How do you choose the right sheet metal cutting equipment? With numerous options ranging from traditional shears to advanced laser cutters, selecting the best tool can be daunting. This article explores the features, advantages, and limitations of various cutting methods such as flame, plasma, and waterjet cutting. By understanding these factors, you’ll be equipped to make an informed decision tailored to your specific needs. Dive in to discover which equipment offers the efficiency and precision your projects demand.
Introduction
With the continuous advancement of sheet metal processing technology, China’s manufacturing capabilities are rapidly evolving, narrowing the gap with developed countries.
Many leading international companies are shifting their production facilities to China, bringing innovative approaches to sheet metal processing techniques.
Traditional sheet metal cutting equipment includes a range of devices such as numerical and non-numerical control shears, presses, flame cutting, plasma cutting, and high-pressure water cutting. These machines have a significant market presence and are known for their cost-effectiveness.
While they may have some limitations compared to modern laser cutting technology, these traditional machines offer distinct advantages in certain applications.
By reviewing the descriptions of various sheet metal cutting tools below, you can determine which equipment best suits your needs and gain a better understanding of how to cut sheet metal effectively.
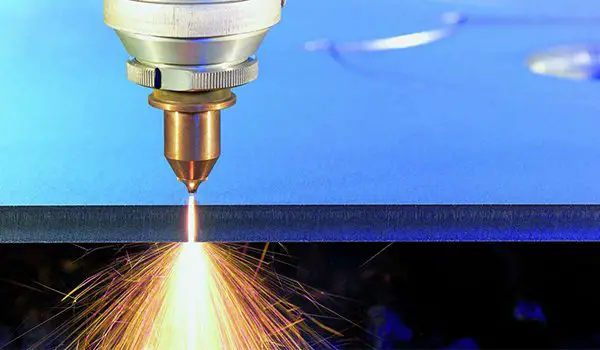
What Are types of Sheet Metal Cutting Equipment
Sheet metal cutting equipment comes in various types, each designed for specific applications, materials, and production volumes. The most common types of sheet metal cutting equipment include both traditional and modern technologies. Here's an overview of the key types:
1. Shears (Manual or Powered)
- Manual Shears: Operated by hand, these are typically used for small-scale operations or light-duty tasks. They are suitable for straight cuts on thin sheets of metal.
- Powered Shears (Guillotine Shears): These machines are powered by hydraulics or motors, allowing for more precise and efficient cutting of thicker materials and larger volumes. They are widely used in metal fabrication shops.
Advantages: Simple, cost-effective, and fast for straight cuts. Suitable for cutting thinner materials.
Limitations: Limited to straight cuts; not ideal for complex shapes or thick materials.
2. Press Brakes
- Function: Primarily used for bending and shaping sheet metal, press brakes can also be equipped with shearing blades to cut sheet metal. These machines use a set of dies to apply force to the material and make precise cuts.
Advantages: Versatile for bending and cutting, suitable for forming complex parts.
Limitations: Not the primary choice for cutting; used more for shaping and bending operations.
3. Flame Cutting (Oxy-Fuel Cutting)
- Function: Flame cutting uses a mixture of oxygen and fuel gases (such as acetylene) to cut through thick sheets of metal. This process is ideal for cutting carbon steels and thick plates.
Advantages: Effective for cutting thick steel, low cost, and simple operation.
Limitations: Slower and less precise than other methods; may cause warping due to heat.
4. Plasma Cutting
- Function: Plasma cutting uses a high-temperature plasma jet to melt and cut through electrically conductive metals like steel, aluminum, and copper. It is a faster and more precise method than flame cutting.
Advantages: High precision, faster cutting speed, can cut thicker metals (up to several inches).
Limitations: Produces rougher edges compared to laser cutting; limited to conductive metals.
5. Laser Cutting
- Function: Laser cutting uses a focused laser beam to melt, burn, or vaporize the material. It is one of the most advanced and precise methods for cutting sheet metal, capable of creating intricate designs with minimal heat distortion.
Advantages: Highly precise, capable of cutting thin and thick metals with minimal distortion. Ideal for complex shapes and fine details.
Limitations: Expensive initial investment and maintenance. May not be cost-effective for cutting very thick metals.
6. Waterjet Cutting
- Function: Waterjet cutting uses a high-pressure stream of water mixed with abrasive particles to cut through materials. It is capable of cutting a wide variety of materials, including metals, without generating heat.
Advantages: No heat distortion, can cut almost any material, precise and versatile.
Limitations: Slower than laser cutting; can be costly, especially for thicker materials. Requires a large space for the equipment.
7. Wire EDM (Electrical Discharge Machining)
- Function: Wire EDM uses a thin wire electrode and electrical sparks to cut through metal. It is ideal for creating intricate, high-precision parts from hard metals.
Advantages: Exceptional precision and ability to cut complex geometries with tight tolerances.
Limitations: Slow process, not suitable for large-scale production or cutting thick materials.
