Choosing the best plasma cutting machine for your workshop is essential for achieving precise, efficient cuts and maximizing productivity. Plasma cutting technology is widely used for cutting various types of metals, and selecting the right machine can significantly impact your workflow. Whether you are working with thick steel or thinner sheet metal, the right plasma cutter will ensure high-quality results while saving time and effort. In this guide, we’ll explore the key factors to
Introduction
Plasma cutters are highly effective welding machines that cut through conductive metallic materials with a jet of hot plasma. This process is accomplished at an extreme temperature and requires careful preparation to ensure the workstation, welding equipment, and personal safety protection is set up before you begin.
A plasma cutting machine is used for all types of metal fabrication projects, it’s commonly used in autobody shops, construction sites, sculptures, decorative panels for interior design, and salvage yards.
It’s a versatile machine that works by sending an inert gas through a torch, which produces an electric arc. This process forces the plasm through the tip of the torch to cut through metal. Plasma cutting creates an arc that can reach an extreme temperature of up to 45,000 degrees Fahrenheit. It’s one of the most effective and fast ways to cut metal.
When you choose a plasma cutter, it’s essential to get familiar with the different types of machines available and the various advantages they provide for your project. A plasma cutting system includes amperage settings that control the power available for cutting and an on/off switch. Once a plasma cutter is appropriately set up with the proper tools and equipment, it is a clean, safe, and effective way of cutting metal.
While plasma cutters are initially an expensive investment, they are available for rent, which makes them significantly more affordable and accessible for a wide range of projects and materials.
It’s essential to determine which type of plasma cutter is best for your home-based workshop, business, repair shop, or construction operation. This guide will provide you with all the details you need to consider when you choose a best plasma cutting machine for your workspace.
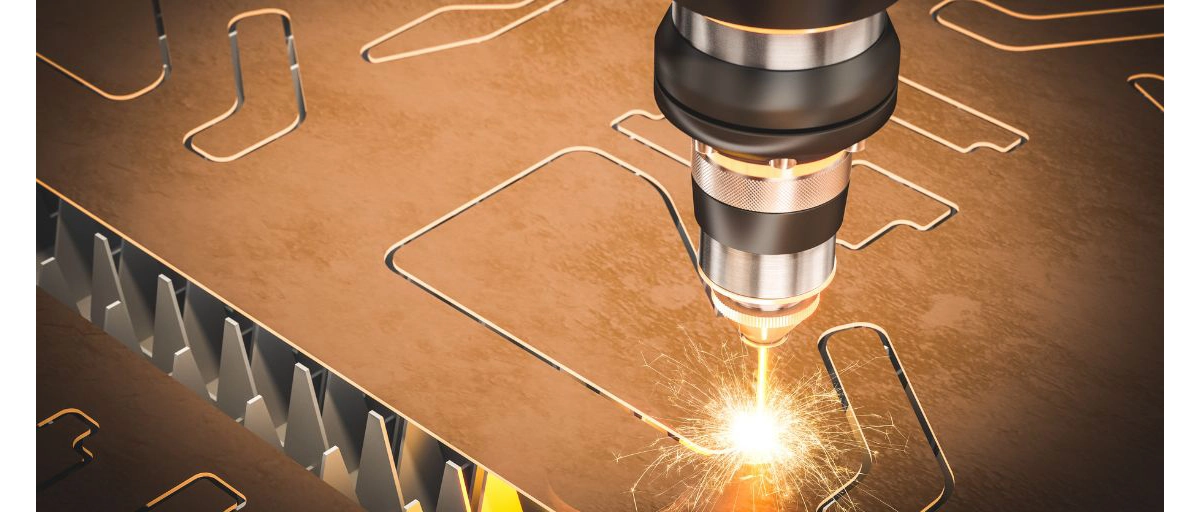
What is Plasma?
