Laser cutting technology has revolutionized modern manufacturing by offering unparalleled precision and versatility, especially in metal fabrication. One area where laser cutters excel is in angle cutting, a technique that allows for intricate bevels and complex geometrical designs. Understanding how laser cutting angles can be optimized is essential for industries like aerospace, automotive, and precision engineering, where both efficiency and accuracy are critical. In this guide, we will explore the key benefits, techniques, and challenges of using laser cutting machines for angled cuts, highlighting how this technology enhances production processes and product quality.
Introduction
Overview of Laser Cutters
A laser cutting machine is a state-of-the-art tool designed for high-precision and high-efficiency material processing. Using a high-energy-density laser beam as its heat source, it precisely cuts through various materials with exceptional accuracy.
This non-contact cutting method is widely utilized across both metal and non-metal industries due to its unparalleled precision, flexibility, and adaptability. From intricate metal sheet designs to delicate non-metal materials, laser cutting delivers superior results that meet the diverse needs of modern manufacturing.
Controlled by computer programs, laser cutting systems are capable of creating complex two-dimensional and three-dimensional prototypes with speed and precision. This significantly boosts production efficiency while ensuring top-tier product quality, making laser cutting machines indispensable for industries that demand intricate designs and rapid fabrication.
Introduction to Laser Cutting Angles
In the laser cutting process, traditional cutting typically involves making straight or curved cuts that are perpendicular to the surface of the workpiece.
However, with advancements in technology and evolving industry requirements, modern laser cutting machines now offer the capability of cutting at an angle. This process, known as angled laser cutting, involves cutting materials at various angles rather than at a 90-degree angle to the surface. This technique opens up new possibilities that traditional cutting methods cannot achieve, offering innovative solutions for structural assembly, welding, and overall function optimization.
So, can laser cutters cut at an angle? Absolutely. Laser cutting machines are highly versatile, capable of making angled cuts to achieve intricate designs, precise bevels, and complex geometrical shapes, providing manufacturers with enhanced flexibility and precision.
Understanding Laser Cutting
Laser Cutting Process Explained
Laser cutting is a highly precise technique that uses a focused, high-energy-density laser beam to irradiate the surface of a material. This causes the material to melt, vaporize, or burn, allowing for its accurate separation or shaping.
The laser cutting process can be broken down into the following key steps:
- Dynamic Fabrication: Computer programs control the system, adjusting the position and power of the laser head in real-time according to the design path. This allows for continuous and highly accurate laser cutting, especially in complex designs.
- Focusing and Positioning: The laser system generates a high-intensity laser beam, which is focused into a fine spot using an optical system. This laser beam is precisely aligned with the target area, allowing for accurate cuts.
- Energy Transmission: The focused laser beam then works on the material’s surface at extremely high energy levels. This causes the material to rapidly absorb the energy, heating it to its melting point or boiling point in a very short time.
- Material Removal: As heat accumulates, the material begins to melt and vaporize. Simultaneously, assist gases like oxygen or nitrogen blow away the molten material or vapor, creating a clean and precise cut.
