Sheet metal processing is an essential part of mechanical manufacturing, particularly in industries such as aviation, home appliances, automobiles, elevators, and more, where sheet metal components are widely utilized. In these fields, the precision and quality of sheet metal fabrication are crucial to ensuring the performance and reliability of the final products.
Among the various operations in sheet metal fabrication, V groove bending is one of the most critical and commonly used methods. This process involves creating a V-shaped groove along the material, allowing for controlled bending without causing cracks or distortions. It is especially important in applications where exact angles and tight tolerances are necessary.
The success of the V-groove bending operation directly influences the final product’s dimensions, shape, and overall appearance. A properly executed bend ensures that the workpiece retains its intended size and structural integrity. Conversely, any errors in the process—such as incorrect angles or surface defects—can negatively affect both the functionality and aesthetic of the component.
Given its importance, maintaining accuracy in bending dimensions and angles is vital. Factors such as material properties, thickness, tool design, and machine settings all play a role in achieving the desired outcomes. By carefully managing these variables, manufacturers can produce high-quality bent parts that meet precise specifications, ensuring the performance and durability required in demanding applications.
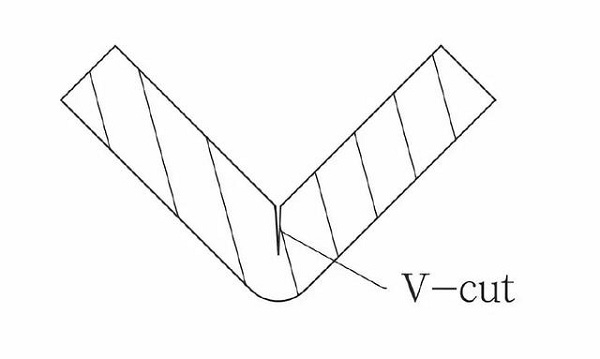
V Groove Bending Process Characteristics
On metal V Grooving machine, we slot a V-shaped groove at the position where the metal sheet needs to be bent, and then bend on bending machine as required.
The characteristics of V groove sheet metal bending process mainly include the following three aspects:
The workpiece arc radius to be small, no creases or indentation
Aftergrooving the sheet metal, the remaining thickness of the sheet becomes half of the original thickness, or even smaller, so that the workpiece arc radius after the bent can be greatly reduced.
In addition, the sheet metal after grooving, the remaining thicknessis thinner, the deformation force during bending will be reduced accordingly, and will not spread to the unbent area. So after bending, there are no creases on the surface of the workpiece. And the less bending pressure avoid the risk of indentation on the decorative surface.
In this way, small arc radius, no creases or no indentation on the decorative surface, which meet the decoration of high-end places such as hotels, banks, commercial centers, airports, etc.
Reduced the bending machine force
In the bending process, we need larger bending force when bending more thick plates. After slotting the sheet metal on CNC metal V-Grooving machine, the remaining thickness of the sheet is greatly reduced, so that the bending force required will also be correspondingly reduced, the thick plate bending can be finished on a smaller tonnage press brake machine. This not only reduces the investment in equipment, but also saves energy and space.
Complex shape workpiece bending and control of bending rebound
The workpiece shown in the figure, which unable to comlete the bend on a general bending machine, but if we slot it on CNC metal V Grooving machine firstly, the workpiece can be completed with some manual bending on the press brake machine.
In addition, the remaining thickness of the plate can be controlled by CNC sheet metal V Grooving machine, which will help to control rebound force and the rebound angle when bending.
For example, If the remaining thickness after grooving is controlled at about 0.03mm on metal V-grooving machine, the rebound angle can be made small, the rebound can be basically ignored.
Sheet metal V-grooving soltting method
n sheet metal production, we put the v-groove metal for bending on the grooving machine, and locate it, then input the thickness of the plate for automatic grooving.
When grooving, we need pay attention to two aspects:
– The V groove angle setting
From the bending process and bending experience, we know that the sheet metal has different degrees of springback deformation during bending and forming, which causes the deviation of the bending angle.
When slotting the sheet metal bending V groove size, the groove can be rationalized according to the required bending angle of the workpiece. Generally, the angle of the V-groove is 1-2° larger than the bending angle. For example, when we bend one workpiece to be 90°, the V-groove angle usually will be slotted to 92°, so that the caused bending angle rebound can be easily avoided.
– The V groove depth setting and remaining thickness setting
In the case of a certain plate thickness, the groove depth and the remaining thickness are corresponding values. Usually we set a remaining thickness value, at the base of the requirements of the bending process. Generally, the default value is 0.8mm, and the minimum should not be less than 0.3mm.
