Press brake tools stand as the linchpin in the metal forming symphony, with every contour and specification dictating the cadence of bending operations. The choice of press brake tools is no trifling matter; it is a decision that reverberates through the quality, precision, and efficiency of the entire metalworking opus. As we embark on this exploration, we shall unfurl the tapestry of press brake tooling, revealing its nuances and guiding you towards the ideal selection for your production masterpiece.
Introduction to Press Brake Tooling
Press brake tooling, the dynamic duo of punch and die, choreographs the transformation of metal sheets with grace and power. The punch, like a maestro's baton, descends with purpose, applying pressure to coax the metal into the desired bend. The die, its steadfast counterpart, cradles the material, sculpting the bend's form and angle with unerring precision. This partnership is not just mechanical; it is an artistry that shapes the destiny of every workpiece. The choice of these tools is a covenant, binding the fates of bend accuracy, material longevity, and process efficiency. Beyond the conventional, modular and quick-change tooling systems emerge as beacons of flexibility, slashing downtime and breathing life into the heart of machine setups.
Different Press Brake Tooling Systems and Standards
1. European System
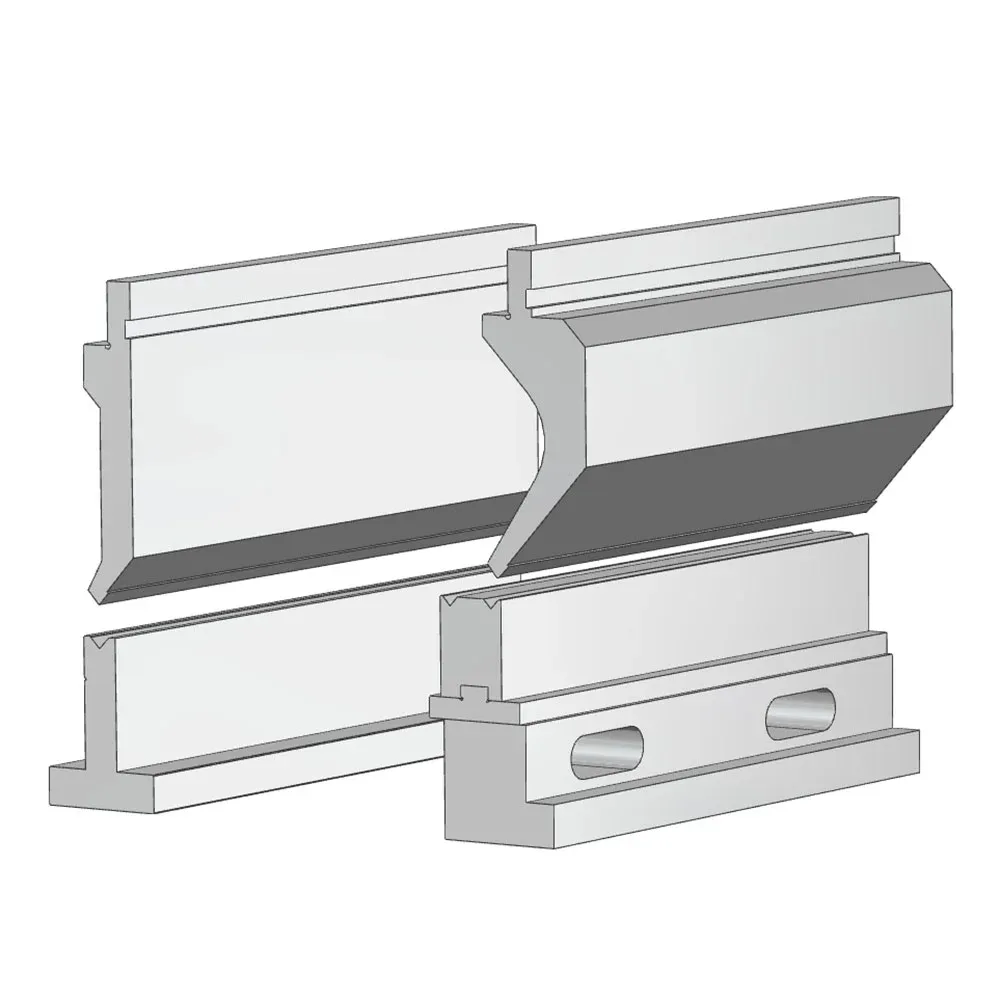
The European system, an emblem of Old-World craftsmanship, reigns supreme in the European market. Its punch and die, with dimensions calibrated to a hair's breadth, are tailored for machines steeped in European tooling heritage. The die and punch angles, be it the jaunty 30° or the stately 85°, are the hallmarks of its precision. Mounted with a clamping system as secure as a knight's grip on his sword, it is a paragon of precision bending across a vast expanse of materials. It is the choice of artisans who demand nothing less than perfection in every curve.
