Customers in various industries rely on different cutting machines based on the material they are working with, and the capabilities of modern technology make it possible to create a wide range of products by completing diverse processes. These processes depend on the thickness and dimensions of the materials, often requiring the use of multiple machines. One such essential machine is the profile bending machine. Many customers have questions about its functions and features.
Profile bending plays a crucial role in the design and production of various parts, producing a wide range of products used in industries such as steel manufacturing, decorative works, structural steel fabrication, and machinery production.
A profile bending machine is used to perform cold bending of metal profiles in various shapes and sizes. Primarily utilized in the metalworking industry, these machines are particularly well-suited for bending tubular profiles, flat bars, beams, and "U" profiles. Due to their versatility, profile bending machines are commonly chosen for a variety of bending tasks. In this article, KRRASS will provide a detailed overview to address your questions about profile bending machines and their capabilities.
What Is Profile Bending
At its core, profile bending is the process of shaping metal profiles or sections into curved or circular shapes using specialised machinery. It’s a versatile and precise method that can work with various materials, including steel, aluminium, and stainless steel. The process involves several key steps:
1. Material Preparation
Before profile bending can take place, the metal profiles need to be prepared. This includes cutting the profiles to the required length and width. The initial profiles can take the form of beams, channels, angles, or other shapes, depending on the desired outcome.
2. Bending Setup
The heart of the profile bending process lies in the bending machine. Typically, these machines consist of three rollers: two positioned below the workpiece and one above it. The angles and positions of these rollers are meticulously adjusted to achieve the desired bend radius and curvature.
3. Rolling
With the material securely placed in the bending machine, the rollers are set into motion. As the profile passes through the rollers, it undergoes gradual deformation, taking on the desired curved shape. The number of passes and adjustments made during the rolling process determines the final curvature achieved.
4. Quality Control
Throughout the bending process, the machine operators watch to ensure that the roll conforms to the specified dimensions and curvature tolerances. Any necessary adjustments are made to achieve the desired result.
What Is Profile Bending Machine?
Playing a very significant role in the manufacture of design parts, profile bending application is frequently preferred in areas such bending processes, iron and steel goods, decorative production, steel structure, and machinery manufacturing. In addition, profile bending machines are used for the cold bending of profiles of various shapes and sizes. These machines are preferred for bending profiles such as tubes, flat bars, profiles, in the metalworking field.
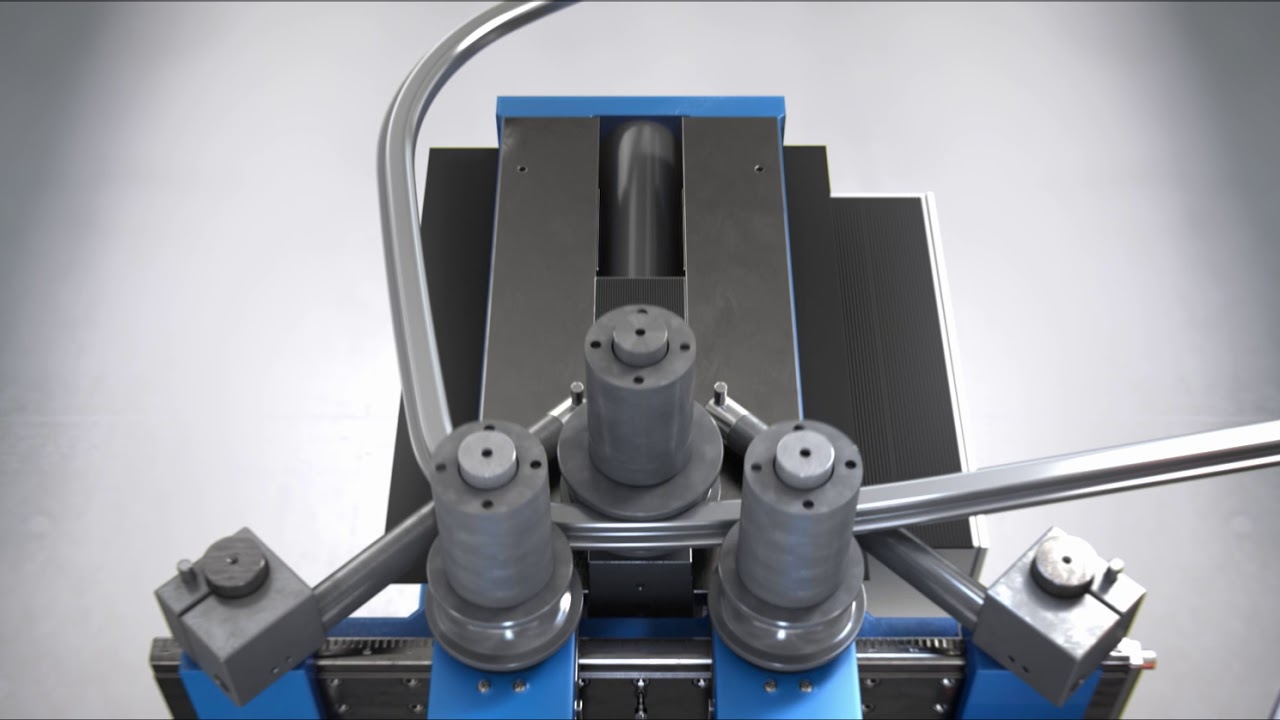
Understanding Profile Bending Machines