Materials Suitable for Laser Cutting Angles
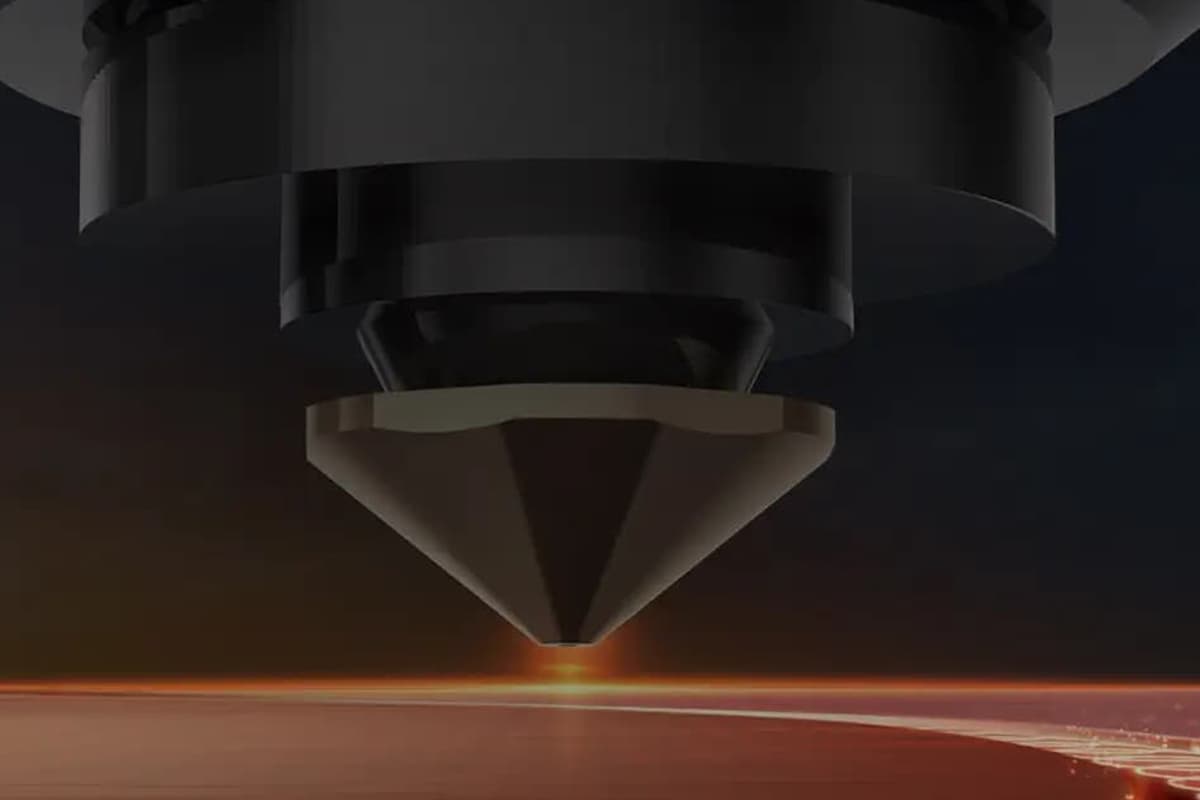
Thanks to its exceptional precision, flexibility, and versatility, laser cutting technology is widely used in various industries. Below are the typical materials suited for laser cutting:
- Composite Materials: Laser cutting is also ideal for processing composite materials such as carbon fiber composites, glass fiber reinforced plastics (GFRP), and other types of composite panels. By fine-tuning specific parameters, efficient cutting of these materials is achieved with minimal waste and maximum precision.
- Metal Materials: Laser cutting, especially with fiber laser cutting machines, excels in processing metals such as mild steel, stainless steel, aluminum, copper, and titanium alloy. These machines are highly effective in cutting thin to medium-thickness metal sheets with remarkable precision.
- Non-metal Materials: Laser cutting also works efficiently with non-metals like plastic, rubber, wood, paper, glass, ceramics, leather, and textiles. CO2 laser cutting machines are particularly effective in delivering high-quality cuts for non-metal materials, ensuring smooth edges and fine details.
Angle Cutting with Laser Cutters
Benefits of Laser Cutting Angles
Angle cutting with laser cutters offers several significant advantages, both in terms of functionality and design:
- Strengthening Structural Integrity and Stability: For engineering components like aircraft parts, bridge connectors, and joints, angle cutting helps to disperse stress more effectively, enhancing the overall stability and fatigue resistance of the structure. This is crucial for components subjected to high mechanical loads.
- Simplifying the Assembly Process: Pre-cutting parts at specific angles enables precise alignment during assembly. This reduces the need for post-cutting adjustments, streamlining welding and other assembly processes, ultimately improving both efficiency and accuracy.
- Material Savings and Design Optimization: Angle cutting allows for better adaptation to complex geometric shapes, reducing material waste. By optimizing the use of remaining materials, laser angle cutting improves resource utilization, which is a key factor in sustainable manufacturing.
- Artistic Beauty and Customization: In decorative architecture and artistic metalwork, angle cutting delivers distinctive visual effects, adding depth and complexity to designs. This capability supports personalized and innovative creations that elevate aesthetic appeal.