2. Amada System
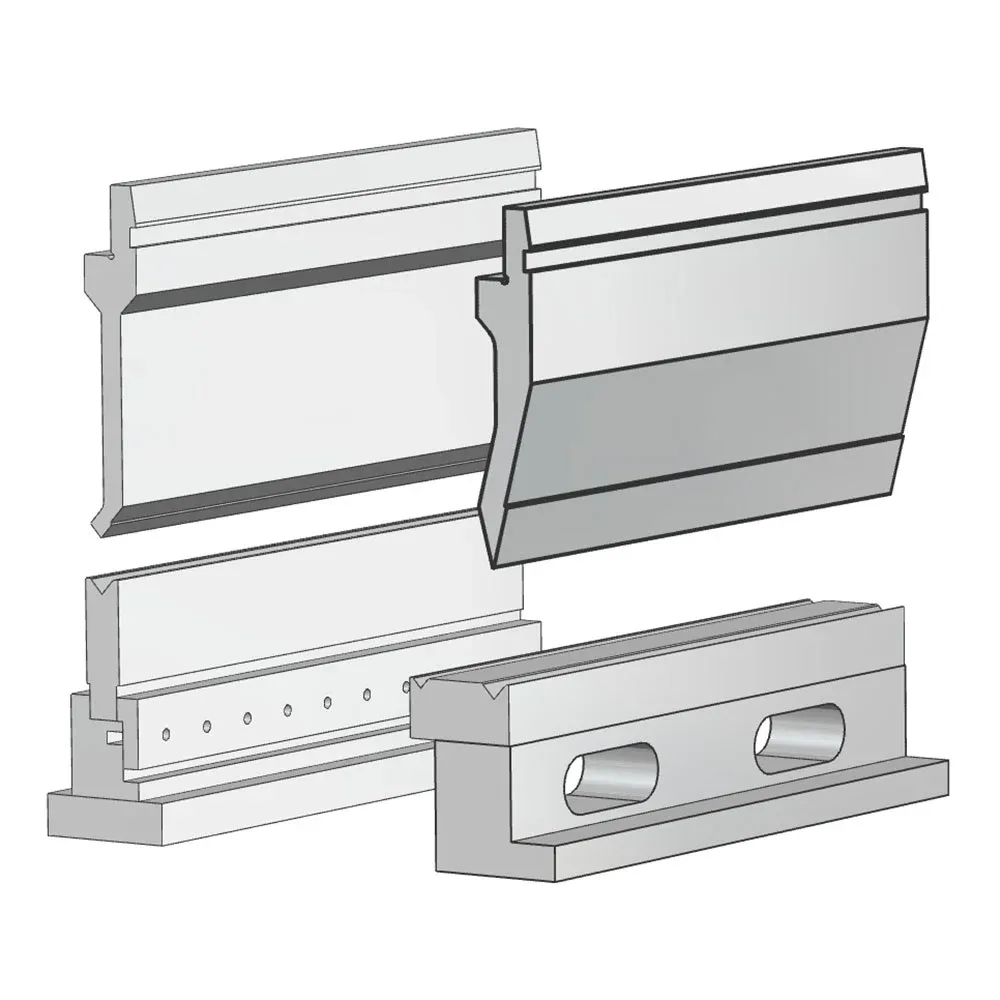
Amada tooling, a vanguard of innovation, marches at the forefront of high-precision bending. Its unique mounting and locking systems embrace the press brake with a lover's embrace, ensuring an unyielding bond. A cornucopia of punches and dies, from the simplest to the most intricate, empowers operators to conjure a symphony of bending variations. Crafted from materials that defy the ravages of time, it is the stalwart companion for high-volume production, where reliability is the currency of success.