Plasma is the lesser-known fourth state of matter, alongside solid, liquid, and gas. It is a high-energy, ionized gas composed of atoms that have lost some or all of their electrons, resulting in a mixture of positively charged ions and free electrons. Plasma is created when a gas is subjected to extremely high temperatures or exposed to an electric current.
You can find plasma in various natural phenomena, such as lightning bolts, stars, and flames. It also plays a role in numerous industrial and medical applications, including plasma TVs, fluorescent lights, plasma cutters, and plasma torches.
What sets plasma apart from the other states of matter is its unique properties. Plasma can conduct electricity, interact with magnetic fields, and emit light.
What is Plasma Cutting?
Plasma cutting involves using a high-velocity jet of ionized gas to melt and cut through metal. Early plasma cutting systems utilized a straightforward torch design, which, while effective, had limitations in terms of cutting speed and accuracy. However, these systems quickly gained popularity due to their ability to cut through a wide range of metals and alloys.
Advancements in the 1970s led to the development of more sophisticated plasma torch designs, which improved both cutting speed and accuracy. The incorporation of computer control systems in the 1980s and 1990s further enhanced the precision and control of plasma cutting systems. Today, plasma cutting technology is widely used across various industries, offering precise and efficient metal cutting capabilities.
What Are Types of Plasma Cutters
While machined-controlled plasma cutting tables are designed for a particular process—fabricating metal—different types of plasma are utilized on various systems. Which plasma source is right for your CNC table depends on the products you manufacture and your work volume. Let’s review some common types of plasma:
Air Plasma
Air plasma tables are ideal for low-volume manufacturing and are often used on entry level steel fabrication machines.
Oxygen Plasma
Oxygen plasma offers a step up in quality from air plasma and is often utilized by mid-range fabrication shops.
High-Definition Plasma
For steel service centers and other shops specializing in high-volume processing, high-definition plasma is the optimal choice. This option also delivers the best quality fabrications.
CNC Plasma Cutters
CNC plasma cutters can produce repeatable quality cuts when compared to a handheld process. Indeed, these state-of-the-art burn tables are designed for impeccable craftsmanship and are therefore a vital resource for any kind of steel fabrication.
How Do They Work?
CNC stands for “computer numerical control” and is used to describe an automated process. Rather than risking damage to the material by fabricating freehand with a handheld torch, steel fabricators use CNC software to program a multi-axis bevel to perform the necessary work. Potential issues with the shape or profile can be identified in the software before fabrication begins, preventing wasteful mistakes. In fact, CNC systems often work in conjunction with CAM (computer aided machining) and CAD (computer aided design) software to deliver precise fabrications.
Impacts on Steel Fabricators
Not only can CNC plasma cutting tables improve the quality and output of work of every manner of steel fabrication, but it can also benefit fabrication shops in other ways. For instance, thanks to automated operation, these types of plasma cutters typically only require one technician to operate, helping to reduce labor costs. Some, particularly industrial-size tables designed for fabrication of oversized materials, can also minimize material handling, reducing the risk of damage to the raw product and improving safety in the shop.
Ten Things to Look for When Purchasing a Best Plasma Cutting Machine
Once you have determined plasma cutting is the right process for you, look at the following factors when making a buying decision.
Determine the Thickness of the Metal You Will Cut Most Often
One of the key factors to consider is the thickness of the metal you’ll be cutting most frequently. Plasma cutting power sources are typically rated based on their cutting capacity and amperage. For instance, if you primarily cut material that’s ¼" thick, a lower amperage plasma cutter should suffice. However, for cutting metal that’s ½" thick, a machine with higher amperage is recommended. While smaller plasma cutters might cut through thicker metal, the quality of the cut may suffer, resulting in a rough or incomplete sever cut with dross or slag. Each plasma cutter has an optimal thickness range, so it’s important to ensure it aligns with your needs. Generally, a machine designed for ¼" material provides around 25 amps of output, a ½" machine delivers 50-60 amps, and for cutting ¾" to 1" material, you would need a machine with around 80 amps of output.
