Have you ever wondered why laser-cut sheet metal doesn’t always turn out perfectly? This article explores common laser cutting issues, such as burrs on workpieces and incomplete cuts, and provides effective solutions. By understanding perforation techniques and fine-tuning cutting parameters, you can improve both the precision and efficiency of your process. Whether you’re dealing with burrs on stainless steel or optimizing perforation methods, this guide will give you the insights needed to achieve flawless results. Dive in and learn how to transform your sheet metal laser cutting process from problematic to precise.
Laser Perforation Techniques in Metal Cutting
In most hot cutting processes, drilling a small hole in sheet metal is essential before cutting begins. However, there are a few exceptions where cutting can start directly from the edge of the sheet.
Historically, a hole would be punched using a punch mold in a laser stamping machine before the laser cutting process. But now, there are two main methods for laser cutting that don't require a stamping device:
1. Blasting Perforation
Blasting perforation involves continuous laser irradiation that creates a localized melt pool at the center of the material. The molten material is then ejected by the high-pressure oxygen assist gas, forming a through-hole.
The size of the perforation depends on the plate thickness, laser power, and assist gas settings. Typically, the perforation diameter is about 50-60% of the plate thickness. As the plate gets thicker, the perforations may become larger and lose their circular shape due to the expansion of the heat-affected zone and gravity effects on the molten material.
This method is ideal for quickly creating holes in non-critical areas or scrap material, but it’s not recommended for applications requiring high precision or tight tolerances. By adjusting laser parameters and gas flow, it’s possible to optimize the process for specific applications.
It's important to note that oxygen pressure used in this process is similar to that used in cutting operations, which helps in material removal but may lead to surface contamination around the perforation site. For cleaner perforations, gases like nitrogen or argon can be used, although they result in slower cutting speeds.
2. Pulse Perforation
Pulse perforation uses a high-peak-power pulsed laser to rapidly melt or vaporize localized material. Inert gases, such as nitrogen or compressed air, are used to prevent excessive oxidation and minimize hole expansion. The gas pressure in this process is lower than that used in oxygen-assisted cutting. Each laser pulse creates microdroplets that are ejected, gradually forming the hole. For thicker plates, this process may take several seconds.
Once the perforation is complete, the auxiliary gas is switched to oxygen to begin the cutting operation. Pulse perforation results in smaller, more precise holes with better quality compared to blast perforation. This technique requires a laser system with higher output power and precise spatial and temporal beam control. Standard CO2 lasers typically lack the capabilities required for this high-precision process.
Pulse perforation also demands an advanced gas control system capable of finely tuning gas type, pressure, and perforation duration. Moreover, the transition from pulsed perforation to continuous cutting must be carefully managed to ensure smooth operation.
To optimize the process, cutting parameters such as focal length, nozzle standoff distance, and gas pressure can be adjusted during the acceleration phase. However, in practical industrial settings, it’s more efficient to adjust the laser’s average power, often by modifying the pulse width and frequency. Research has shown that adjusting both pulse width and frequency simultaneously produces the best results in terms of cut quality and process stability.
By mastering these perforation techniques and optimizing their settings, laser cutting can be fine-tuned for various applications, improving both efficiency and precision in metal fabrication.
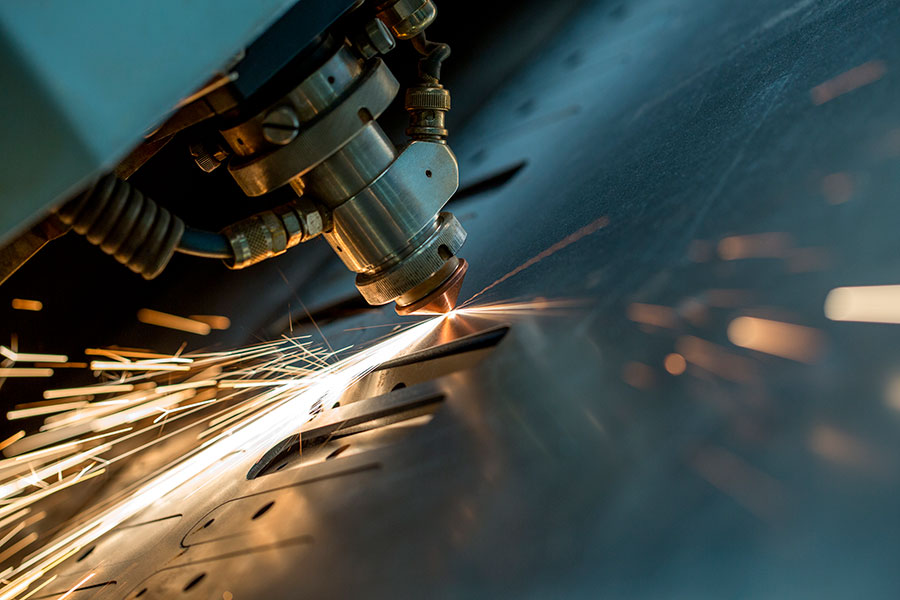
Analysis of the deformation of small holes cutting (small diameter and thickness)
When cutting small holes with high-power laser systems, deformation and quality issues can arise due to the energy concentration in a confined area. Traditional pulse perforation (soft puncture) techniques, while effective for less powerful systems, may lead to charring and hole distortion in high-power applications.