3. Trumpf System
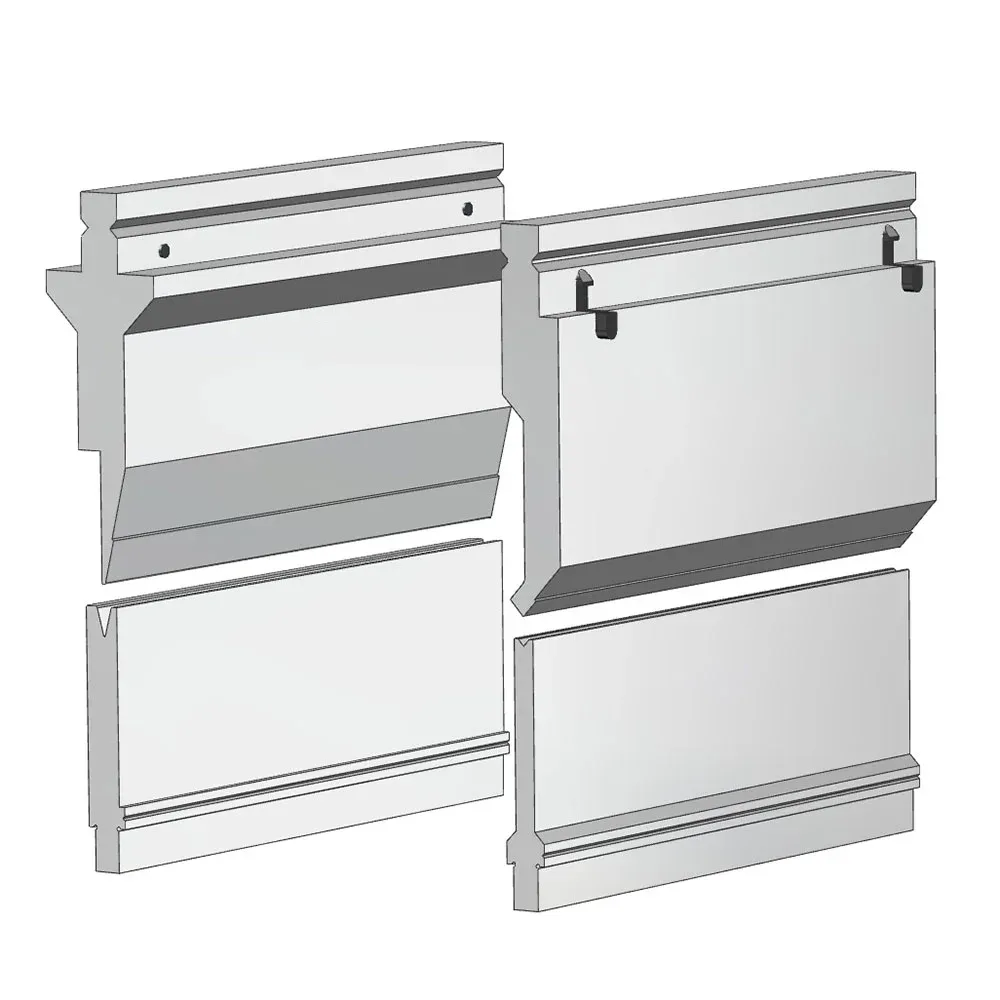
Trumpf, a titan in the press brake realm, bequeaths a tooling system engineered for speed and precision. The quick-change functionality is a magician's sleight of hand, whisking tools in and out with a flourish, banishing downtime to the shadows. Tailor-made for Trumpf press brakes, it is a precision instrument, each tool a virtuoso in the high-stakes performance of accurate and repeatable bending. In the arena of high-precision applications, it is the undisputed champion.