8. Punching
- Function: Punching involves using a punch press to force a die into a sheet of metal, creating holes, slots, or other shapes. This process is often used for high-volume production.
Advantages: Fast and cost-effective for producing repetitive shapes or holes in large quantities.
Limitations: Limited to punching holes and shapes, not ideal for cutting complex contours.
9. Nibbling
- Function: Nibbling uses a tool with a series of small blades to cut along a path, creating a series of small, overlapping cuts. It is suitable for cutting complex shapes or curves in thinner metals.
Advantages: Good for cutting curves and intricate shapes.
Limitations: Slower than other methods and produces rougher edges.
10. Bandsaw Cutting
- Function: A bandsaw uses a continuous loop of toothed metal to cut through sheet metal. This process is more commonly used for cutting thicker materials or for creating straight cuts.
Advantages: Can cut through thick metals; versatile in handling different materials.
Limitations: Slower than plasma or laser cutting; limited to straight or simple cuts.
11. CNC Laser Cutting
- Function: A more advanced version of laser cutting, CNC (Computer Numerical Control) laser cutting uses computer programming to control the laser for cutting complex and highly accurate designs. This method is widely used in the production of parts with intricate designs and high tolerances.
Advantages: Exceptional precision, fast, and capable of cutting a wide range of metals with minimal heat distortion.
Limitations: High initial cost; may not be cost-effective for thick materials.
What is the sheet metal laser cutting machine?
Computer numerical control (CNC) laser cutting is a sheet metal manufacturing process performed by a CNC laser cutting machine. The main form of sheet metal laser cutting is “vaporized cutting”, in which a laser beam melts the material and high-pressure gas removes the melted material. The 3 main types of laser cutting machines are flying optics; moving materials; and hybrid laser cutting. The flying optical laser cutting machine has a fixed bed for cutting materials, and the laser beam head (optical) moves in the X and Y directions above. The working method of moving the material is very similar to that of a standard punch. The beam is in a fixed position and the material moves in the X and Y directions underneath. The mixer usually moves the workpiece in one (X) direction, while the optical head/beam moves in the vertical (Y) direction.
Most CNC laser cutting machines have a processing range of 0.3 mm to 25 mm, which is suitable for higher power models. The laser cutting machine can cut a variety of materials, including low carbon steel, stainless steel, aluminum, zinc steel, pre-galvanized steel, copper, brass, etc. CNC laser cutting uses various gases to assist the cutting process, including compressed air, nitrogen, and oxygen.
Laser cutting machines are generally faster than CNC punching machines when it comes to thinner gauge materials and fewer individual holes. This is because the initial perforation of the material slows down the speed of the laser cutting machine. This is also true for thicker gauges, as more heat is required to melt the material.
Laser Metal Cutting and Fabrication Basics
Metal cutting is part of the metal fabrication process, which creates new metal structures, such as machines and component parts, by cutting, bending, and assembling metal into new shapes and formats. Industrial metal cutting machines are critical for precisely cutting thin sheets of metal to produce component parts for things we use every day, particularly electronics, automobiles, and medical equipment.
Metal is also laser cut to create circuit boards, casings for wires, car doors, hub caps, and much more. In the medical field, laser-cut metal is used to make hospital beds and gurneys, as well as surgical instruments and orthopedic pins, rods, and plates.
But, despite their importance to the industrial sector, laser cutters aren't just for large, professional metal shops. Today's metal laser cutters are compact and budget-friendly, making them accessible for businesses of all sizes. Thanks to these technological advances, small businesses and hobbyists can now use laser metal cutters to create unique items like intricate signs and plaques, accurate model buildings, stencils, coasters, keychains, ornaments, and even jewelry.
Investing in a laser metal cutter to do your metal cutting in-house is a surefire way to boost your business. Not having to send metal out to be cut by a third party boosts your profitability and puts you in control of your projects' timelines, eliminating wait times that can slow production. Having a laser metal cutter in-house also allows you to take on new types of projects and expand your business offerings, which increases your long-term return on investment.
CO2 Laser vs. Fiber Laser Metal Cutting Machine
There are two major types of laser metal cutters: Fiber and CO2 lasers. Both use intense beams of light to cut through metal and are far more powerful and expensive than metal engravers. CO2 laser metal cutters use oxygen, mirrors, and glass tubes to create and direct their lasers. Fiber laser metal cutters don’t require a support gas because they use rare elements, like erbium, ytterbium, and neodymium, to create an optical laser.
In order to decide which is best for you, consider what types of metal you plan to cut. Each type of metal has different properties that impact how it can be cut. CO2 lasers are excellent for cutting steel and stainless steel but can have trouble cutting aluminum and brass, which are both highly reflective. Fiber lasers are more powerful than CO2 lasers, so they can easily cut through most metals, and are especially good at cutting copper and aluminum.