The primary cause of this phenomenon is the intense localization of laser energy during pulse perforation. This concentrated heat input can result in excessive material melting, vaporization, and thermal stress in the surrounding non-processing area. Consequently, the hole geometry becomes compromised, and the overall processing quality deteriorates.
To mitigate these issues in high-power laser cutting systems, it is recommended to transition from pulse perforation to blasting perforation (also known as single-pulse piercing or ordinary puncture). This method utilizes a single, high-energy pulse to rapidly create the initial hole, reducing the heat-affected zone and minimizing material distortion.
Key advantages of blasting perforation for small hole cutting with high-power lasers include:
- Reduced thermal input to the surrounding material
- Faster processing times
- Improved hole geometry and edge quality
- Minimized risk of material charring and deformation
Conversely, for lower-power laser cutting machines, pulse perforation remains the preferred method for small hole cutting. This technique offers several benefits in less powerful systems:
- Enhanced control over the cutting process
- Improved surface finish quality
- Reduced risk of thermal damage to delicate materials
- Better precision for intricate designs
Addressing Burr Formation in Low Carbon Steel Laser Cutting
When cutting low carbon steel with CO2 laser technology, burr formation can be a significant issue. Understanding the root causes and implementing appropriate solutions is crucial for achieving clean, precise cuts. Here are the primary factors contributing to burr formation and their respective remedies:
- Incorrect Focal Position: Conduct a focal position test and adjust the offset accordingly. Proper focus ensures optimal energy concentration at the cutting point.
- Insufficient Laser Power: Verify the laser generator’s functionality and check the output settings on the control panel. Adjust the power to match material thickness and cutting requirements.
- Suboptimal Cutting Speed: Increase the cutting speed through the machine’s control system. Finding the right balance between speed and power is essential for clean cuts.
- Compromised Assist Gas Quality: Ensure high-purity assist gas (typically nitrogen or oxygen) is used. Gas purity directly affects cut quality and burr formation.
- Focal Point Drift: Periodically perform focal point tests, especially for long cutting sessions. Adjust the offset to compensate for any drift caused by thermal effects or mechanical wear.
- System Instability from Extended Operation: If persistent issues occur after long runs, consider a complete system restart. This can resolve software glitches or thermal-related instabilities.
Analysis of the burr on the workpiece when cutting stainless steel and aluminum zinc plate with the laser cutter.
When cutting low-carbon steel, stainless steel, or aluminum-zinc plates with a laser cutter, burr formation is a common challenge that requires careful consideration of multiple factors. The root causes of burrs can vary depending on the material properties and cutting parameters.
For low-carbon steel, initial investigation should focus on key factors influencing burr formation, such as laser power, cutting speed, focal point position, and assist gas pressure. However, simply increasing the cutting speed is not always an effective solution, as it may compromise the laser’s ability to fully penetrate the material, especially when processing thicker plates or highly reflective materials like aluminum-zinc alloys.
In the case of aluminum-zinc plates, which are known for their high thermal conductivity and reflectivity, additional considerations are necessary. The laser’s interaction with these materials can be more complex, often requiring a fine balance between power, speed, and focal point adjustment to achieve clean cuts with minimal burr.
To optimize cutting performance and reduce burr formation, consider the following factors:
- Nozzle condition: A worn or damaged nozzle can disrupt gas flow, leading to inconsistent cuts and increased burr. Regular inspection and replacement of nozzles are crucial for maintaining cut quality.
- Motion system stability: Vibrations or instability in the guide movement can cause fluctuations in the focal point position, resulting in irregular cuts and burr formation. Ensure the machine’s motion system is properly maintained and calibrated.
- Assist gas selection and pressure: For stainless steel and aluminum-zinc plates, nitrogen is often preferred as an assist gas to prevent oxidation. Optimize gas pressure to effectively remove molten material without causing excessive turbulence.