4. LVD System
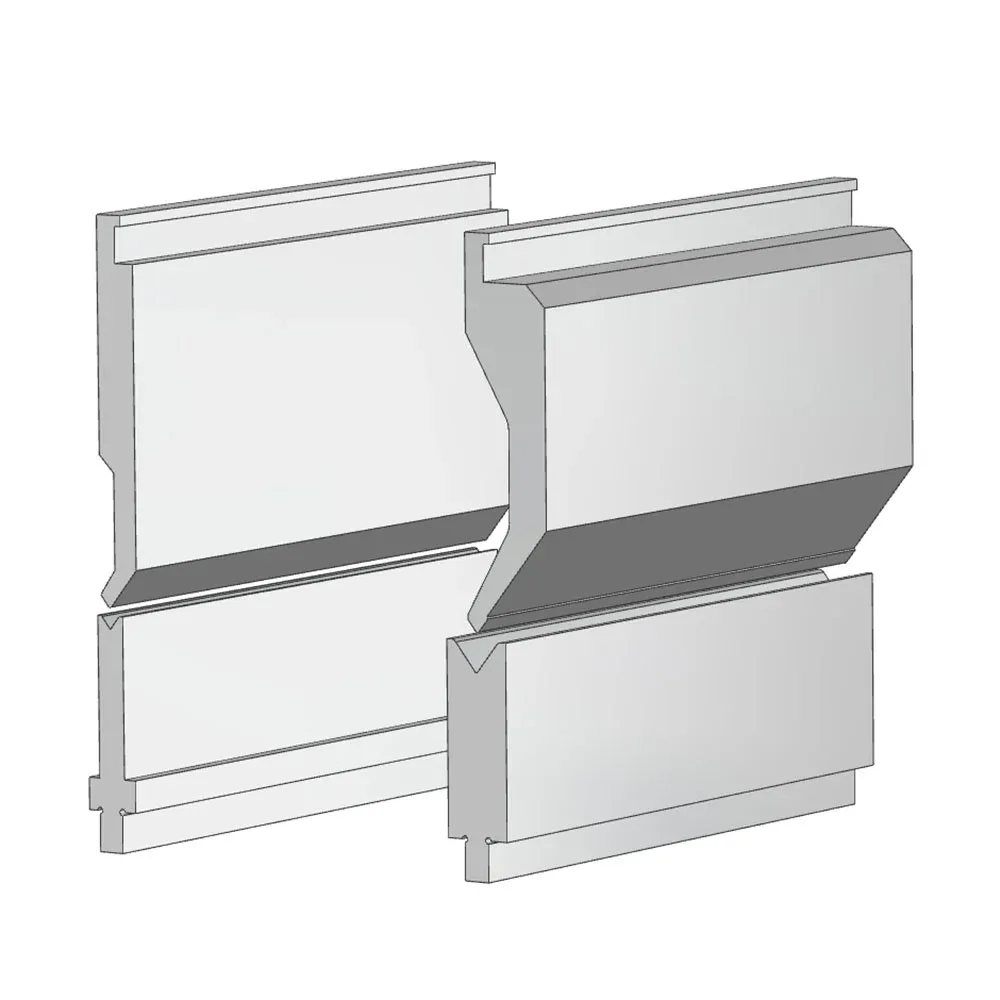
LVD, a maestro of sheet metal bending, presents a tooling system suffused with flexibility. Adhering to international standards, it is a global citizen, harmonizing with diverse press brake systems. Its modular tooling is a modular marvel, a set of building blocks that allows users to erect bespoke tool setups for every bending conundrum. Precision and versatility are its twin mantras, enabling it to tame materials and thicknesses of every ilk.