According to the plate thickness, we set the V grooving times and the V grooving depth. Due to the need to control burrs and protect the tools, the grooving depth should not be too large. Usually the depth of the first groove cannot exceed 0.8mm, and it must be carried out in at least two grooving.
For example, for a stainless steel plate thickness of 1.2 mm, the remaining thickness should be 0.5 mm after slotting, the first V grooving depth can be 0.5 mm, and the second V grooving depth will be 0.2mm. After two times of V grooving, the remaining plate depth amount just reached 0.5mm, and the burrs were relatively small, as shown in the below figure:
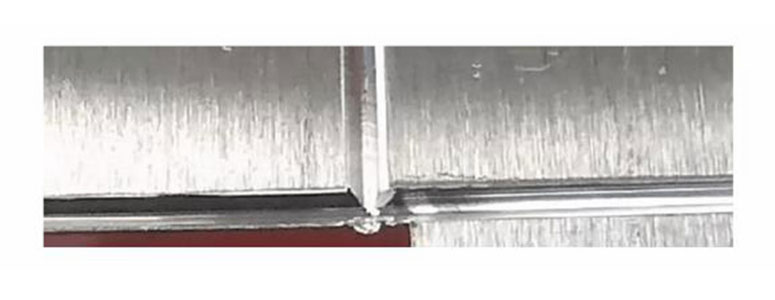
The Groove Machine and Cutting Tools
If you’re thinking of using the V-grooving technique to produce parts, first think carefully about the application. V-grooving is used mostly in low-stress architectural applications, and the finished piece will be only as strong as the remaining thickness of material at the bend. V-grooving is not a process for all manufacturing situations.
If you choose to use V-grooving, you need to account for the radius reduction from the thinning of the material at the cut. Whether radius reduction is a good or bad thing just depends on the function of the part. For instance, V-grooving can start with 0.080-in.-thick material at the bend line and reduce it to 0.030 in. Generally, V-grooving reduces the thickness at the point of bend to between a third or half of the original thickness. Obviously, V-grooving is not for applications that require bend strength. Nevertheless, you can produce a very sharp corner without stress cracks on the outside of the bend.
Because V-grooving reduces the material thickness at the bend, it requires less tonnage to complete the bend. This means that thicker sheets can be bent with less forming tonnage.
The groove can be produced on a horizontal shaper machine, which uses linear movement to use a single point of a cutter to cut a path on a flat surface, like the way a lathe removes material from a cylindrical object. This allows for the forming of an extremely sharp inside bend radius without creating stress cracks on the outside of the bend and without the excessive tonnage requirements of a bottoming or coining operation.
Historically speaking, before V-grooving and modern CNCs teamed up, the little V-grooving that was being done used a machine shop planer to cut the V-grooves. But without a proper way to secure the sheet metal to the machine table, the V-groove depth was difficult to control and extremely inefficient.
More recently shops have relied on CNC grooving machines designed for the task. The accuracy of these machines is the same as any other CNC equipment, positioning within 0.005 in. on average. The machines place the cut or miter precisely on the bend line, with the correct cut angle that will create the formed dimension. They’re called various names, including CNC V-grooving machines, V-groovers, CNC V-cutting machines, or simply V-grooving machines.
In a modern CNC V-cut horizontal shaping machine, the sheet is positioned directly under a cutter. The controller’s program uses the material parameters (thickness, quality, etc.) to guide the depth and location of the cut. These machines look very similar to a modern laser or plasma cutter.
The knives (cutting tools) you insert in the machine will depend on the bend angle you need. For example, if you need the internal bend angle to be between 45 and 60 degrees, you’ll need a rhombic-shaped cutter with a 35-degree cut angle. If your internal bend angle is between 60 and 80 degrees, you’ll need a triangular cutter; and for internal bend angles between 80 and 90 degrees, the cutter should also have a cut angle between 80 and 90 degrees. Figure 1 shows the basic cutter shapes, but you also might need to fine-tune the knife angle to achieve the groove angle you need.
If you are a regular reader of Bending Basics, you know that the springback will need to be compensated for. When V-groove bending, you need to account for springback not only with the press brake tooling, but also the angle of the cut. In most cases, an extra 1 or 2 degrees in the groove cut angle can take care of it.
Sometimes, though, you’ll run across material types and bend angles that have significant springback, and you’ll need to cut a greater groove angle to deal with it. The larger groove provides clearance to ensure that the notch you cut won’t bind during forming. With the right punch tool angle, you should have only a minor gap in the V-cut between mating edges (see Figure 2).