- Focal length and position: Adjust the focal point position relative to the material surface to achieve the optimal power density for clean cuts. This may vary depending on material thickness and composition.
- Cutting parameters optimization: Fine-tune laser power, cutting speed, and pulse frequency (if applicable) based on material-specific requirements. Consider using parameter databases or conducting cutting trials to determine the optimal settings for each material type and thickness.
- Beam quality and optics condition: Ensure the laser beam is properly aligned and focused, and that all optical components are clean and in good condition to maintain consistent cutting performance.
Analysis of the incomplete cutting state of the laser.
After comprehensive analysis, the following factors have been identified as the primary contributors to unstable laser cutting processes:
- Improper nozzle selection relative to plate thickness:
The nozzle geometry and diameter significantly influence the gas flow dynamics and cutting efficiency. Mismatched nozzles can lead to insufficient assist gas pressure or improper beam focusing, resulting in incomplete cuts. - Excessive cutting speed:
When the traverse rate surpasses the optimal speed for a given material and thickness, it can lead to insufficient energy density at the cutting front. This often results in dross formation, incomplete penetration, or irregular kerf width. - Incorrect focal length for thicker materials:
For cutting 5mm carbon steel plates, it is crucial to replace the standard lens with a 7.5″ focal length laser lens. This adjustment optimizes the beam focus depth, ensuring proper energy concentration throughout the material thickness.
Additional factors that may contribute to unstable processing include:
- Assist gas pressure and type mismatch
- Contaminated or damaged focusing optics
- Fluctuations in laser power output
- Improper standoff distance between the nozzle and workpiece
- Material inconsistencies or surface contaminants
The solution for non-normal spark patterns when cutting low carbon steel
Abnormal spark patterns during the laser cutting of low carbon steel can significantly impact the quality of cut edges and overall part precision. If other cutting parameters are within normal ranges, consider the following potential causes and solutions:
- Nozzle degradation:
The laser nozzle may have deteriorated or become damaged. Promptly replace the nozzle with a new one to restore optimal cutting performance. Regular nozzle inspection and replacement should be part of your preventive maintenance schedule. - Cutting gas pressure adjustment:
If immediate nozzle replacement is not feasible, a temporary solution is to increase the cutting gas pressure. This can help compensate for reduced gas flow due to nozzle wear or partial blockage. However, monitor cut quality closely, as excessive pressure may lead to other issues such as increased dross formation. - Loose nozzle connection:
The threaded connection between the nozzle and laser cutting head may have become loose. In this case:
- Immediately halt the cutting operation to prevent further damage.
- Carefully inspect the laser head assembly, paying particular attention to the nozzle connection.
- If loose, securely tighten the threaded connection, ensuring proper alignment.
- Perform a test cut to verify the issue has been resolved.
- Additional considerations:
- Verify the cleanliness of the nozzle orifice and clear any obstructions.
- Check for proper centering of the laser beam within the nozzle.
- Ensure the focal point of the laser is correctly set for the material thickness.
- Examine the condition of the protective lens and replace if necessary.
Selection of Puncture Points in Laser Cutting
The Working Principle of Laser Beam Cutting:
During the laser cutting process, the focused laser beam creates a localized melt pool on the material surface. As the beam continues to irradiate, it forms a depression at the center. High-pressure assist gas, coaxial with the laser beam, rapidly expels the molten material, creating a keyhole. This keyhole serves as the initial penetration point for contour cutting, analogous to a pilot hole in conventional machining.
The laser beam typically travels perpendicular to the tangent of the cut contour. Consequently, as the beam transitions from initial penetration to contour cutting, there’s a significant change in the cutting vector. Specifically, the vector rotates approximately 90°, aligning the cutting direction with the contour tangent.
This rapid vectorial shift can lead to surface quality issues at the transition point, potentially resulting in increased roughness or kerf width variations.
In standard operations where surface finish requirements are not stringent, automated CNC software generally determines puncture points. However, for applications demanding high surface quality or tight tolerances, manual intervention becomes crucial.
Manual adjustment of the puncture point involves strategically repositioning the initial penetration location. This optimization aims to minimize the impact of the vector change on the cut quality. Factors to consider include:
- Material properties (thickness, thermal conductivity)
- Laser parameters (power, frequency, pulse duration)
- Assist gas type and pressure
- Desired contour geometry
By carefully selecting the puncture point, engineers can significantly improve the overall cut quality, reducing post-processing requirements and enhancing part precision. Advanced techniques such as ramping or dimpling may also be employed to further optimize the penetration process.