5. Wila System
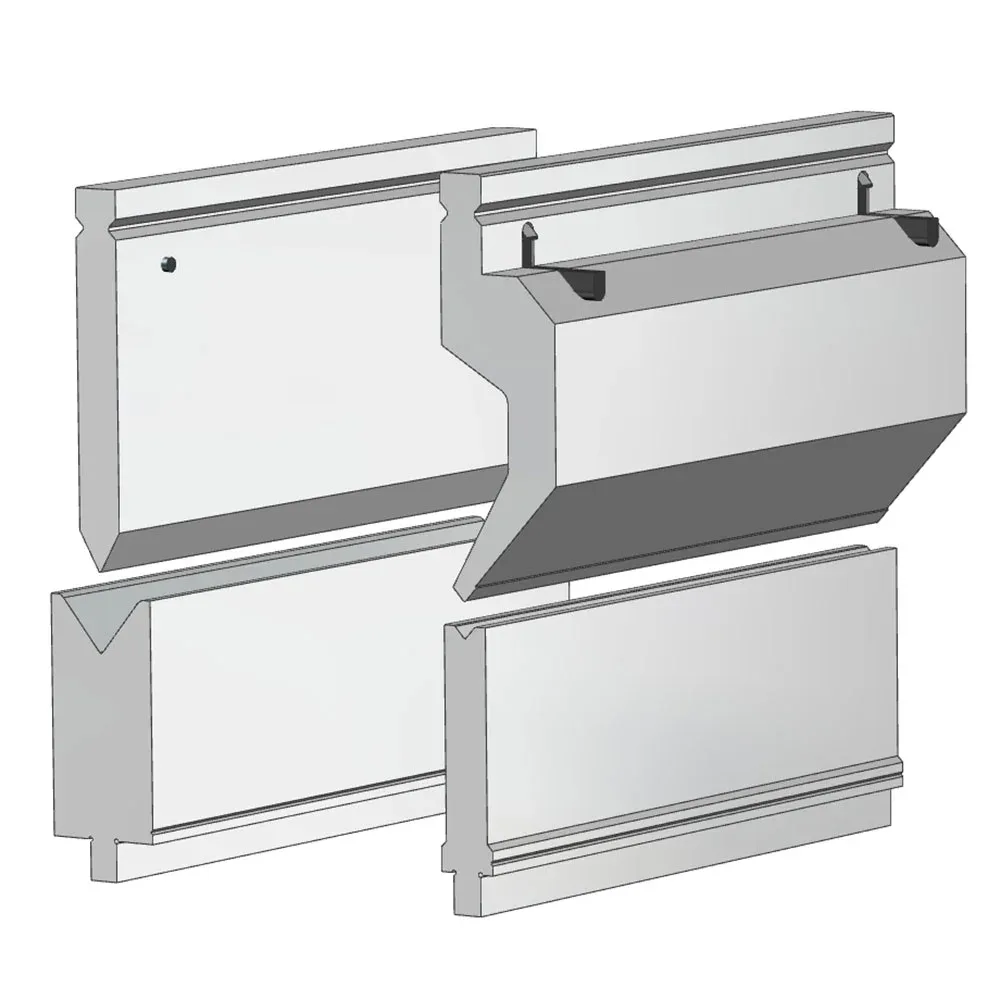
Wila tooling systems, crafted with the passion of master artisans, are a testament to quality and innovation. The clamping systems, a mechanical ballet of security, hold fast even under the most Herculean loads. Forged from materials of the highest pedigree, they endure the trials of time and labor, their performance as consistent as the northern star. From the simplest bends to the most labyrinthine tasks, they are the trusty steeds of the bending journey.