Applications of Laser Cutting at an Angle in Various Industries
Angle cutting with laser cutters is crucial across numerous industries, providing tailored solutions that enhance product performance and design. Here are some key applications:
- Aerospace Industry: In aircraft manufacturing, the need for mass oblique joint designs is essential to strengthen the rigidity of the body structure while reducing weight. Angle cutting plays a pivotal role in achieving these designs, ensuring both structural integrity and performance.
- Automotive Manufacturing: Precision is paramount in automotive components, such as body structural parts, interior components, and engine parts. Accurate angle cutting ensures a tight fit between these parts, facilitating efficient production and enhancing overall vehicle safety and performance.
- Architectural Industry: Complex node connectors in steel structures often require precise angle cutting to meet both mechanical performance standards and aesthetic requirements. This technique allows for innovative designs while maintaining the necessary strength and durability.
- Furniture Manufacturing: Creative furniture design frequently involves angle cutting to achieve unique appearances and stable structures. By incorporating angled cuts, designers can create visually striking and functional pieces that stand out in the market.
- Electronic and Precision Instrument Manufacturing: In this sector, angle cutting is essential for producing small, delicate metal shells and internal brackets. This process improves packaging density and thermal performance, leading to more efficient and reliable electronic devices.
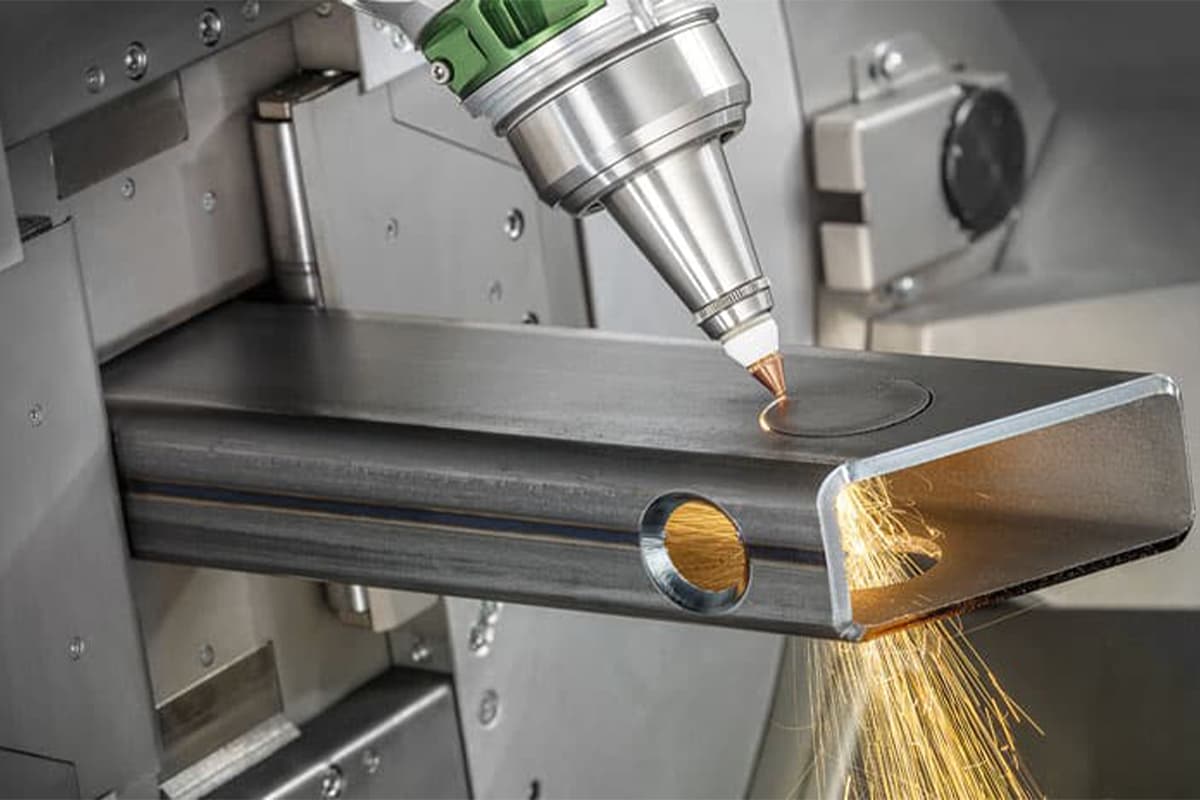
Factors Influencing Laser Cutting Angles
1. Material Considerations
The properties of different materials significantly affect the effectiveness of angle cutting with laser cutters. For instance, materials with high melting points or reflective surfaces can present challenges when cutting at angles. Understanding the specific properties of the materials being used is essential to ensure compatibility with laser cutting machines and achieve optimal results.