It’s important to note that while manual puncture point selection can yield superior results, it requires expertise and may increase programming time. Therefore, a cost-benefit analysis should be conducted to determine when this level of optimization is warranted.
Analysis of the burr on the workpiece when cutting stainless steel and aluminum zinc plate with the laser cutter.
When cutting low-carbon steel, stainless steel, or aluminum-zinc plates with a laser cutter, burr formation is a common challenge that requires careful consideration of multiple factors. The root causes of burrs can vary depending on the material properties and cutting parameters.
For low-carbon steel, initial investigation should focus on key factors influencing burr formation, such as laser power, cutting speed, focal point position, and assist gas pressure. However, simply increasing the cutting speed is not always an effective solution, as it may compromise the laser’s ability to fully penetrate the material, especially when processing thicker plates or highly reflective materials like aluminum-zinc alloys.
In the case of aluminum-zinc plates, which are known for their high thermal conductivity and reflectivity, additional considerations are necessary. The laser’s interaction with these materials can be more complex, often requiring a fine balance between power, speed, and focal point adjustment to achieve clean cuts with minimal burr.
To optimize cutting performance and reduce burr formation, consider the following factors:
- Nozzle condition: A worn or damaged nozzle can disrupt gas flow, leading to inconsistent cuts and increased burr. Regular inspection and replacement of nozzles are crucial for maintaining cut quality.
- Motion system stability: Vibrations or instability in the guide movement can cause fluctuations in the focal point position, resulting in irregular cuts and burr formation. Ensure the machine’s motion system is properly maintained and calibrated.
- Assist gas selection and pressure: For stainless steel and aluminum-zinc plates, nitrogen is often preferred as an assist gas to prevent oxidation. Optimize gas pressure to effectively remove molten material without causing excessive turbulence.
- Focal length and position: Adjust the focal point position relative to the material surface to achieve the optimal power density for clean cuts. This may vary depending on material thickness and composition.
- Cutting parameters optimization: Fine-tune laser power, cutting speed, and pulse frequency (if applicable) based on material-specific requirements. Consider using parameter databases or conducting cutting trials to determine the optimal settings for each material type and thickness.
- Beam quality and optics condition: Ensure the laser beam is properly aligned and focused, and that all optical components are clean and in good condition to maintain consistent cutting performance.
Analysis of the incomplete cutting state of the laser.
After comprehensive analysis, the following factors have been identified as the primary contributors to unstable laser cutting processes:
- Improper nozzle selection relative to plate thickness:
The nozzle geometry and diameter significantly influence the gas flow dynamics and cutting efficiency. Mismatched nozzles can lead to insufficient assist gas pressure or improper beam focusing, resulting in incomplete cuts. - Excessive cutting speed:
When the traverse rate surpasses the optimal speed for a given material and thickness, it can lead to insufficient energy density at the cutting front. This often results in dross formation, incomplete penetration, or irregular kerf width. - Incorrect focal length for thicker materials:
For cutting 5mm carbon steel plates, it is crucial to replace the standard lens with a 7.5″ focal length laser lens. This adjustment optimizes the beam focus depth, ensuring proper energy concentration throughout the material thickness.
Additional factors that may contribute to unstable processing include:
- Assist gas pressure and type mismatch
- Contaminated or damaged focusing optics
- Fluctuations in laser power output
- Improper standoff distance between the nozzle and workpiece
- Material inconsistencies or surface contaminants
The solution for non-normal spark patterns when cutting low carbon steel
Abnormal spark patterns during the laser cutting of low carbon steel can significantly impact the quality of cut edges and overall part precision. If other cutting parameters are within normal ranges, consider the following potential causes and solutions:
- Nozzle degradation:
The laser nozzle may have deteriorated or become damaged. Promptly replace the nozzle with a new one to restore optimal cutting performance. Regular nozzle inspection and replacement should be part of your preventive maintenance schedule. - Cutting gas pressure adjustment:
If immediate nozzle replacement is not feasible, a temporary solution is to increase the cutting gas pressure. This can help compensate for reduced gas flow due to nozzle wear or partial blockage. However, monitor cut quality closely, as excessive pressure may lead to other issues such as increased dross formation. - Loose nozzle connection:
The threaded connection between the nozzle and laser cutting head may have become loose. In this case:
- Immediately halt the cutting operation to prevent further damage.
- Carefully inspect the laser head assembly, paying particular attention to the nozzle connection.
- If loose, securely tighten the threaded connection, ensuring proper alignment.