Profile bending machines are essential tools in the structural fabricating industry. These machines are designed to bend various types of profiles, including beams, channels, angles, and tubes, to create smooth curves and precise shapes. By using a combination of rollers and hydraulic pressure, profile bending machines can achieve tight radii and eliminate any flat areas that may occur during the bending process.
To understand how profile bending machines work, it is important to know the key components of these machines. The main components include the bending rolls, which can be adjusted to accommodate different profile sizes and shapes, and the hydraulic system, which provides the necessary force to bend the profiles. Some advanced profile bending machines also feature CNC controls, allowing for precise and automated bending operations.
Profile bending machines are commonly used in industries such as construction, automotive, aerospace, and shipbuilding. They are used to create curved components for various applications, including handrails, frames, arches, and structural supports. These machines offer a versatile solution for bending profiles of different materials, including steel, aluminum, and stainless steel.
In addition to their bending capabilities, profile bending machines can also be used for other operations, such as straightening, rolling, and flanging. This makes them a valuable asset in any structural fabricating workshop, as they can perform multiple tasks with a single machine.
Overall, understanding profile bending machines is crucial for anyone involved in the structural fabricating industry. These machines offer a cost-effective and efficient solution for bending profiles, allowing for the creation of complex and aesthetically pleasing shapes.
Applications
Profile bending machines have a wide range of applications in various industries. One of the main applications is in the construction industry, where these machines are used to create curved components for architectural structures, such as handrails, canopies, and spiral staircases. The ability to achieve precise and smooth curves makes profile bending machines an ideal choice for creating visually appealing and functional designs.
Another common application of profile bending machines is in the automotive industry. These machines are used to bend profiles for vehicle frames, exhaust systems, and roll bars. The ability to bend profiles of different materials, such as steel and aluminum, makes profile bending machines suitable for various automotive applications.
Profile bending machines are also used in the aerospace industry for bending profiles used in aircraft structures, such as wing components and fuselage frames. The precise bending capabilities of these machines ensure the structural integrity and aerodynamic performance of the aircraft.
In the shipbuilding industry, profile bending machines are used to create curved profiles for ship hulls and decks. The ability to bend large and heavy profiles makes these machines essential for shipbuilding operations.
Other industries that benefit from profile bending machines include furniture manufacturing, where these machines are used to create curved metal components for chairs and tables, and the energy sector, where they are used to bend profiles for solar panel frames and wind turbine towers.
