You know how fiber laser cutting technology has shaken up the sheet processing world? Well, bending techniques of press brake has its own story of progress and little details that are just as interesting.
It's a super important technique in metal fabrication. It's like the magic that turns plain metal sheets into all kinds of cool and useful designs. Let's dig into the nitty-gritty of press brake bending and use examples from the laser tech world to really understand how this bending thing works.
What's the Deal with Press Brake Bending?
Think of press brake bending as the heart of metal fabrication, kind of like how the resonator is key in laser technology. Basically, it's a process where a press brake uses punches and dies to push and shape sheet metal into whatever shape you want. This is a must-have in manufacturing and production because it turns those raw metal sheets into actual useful parts.
The Different Types of Press Brakes
Press brakes come in all sorts of flavors, and each one has its own perks. It's a bit like how different laser generators do different jobs:
- Hydraulic Press Brake: This one's like the Swiss Army knife of press brakes. It runs on hydraulic oil and has two synchronized cylinders that work together.
- Mechanical Press Brake: It's all about that flywheel, crank mechanism, and clutch. It's super fast and efficient when it comes to bending.
- CNC Press Brake: Computer power makes this brake super precise and programmable.
Here's what sets them apart:
- Power Source: You've got hydraulic oil, mechanical force, or computer controls.
- Precision: CNC press brakes usually win in the accuracy department.
- Speed: Mechanical press brakes are often quicker than the hydraulic ones.
Bending Techniques of Press Brake
In the world of press brake work, there are different ways to get the job done, just like there are different paths for a laser beam. Some are all about precision, and others are more about speed:
Bottoming: Pushing to the Limit
Bottoming, or bottom bending, is when you really push that sheet metal down until it hits the bottom of the die. Here's what you need to know:
- High Force: You're using a lot of pressure to make sure the metal gets all the way to the bottom.
- Precision: This method gives you really accurate bends, especially when you know the material thickness and it's consistent.
- Bend Deduction: This is super important in bottoming. It helps account for that springback and figure out the actual bend angle.
Air Bending: Simple and Flexible
Air bending is a favorite for a lot of operators. The metal sits on the die, and the punch comes down to create the bend. Check out these cool things about it:
- Variable Angles: Since the metal doesn't touch the die's side walls, you can get all kinds of angles with just one V die opening. That gives you a lot of flexibility.
- Less Force Needed: Compared to other methods like coining, air bending doesn't need as much force. That's why it's popular for hydraulic press brakes.
- Material Matters: The type of material, its thickness, and the grain direction all have a big impact on the final result.
Coining: Shaping with Force
The coining method is all about showing off the power of the press brake. You apply a ton of force to make the metal fit the die's exact shape.
- Dimensional Accuracy: Coining makes sure the sheet metal is a perfect match to the punch and die shape.
- Less Springback: With all that force, the metal doesn't spring back as much, so you get more consistent results.
- Machine Demands: But be careful, because this method needs a lot of bending force. If you don't take care of the machine, it might not last as long.
Three-Point Bending: Predictable and Efficient
Three-point bending is known for being reliable and consistent. The punch and die have three contact points that give you a steady bend.
- Consistent Radius: No matter how the material thickness changes, you get a stable bend radius.
- Efficiency: This process saves time because the punch doesn't have to go all the way down on the workpiece.
- Less Tool Wear: Because it's so controlled, the tools and dies don't wear out as fast.
Rotary Bending: A Different Approach
Rotary bending is a bit of a rebel. Instead of using regular punches and dies, it uses rotating tools.
- Less Surface Damage: The metal moves against the rotating tool, so there's less chance of scratching the surface.
- Faster for Complex Bends: This method really shines when you're dealing with tricky bends or a lot of pieces.
Folding: Bending Back on Itself
Folding is all about bending the metal so it folds back on itself. It's not just about the bend, but also how the whole process works.
- Versatile Material Handling: You can use it for different material thicknesses and types.
- Precision: The accuracy of the fold depends on the back gauge, where it's positioned, and the CNC controller that's running the press brake.
Tools for the Job
Just like a good laser beam is crucial for laser cutting, the tools in press brake bending are key to getting the results you want:
- Punches: These are the upper tools that push the metal sheet into the dies.
- Dies: The lower tools that give the metal its shape when the punch pushes.
- Backgauges: These help position the metal sheet perfectly for the bend.