- Perform a test cut to verify the issue has been resolved.
- Additional considerations:
- Verify the cleanliness of the nozzle orifice and clear any obstructions.
- Check for proper centering of the laser beam within the nozzle.
- Ensure the focal point of the laser is correctly set for the material thickness.
- Examine the condition of the protective lens and replace if necessary.
Selection of Puncture Points in Laser Cutting
The Working Principle of Laser Beam Cutting:
During the laser cutting process, the focused laser beam creates a localized melt pool on the material surface. As the beam continues to irradiate, it forms a depression at the center. High-pressure assist gas, coaxial with the laser beam, rapidly expels the molten material, creating a keyhole. This keyhole serves as the initial penetration point for contour cutting, analogous to a pilot hole in conventional machining.
The laser beam typically travels perpendicular to the tangent of the cut contour. Consequently, as the beam transitions from initial penetration to contour cutting, there’s a significant change in the cutting vector. Specifically, the vector rotates approximately 90°, aligning the cutting direction with the contour tangent.
This rapid vectorial shift can lead to surface quality issues at the transition point, potentially resulting in increased roughness or kerf width variations.
In standard operations where surface finish requirements are not stringent, automated CNC software generally determines puncture points. However, for applications demanding high surface quality or tight tolerances, manual intervention becomes crucial.
Manual adjustment of the puncture point involves strategically repositioning the initial penetration location. This optimization aims to minimize the impact of the vector change on the cut quality. Factors to consider include:
- Material properties (thickness, thermal conductivity)
- Laser parameters (power, frequency, pulse duration)
- Assist gas type and pressure
- Desired contour geometry
By carefully selecting the puncture point, engineers can significantly improve the overall cut quality, reducing post-processing requirements and enhancing part precision. Advanced techniques such as ramping or dimpling may also be employed to further optimize the penetration process.
It’s important to note that while manual puncture point selection can yield superior results, it requires expertise and may increase programming time. Therefore, a cost-benefit analysis should be conducted to determine when this level of optimization is warranted.
FAQs
Is It Dangerous To Operate A Laser Cutter?
Laser cutting is an environmentally friendly cutting method that generally does not cause any harm to the body. Compared with ion cutting and oxygen cutting, the laser cutting process produces less dust, weaker light and less noise. However, failure to follow proper safety procedures may result in personal injury to the user or damage to the machine.
1. Be careful with flammable materials when using this machine. Some materials, such as foam cores, PVC materials, highly reflective materials, etc., will not be cut by a laser cutter.
2. When the machine is running, it is forbidden for the operator to leave without authorization, so as to avoid unnecessary losses.
3. Do not stare at the laser processing operation. It is forbidden to observe the laser with binoculars, microscopes, magnifying glasses, etc.
4. Do not store any explosive or flammable materials in the laser processing area.
What Affects The Accuracy Of Laser Cutting System?
There are many factors that affect the accuracy of a CNC laser cutter, some of which are determined by the equipment itself, such as the accuracy of the mechanical system, the vibration level of the workbench, the quality of the laser beam, the influence of auxiliary gas and nozzles, etc. There are also factors of the material, such as the physical and chemical properties of the material, the reflectivity of the material, and the factors that determine the output power, focal length position, cutting speed, auxiliary gas and other related parameters, according to the specific processing object and the user's quality requirements. , and make appropriate adjustments.
How Does A Laser Cutter Focus?
The choice of the focus position is particularly important because the laser power density has a great influence on the cutting speed. The spot size of the focused laser beam is proportional to the focal length of the lens. In the industrial field, there are three simple ways to determine the cutting focus:
1. Printing method: Move the cutting head from top to bottom, print the laser beam on the plastic plate, and focus on a small printing diameter.
2. Inclined plate method: Use a plastic plate to pull horizontally at an angle to the vertical axis, find a very small point of the laser beam, and focus it.
3. Blue spark method: remove the nozzle, blow air, focus the pulsed laser on the stainless steel plate, move the cutting head from top to bottom, until the blue spark reaches very large.
At present, many manufacturers' equipment has achieved autofocus. The autofocus function can improve the processing efficiency of the laser cutting machine. Thick plate drilling time is greatly shortened. By processing workpieces of different materials and thicknesses, the machine can automatically and quickly adjust the focus to a better position.
How Many Types Of Laser Generators?
At present, the lasers used for laser processing and manufacturing mainly include CO2 lasers, YAG lasers and fiber lasers. Among them, high-power CO2 lasers and YAG lasers are widely used in security processing. Fiber lasers based on fiber bits have obvious advantages in reducing threshold, oscillation wavelength range, and wavelength tuning performance, and have become a new technology in the field of lasers.
