Our current economy is facing challenges, with rising material costs and freight expenses causing issues for manufacturers. As a result, many metal fabrication companies are looking for ways to increase capacity without the need for costly building expansions. One effective solution has been the rise of robotic press brake bending. Manufacturers are expected to prioritize operational efficiency and enhanced production capabilities, making robotic press brakes a game-changer.
By integrating advanced features, robotic press brake bending significantly boosts production rates and streamlines the entire manufacturing process. This technology helps manufacturers enhance accuracy and minimize setup times, leading to substantial gains in efficiency.
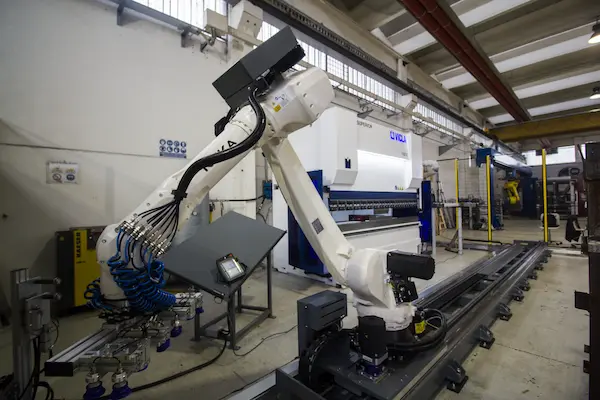
Enhance Your Bending Efficiency with Robotic Press Brake Bending
Robotic press brake bending systems offer metal fabricators a significant boost in productivity and efficiency. These advanced systems use robots to perform precise bending operations on metal sheets with press brake machines, which apply controlled force along a predefined axis to shape the material. By automating the bending process, robotic press brake bending enhances accuracy, safety, and speed while reducing reliance on manual labor and minimizing human error.
There are various types of robotic press brake bending systems, tailored to the size, shape, and complexity of the parts being processed. Some systems integrate standard robotic arms with existing press brakes, requiring offline programming and simulation for accurate bending operations. Other systems feature robots specifically designed for bending, capable of maneuvering around the tool zone to handle small and intricate parts. These systems often come with press brakes that have larger open heights, reducing setup time and increasing operational flexibility.
Why Transition to Robotic Automation for Your Press Brake?
Transitioning to robotic automation for press brake operations comes with numerous advantages that can significantly enhance efficiency and productivity.
- High-Volume Production: For jobs that consistently require the use of one press brake and operator, robotic automation can streamline operations and free up human resources.
- Repetitive Tasks: Tasks that involve high repetition are often unsuitable or unsafe for manual labor. Robotic systems can handle these processes, ensuring consistency and reducing the risk of injury.
- Intermittent Low-Volume Jobs: Robotic press brake systems can be programmed to manage low-volume jobs that occur sporadically, allowing for quick adjustments and efficient production without significant downtime.
- Handling Large Parts: When working with large components that are cumbersome or require multiple operators, robotic automation can simplify handling and ensure precision during the bending process.
Robotic press brake automation systems offer substantial benefits for manufacturers aiming to produce high-quality metal parts while keeping per-piece costs low. These systems are not limited to repetitive tasks; they can be easily programmed using offline tools for short-run applications, significantly reducing turnaround times while maintaining superior quality.
Midwest Engineered Systems specializes in custom-engineered robotic solutions designed to enhance your press brake operations throughout the metal bending process. Our robots are programmed for optimal placement and holding power, ensuring each part meets stringent quality standards.
What Are Robotic Press Brakes?
Robotic press brakes are advanced manufacturing systems that integrate robotic automation with traditional press brake technology to perform precise metal bending operations. These systems utilize robotic arms to handle and manipulate metal sheets, applying controlled force to bend them along predetermined axes, thus enhancing the efficiency and accuracy of the bending process.
Key Features of Robotic Press Brakes:
- Automation: Robotic press brakes automate the bending process, reducing the need for manual labor and minimizing the risk of human error.
- Precision: Equipped with sophisticated programming and control systems, these robots ensure high accuracy in bending operations, allowing for intricate and complex designs.
- Versatility: Robotic press brakes can handle various part sizes and shapes, making them suitable for a wide range of applications in metal fabrication.