2. Thickness Limitations
The thickness of the material is a crucial factor in the effectiveness of angle cutting. Thicker materials may require higher power settings and slower cutting speeds to achieve clean, precise cuts. It’s important to consult the specifications and guidebooks of the laser cutting machine to ensure it can accommodate the maximum thickness while performing angle cuts effectively.
3. Beam Divergence
The divergence of the laser beam during propagation is another key factor influencing angle cutting. A more concentrated laser beam results in a smaller focused spot diameter and higher energy density, which can enhance precision in angle cutting. However, beam divergence can cause the focus points to offset when cutting at larger angles, potentially affecting cutting precision and efficiency.
4. Lens Focus
The choice and adjustment of lens focal length are vital for achieving high-quality angle cuts. In a laser cutting machine, the lens focal length can be adjusted to control the location and depth of the laser point, thus altering the energy distribution on the material's surface. To maintain optimal energy density and cutting effectiveness during angle cutting, it’s beneficial to dynamically adjust the lens focal length according to the specific cutting angle.
Techniques for Laser Cutting at an Angle
1. Bevel Cutting with Laser Technology
Bevel cutting involves adjusting the angle and focal length of the laser head so that the laser beam interacts with the material surface at an angle, creating a ramped edge on the workpiece. This technique is widely utilized in various applications, such as tubes, welded joints, and frame structures, as it pre-creates optimal welded angles for parts. This enhances both welding quality and efficiency, making it an essential method in metal fabrication.
2. Tilt Cutting Methods
Tilt cutting technology involves positioning the workbench or laser head at a specific angle rather than perpendicular to the workpiece surface during the cutting process. This method allows for the creation of cuts at different angles in a single operation, making it particularly effective for manufacturing components that require precise angular configurations. By minimizing subsequent processing steps, tilt cutting significantly boosts production efficiency, especially for specialized design products such as architectural decorative elements and furniture components.
3. Rotational Cutting Approaches
In advanced laser cutting systems, rotational cutting technology is employed, enabling the laser cutting head to move along the X-Y axis while also rotating around the Z-axis. This capability allows for changes in the incident angle of the laser beam throughout the cutting process. Rotational cutting is particularly suited for producing intricate three-dimensional geometrical shapes, such as aviation blades, turbine components, and artistic engravings. This flexibility meets the diverse cutting needs for various angles and curved lines, enhancing design possibilities.
Challenges of Laser Cutting Angles
1. Heat Distortion Issues
When cutting at an angle, particularly with thicker or heat-sensitive materials, the high temperatures generated by the laser beam can create uneven heat distribution across the workpiece. This thermal deformation may compromise the precision of the cutting edge, leading to defects such as slag, burrs, and changes in internal stress within the metal due to overheating. As a result, the final product quality can be adversely affected.
2. Material Warping Concerns
Thin sheet metals and other materials susceptible to heat can experience warping or twisting as heat accumulates during angle cutting. The cooling shrinkage process may cause irreversible shape changes, particularly when working with large angles and deep incisions. This deformation complicates subsequent fabrication processes and can hinder the performance of the final product.