How Thick Can A Laser Cutter Cut?
At present, the cutting thickness of laser cutting machine is generally less than 100mm, and it has obvious advantages compared with other cutting methods for materials requiring fine cutting size less than 20mm.
What Are Laser Cutting Machines Used For?
Laser cutting machines are widely used in automobile manufacturing, sheet metal fabrication, kitchenware making, advertising industry, machinery manufacturing, Chassis cabinets, elevator manufacturing, fitness equipment and other industries.
Some Troubleshootings
Troubleshooting
Problems | Symptoms & Causes | Solutions |
Turn on continuously. | 1. First check the motherboard parameters, whether the laser mode is correct. | The laser mode is "analog signal" or "dual head laser control". |
2. The wiring board is broken or the button panel is broken. | Replacing the terminal block or key panel. | |
3. Laser power failure. | Replacing the Laser Power Supply. | |
4. Mainboard failure. | Replace the motherboard. | |
High pressure ignition at work. | 1. First determine the location of the high-voltage ignition, such as the high-voltage connection between the laser tube and the laser power supply, check whether the connector is placed correctly or the underside of the high-voltage support is wet. | Clip the connector to the insulating bracket or dry the damp part with a blower. |
2. Check whether the high-voltage joints are firmly connected and whether there is any virtual connection or virtual welding. | Ensure that the solder joints are free from virtual connections and the butt is firm. | |
3. If the ignition is inside the laser power supply. | Replacing the Laser Power Supply. | |
4. The high-voltage end of the laser tube ignites or still ignites after replacing the laser power supply. | Replace the laser tube. | |
Cleaning is uneven or deep and shallow. | 1. Check the lens and light path. | Clean the lens, adjust the light path. |
2. Check the graphics resolution and scanning accuracy. | Increase graphics resolution and scanning accuracy. | |
3. The laser tube is aging or there is a problem with the laser power supply. | Replace the laser tube or laser power supply. | |
There is a wave phenomenon in the straight line of the outline. | 1. The reflector or focusing lens is loose. | Fix the trolley, or replace the slider. |
2. There is a problem with the mechanical part or the software. | Overhaul of mechanical or graphic parts. | |
Laser light outlet sparks. | 1. If it is used in the rubber plate industry, there are impurities in the offset plate, and this phenomenon is prone to occur, and it should have no effect. | No need to deal with, it is recommended that customers choose high-quality offset plates. |
2. Check the white jet tube of the laser head to see if there is a strong airflow, because the trachea path is long and easy to be broken, blocked or worn. | Clean or replace the white jet tube. | |
3. Check whether the air pump itself is faulty, such as the air output of the air pump is small or does not work. | Replace the air pump. | |
Recycled water heat up fast. | 1. Laser working light intensity is too large. | On the premise of ensuring the cutting depth, the light intensity should be reduced as much as possible. |
2. Continuous uninterrupted work for too long. | Require customers to stop for half an hour every 3 hours. | |
3. Check whether the backflow of the cooling water outlet pipe is normal, whether the water flow is smooth, and whether the latex tube in the laser machine is discounted. | Straighten the water pipes to make the water flow smoothly. | |
4. Check whether the water pump or inlet and outlet pipes are too dirty, and whether the water protection is blocked or not. | Clean the water pump and water pipe, replace the water protection. | |
5. Check whether the water output and water pressure of the submersible pump are normal, if the water output is very small. | Replace the water pump or chiller. | |
Chiller Alarm. | 1. First, ensure that the user's power supply system is normal, and the low voltage may cause the chiller to alarm. | Ensure that the voltage is normal, if necessary, a voltage regulator can be used. |
2. See if the water in the chiller is enough, if the water is too low, it will alarm. | Top up with purified water. | |
3. Whether the water pipe is blocked or discounted, and whether the water protection is blocked, it will cause an alarm. | Clean or straighten water pipes and water protection. | |
4. Whether the water temperature is too high, the water temperature exceeds the limit value, it will cause an alarm. | Change the water often, or stop for half an hour and then start the cutting. | |
5. Check whether the water pump in the chiller is normal, there is no water or the water flow is very small. | Replace the chiller. | |
No display on boot and No button action. | 1. Restart the laser cutting system to see if the beam and the trolley are reset normally. The panel always shows that the power-on reset is in progress. | Check if the connector of the control panel or motor cable is loose. |
2. The power-on reset is normal, press the direction keys and function keys on the machine panel to see if it is normal, if the keys are all normal. | The LCD block is broken, replace it. | |
