snips take center stage as hand tools designed to cut sheet metal. Divided into two types – tinner snips and compound action snips – these handheld wonders cater to different metal-cutting needs. Tinner snips, with long handles and short blades, excel in cutting low-carbon tin or mild steel.
Straight pattern tin snips are perfect for clean, straight lines or gentle curves. On the other hand, duckbill pattern tin snips handle sharper curves. There’s even a variety of tin snips, like circle and hawksbill patterns. They are ideal for cutting circles and radii, demonstrating the sheer versatility of these handheld tools.
Enter the compound action snip, a linkage-enhanced tool for cutting aluminum, mild steel, or stainless steel. With three types – straight-cutting, left-cutting, and right-cutting – these snips offer versatility in handling different cutting curves. Variations include
- Upright snips for tight spaces
- Long cuts snips for extended straight cuts
- Hard snips with head-treated blades for more rigid metals
Precision becomes the hallmark of snips, emphasizing their suitability for intricate cutting work. However, the labor-intensive nature of hand operation adds a layer of commitment to the metal-cutting process.
- Nibblers
In the realm of nibblers, where some mimic tin snips, most operate on a punch-and-die formation. Nibblers employ a blade moving in a line around a fixed die. It uses a series of up-and-down punching strokes to “nibble” away at the material and create precise cuts. Robust, durable, and capable of distortion-free cuts, nibblers operate with speed and low-force feed. Nibblers excel in tasks where precision is paramount, making them a reliable choice for metal artisans.
Metal shearing is a precise cutting process that plays a vital role across various industries, delivering efficiency, accuracy, and minimizing waste.
There are multiple types of shears used in sheet metal cutting. The hydraulic power of the alligator shear and the versatility of the bench shear are particularly notable. Additionally, the precision of snips and the speed of metal guillotines contribute to enhanced efficiency. Each type of shear is essential in the ever-evolving world of metal fabrication, as manufacturers seek the perfect cut for their projects.
At KRRASS Machinery, we take pride in offering a wide range of precision metal shears designed to elevate your metal fabrication process. Our advanced tools ensure exceptional efficiency, accuracy, and high-quality results for every project. Trust KRRASS to meet the demands of your metalworking needs.
Metal Shearing Advantages
- Incredibly fast, with shearing cutting through sheet metal in just seconds
- Creates clean cuts with smooth edges
- Can be performed on sheet metal in a variety of diameter sizes
- Cost-effective for high-volume manufacturing applications
- Doesn’t produce waste in the form of chips
- Can be performed on room-temperature sheet metal, eliminating the need for heating sheet metal
- Numerous types of metals support shearing, including aluminum, steel, stainless steel, bronze, iron and copper
Shearing Disadvantages
- Not ideal for low-volume manufacturing applications
- Exceptionally hard metals like tungsten cannot be sheared
- May cause deformity in sheet metal
Shearing vs Die Cutting: What’s the Difference?
Shearing and die cutting are similar metal fabrication processes that involve cutting metal with one or more blades. The two metal fabrication processes, however, use different types of cutting blades. In shearing, straight blades are used. In die cutting, curved blades are used.
What Is the Shearing Machine Mainly Used for?
The shearing machine provides efficient support for industrial production with its high-precision and high-speed cutting capabilities.
These machines are specialized tools used in industries such as machinery manufacturing, aerospace, and automobile manufacturing.
In the aerospace industry, for instance, the shearing machinery can be utilized to cut high-strength steel plates to produce aircraft parts.
The machine can also be utilized in the production of automobile components, such as bodies and doors, by cutting both steel and aluminum plates.
In addition to industrial applications, shearing machines are also used in various other fields, including household appliances, electronics, and building decoration.
For example, in the household appliance industry, the shearing machine is used to cut stainless steel plates for products such as refrigerators and air conditioners.
In the electronics industry, it can be used to cut aluminium plates for the production of computer and mobile phone shells.
What Are the Blade Materials of the Shearing Machine?
The blades of a shearing machine are typically made from materials such as high-speed steel, carbon steel, and other alloys. High-speed steel is a popular choice due to its excellent wear resistance and rigidity.