- Increased Productivity: By streamlining operations, robotic press brakes can significantly boost production rates, especially for high-volume jobs or repetitive tasks.
- Enhanced Safety: Automating the bending process reduces the physical demands on operators, lowering the risk of workplace injuries associated with manual handling and repetitive strain.
- Flexible Programming: Many robotic press brakes can be programmed using offline tools, allowing for quick changes between different jobs and accommodating low-volume or short-run production with ease.
Applications of Robotic Press Brakes:
- High-Volume Manufacturing: Ideal for industries that require consistent production of metal parts, such as automotive and aerospace.
- Complex Part Fabrication: Suitable for tasks involving intricate designs that require precision and consistency.
- Custom Solutions: Manufacturers can customize robotic press brake systems to meet specific production needs, enhancing operational efficiency.
Robotic press brakes represent a significant advancement in metal fabrication technology, combining the strengths of robotics with traditional bending methods to achieve higher quality and efficiency in metalworking.
3 Pratical Uses of Robotic Press Brake Bending
Minimize Human Error with Robotic Press Brakes
Reducing manual interventions in your production process significantly lowers the chances of human error. Robotic press brakes contribute to this by offering several key advantages:
- Consistent Accuracy: A robotic press brake is fully programmable, ensuring that each part is produced with uniform precision. It can adjust itself to compensate for any operator mistakes, whether they use excessive or insufficient force.
- Quality Assurance: With robotic automation, you can expect high-quality parts every time, regardless of the operator's experience level. Even if a new operator makes an error, the robotic system can adapt, minimizing defects.
- Elimination of Fatigue: Unlike human operators, robots do not tire or become distracted. While a human operator might pause production for a break, a robotic press brake can operate continuously, ensuring consistent productivity without interruptions.
Boost Your Productivity with Robotic Press Brakes
Robotic press brakes significantly enhance your production capabilities. Traditional press brakes provide only one opportunity to form each part, bringing the metal sheet down to shape it.
In contrast, robotic press brakes are programmed to manipulate metal sheets efficiently without the need to reform them continually. This flexibility allows for the formation of multiple parts in a single operation without requiring adjustments after the initial part is created.
Additionally, robotic press brakes occupy the same footprint as a traditional press brake while maximizing output. They can run around the clock, programmed for optimal speed, which helps meet production deadlines effectively. This continuous operation ensures that your manufacturing process remains streamlined and responsive to production demands.
Produce Tighter Tolerances
Consistent tolerances are essential when manufacturing parts. If different parts have different tolerances, they may not work together correctly, reducing durability.
A robotic press brake allows you to set the exact pressure that forms each part, meaning you set tighter tolerances for each part.
If you're manufacturing something that must fit together perfectly, having tighter tolerances is critical.
A robotic press brake also reads the thickness of the sheet of metal and makes minor adjustments to compensate for any thickness variations: even if your sheet metal supplier has some slightly thicker or thinner sheets than others, the robotic press brake compensates.
Types of Robotic Press Brake Bending
Robotic press brake bending systems come in various configurations, each designed to meet specific manufacturing needs and requirements. Here are the primary types of robotic press brake bending:
Articulated Robotic Arms
- Description: These systems utilize multi-jointed robotic arms capable of extensive movement and flexibility.
- Advantages: Ideal for complex bending operations and can reach difficult angles and positions. They can handle a variety of part shapes and sizes.
Collaborative Robots (Cobots)
- Description: Designed to work alongside human operators, these robots can safely interact within the same workspace.
- Advantages: They can be used for tasks that require human oversight or assistance, providing flexibility in the production line while enhancing safety.
Delta Robots
- Description: Featuring a parallel link design, delta robots are known for their speed and precision.
- Advantages: Highly efficient for high-speed applications, making them suitable for high-volume production of small to medium-sized parts.
SCARA Robots
- Description: Selective Compliance Assembly Robot Arm (SCARA) robots have a rigid arm that can move horizontally and vertically.
- Advantages: Excellent for precise and repetitive bending tasks, particularly in applications where speed is essential.
Hybrid Robotic Systems
- Description: These systems combine features of traditional press brakes with robotic automation.
- Advantages: They offer the benefits of both systems, allowing for manual intervention when necessary while still providing the efficiency of robotic automation.
Specialized Bending Robots
- Description: Some robots are specifically designed for bending applications, equipped with specialized end-effectors and tools.