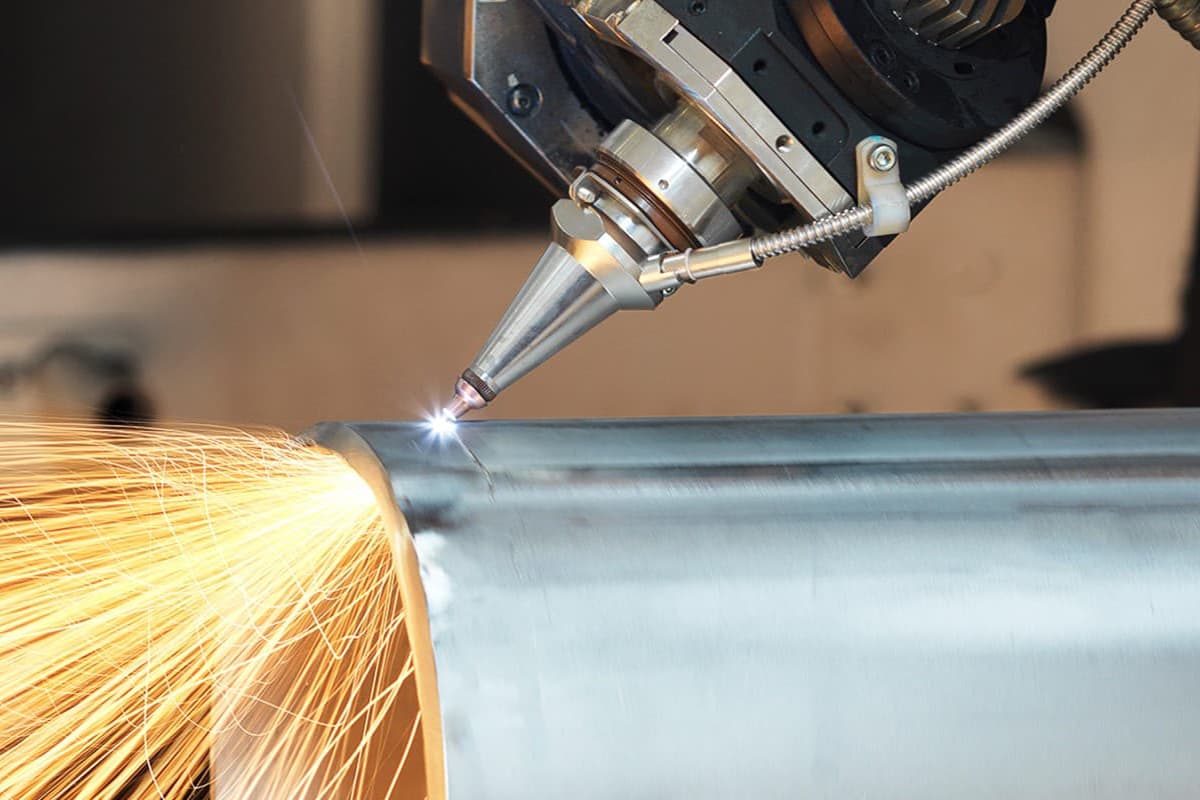
3. Overcoming Limitations in Angle Cutting
To mitigate these challenges, several strategies can be employed:
- Dynamic Focus and Power Control: Adjusting the laser focus point and input power in real-time ensures even energy distribution. This approach decreases the heat-affected zone, minimizing the risk of thermal deformation.
- Optimization of Assist Gases: Utilizing the appropriate assist gases, such as nitrogen and oxygen, enhances the blowing effect on molten material, accelerates the cooling process, and reduces the likelihood of warpage.
- Multiple-Axis Linkage Technology: Employing a laser cutting machine with multi-axis linkage allows for greater flexibility in adjusting the angle and position of the laser head. This capability facilitates complex and precise angle cutting while better controlling heat input to prevent workpiece deformation.
- Pre-Cooling and Post-Treatment Processes: Implementing pre-cooling methods for the workpiece or rapid cooling techniques after cutting helps manage the temperature, significantly reducing the occurrence of heat distortion.
Conclusion
In summary, the ability to perform angle cutting with laser technology has become increasingly significant in modern manufacturing due to its notable advantages. This technique ensures high precision and accuracy, effectively meeting the complex angle-cutting requirements found in industries such as aerospace and automotive manufacturing, as well as other sectors that demand precision components.
When compared to traditional cutting methods, laser cutting at an angle excels in both time efficiency and cost-effectiveness. The automatic control and high-efficiency fabrication processes significantly reduce production costs while enhancing overall operational efficiency. Additionally, this method minimizes material waste, maximizing resource utilization and promoting sustainable production practices.
Despite the challenges posed by heat deformation and material warping, advancements in technology—such as dynamic focusing, intelligent control systems, and the development of composite processing techniques—are addressing these issues. These innovations are continually expanding the applications and capabilities of laser angle cutting.
For more information about laser cutting machines and their benefits, please visit our official website or contact our sales team for further details.