6. American System
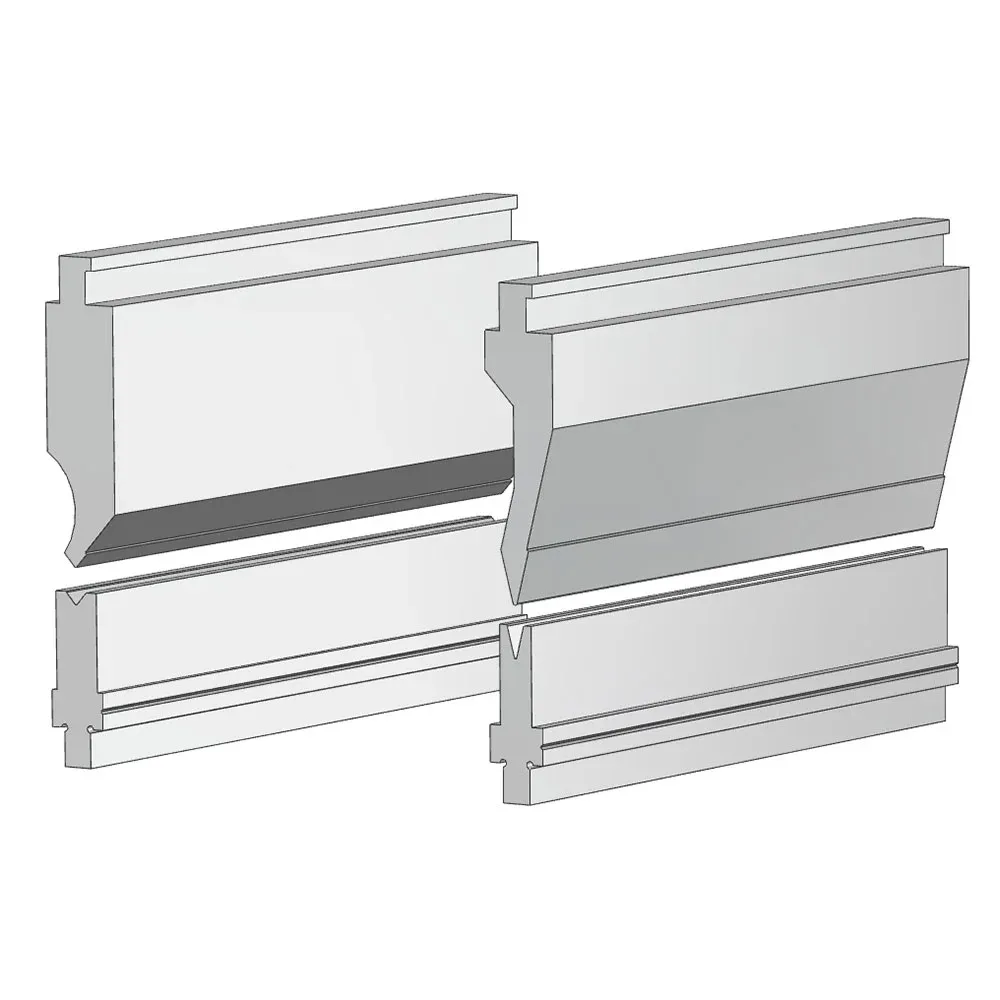
The American system, a homegrown hero in the United States and Canada, wields tooling with dimensions and designs as unique as the American spirit. With a die profile that cuts deeper than its European counterparts, it is the weapon of choice for heavy-duty bending, where titanic plates yield to its might. The hook-and-clamp mechanism, a mechanic's handshake, facilitates tool changes with ease, ensuring the rhythm of production never falters.
How to Choose the Right Press Brake Tools
1. Material Type and Thickness
The material, that elemental protagonist, dictates the tooling's destiny. Hardened materials like stainless steel or high-strength steel demand tools of indomitable strength, able to withstand the crucible of pressure and wear. Thicker materials, behemoths of the metal world, call for dies of greater depth and expanse, a fitting stage for their transformation.
