Press brake bending is a paramount process technology in the metal forming industry. The pressure between the punch and die can make the metal sheet bend and deform precisely. This makes the products widely applied in manufacturing industries.
Compared with manual bending, press brake bending features high efficiency, low cost, etc., and plays a pivotal role in metal manufacturing companies. There are commonly three sheet metal bending methods, air bending, bottoming and coining.
Among these bending methods, press brake coining is the most popular one, because it can offer precise and consistent bending results. The metal can be bent to the angle fitting the punch and bottom of the die precisely through high tonnage. Thus ensures the anticipated bending results.
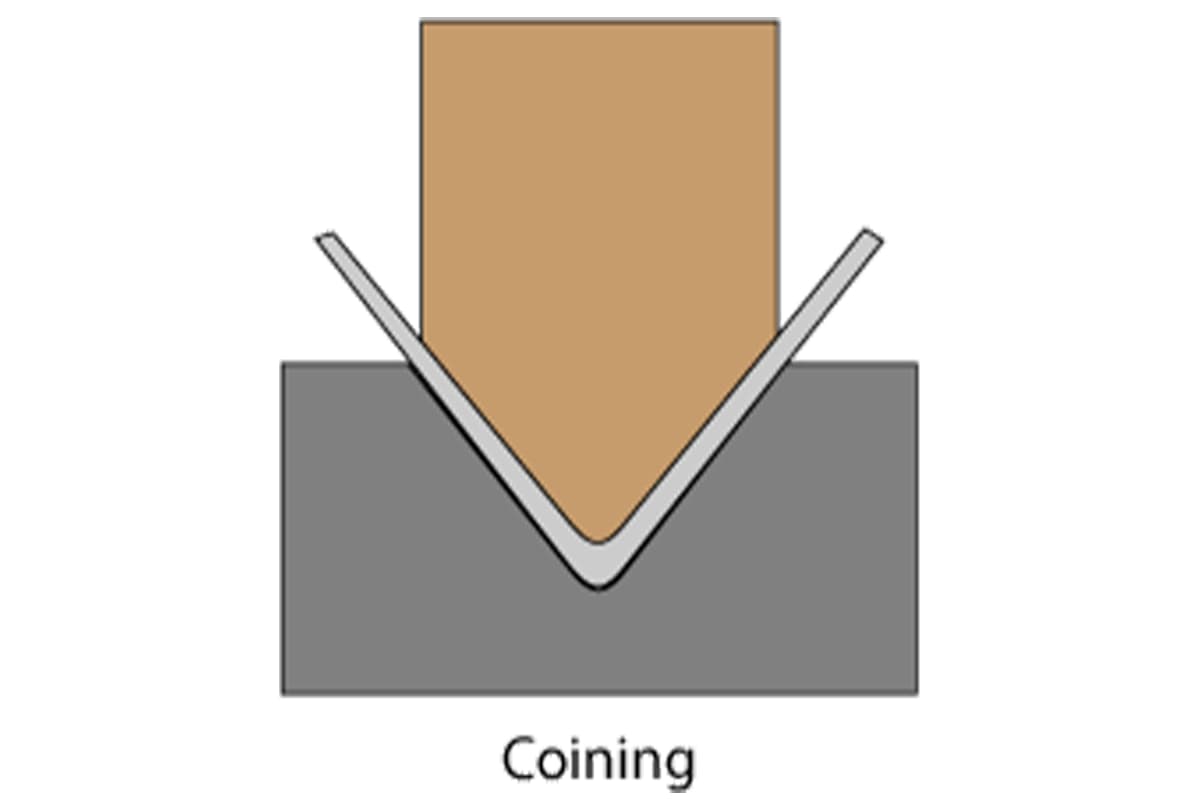
What are the Components and Principles of Press Brake Bending?
The upper or lower die of a press brake machine applies pressure to metal sheets, which causes them to stretch and then shrink. This is called press brake bending.
To understand this technique better, we first need to go through the components and principles involved. Let’s do that!
- Basic Components
A press brake is mainly made up of c-shaped frames, a top die or punch, a bottom die, and a hydraulic system. The flow of fluid that moves the top die is controlled by the hydraulic system. This system has tanks, pumps, motors, valves, and pipes. They all work together to move the top die.