Overall, the applications of profile bending machines are vast and varied. These machines play a crucial role in the fabrication of curved components for different industries, enabling the creation of innovative and structurally sound designs.
Applications of Profile Bending in Modern Construction
One of the most notable applications of profile bending is in the realm of modern construction. Here, it plays a pivotal role in shaping architectural designs and structural elements.
Profile bending allows architects and builders to create archways and curved facades that add a touch of elegance and uniqueness to buildings with metal elements. In large-scale construction projects, profile bending is often used to shape structural beams and columns. These curved components provide both strength and visual appeal to the structure. Whether it’s a curved roof support or an arched entrance, profile bending ensures structural integrity while adding architectural flair.
Interior and exterior staircases are often designed with curved or spiral shapes to increase space efficiency and create visual interest. Profile bending may be used for crafting metal handrails, balustrades, and support structures needed for these intricate staircases.
Advantages
rofile bending machines offer several advantages over traditional bending methods. One of the main advantages is their ability to achieve tight radii and eliminate flat areas, as demonstrated in the video linked in the user input. This is especially important when a perfect radius is desired, as it ensures the aesthetic appeal and structural integrity of the bent profiles.
Another advantage of profile bending machines is their versatility. These machines can bend profiles of different sizes, shapes, and materials, allowing for a wide range of applications. Whether it's bending small tubes or large beams, profile bending machines can handle the task with precision and efficiency.
Profile bending machines also offer increased productivity and cost-effectiveness. With their automated controls and efficient bending processes, these machines can significantly reduce the time and labor required for bending operations. This not only improves productivity but also reduces manufacturing costs, making profile bending machines a smart investment for any fabrication workshop.
Furthermore, profile bending machines provide consistent and accurate results. The CNC controls on advanced machines allow for precise bending angles and repeatability, ensuring that each profile is bent to the exact specifications. This eliminates the need for manual adjustments and reduces the risk of errors.
Lastly, profile bending machines are relatively easy to operate and maintain. With proper training and regular maintenance, these machines can have a long service life and deliver consistent performance. This makes them a reliable and valuable asset in any fabrication facility.
In conclusion, the advantages of profile bending machines make them an indispensable tool in the structural fabricating industry. From achieving tight radii to increasing productivity and cost-effectiveness, these machines offer a versatile and efficient solution for bending profiles of different shapes and sizes.
Profile Bending Materials and Techniques
The materials used in profile bending are as diverse as the applications themselves. Depending on the project’s requirements, metals like steel, aluminium, and stainless steel can be employed. The choice of material often depends on factors such as strength, corrosion resistance, and cost.
Cold Bending vs. Hot Bending
Profile bending can be performed using either cold bending or hot bending techniques. Cold bending is the more common method, where the metal is bent at room temperature. Hot bending, on the other hand, involves heating the metal to a specific temperature before bending it. Hot bending is often used for larger sections or when tight radii are required.
Roll Forming vs. Press Braking
Roll forming and press braking are two primary techniques used in profile bending. The former involves passing the metal profile through a series of rollers that gradually shape it into the desired curve. Three-roll and four-roll bending machines are the most common types of equipment used in this process. Three-roll machines are well-suited for simpler bends, while four-roll machines offer greater control and are capable of handling more complex profiles. Press braking, on the other hand, uses hydraulic presses to bend the profile. The choice between these techniques depends on the complexity of the bend and the material being used.
Features and Types of Profile Bending Machines
KRRASS Profile Bending Machines include two main models: the PBH Profile Bending Machine and the PBM Profile Bending Machine. Below is an overview of the key features of each model:
1. PBH Profile Bending Machine
The KRRASS PBH Profile Bending Machine is an excellent choice for continuous production lines, offering high efficiency and ease of use. Designed for rapid operation, the PBH machine features powerful curvilinear rollers that deliver flawless results with minimal effort. Additionally, the PBH is designed to be energy-efficient, reducing operational costs while maintaining top performance.