Select the Ideal Cutting Speed
Are most of your cuts made in a production environment, or is speed less of a concern? When purchasing a plasma cutter, manufacturers typically provide cutting speeds for various metal thicknesses, measured in IPM (inches per minute). If you regularly cut ¼" metal, a machine with a higher amperage will cut through it faster than a lower-amperage model, even though both can handle the task. For production cutting, a general guideline is to choose a machine capable of cutting approximately twice the thickness of your standard material. For instance, to achieve fast, high-quality cuts on ¼" steel in a production setting, a 1/2" class (60 amp) plasma cutter would be ideal.
If you’re making long, continuous cuts or working in an automated setup, it's important to check the machine’s duty cycle. The duty cycle refers to how long you can continuously cut before the machine or torch overheats and requires cooling. It’s measured as a percentage over a 10-minute period. For example, a duty cycle of 60 percent at 50 amps means you can cut continuously for six minutes out of every 10. A higher duty cycle allows for longer continuous operation without breaks.
Can the machine offer an alternative to high frequency starting?
Most plasma cutters have a pilot arc that utilizes high frequency to conduct electricity through the air. However, high frequency can interfere with computers or office equipment that may be in use in the area. Thus, starting methods that eliminate the potential problems associated with high frequency starting circuits may be advantageous.
The lift arc method features a DC+ nozzle with a DC- electrode inside. Initially, the nozzle and the electrode physically touch. When the trigger is pulled, current flows between the electrode and the nozzle. Next, the electrode pulls away from the nozzle and a pilot arc is established. The transfer from pilot to cutting arc occurs when the pilot arc is brought close to the work piece. This transfer is caused by the electric potential from nozzle to work.
Compare consumable cost versus consumable life
Plasma cutting torches have a variety of wear items that require replacement, commonly called consumables. Look for a manufacturer that offers a machine with the fewest number of consumable parts. A smaller number of consumables mean less to replace and more cost savings.
Look in the manufacturer's specifications for how long a consumable will last - but be sure when comparing one machine against another that you are comparing the same data. Some manufacturers will rate consumables by number of cuts, while others will use the number of starts as the measurement standard.
Test the Machine and Evaluate Cut Quality
Conduct test cuts on several machines using the same cutting speed and material thickness to determine which machine delivers the best quality. Compare the results by inspecting the metal for dross on the underside and checking whether the kerf (the gap created by the cut) is perpendicular or angled.
Choose a plasma cutter that produces a tight, focused arc. For example, Lincoln Electric consumables are designed to concentrate the plasma swirl, resulting in a more precise arc and enhanced cutting power.
Additionally, perform a test by lifting the plasma torch away from the plate while cutting. Assess how far you can move the torch from the workpiece while still maintaining an effective arc. A longer arc indicates higher voltage and the capability to cut through thicker materials.
Pilot to cut and cut to pilot transfers
The transfer from pilot arc to cutting arc occurs when the pilot arc is brought close to the work piece. A voltage potential from nozzle to work is mechanism for this transfer. Traditionally, a large resistor in the pilot arc current path created this voltage potential. This voltage potential directly affects the height at which the arc can transfer. After the pilot arc transfers to work a switch (relay or transistor) is used to open the current path.
Look for a machine that provides a quick, positive transfer from pilot to cutting at a large transfer height. These machines will be more forgiving to the operator and will better support gouging. A good way to test transfer characteristics is by cutting expanded metal or gratings. In these instances, the machine will be required to quickly transfer from pilot to cut and back to pilot very quickly. To get around this, they may recommend you cut expanded metal using only the pilot current.
Check the machine's working visibility
As you are working on an application, you want to be able to see what you are cutting, especially when tracing a pattern. Visibility is facilitated by the geometry of the torch - a smaller, less bulky torch will enable you to better see where you are cutting, as will an extended nozzle.