The press brake’s main body is the c-shaped frame, which holds up the top and bottom dies.
- Bending Principles
At the start of bending, the sheet is free to bend. It is put on the bottom die, and the top die bends the metal sheets by applying pressure. The bending force arm and radius of curvature get smaller as the upper or lower die presses on the plate. This makes the plate slowly fit into the V-groove of the lower die.
At the end of the stroke, when the upper and lower dies are fully touching, they make a V-shape. This is basically called bending. Multiple aspects of bending need your attention, and one key principle is checking the straightness and indentation.
To get rid of indentations, operators increase the shoulder radius of the lower die. This process uses an anti-indentation film or an indentation-free lower die. On the other hand, the rigidity of the machine frame (frame design, choice of steel, etc.) determines how straight the bent products are.
Press Brake Fundamentals: Types of Press Brake Bending
The bending technique has been developed for hundreds of years in metal fabrication, with the advancement of technology, there are many bending methods for option. These methods are varied from each other, and here are the types of bending:
Air Bending
Air bending is a bending process that involves the use of a punch brake to bend sheet metal. Once positioned inside the punch press, the top die presses down and into the bottom die. Because the sheet metal is positioned between these two dies, it bends to form the shape of the dies.
Coining
Also using a press brake is the bending process known as coining. Coining is a high-performance bending process that’s characterized by greater force. Like air bending, it compresses sheet metal between a top die and a bottom die. The difference between these two processes is that coining uses up to 30 times more pressure to bend sheet metal than air bending, making it highly useful for bending thick and/or hard sheet metal.
Bottoming
Bottoming is a bending process in which sheet metal is pressed against a bottom die featuring a V shape. While other bending processes typically support the use of both U- and V-shaped dies, bottoming only uses a V-shaped die. It’s often preferred over air bending because of its higher level of accuracy as well as less recoil with the finished sheet metal.
Roll Bending
As shown in the image above, roll bending is a more rudimentary bending process that involves the use of multiple rollers to bend sheet metal. It’s typically performed using a roll bender with three separate rollers. One roller is placed at the top, whereas the remaining two rollers are positioned directly underneath the top roller. When sheet metal is fed through the rollers, it bends
3-Point Bending
Finally, three-point bending is a relatively new bending process that requires the use of an adjustable die. Unlike with other bending processes, the bottom die isn’t fixed in a stationary position. Rather, the bottom die used in three-point bending features an adjustable height. It can be raised or lower, allowing for a greater level of versatility. Like coining, though, three-point bending is a more costly bending process compared to other bending processes.
Step into Press Brake Coining
Historical Context
The word “coining” dates back to ancient coining technology. In ancient, the metal sheet was placed into the die and could be pressed into the geometry shape of the coin through high pressure and precise die shape. This method ensures that each coin’s shape and size is very precise. As time passes by, this technology is used in other metal manufacturing industries, especially metal sheet bending.
Process
The coining is a sheet metal fabrication process, its core is to use high tonnage to make metal sheets utterly fit the geometry shape of the punch and dies. This is realized by putting the metal sheet on the die and using the punch to exert much pressure. This method ensures the metal will not be deformed and bent during the bending process.
Here are the key procedures of the coining process:
- Material preparation: first, choose the proper metal material, and then cut it into the required shape and size.
- Die setting: the punch and die must be designed strictly to ensure that their geometric shapes can be matched with the bending angle. Set the tool on the press brake.
- Metal positioning: the metal sheet is positioned on the press brake to ensure that it won’t move and deviate during the bending process.
- Exerting the high tonnage: the punch uses high tonnage to press the metal sheet, making it fit the shape of the die and punch. This process needs high precision and control.
- Bending finish: once bending is finished, the sheet metal will keep its required geometric shape to achieve high-precision bending.
Benefits
- Precision: coining is a high-precision bending method, that can produce precise and consistent bending, and is very suitable for applications requiring high precision, such as aerospace and medical device manufacturing.
- Consistency: due to the metal conforming exactly to the shape of the punch and die, coining can produce consistent bending, whether for mass production or custom production.
