Metal shearing plays a crucial role in metal processing, extending far beyond just altering the shape of metal materials. It encompasses several important aspects, such as metal reuse, recycling, and enhancing productivity. In various industries, including automobile manufacturing, construction, machinery production, aerospace, and electronics, metal shearing technology is widely applied. It has become an essential process that drives industrial advancement and innovation.
Mechanical metal shears and hydraulic metal shears are two major metal shearing methods, each of them has unique characteristics and applicable scenarios. Mechanical metal shears rely on mechanical force to cut, simple structure, easy maintenance, fast cutting speed, suitable for large-scale, high-efficiency metal shearing needs. Hydraulic metal shear machine, on the other hand, through the hydraulic cylinder to generate a strong force to cut, although relatively slow, but its shear force, suitable for cutting the thickness of larger or harder metal materials. This type of machine is often used to handle thicker sheet metal or jobs that require higher shearing forces, so we need to emphasize the need to choose the right type of metal shear.
Mechanical Metal Shearing
Working principle and structural characteristics
Mechanical metal shear is the use of mechanical transmission and shear principle for cutting metal materials. Its working principle mainly includes the following steps:
The motor drives the mechanical transmission system (such as gears, cranks, etc.) to rotate, generating mechanical force.
The mechanical force is transmitted to the shear blade through the transmission system, so that the blade exerts a shearing force on the workpiece.
The workpiece is placed on the table and clamped by the shear blade and presser foot. As the shear blade descends, the workpiece is sheared.
Mechanical transmission system: including motor, gear drive, crank mechanism, etc.
Cutting parts: including upper knife, lower knife, presser foot, etc.
Working table: used to support the workpiece and keep the workpiece stable.
Structural composition and introduction of key components
Motor: provide power source.
Gear transmission: convert the rotary motion of the motor into the linear motion of the shear blade.
Crank mechanism: Convert the rotary motion into the up and down motion of the shear blade.
Upper and lower knives: used to clamp and shear the workpiece.
Pressure foot: Used to fix the workpiece to prevent it from moving during the shearing process.
Advantage analysis
Simple structure: the structure of the mechanical metal shear is relatively simple, easy to manufacture and maintain.
Fast cutting speed: the mechanical transmission system enables the shear blade to fall quickly, improving the shearing efficiency.
Suitable for mass production: due to the fast shearing speed, it is suitable for large-scale, high-efficiency metal shearing needs.
Disadvantage analysis
Noisy: mechanical transmission will produce noise, affecting the working environment.
Energy efficiency is relatively low: due to mechanical transmission will have energy loss, energy efficiency is relatively low compared to the hydraulic metal shear.
Higher material requirements: mechanical metal shear on the hardness and thickness of the workpiece has certain requirements, can not cut too hard or too thick material.
Hydraulic metal shearing
Working principle and structural characteristics
Hydraulic metal shear is a use of hydraulic transmission principle, through the high-pressure liquid drive shear mechanism to achieve rapid and efficient shear of metal materials, special equipment. Its core structure mainly includes a power source, control logic valve, transmission mechanism, shear mechanism and worktable and other major parts. The power source is usually provided by the hydraulic pump station, through the control logic valve to distribute and regulate the flow direction and pressure of the hydraulic oil, so as to drive the transmission mechanism, so that the shear mechanism in accordance with the preset cycle of shear operation.
Advantage analysis
- power source: usually consists of electric motor, hydraulic pump, oil tank, etc., is responsible for providing stable high-pressure hydraulic oil flow.
- control logic valves: including directional control valves, pressure control valves and flow control valves, etc., responsible for regulating and controlling the flow direction, pressure and flow of hydraulic oil, so as to realize the various actions of the shear.
- transmission mechanism: through gears, bearings, connecting rods and other components of the hydraulic energy into mechanical energy, drive the shear mechanism for shearing action.
- shear mechanism: including blade, knife seat, guide device, etc., is to realize the key part of the metal shear. Blades are usually made of high-strength wear-resistant materials, with high shear strength and wear resistance.
Analysis of disadvantages
- large energy consumption: hydraulic metal shears need to consume a large amount of electricity and hydraulic oil to provide power, so the energy consumption is large, the cost is high.
- high maintenance costs: due to the complexity of the hydraulic transmission system, the need for regular replacement of hydraulic oil, cleaning hydraulic components and other maintenance work, so the maintenance cost is high.
- Large noise: hydraulic metal shears will produce large noise in the working process, the working environment and the operator has a certain impact.
- High quality requirements for oil: the hydraulic transmission system requires high quality of hydraulic oil, you need to use high cleanliness, good anti-wear hydraulic oil, otherwise it is easy to cause wear and tear of hydraulic components and failure.