- Advantages: These robots are optimized for particular bending tasks, improving accuracy and efficiency in complex operations.
Integrated Robotic Press Brakes
- Description: These systems combine the press brake and robotic automation into a single unit.
- Advantages: They streamline the bending process, reduce the need for additional equipment, and enhance workflow efficiency.
Applications of Robotic Press Brake Bending:
- High-Volume Production: Perfect for industries like automotive, aerospace, and heavy machinery where consistent quality and speed are paramount.
- Complex Shapes: Suitable for manufacturers producing intricate parts that require precision and repeatability.
- Flexible Manufacturing: Ideal for facilities that handle a variety of part sizes and types, allowing for quick adjustments in programming.
Each type of robotic press brake bending system is tailored to specific production environments and requirements, making it essential to choose the right
Do You Need to AUTOMATE Your Press Brake?
If you said yes to any of these questions, Krrass robotic press brakes could be your solution to address key business challenges.
- Does your press brake sit idle during the day?
- Do you have a lot of quality variances and scrap?
- Do you lose time in downstream operations due to those quality shortcomings?
- Do you want to increase capacity overnight or during off shifts or run lights-out?
- Do you struggle to attract and retain skilled workers?
- Do your employees experience problems due to straining and repetitive motion?
- Are you concerned about operator safety around the press brake machines, especially when forming small parts?
Robotic Bending: Advantages and Limits
A robotic bending cell is a system that integrates a robot and a bending press, designed to perform operations of picking, bending, and depositing metal sheet profiles. It is a solution born out of the need for companies to make the production cycle more efficient while keeping production costs low without compromising quality.
The modern era of mechanical processes is characterized by a common thread: an increase in the level of quality in the repeatability of machining processes. In the field of sheet metal processing, continually improving productivity is one of the current major challenges, especially considering the growing variability in shapes, sizes, and quantities of pieces demanded by the market.
What are the possible solutions? As always, there is no one-size-fits-all formula, but there are options that better suit each individual company.
Robots and Innovations in Industrial Bending: Latest Developments
Bending automation has made significant strides compared to a few years ago, considering collaborative robots (cobots) or automated tool changer.
Before the advent of cobots and anthropomorphic robots, a Cartesian robot was used. This is a robotic arm that moves along a large steel frame positioned in front of the bending press.
Technological evolution in recent years has allowed freeing the robot from the elevated horizontal sliding beam, giving rise to the anthropomorphic bending robot.
Automation of Bending
The sheet metal processing sector is experiencing remarkable technological evolution, especially in the field of press bending. Traditionally, the bending phase has always been considered the bottleneck of the entire process because it is where the most significant waste occurs, both in terms of material and time.
Automated solutions act on two fronts: speeding up the bending cycle and reducing human error.
The automated bending cell relieves operators from strenuous, repetitive, and unstimulating work, allowing them to focus on other tasks.
Advantages of Robotic Bending
In the new smart factory, the programming phase of different processing stages is managed by the technical office, which becomes the true operational center of the workshop.
With everything controlled from a single location, the bad habit of having programs in the machine more accurate than the technical drawings or relying solely on the notes of the benders ceases.
Reduces Costs
By reducing the discretion of the human factor, costs can be reduced. Positive impacts include a reduction in material waste and a decrease in the production cycle (operators can focus on optimizing other production cycles).
Additionally, the work of people involved in other areas is expedited.
Lifts operators from repetitive, strenuous, and risky activities
Another aspect not to be overlooked is the safeguarding of the health of operators who, freed from taxing and dangerous activities, can engage in other tasks.
Operators can cease manual handling of large sheets, eliminate the risk of finger crushing during the bending phase, especially for very small pieces, and reduce risks and fatigue from manual tool changes.
Improves Job Estimation
Automation allows precise measurement of the time, material, and energy required to produce a piece. This enables more accurate quotations and eliminates the discretion of the human factor. How often does one base the price on skilled operators who are not always the same ones producing the piece?
Additionally, knowing in advance the timing, energy, and material, the company can make accurate forecasts of costs and revenues for the current year, improving the overall management of cash flows.
Robotic Bending vs. Manual Work
It is a common misconception to believe that automated bending will lead to the end of thousands of jobs. The same was said of the advent of the PC, but facts have shown that the introduction of new technology tends to have more positive than negative effects.