3. There is no display on the boot panel, and the laser head does not work. | Check whether the board has DC 24V input. | |
4. If the display is normal after the control panel is replaced, the buttons still have no action, and the device is controlled by the data cable to move back and forth, left and right, and there is no action, the board is broken. | Replace the board. | |
Unstable or uncontrolled current. | 1. There is a problem with the main board or wiring board. | Replace the motherboard or terminal block. |
2. There is a problem with the laser power supply. | Replacing the Laser Power Supply. | |
Turn on the laser head or Beam jitter phenomenon. | 1. Check the motherboard parameters first. | Redownload the configuration. |
2. Move the laser head and beam by hand after shutdown. If the resistance is obvious, check the left tensioner and slider. | Clean guide rails, slide blocks, replace tensioning pulleys. | |
3. Check whether the synchronous belt and the bald blowing pipe or the red light are stuck, and whether the beam is seriously offset. | Adjust the beam and belt, straighten out the blowpipe and red light. | |
4. Check whether the motor and driver are faulty. | Replace the motor or drive. | |
5. For models equipped with resistor banks, it is necessary to measure whether the resistance value is normal, if there is any problem. | Replace the resistor bank. | |
6. If the problem still exists, it may be the motherboard failure. | Replace the motherboard. | |
Computer download processing data failure, or show communication failed, or the laser cutter does not move. | 1. Whether the power-on reset is normal, if not normal. | Solve the above faults step by step. |
2. The reset is normal, press the test button to self-test, if the self-test cannot be completed. | Check whether the software engraving or cutting column is selected as "output". | |
3. Self-test can be completed to check whether the grounding is reliable. | Handle the grounding well and meet the relevant requirements. | |
4. Check whether the motherboard data interface is open for welding. | Welding needs to be returned to the factory for maintenance. | |
5. Download to the board through the U disk to perform processing. | Can not be processed, the board is broken. | |
6. Computer USB failure. | Change the USB port or change the computer. | |
Hook not closed. | 1. Measure whether the beam is parallel and diagonal. Under normal circumstances, the left and right deviation is not more than 2MM, and the square diagonal error of 500MM is not more than 0.5MM. | Adjust the parallelism of beams and longitudinal beams to reduce errors. |
2. Check whether the tension of the trolley belt and the beam belt is appropriate, and whether the tension of the belts on both sides is the same. | Adjust the tightness of the belt, do not differ too much on both sides. | |
3. In the power-on state, push and pull the trolley and beam by hand, and move the trolley head up and down gently to see if there is any mechanical gap. | Tighten the motor or drive shaft synchronous wheel, replace the slider. | |
Sweeping or crochet misalignment. | 1. Any graphics that are too fast will cause dislocation. | reduce work speed. |
2. Enlarge the original graphic in the output software to check whether the graphic itself is dislocated. | Correct errors in original graphics. | |
3. Try to make another template to see if there is only a certain graphic that has problems, if the graphic does not. | Graphic data error, re-create the renderings. | |
4. Check whether the timing belt is too loose, and whether the belts on both sides of the beam have the same degree of tension. | Adjust the tension of the timing belt. | |
5. Whether there is a gap between the motor and the synchronous wheel of the transmission shaft. | Fasten the synchro wheel. | |
6. Check whether the beam is parallel, and whether the beam support and the trolley slider are worn. | Adjust the parallelism of the beam and replace the support or slider. | |
7. Motherboard or drive failure. | Replace the motherboard or drive. | |
Sweeping or edging with serrations. | 1. Too fast. | Reduce speed. |
2. If output in BMP bitmap format, check the graphics resolution. | On the premise that the graphics size is correct, try to increase the resolution as much as possible. | |
3. Whether the timing belt of the trolley and the beam is too loose or too tight. | Adjust the tension of the timing belt. | |
4. Check the X-direction tensioner to see if there is a gap due to wear. | Replace the tensioner. | |
5. In the stop state, check whether there is any gap between the trolley or the slider. | Replace the slider or tighten the trolley. | |
6. Check whether the four laser lenses are damaged or loose, especially whether the reflector and focusing mirror above the car head are securely installed. | Fasten loose lenses, or replace damaged lenses. | |
7. Check whether the beam support and the support wheel are worn. | Replacing the support or support wheel. | |
The cleaning effect is not good, the outline is very thick. | 1. Check whether the focal length is correct, especially after cleaning the lens or replacing it with a new lens (note that the focusing lens is directional). | Adjust the correct focus value. |
2. Check whether the four lenses are damaged or too dirty (the lenses are damaged or too dirty, which will scatter the laser light). | Replace or clean lenses. | |