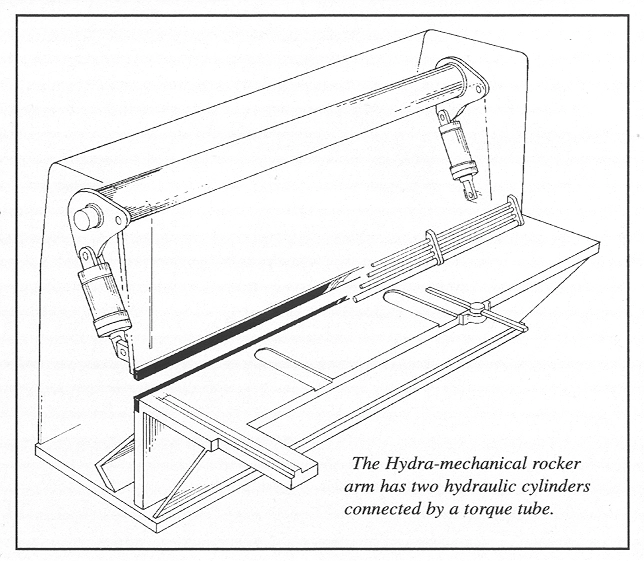
Comparison of mechanical and hydraulic metal shearing
Performance Comparison
Mechanical metal shears usually convert the rotary motion of the motor into the linear reciprocating motion of the shear mechanism through the transmission mechanism, and use the blades to shear the metal. Its structure is simple, direct action, so it has a high shearing speed and precision. Hydraulic metal shear is the use of hydraulic transmission system to drive the shear mechanism, through the expansion and contraction of the hydraulic cylinder to realize the shear action. Hydraulic transmission has a larger torque and stable shear force, so it is suitable for cutting thicker or harder metal.
Cost Comparison
In terms of initial investment cost, mechanical metal shears are usually less expensive because of their relatively simple structure and lower manufacturing cost. Hydraulic metal shears, on the other hand, are relatively more expensive because they need to be equipped with a hydraulic system and have a higher manufacturing cost. However, in terms of long-term operating costs, hydraulic metal shears have relatively low maintenance costs due to their stable shearing force and less wear and tear.
Comparison of Applicable Scenarios
Mechanical metal shears are suitable for scenarios that require high shearing speed and precision, such as the shearing and processing of thin sheet metal. In addition, the mechanical shear also has a smaller footprint and lower noise, suitable for the higher requirements of the working environment of the occasion. Hydraulic metal shears, on the other hand, are suitable for shearing thicker or harder metals, such as the dismantling and recycling of scrap cars. In addition, hydraulic shears have a larger shearing force and greater adaptability to cope with a variety of complex shearing needs.
The advantages of hydraulic shearing machine
CNC system's compensation function and automatic detection
The machine is equipped with these additional functions, which can automatically adjust during the cutting process to ensure the cutting precision of the sheet metal. For example, during cutting, if there are changes in material thickness or hardness, the CNC system will automatically adjust the position of the tool and cutting pressure to maintain the required dimensions and shapes.
High-precision rear gauge control
Utilizing a computer-controlled rear gauge servo system with precision ball screw drive. This means that when cutting different sizes and shapes of workpieces, the machine can precisely control the position of the rear gauge, ensuring cutting accuracy and consistency.
Rolling material support ball device
This device not only reduces frictional resistance but also protects the workpiece surface from scratches. Especially for cases where a high-quality surface finish of the workpiece is required, this design ensures that the workpiece is not damaged during the cutting process.
Strong structure and integrity
The hydraulic shearing machine has strong rigidity and integrity, with flexible and reliable motion of rolling guide rails. The brush material support surface reduces noise, while the pneumatic clamping system provides vertical rear support on the large table, making the machine more stable and reliable during operation.
Blade frame design
The mounting surface of the blade on the blade frame is curved, ensuring uniform blade clearances and improving the quality of the sheared section. This design ensures that the edges of the cut workpieces are smooth and neat.
Material stop structure
The material stop is driven by a motor, moving two lead screws synchronously through sprockets. This structural design makes the fixation of workpieces more reliable and flexible, preventing the workpiece from shifting or shaking during cutting, thus ensuring cutting precision and stability.
Choosing the Right Shearing Machine
The choice between a mechanical and hydraulic shearing machine depends on several factors, including the material being cut, the thickness and strength of the material, the precision required for the cut, and the budget available for equipment purchase and maintenance.
– For workshops and facilities that work primarily with lighter gauge materials and require a cost-effective solution, a mechanical shearing machine may be the best fit.
– Conversely, for heavy-duty operations dealing with thicker materials and requiring high precision, a hydraulic shearing machine would be more appropriate.
Both mechanical and hydraulic shearing machines serve the metalworking industry with their unique strengths. The mechanical shearing machine, with its simplicity and cost-effectiveness, is an excellent choice for lighter cutting tasks. In contrast, the hydraulic shearing machine’s power and precision make it ideal for more demanding applications.
Understanding the operational principles, advantages, and limitations of each type is crucial for making an informed decision that aligns with the specific needs of a project or a production facility. By carefully considering these factors, manufacturers can select the most suitable shearing machine to enhance their productivity and ensure the highest quality of work.
Conclusion
Mechanical metal shears and hydraulic metal shears each have their own advantages and disadvantages. Mechanical shears have the advantages of simple structure, low price, high shearing speed and high precision, suitable for scenes with high requirements for shearing speed and precision. Hydraulic shears, on the other hand, have the advantages of large shearing force, adaptability and lower long-term operating costs, suitable for shearing thicker or harder metals.
When choosing a metal shearing method, key factors to consider include the thickness and hardness of the metal material, shear speed and accuracy requirements, working environment and floor space constraints. In addition, factors such as the maintenance cost and service life of the equipment also need to be considered.