2. Bend Angle and Radius
The bend angle and radius, the geometric architects of the workpiece, decree the form of punch and die. A sharp bend, a delicate incision, requires a die opening as precise as a surgeon's scalpel. A wide bend, a sweeping curve, demands a die of broader girth. Your tooling system must be the pliable clay in the hands of these geometric masters.
3. Tooling System Compatibility
Compatibility, the golden thread that weaves safety, efficiency, and precision into the fabric of production. Choose tooling that melds with your press brake machine's essence, for different manufacturers spin their tooling tales in unique tongues. To stray from this harmony is to court chaos in the workshop.
4. Tolerances and Precision
In the rarefied air of high-precision projects, quality tooling is the oxygen that sustains success. Systems like Amada or Trumpf, precision's paladins, maintain tolerances as tight as a drum. While others, like the European system, offer a more versatile yet still accurate embrace, each has its place in the pantheon of precision.
5. Cost vs. Quality
The scales of cost and quality must be balanced with the wisdom of a sage. High-end systems like Trumpf or Wila, laden with features and promises of longevity, may command a princely sum. Yet, depending on your production saga and budgetary ballad, a more modest tooling system may prove the perfect refrain.
6. Availability of Tooling Parts and Support
The lifeblood of your tooling lies in the availability of spare parts and the succor of support services. Manufacturers such as LVD, Amada, and Wila unfurl a safety net of global service networks, ensuring your tools are nursed back to health and primed for every bending battle.
FAQs
Can I use European-style tools on an American press brake machine?
In most cases, European-style tools are not directly compatible with American press brake machines due to differences in mounting systems and tool dimensions. The American system typically uses a hook-and-clamp mechanism and has specific die profiles that differ from the European standards. It is crucial to use tools that are specifically designed for your machine's tooling system to ensure proper functioning, safety, and accuracy.
How often do I need to replace press brake tools?
The frequency of tool replacement depends on several factors such as the volume of production, the type of material being bent, and the quality of the tools. High-volume production with abrasive materials like stainless steel will wear out tools more quickly. Generally, if you notice a significant decrease in bending accuracy, increased burrs or marks on the workpiece, or visible signs of wear on the punch or die, it may be time to consider replacement. Regular maintenance and proper tool usage can extend the lifespan of the tools.
Are quick-change tooling systems worth the investment?
Quick-change tooling systems can be highly beneficial, especially in production environments where minimizing downtime is critical. They allow for rapid tool swaps, reducing setup times between different bending jobs. While they may have a higher initial cost compared to traditional tooling, the long-term savings in increased productivity and flexibility often make them a worthwhile investment. If your production involves frequent changes in tooling for different parts or if you have tight production schedules, a quick-change system can significantly enhance your operational efficiency.
How do I ensure the accuracy of bends when using press brake tools?
To ensure accurate bends, first, select high-quality tooling that is compatible with your machine and designed for the required precision. Properly calibrate your press brake machine regularly to maintain its mechanical accuracy. Set the correct tooling parameters such as punch and die clearances according to the material thickness and type. Additionally, train operators to use the tools and machine correctly, following standard operating procedures. Performing test bends and adjusting based on the results before starting full production runs can also help achieve accurate bends.
Can I retrofit my existing press brake machine with a different tooling system?
Retrofitting an existing press brake machine with a new tooling system can be complex and may not always be feasible. It depends on the machine's design and its compatibility with the new tooling's mounting and mechanical requirements. Some machines may require significant modifications to accommodate a different tooling standard, which can be costly and time-consuming. It is advisable to consult with the press brake manufacturer or a tooling specialist to assess the viability and potential implications of retrofitting before proceeding.
Conclusion
The choice of press brake tooling is a journey through a labyrinth of standards and systems - European, Amada, Trumpf, LVD, Wila, and American - each a world unto itself, brimming with strengths and suited to different production odysseys. By heeding the clarion call of material, bending requisites, machine compatibility, and cost, you can fetch a path of enlightenment, optimizing your press brake operations into a symphony of efficiency and quality that will echo through the annals of metalworking.