- Wide applicability: coining is widely applied to various metal materials with different types and thicknesses, making it a universal bending method.
- Surface hardening: coining work-hardens the surface of the metal, enhancing its durability and resistance to wear. The hardening effect can extend the lifespan of components, reducing the need for frequent replacements.
- Detailed surface finish: the coining process produces a very fine and detailed surface finish, which is essential for parts that require both aesthetic and functional precision.
- Rapid prototyping and production: coining enables rapid prototyping, followed by full-service fabrication and production.
Applications of Coining
Coin and Medal Manufacturing
Coining has a long history in the production of coins and medallions. The process of coining uses high-pressure dies to imprint detailed designs onto metal blanks, ensuring precise and consistent shapes and sizes. This method is ideal for producing currency and commemorative medallions. For instance, the U.S. Mint uses coining to produce billions of coins annually, each with intricate designs and consistent dimensions.
Precision Metal Parts
Industries requiring high precision, such as electronics and medical tooling, rely on coining to create complex parts with sharp, crisp corners and well-defined features. For example, in electronics, components often require precise bends to fit into small assemblies, and coining provides the necessary accuracy. In medical devices, precise bends are crucial for the functionality and safety of tools like surgical instruments.
Wire Forms Fabrication
In the wire forms industry, coining is used as a secondary operation to create intricate and precise shapes on the wire's surface. This technique is particularly useful in electronics and circuits, where flat surfaces or functional shapes are needed in wire forms. For example, coining can produce the exact bends required for connectors and terminals in electronic devices.
Aerospace and Medical Device Manufacturing
The aerospace and medical device industries benefit greatly from coining due to its high precision. In aerospace, components need exact bending angles to ensure structural integrity and aerodynamic efficiency. For example, turbine blades and structural brackets are often coined to achieve the precise shapes necessary for optimal performance. In medical device manufacturing, precise bends are crucial for tools like stents and catheters, where accuracy is critical for patient safety.
General Metal Fabrication
Coining is versatile and can be applied to various metal materials of different types and thicknesses. It is widely used in precision sheet metal fabrication to produce precise and consistent bends. This consistency is crucial for industries like automotive manufacturing, where parts such as brackets and reinforcements must meet strict specifications to ensure vehicle safety and performance.
Processing Problems and Solutions
The theory behind coining is that with enough force, your metal will bend to the precise angle of your tooling. Several processing problems can arise during coining, such as die wear, material deformation, and dimensional inaccuracies.
Die Wear
Die wear is common due to the high pressures involved in coining. Regular inspection and maintenance of the dies are necessary to prevent wear from affecting the quality of the bends. Using high-quality die materials and proper lubrication can help minimize wear and extend the life of the tooling.
Material Deformation
Material deformation, such as cracking or thinning, can occur if the material properties are not well-suited to the coining process. Proper material selection and preparation, along with precise control of the press brake settings, can help mitigate these issues and ensure consistent results.
Dimensional Inaccuracies
Achieving the desired dimensional accuracy requires careful control of the coining process. Any deviations in the press brake settings or tooling alignment can lead to inaccuracies. Regular calibration and maintenance of the equipment, along with skilled operator training, are essential to maintain precision.
Comparison with Other Bending Methods
Air Bending vs. Coining Sheet Metal
Tonnage Difference
Since force doesn’t produce the bend in air bending, air bending usually requires less tonnage, making it a popular choice for hydraulic press brake machines. Because of the small contact square between the metal and the die, the required force is relatively low during the bending process, which means less pressure is needed to achieve the desired bend angle.
While coining requires high tonnage -often five to ten times more than air bending- to ensure the metal completely conforms to the punch and die. This means the coining usually needs more tonnage. This high pressure is necessary to achieve precise bends and minimize springback.
Contact Difference
In air bending, the contact square between the metal and die is extremely limited, that is only several points of contact, which is beneficial to reduce the abrasive and damage on the metal surface.
While in coining, the touch between the metal and tool is more closer, to ensure the metal can be bent completely according to the shape of the die, which may lead to some metal thinner and deformation.