Look for the portability factor
Many consumers use their plasma cutter for a variety of cutting applications and need to move the machine around a plant, job site or even from site to site. Having a lightweight, portable unit and a means of transportation for that unit - such as a valet style undercarriage or shoulder strap - make all the difference. Additionally, if floor space in a work area is limited, having a machine with a small footprint is valuable.
Also, you want a machine that offers storage for the work cable, torch and consumables. Built-in storage drastically improves portability since these items will not drag on the ground or get lost during machine transport.
Determine the ruggedness of the machine
For today's hard job site environments, look for a machine that offers durability and has protected controls. For example, fittings and torch connections that are protected will wear better than those that aren't. Some machines offer a protective cage around the air filter and other integral parts of the machine. These filters are an important feature since they ensure oil is removed from the compressed air. Oil can cause arcing and reducing cutting performance. Protection of these filters is important as they ensure oil and water, which reduces cutting performance, is removed from the compressed air.
Find out if the machine is easy to operate and feels comfortable
Look for a plasma cutter that has a big, easy-to-read control panel that is user-friendly. Such a panel allows someone who does not normally use a plasma cutter to be able to pick it up and use it. In addition, a machine with procedural information clearly printed on the unit will help with set-up and troubleshooting.
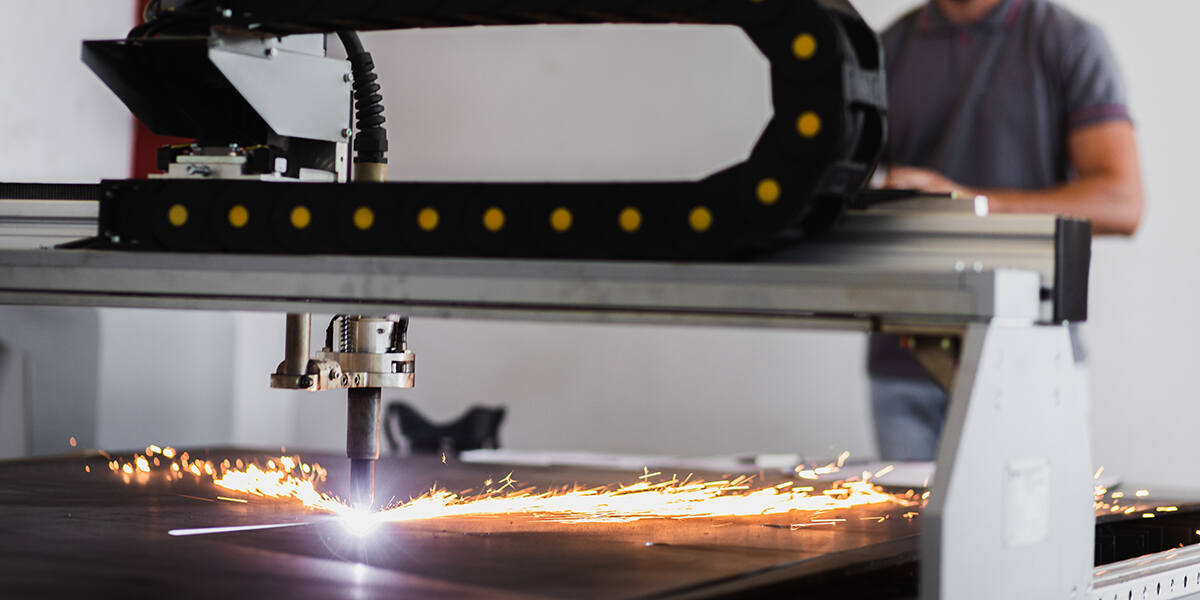
Assessing Your Plasma Cutting Needs
Before selecting the best plasma cutter for your project, it's crucial to evaluate your specific needs and determine which machine will be the most suitable. Consider the following factors to ensure you choose the right equipment for your workshop or business.