Known for its reliability and durability, the KRRASS PBH Bending Machine minimizes cycle time, making it ideal for high-demand production environments. It also boasts a high drive torque for maximum bending power. With its robust build, the PBH is not only precise but also long-lasting, making it a trusted solution for various metalworking applications.
2. PBM Profile Bending Machine
The KRRASS PBM Profile Bending Machine is equipped with large shaft diameters and strong shaft bearings, which help minimize error margins during the bending process. These machines are fitted with hardened steel rollers that ensure precise and accurate bending, while the mechanical side supports contribute to a long service life.
PBM machines come with hydraulic motor-supported cylinders and lower shafts, as well as a durable cast body and control panel. They also feature brake motors for enhanced safety. The PBM series includes advanced equipment like metal bar bending apparatus, digital displays, special cylinders, and support arms designed for bevel adjustments, all of which simplify the bending process and improve production efficiency.
KRRASS PBM Machines are fast, energy-efficient, and versatile, offering maximum flexibility and bending capacity. The machine’s ability to adjust the distance between the side rollers allows for precise control over the bending process. The advanced technology in KRRASS machines ensures optimal alignment, achieving the highest bending quality with minimal deformation. In summary, the KRRASS PBM is a powerful, energy-efficient, and user-friendly bending machine designed for exceptional performance and longevity.
Choosing the Right Profile Bending Machine
Choosing the right profile bending machine is essential to ensure optimal performance and efficiency in bending operations. There are several factors to consider when selecting a profile bending machine:
1. Profile Size and Shape: Determine the maximum size and shape of the profiles you will be bending. Make sure the machine you choose can accommodate the profiles you work with.
2. Material Compatibility: Consider the types of materials you will be bending, such as steel, aluminum, or stainless steel. Ensure that the machine is capable of bending the specific materials you work with.
3. Bending Capacity: Assess the bending capacity of the machine, including the maximum bending force and the maximum bending radius. This will determine the range of profiles you can bend with the machine.
4. Automation and Controls: Determine whether you require manual or automated controls for your bending operations. Advanced profile bending machines with CNC controls offer precise and automated bending processes, improving efficiency and accuracy.
5. Maintenance and Support: Consider the maintenance requirements and availability of technical support for the machine. Ensure that you can easily access spare parts and receive assistance when needed.
By carefully evaluating these factors, you can choose the right profile bending machine that meets your specific bending requirements and maximizes productivity.
Expert Tips for Using Profile Bending Machines
To get the most out of your profile bending machine, consider the following expert tips:
1. Proper Setup: Ensure that the machine is properly set up and calibrated before starting any bending operations. This includes adjusting the bending rolls, hydraulic pressure, and other settings as per the requirements of the profiles you are bending.
2. Material Preparation: Prepare the profiles by removing any burrs or sharp edges that may affect the bending process. This will help achieve smooth and accurate bends.
3. Lubrication: Apply lubrication to the bending rolls and the profiles to reduce friction and ensure smooth bending. Regularly check the lubrication levels and replenish as needed.
4. Safety Measures: Follow all safety guidelines and use appropriate personal protective equipment when operating the profile bending machine. This includes wearing safety glasses, gloves, and hearing protection.
5. Quality Control: Inspect the bent profiles for any defects or imperfections. Use measuring tools to ensure that the bending angles and dimensions meet the required specifications.
6. Regular Maintenance: Perform regular maintenance tasks, such as cleaning, lubrication, and inspection of the machine. Refer to the manufacturer's guidelines for specific maintenance procedures.
By following these expert tips, you can enhance the performance and longevity of your profile bending machine, while ensuring safe and accurate bending operations.