3. Check the quality of the light spot at the light outlet of the laser tube. If there are two points or the light spot is not round, hollow, etc., it is the support point of the laser tube, whether the direction is appropriate, and the laser tube itself. | Adjust the support, rotate the direction, replace the laser tube. | |
Working without laser. | 1. First check whether the laser tube itself emits light (test at the light outlet) the laser tube emits light. | Check whether the lens is damaged and whether the optical path is shifted. |
2. There is no light at the light outlet of the laser tube, check whether the water circulation is normal (see whether the water flow of the water pipe is smooth), if there is no water flow or the water flow is not smooth. | Clean the water pump and straighten out the water pipes. | |
3. The water circulation is normal, whether the laser power indicator light is on, and whether the power fan is rotating. | The laser power supply is broken, replace the laser power supply. | |
4. Press the laser power burst button, if there is no light. | Either the laser power supply or the laser tube is faulty. | |
5. If there is light in the spot. | Water protector is broken, replace it. | |
6. If the water protection signal line is shorted, there is still no light. | The main board or wiring board is faulty, replace it. | |
Sweeping becomes shallower. | 1. Check the working light intensity and speed, and the water temperature. If the speed is too fast, the light intensity is too small, and the water temperature is too high. | Increase the light intensity, reduce the speed, replace the circulating water. |
2. See if the outline depth is normal, if it is normal. | Increase graphics resolution or scan accuracy. | |
3. The outline is still very shallow, or sometimes deep and sometimes shallow. | Whether the lens is dirty or damaged, and whether the optical path is offset. | |
4. Connect the ammeter to see if the current can reach 20MA, but the depth is still not enough. | Laser tube aging, replace the laser tube. | |
The laser cutter sometimes has light and sometimes has no light. | 1. Check whether the lens is too dirty or damaged, and whether the optical path is seriously deviated. | Clean or replace the lens, adjust the light path. |
2. The optical path of the lens is normal, check whether the water circulation is normal, such as intermittent water. | Clean or replace the water pump, unclog the water pipes. | |
3. The water circulation is normal, it may be a water protection failure. | Replace water protection. | |
4. If the problem persists, the motherboard, laser power supply, and laser tube may all cause this phenomenon. | Replace the above accessories alternately and find the reason. | |
After graphic output wrong size. | 1. Check if the plotter unit is 1016 when outputting in PLT format in Coreldraw. | Change the plotter unit to 1016. |
2. See if the resolution is correct. | Recalculate resolution. | |
Machine reset unusual. | 1. The direction is correct when resetting, but when it reaches the apex, the trolley and the beam cannot stop (check the parameters of the main board for the new machine first, if it is correct). | Check if it is stuck during movement, motherboard, sensor failure, replace it. |
2. The beam is reset normally, and the laser head does not reset. It may be that the tensioner is stuck or the motor shaft is broken, and the parameters are wrong. | Replace the tensioner or small motor, modify the parameters, and check the connector of the motor wire. | |
3. Opposite the direction of movement of the beam, and hit the side end. | The motherboard parameters are wrong, stop the machine to correct the motherboard parameters and download the configuration again. | |
4. Drive or motor failure. | Replace the drive or motor. | |
The machine stops cutting halfway, misses cutting, random cutting. | 1. Check the grounding condition of the machine and measure whether the ground wire meets the standard (the resistance to ground should not be greater than 5 ohms). | Transform the ground wire to meet the relevant standards. |
2. Check whether there are errors in the original graphics, such as the graphics have intersections, not closed, missing strokes. | Correct errors in graphics. | |
3. If there is no such problem when doing other graphics, it is only a certain graphics that has such a problem. | Graphic data processing error, re-do the renderings. | |
4. The problem remains. | It may be the problem of the computer serial port and the motherboard of the machine. |
Conclusion
With the rise of advanced cutting technologies, fiber laser cutting systems and CO2 laser cutting machines have been widely adopted across various industries, including automotive, shipbuilding, aerospace, nuclear, machinery manufacturing, and steel production. This has led to an increased demand for laser cutting technology and equipment. However, due to the lack of expertise in applying these advanced techniques, many issues arise during actual use. This article offers a range of processing methods to address common problems encountered in sheet metal laser cutting, providing valuable insights for professionals in the field. The goal is to assist technicians in overcoming these challenges and improving their cutting processes.