What type of work will you be performing with the plasma cutter? Plasma cutters are versatile tools capable of cutting through almost any metal, making them suitable for a wide range of projects. However, oxy-fuel cutters might also be a faster option for certain metals.
When deciding on a plasma cutter or similar welding equipment, keep these considerations in mind:
- Frequency of Use: Will you be using the plasma cutter for a one-time project, occasional tasks, or ongoing production for business or commercial purposes?
- Portability: Do you need a plasma cutter that can be easily moved between different locations, or will it be stationed in a single place?
- Power Source: Do you have access to a generator for powering the plasma cutter, or will you need a consistent power supply to support the equipment?
- Material Thickness: How thick is the metal you will be cutting? While plasma cutters are effective for various materials, some metals may be better suited for other types of cutting, such as oxy-fuel cutters.
- Electricity Consistency: Stable electricity is essential for optimal plasma cutting performance. Fluctuations in power can affect efficiency and productivity.
By understanding your available resources and the type of materials and tasks you plan to undertake, you can make a more informed decision about which plasma cutter brand and model will best meet your project requirements.
One notable distinction between brands is the specific features or styles they offer, which can enhance the functionality or convenience of the machine.
Some Questions About Plasma Cutter
What can I use a plasma cutter for?
Plasma cutting is ideal for cutting steel, and non-ferrous material less than 1 inch thick. Oxyfuel cutting requires that the operator carefully control the cutting speed so as to maintain the oxidizing process. Move too quickly and the cutting stops. Plasma is more forgiving. Plasma cutting shines in many niche applications, such as cutting expanded metal, which is awkward and slow with oxyfuel. Also, compared to mechanical cutting, plasma is usually much faster, and can easily make non-linear cuts.
How does plasma cutting compare to oxyfuel cutting?
Plasma cutting can be performed on any type of conductive metal – mild steel, aluminum and stainless are some examples. With mild steel, operators will experience faster, thicker cuts than with alloys.
Oxyfuel cuts by burning, or oxidizing, the base metal. It’s limited to steel and other ferrous metals that support the oxidizing process. Metals like aluminum and stainless steel form an oxide that inhibits further oxidization, making conventional oxyfuel cutting impossible. Plasma cutting, however, does not rely on oxidation to work, and thus it can cut aluminum, stainless and any other conductive material.
While different gasses can be used for plasma cutting, most people today use compressed air for the plasma gas. In most operations, compressed air is readily available, and thus plasma does not require fuel gas and compressed oxygen for operation. Some portable units also supply air from an on-board compressor.
Plasma cutting is typically easier for the novice to master, and on thinner materials, plasma cutting is much faster than oxyfuel cutting. However, for heavy sections of steel (1 inch and greater), oxyfuel is still preferred since oxyfuel is typically faster and requires lower capacity power supplies than plasma.
What are the limitations to plasma cutting? Where is oxyfuel preferred?
Oxyfuel may still be the preferred process for some applications. Plasma cutting machines are more expensive than oxyacetylene. Torch cutting also operates independent of electrical power or compressed air which may make it a more convenient method for some users. Oxyfuel can also cut thicker sections (>1 inch) of steel more quickly than plasma. In-plant users, however, can benefit from plasma technology using pre-existing shop services at little additional cost, while eliminating the consumable cost of oxygen and fuel gas, as well as the safety hazard associated with compressed gases.
Conclusion
KRRASS Machinery is your ultimate destination for all custom fabrication needs. We specialize in manufacturing heavy-duty CNC plasma cutting tables tailored to every type of steel fabrication. Our tables are customized to meet individual requirements, featuring options for air, oxygen, or high-definition plasma cutting. Additionally, our burn tables come with free and unlimited lifetime support. Contact us today to learn more about how we can assist with your fabrication needs by our best plasma laser cutting machine.