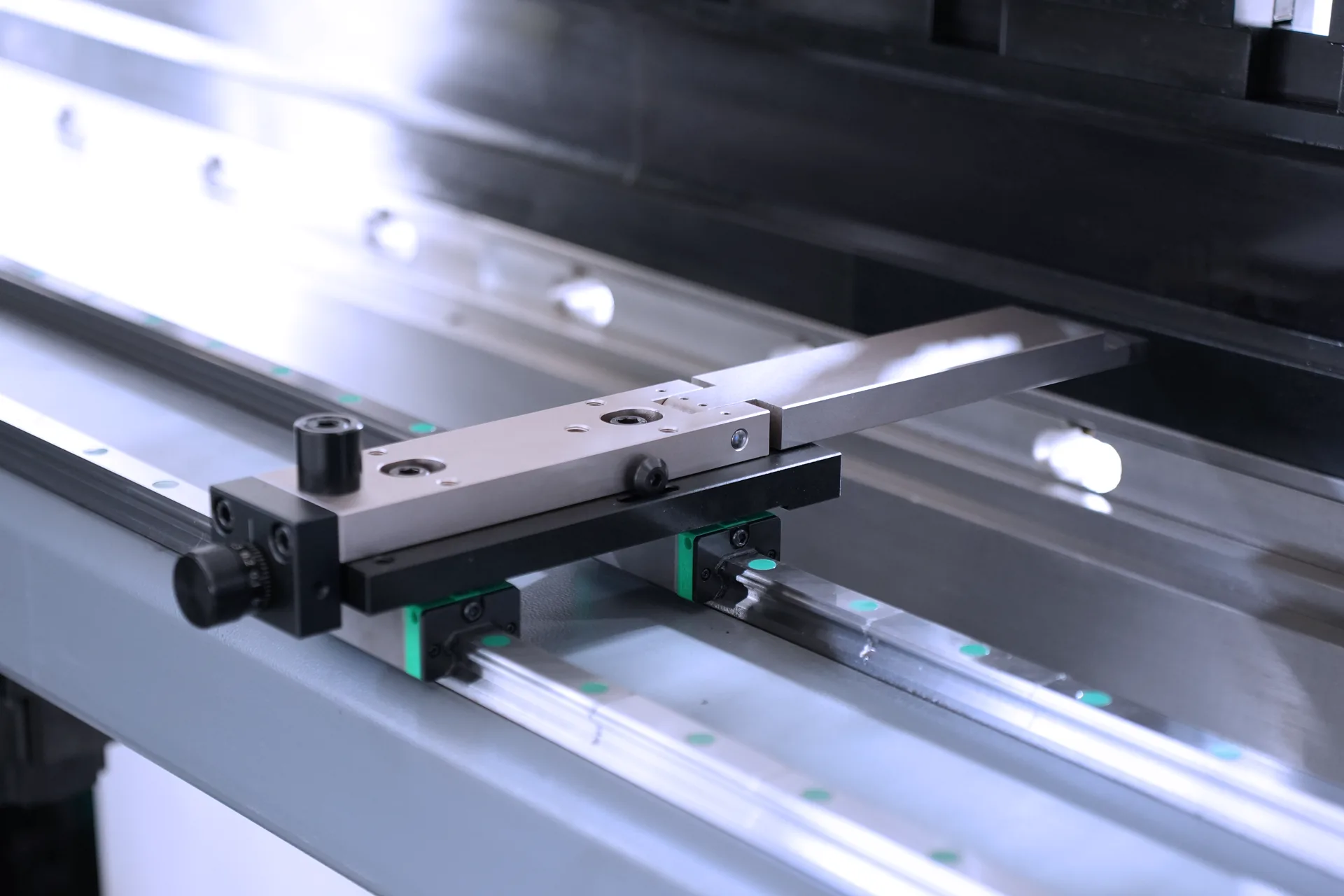
Common Mistakes and How to Avoid Them
Making mistakes in bending is like losing power in a laser beam - it's not good. Here are some common problems and how to fix them:
Over-bending: Too Much of a Good Thing
Over-bending happens when you use too much force during the press brake work. It's like when you use too much power with a laser beam - it can mess things up.
When you're bending sheet metal, you need to be precise. The material thickness, the type of metal, and the angle you want all matter when it comes to how much force to use. Here's why over-bending might happen:
- Wrong Force Calculation: You might not have estimated the right amount of force based on the material thickness and bend radius.
- Lack of Knowledge: You might not know which bending method is best for the metal you're using, like air bending or bottom bending.