Bend Angle Determination
The angle of air bending is determined by the depth at which the punch descends into the die.
Coining utilizes high tonnage pressure to make the metal completely fit the punch and die’s exact angle. The angles of the punch and die determine the angle of the bend in the metal sheet.
Precision Levels
Coining is renowned for its high precision and consistency. The method ensures that the metal conforms exactly to the die's shape, resulting in minimal springback and highly accurate angles.
Air bending, while flexible and capable of producing various angles, is more prone to springback effects. The final bend angle can vary depending on material properties and thickness, making it less reliable for applications requiring tight tolerances.
Flexibility
Air bending offers greater flexibility in adjusting bend angles post-operation due to its lower tonnage requirements and fewer constraints on tooling.
Coining, while precise, is less flexible because it requires specific tooling designed for exact angles. Adjustments after coining are more challenging due to the high pressure applied during the process.
Bottom Bending vs. Coining
Tonnage Requirements
Bottom bending usually needs less tonnage —more than air bending but less than coining— because the metal does not exactly fit the die’s shape. For larger bend radii, bottoming requires tonnage roughly the same as for air bending for larger bend radii.
Coining requires larger tonnage to ensure the metal conforms exactly to the shape of the punch and die.
Mechanisms
Bottom bending involves pressing the sheet metal into a die until it fully contacts its surface, which helps mitigate springback but does not guarantee exact conformity to the die shape. In order to get a certain angle, you need to use tooling that has a slightly more acute angle in order to account for the springback that will naturally occur once the sheet metal is released.
Coining utilizes a similar principle but applies significantly higher tonnage to ensure that the metal flows into the die's shape completely, resulting in a precise bend that matches the die exactly.
Material Conformity
Bottom bending differs from coining in that the punch and die don’t make full contact with the metal.
Coining can ensure the metal is bent completely according to the die shape, thus acquiring more precise results.
Comparison Table
Bending Method | Tonnage Requirements | Precision Levels | Flexibility | Resulting Shapes |
Air Bending | Low | Moderate, prone to springback | High, can adjust post-bending | Variety of angles possible |
Bottom Bending | Moderate | High, but some springback | Moderate, limited adjustments | Varies, can achieve tight tolerances |
Coining | High | Very high, minimal springback | Low, precise tooling needed | Exact replication of die shape |
In conclusion, compared with coining, air bending requires less tonnage, and few contact, and its bending angle may not be consistent with coining. Because bottom bending uses less tonnage than coining, the material doesn’t entirely conform to the bend angle of the tooling. While coining needs more tonnage and can generate high consistency and precision bending.
FAQ
Q. What is the Rule for Bending Metal?
Ans. Bending metal depends on a few things, like the material, how thick it is, and the shape you want. Usually, the inside bend should match how thick your metal is. So, if your sheet is ⅛” thick, use a bending tool with a ⅛” radius for the best results. Similarly, for a thin sheet of 0.020”, use an equal radius.
The smallest bend you can make without breaking the metal depends on its flexibility and strength against cracks. People who sell these things usually write this information down in guides. They’d talk about safely shaping the metal to avoid issues. Likewise, they’ll also suggest minimal bends based on what kind of material you’re working with.
Remember to check whether you need to fold along or across any texture (like grains) because that matters, too.
Q. At What Temperature Does Metal Start to Bend?
Ans. Warm the thick sheet up to 200 to 300 degrees Fahrenheit before you shape it. This is especially important if you want to bend it to at least 0.75 inches. However, finding the right bending temperature requires knowing the chemical makeup, surface and edge states, and thickness of the material.
Conclusion
In simple terms, when you use press brakes to bend metal sheets, you put pressure on them to make them stretch and then shrink. However, to get the desired outcome, you need to adjust parameters like the straightness of the sheet.
There are different types of bending techniques for press brakes. They differ mostly based on the position of the workpiece and how it’s pressed. Besides, the intensity of the pressure and the range of tasks the process can cover also differ.
The hydraulic systems of a press brake mainly conduct the bending process. And, of course, the quality of the press brake defines the end result. And if you need the best press brakes, Krrass Machinery is here. Contact us today to find the press brake that suits your needs.