Bending automation will drive the development of human skills. New skills will range from machine maintenance to programming.
Thanks to the time saved, versatile figures capable of performing multiple tasks could emerge— for example, a laser cutter or a welder could learn to manage a robotic bending station much more quickly than a manual machine.
Limits of Robotic Bending
As with any other machinery, it would be wrong to think that a robotic bending cell can do anything.
These are application limits that must be known and explored before proceeding with the machinery purchase, so as not to end up dissatisfied with the investment made.
Looking at the issue from another perspective, the question to ask is: what factors should be considered when choosing an automatic bending system?
What kind of work do you do?
The essential prerequisite is that the work is repeatable, so it cannot include prototyping. This is because it makes no sense to invest time in programming a product that will be made only once and never again.
If a workshop regularly produces different parts for customers, however, the program can be easily recalled, and it might make sense to invest in a robotic bending cell.
Furthermore, to get the maximum benefit from an automated system, it is crucial to ensure maximizing the variety of operations that can be performed on it.
What are the best jobs for a robotic bender? Surprisingly, it covers a fairly wide range of applications:
- repeated high-volume jobs;
- low-volume jobs that are repeated;
- heavy jobs can all make sense.
Evaluate all costs
The cost of an automated system is certainly important, and it is undeniable that, for the same price, one could purchase one or more independent bending machines. However, the significant limitation of this reasoning is that, for each bending machine, an operator is needed. Are we sure the game is worth the candle?
When introducing an automated bending system, it is possible to optimize human resources as well. An experienced operator can manage an independent bending machine while monitoring a robotic cell.
Organize work and space
In addition to choosing the right-sized tooling, a workshop must also consider how the parts will be removed from the cell. Will they be assembled into kits, placed on a conveyor belt, removed via a chute, or stacked on pallets?
Decisions like these will influence the length and width requirements of the cell.
Always Monitor Production
It is a misconception to believe that merely programming in the technical office, hitting start, and waiting for the system to do all the work is sufficient. This oversimplification disregards the variables involved in sheet metal processing.
With a traditional bending machine, the operator can manually intervene to manipulate the piece and avoid potential collisions. In the case of a robotic system, the automated bending machine will only perform what it is programmed for, so the tool configuration must be precise.
A tool out of place could cause significant damage. It is crucial for the operator of the bending machine to ensure that every part is in its proper position because the robot cannot reposition the part to accommodate a misplaced tool.
In conclusion, working with a robotic bending machine requires meticulous attention to detail.
The Future of Manufacturing: Embracing Press Brake Automation and Robotics
As technology continues to evolve, the role of press brake automation and robotics in manufacturing will become increasingly vital. Here are some key trends shaping this future:
Enhanced Customization
Advanced automation and robotics will empower manufacturers to produce tailored products that meet specific customer needs, creating new market opportunities and differentiating them from competitors.
Sustainable Manufacturing Practices
Automated systems and robotic solutions can significantly reduce waste, conserve energy, and optimize the use of raw materials. This sustainability focus is becoming crucial for businesses committed to environmentally friendly operations.
Shifts in Workforce Skills
As automation and robotics become more prevalent, the workforce will need to acquire new skill sets. Robust training programs will be essential to prepare employees for the integration of these advanced technologies.
Increased Global Competitiveness
Companies that adopt press brake automation and robotics will gain a competitive advantage in the global marketplace. Improved efficiency, cost reduction, and the ability to offer customized solutions will position these businesses for success.
Conclusion
The future of manufacturing will be significantly shaped by advancements in automation and robotics. These technologies bring a multitude of benefits, including enhanced productivity, greater precision, reduced labor costs, and more sustainable practices. By leveraging innovations such as AI, IoT, Industry 4.0, and augmented reality (AR), manufacturers can develop smart factories that are not only efficient but also adaptive and environmentally conscious.
The success of manufacturing enterprises will increasingly depend on their willingness to embrace and integrate these technological innovations. Companies investing in automation and robotics will be better equipped to compete on a global scale, provide customized products, and meet the evolving needs of the workforce. Ultimately, the effective implementation of automated press brakes and robotics will define the future landscape of manufacturing.
Advanced technology by robotic arm to make bend easier