- Bad Equipment Settings: You might not have set the press brake machine correctly for the workpiece.
Operators need to really understand their machines and the materials they're working with. By using the right amount of force and checking the machine often, you can avoid over-bending.
Tooling Problems: Picking the Right Tools
Choosing the wrong punch and die is like picking the wrong resonator for laser work - it can ruin your results. The punch and die are super important in press brake bending, just like the laser is in cutting. They decide how precise and good the work will be.
If you pick the wrong tools, you might end up with:
- Deformation: The sheet metal could get distorted and you'll have to waste time and materials fixing it.
- Inconsistency: Different metals and material thicknesses need different tools. If you use the same tool for everything, you'll get different results every time.
One way to solve these problems is to use a CNC controller. Modern press brake machines usually have one, and it can help you pick the right tools based on things like the material type, thickness, and the bend angle you want. Using technology can really cut down on tooling errors.
Springback: Dealing with Metal's Memory
Metals, especially ones like carbon steel that we use a lot in fabrication, like to spring back a little after bending. This is called springback, and it can mess up your press brake work.
To understand springback, you need to know:
- Material Ductility: Some metals are more likely to spring back because of how stretchy they are. Knowing this helps you guess how much springback to expect.
- Bending Methods: Different techniques like coining or air bending affect the workpiece differently and can change how much it springs back.
To stop springback from ruining your work, operators need to plan for it. Using tools and technology that can predict springback, along with your own experience, can help you get the final bend angle and shape just right.
Handling Materials: Keeping Them Safe
Taking care of the material during the bending process is really important. Think of the sheet metal like the delicate surface of a laser lens - if you're not careful, you can damage it.
Press brake operation depends on:
- Safe Movement: Using things like back gauges to put the sheet in the right place under the press brake ram.
- Protecting from Outside Stuff: Making sure the worktable and tools are clean and free of anything that could scratch or damage the surface.
Consistency is Key: Force and Results
If you don't apply the bending force evenly, it's like having a laser beam with changing power - you won't get the results you want. For press brakes to make consistent bends, you need to apply the force evenly across the workpiece.
Here's what can affect this:
- Machine Calibration: Checking and adjusting the press brake machine regularly makes sure it gives the right force all the time.
- Operator Training: Operators need to know how important it is to apply the force evenly and be able to spot when it's not.
Safety First: Don't Skip the Rules
Just like any other big machine in metal fabrication, press brakes can be dangerous. Ignoring safety rules is a really bad idea when you're using a press brake - it can lead to serious injuries.
Here are the safety things you need to think about:
- Easy Access to Emergency Stop: Make sure the emergency stop button is easy to reach and works.
- Regular Maintenance: Keep the press brake and all its parts in good shape to avoid sudden problems.
- Operator Training: Every operator needs to know the machine's safety features and why it's so important to follow the rules.
Essential Safety Steps
Just like we care about laser safety, when you're using a press brake to push metal with a lot of force, you need to be really careful. A well-maintained brake is like a well-calibrated laser - it keeps you safe:
Training and Certification: Why It Matters
It's no secret that trained and certified operators do a better job. When you're working with hydraulic press brakes and bending sheet metal, knowing what you're doing is super important. Understanding all the details of the bending process, from the bend radius to the material thickness, makes a big difference in the final product.
- Know Your Machines: Operators should be familiar with different types of press brakes and what they can do.
- Understand Bending Methods: From air bending to bottom bending, a trained operator knows which one to use for the best results.
- Material Know-How: Recognizing the differences in metals and their properties helps you use the right amount of force when bending.
Regular Machine Maintenance: Keeping It in Shape
Think of a press brake machine like a musical instrument - it needs regular care to sound its best. There are similarities between a CO2 resonator and a press brake. Both need careful attention to work well.
- Longer Life: Checking on the machine regularly can make it last a lot longer.
- Avoid Downtime: Maintenance catches problems before they get big and saves you production time.
- Precision Guaranteed: Keeping the press brake in good condition means you get accurate and consistent bends.
Personal Protective Equipment (PPE): Staying Safe
Working with a press brake isn't without risks, so wearing the right PPE is really important. Each piece of equipment has a job and protects you from different dangers in press brake work.
- Shields: These are really important for keeping you safe from flying bits and pieces during bending.
- Safety Glasses: You need these to protect your eyes from any small particles or bits that might break off.