The cutter angle you need equals the required angle of cut plus a small amount of additional cut angle to compensate for springback. This is usually calculated as half the degrees of the internal bend angle (so a 90-degree V-groove bend would give you a 45-degree cut angle) plus half the degrees of springback, if necessary.
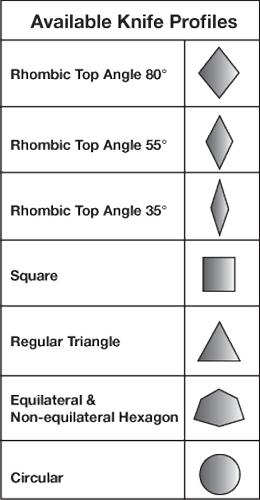
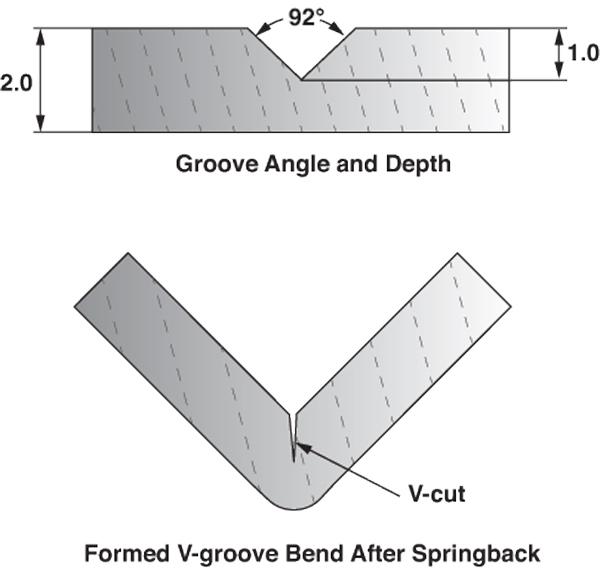
Application Prospect of V groove Bending Forming Technology
Due to the obvious advantages of V-groove bending technology, and there is no need to change the traditional bending methods and equipment, only need to increase the sheet metal V-groove machine, so the V-groove bending technology has been widely used in the emerging middle and high-end decoration industry application.
Subsequently, this technology was successfully applied to the elevator manufacturing industry. Due to the advantages of the V-groove bending process, the manufacture of the elevator shell is more efficient, precise, and has a better appearance.
Next, some experts in medical device manufacturing and electric control cabinet manufacturing industries also showed strong interest in V-groove bending forming technology. In the manufacture of medical devices, the V-groove bending process can be applied to the processing of various parts to improve product quality and performance. In the manufacture of electrical control cabinets, the V-groove bending technology can achieve a more refined and complex bending structure, improving the strength and durability of the cabinet.
With the in-depth understanding of V-groove bending forming technology, people find that its application fields will be broader. In addition to the above industries, V-groove bending technology can also be used in aerospace, automobile manufacturing, rail transit and other fields, as well as various engineering, architectural decoration and other fields. With the continuous development and innovation of technology, V-groove bending forming technology will surely show its unique charm in more fields, and bring more convenience and benefits to sheet metal processing.
What are the types of sheet metal v-groove machines?
Manual V-groove machine: The manual V-groove machine requires the operator to manually control the movement and cutting depth of the cutting tool, which is suitable for some simple V-groove processing requirements.
Semi-automatic V-groove machine: In the cutting process of semi-automatic V-groove machine, the movement of the tool and the cutting depth are partly controlled by the operator, but it may be equipped with some automation functions, such as automatic tool adjustment or automatic feeding function, which improves the processing efficiency and accuracy .
Fully automatic V-groove machine: The fully automatic V-groove machine has a high degree of automation, including fully automatic tool adjustment and feeding, usually using a CNC control system, which can achieve more complex V-groove processing and improve production efficiency and accuracy.
CNC V-groove machine: CNC V-groove machine is an advanced automation equipment, through the computer numerical control system to control the movement and cutting parameters of the cutting tool, it can precisely control the size and shape of the V-groove, suitable for complex V-groove processing needs.
Hydraulic V-groove machine: The hydraulic V-groove machine uses a hydraulic system to drive the cutting tool, which can achieve greater cutting force and stability, and is suitable for processing thicker metal sheets or special needs that require greater cutting force.
Mechanical V-groove machine: The mechanical V-groove machine adopts mechanical transmission mode, and the movement of the cutting tool is realized through transmission devices such as gears and belts, which is suitable for some small and medium-scale V-groove processing needs.
Conclusion
V groove bending, as a new type of bending process, is the result of market choice. Krrass has been dedicated to the research and production of sheet metal V-Grooving bending for 20 years, continue to explore and pursue new technology, users can produce more excellent products.