PBT Brofile Bending Machines Overview
ARKUS12 | PBT15 | PBT25 | PBT35 Servo Wide | HELIX Servo | |
---|---|---|---|---|---|
X-axis | |||||
Force X-axis | 12 t | 15 t | 27 t | 35 t | 65 t |
Positioning accuracy of the X-axis | 0,01 mm | 0,01 mm | 0,01 mm | 0,01 mm | 0,01 mm |
Drive of X-axis | Valve controlled hydraulics | Valve controlled hydraulics | Valve controlled hydraulics | SERVOHydraulics clean - low noise - 70% energy savings | SERVOHydraulics clean - low noise - 70% energy savings |
Stroke of X-axis | 200 mm | 300 mm | 265 mm | 390 mm | 445 mm |
Max. insertion width | 135 mm with roll ring D105 60 mm with bending device | 263 mm with roll ring D105 238 mm with roll ring D130 | 243 mm with roll ring D150 | 293 mm with roll ring D150 (optionally 350 mm with roll ring D150) | 415 mm with roll ring D220 |
Hydraulic oil volume | 7 litres | 17 litres | 17 litres | 9 litres | 9 litres |
Y-axis | |||||
Shaft drive; individually driven! | Electric motors, clean and low noise | Electric motors, clean and low noise | Electric motors, clean and low noise | SERVO DRIVE - clean - low noise - 100% torque at any speed | SERVO DRIVE - clean - low noise - 100% torque at any speed |
Dynamic speed control of the shafts | 1 – 30 rpm | 1 – 20 rpm | 1 – 22 rpm | 1 – 16 rpm | 1 – 8 rpm |
Max. torque per shaft | 500 Nm | 800 Nm | 1600 Nm | 3000 Nm | 9000 Nm |
Shaft height | 110 mm (optionally 220 mm) | 275 mm | 300 mm | 400 mm | 500 mm |
Shaft diameter Ø | 40 mm | 40 mm 65 mm | 105 mm | 105 mm | 130 mm |
Shaft supports | optional | series | series | series | series |
Front shaft distance | 256 (optional 80) – 518 mm | 110 - 800 mm | 200–1000 mm | 360-1120/1400 mm | 630–1330 mm |
Z-axis | |||||
Manual Z-axis (static) | series | series | series | - | - |
Cranked Z-axis (dynamic) | optionally | optionally | optionally | optionally | - |
CNC-controlled Z-axis (dynamic) | optionally 4 t | optionally 2 t | optionally 2 t or 4 t | optionally 4 t | series 4 t |
Control / Software:: | |||||
Machine control | Manual / Tablet Teach-In / TABLET350 / PC400 | PC400 | Manual / Tablet Teach-In / TABLET350 / PC400 | PC400 | PC400 |
Operating system | Windows 10 | Windows 10 | Windows 10 | Windows 10 | Windows 10 |
General technical data: | |||||
Connection | 3 x 400 VAC, 16 A | 3 x 400 VAC, 20 A | 3 x 400 VAC, 32 A | 3 x 400 VAC, 32 A | 3 x 400 VAC, 62 A |
KW | 2 kw | 4 kw | 7 kw | 15 kw | 34 kw |
Length / width / height | 905 mm / 950 mm / 1125 mm | 1400 mm / 1450 mm / 1370 mm | 1680 mm / 1.250 mm / 1390 mm | 1970 mm / 1.860 mm / 1420 mm | 2520 mm / 2240 mm / 1760 mm |
Weight | 540 kg | 1275 kg | 1150 kg | 2250 kg | 5500 kg |
Transportability of the machine | Pallet truck | Pallet truck | Pallet truck / Drawbar | Crane | Crane |
End
Krrass CNC profile bending machines combine high bending performance with modern mechanical engineering and powerful hydraulic systems. The equipment can bend medium and heavy steel profiles with great precision. Siemens brand electrical components, CNC controllers with stored self-running programs, high drive forces, and hydraulically adjustable bending rolls make the entire range of profile bending machines a powerful solution for metal construction, fitters, and general mechanical engineering. Haas Machinery provides innovative solutions for high-precision machining.