- Gloves: They keep your hands safe from cuts, heat, and other hazards.
Clear Work Zones: Less Mess, More Success
In the busy world of metal fabrication, having a clean and organized workspace is key. The area around the press brake should be clear of anything that could get in the way of the bending process or be dangerous.
- Prevent Accidents: A tidy zone means fewer chances of tripping or things falling and causing accidents.
- Work Faster: When everything is in its place, you can work more efficiently because you can find tools and materials easily.
- Reduce Waste: Keeping things organized helps you waste less, which makes everything run smoother.
Proper Material Handling: Treating Materials Right
Whether you're working with carbon steel sheets or other metals, you need to handle them carefully. How you store and move them can really affect the final product.
- Safe Storage: Stack materials in a way that they won't fall over or get damaged.
- Easy Transportation: Use things like trolleys to move heavy sheet metal and avoid getting hurt.
- Keep Quality: Handling materials the right way makes sure they stay in good shape and don't get dents or deformations.
What Affects Bending Accuracy
Getting the perfect bend is like getting a super precise laser cut. There are a lot of things that can change the final result:
- Material Type and Thickness: Different metals and how thick they are can change the bend angle.
- Grain Direction: Which way the metal grains are going can affect how the bend turns out.
- Tool Condition: If your tools are worn out, you won't get as precise a bend.
- Operator Skill and Experience: The more you know and the more you've done, the better your results will be.
Tips for Better Press Brake Work
Here's how you can make your press brake jobs even better, kind of like how you optimize laser operations:
Calibration: Getting It Right
The hydraulic press brake, like other machines, needs to be calibrated regularly. Making sure it's calibrated correctly means your bends will be accurate, with the right bend angle and radius. Precision in these things is really important for good quality and less waste.
- Calibration Challenges
o Bend Deduction Math: You need to use the right formula based on the material and the bend you want.
o K Factor: This number, which tells you where the neutral axis is, has to be right for accurate bending.
Keeping Tools in Good Shape
Taking care of the punch and die is really important for consistent press brake work. If your tools are dull or dirty, the bends won't be as good and you might need more force to bend. Paying attention to tool maintenance means your tools will last longer and you'll get better results every time.
Tool Maintenance Basics:
o Check for Wear: Looking at your tools regularly for signs of wear can stop a lot of problems before they start.
o Cleaning: Getting rid of metal bits, oil, and other junk keeps your tools working well and lasting longer.
Don't Overload the Press Brake
Every press brake has its limits, like how much weight it can handle and how thick the material can be. If you go over these limits, you're not just risking the machine and the results, but also your safety.
- Signs of Overloading
o Vibrations: If the machine is shaking more than usual, it might be under too much stress.
o Metal Deformations: If the metal doesn't bend the way it should or has weird shapes, it could mean the machine is overloaded.
o Emergency Stop Trips: Modern machines have safety features like emergency stop buttons that might go off if it's overloaded.
Use the Latest Tech
New technologies like CNC controllers have changed the way press brakes work. Making sure your machine has the newest software and tech makes your bending faster, more precise, and more flexible.
- Benefits of Updated Tech
o Better Precision: Advanced software can calculate bend angles, allowances, and other things more accurately.
o Less Waste: Optimized processes mean you waste less material and have to do less rework.
o Easier for Operators: Modern systems make it easier for operators to do a good job every time.

The Cost of Press Brake Bending
Setting up and running a press brake costs money, just like running a laser machine:
- Initial Cost: Buying the machine and getting it set up.
- Operating Expenses: Daily costs like power, materials, and paying people to work.
- Maintenance Costs: Keeping the machine in good shape and replacing parts that wear out.
- Training and Certification: Paying to train people to use the machine the right way.
Alternatives to Press Brake Bending
Just like there are other ways to cut besides lasers, there are other ways to bend metal too:
- Roll Forming: This is good for bending long pieces of metal continuously.
- Tube Bending: Perfect for making cylindrical shapes.
- Stamping: Uses dies and high pressure to shape metal.
- Rotary Draw Bending: Shapes metal with a rotating form.
In Conclusion
Press brake bending is a great way to shape metals. It's precise, efficient, and versatile, just like how laser technology has changed sheet cutting. Even though these two areas are different, they both show that understanding how the machinery works, what it can do, and what affects its performance can lead to amazing results.
Whether you're bending metal or cutting it with a laser, knowing the details makes you better at what you do. It gives you the power to make better products and be more successful in manufacturing.