With its high stiffness, high-speed steel blades significantly boost the cutting efficiency of the shearing machine. When finely processed, these blades can also enhance the machine's shearing precision. In contrast, carbon steel is a more cost-effective blade material known for its high toughness.
The toughness of carbon steel blades makes them resistant to vibrations and deformations during cutting. Additionally, when subjected to heat treatment, carbon steel blades can also improve the shearing precision of the machine.
In summary, shearing machine blades can be made from materials such as high-speed steel, hard alloy, carbon steel, and others. The choice of blade material is determined by the machine's specific operating conditions and the available budget.
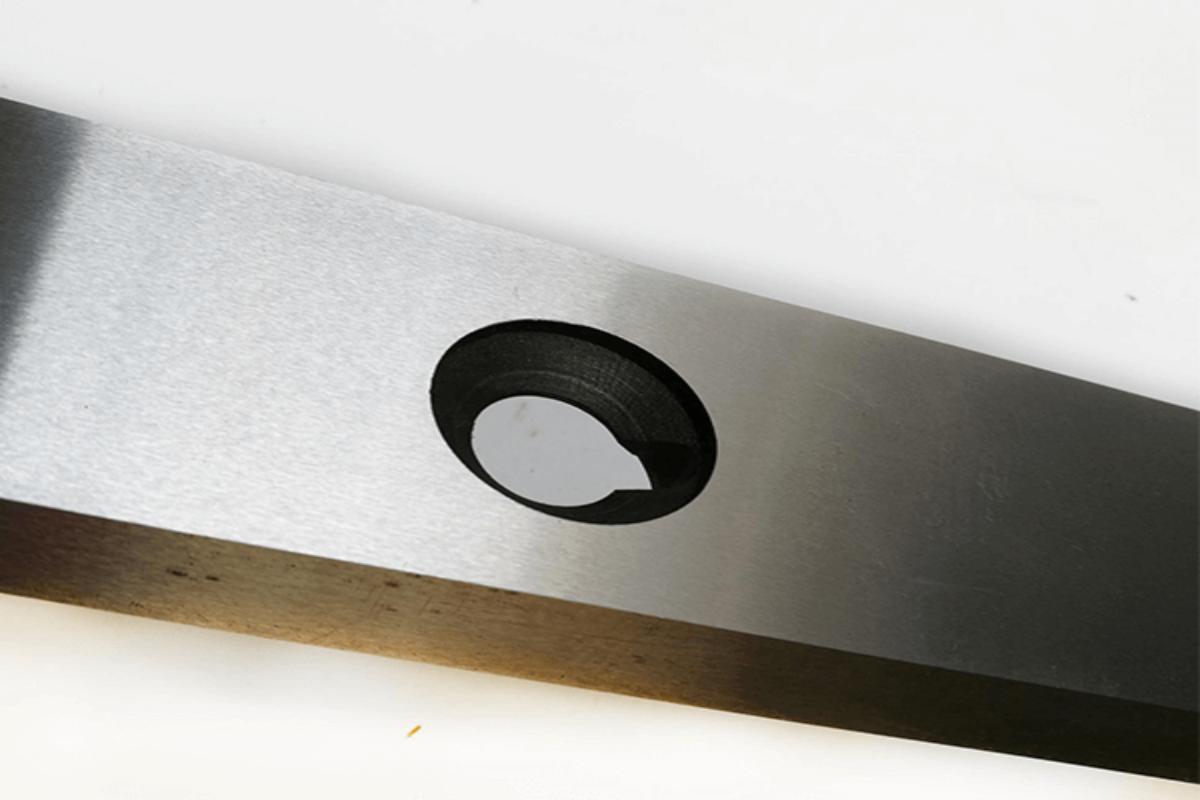
Conclusion
When selecting a hydraulic shearing machine for metal manufacturer, it's essential to carefully evaluate factors such as common machine prices, functions, warranty, and other important details.
KRRASS is a trusted sheet metal processing machine manufacturer with over 10 years of experience. The quality and performance of their press brakes, plate shearing machines, laser cutting machines, and other equipment are well-established and reliable.
Reviewed by 1 user
Appricate this, the shearing machine is great
We need this high-quality shearing machine to cut up our steel