Since CO2 lasers tend to be cheaper than fiber lasers, they are an excellent choice for small businesses and hobbyists planning to laser etch steel or stainless steel. If you want to cut a larger variety of metals, or need smaller and more precise cuts, a fiber laser may be worth the investment.
What Cutting Method Should I Choose?
Metal-processing applications often present the dilemma of selecting the best metal cutting machine, with each of the main metal-cutting processes having their own characteristics in terms of cutting thickness and accuracy. Here we provide a summary of these characteristics to enable the best metal-cutting option for your application.
Before discussing the technology and capabilities of each procedure, let’s first identify the most pressing issues for metal formers and fabricators surrounding cutting technology in general.
- Equipment purchase and use cost. Each cutting method requires different CNC, dust-removal equipment and CAD/CAM software. Also, consider that a laser cutting machine provides higher speed and precision to cut thin sheets than flame or waterjet, which directly impacts equipment cost. When assessing the cutting cost per unit length or per part, note that this includes costs for gas, nozzles and electrodes, as well as for electricity and water. Sometimes, equipment-acquisition costs and labor costs (e.g., loading and unloading) are shared. Therefore, it’s important to consider the scope of comparisons.
- Ease of Use. This requirement primarily relates to software, especially CNC and CAM software. By integrating professional experience, learning times can be reduced. In some cases, equipment manufacturers integrate features that substitute for experience. For example, some machine providers have integrated complete sets of process parameters directly into the CNC and nesting software, which allows new users to quickly master them while maintaining the same cut quality as more experienced personnel. Although not simple to quantify, this consideration should not be overlooked.
- Productivity. Speed often represents the deciding factor in determining output capacity.
- Precision of cut parts. Many methods are available to determine the accuracy of a part made from metal. Inner holes typically require higher tolerances than outer contours, with many cutting-machine suppliers offering ways to cut better-quality holes. Users often measure the top surface to determine part dimensions, but keep in mind that the slope of the cut can affect bottom-surface dimensions.
- Edge quality and metallurgical properties. Each metal-cutting process differs in effects on metal machinability and forming properties as well as weldability.
- Maintenance needs. To reduce the long-term cost, consider the maintenance needs of machines for the various metal-cutting processes, as well as ease of maintenance.
Now, let’s explore these considerations for systems that employ flame cutting, fine plasma cutting, 3-kW fiber laser cutting and waterjet cutting. To standardize, we will compare the cost considerations and cutting characteristics for complete systems that include a 5 by 10-ft. cutting area, an industrial CNC setup (neither entry level nor maximum configuration) and CAD/ CAM software. As far as purchase price, flame-cutting machines represent the lowest initial cost, followed by plasma, waterjet and fiber laser cutting machines.
Flame Cutting
The oxyfuel cutting process represents the simplest of all cutting methods discussed here. This process involves preheating ferrous material, primarily mild and low-alloy steel, with a gas combustible to reach the "ignition temperature" (approximately 1800 F), then injecting pure oxygen to cause an exothermic reaction with the hot steel, which rapidly erodes the steel.
The flame typically can cut material in thicknesses from 0.25 to 6 in. Multiple flame-torch installations on a machine, simple to do and affordable, greatly boost machine capacity.
CNC oxyfuel machines offer a relatively low cutting speed that requires a high use of gas. Cutting cost becomes more favorable on thicker plate.
To achieve the fastest cutting speed with the highest-quality cut, flame CNC cutting machines should be operated by highly skilled operators, though advances in the machinery enable use by less-skilled operators in some cases. Even so, due to long preheating times and slow cutting speeds, oxyfuel cutting typically lacks in productivity compared to other processes. And, flame cutting results in a large heat-affected area with rough edges and hanging slag.
Flame-cutting bed maintenance, a simple affair, is performed easily by the user.
Plasma Cutting
Plasma proves an ideal technology for cutting carbon steel in thicknesses to 2 in., and stainless steel or aluminum in thicknesses to 6.25 in. Achieve cost-effective cutting on carbon steel in thicknesses starting at 0.25 in.
A relatively simple process to learn and use, plasma cutting becomes more effective through the use of the most recent control and process software. In most cases, nesting software includes process parameters to ease use by inexperienced operators. Overall, plasma cutting delivers greater efficiency and speed than other processes, but laser machines cut more quickly for workpiece thicknesses greater than 0.25 in. At thicknesses below 2 in., plasma cuts more quickly than flame. Expect tolerances of ±0.015 in. on carbon steel.
Plasma cutting results in a small heat-affected zone and delivers a weldable edge with no hanging slag. Similar to oxyfuel cutting machines, plasma cutting machines offer simple maintenance.
Fiber Laser Cutting
Fiber laser cutting employs the latest laser technology, with solid-state laser generators operating more efficiently than their CO2-laser counterparts. Additionally, the wavelength of a fiber laser can be used for conduction in thin, flexible fibers—simpler and more flexible than operation of a CO2 laser, which only conducts via mirror reflection.
In operation, a high-energy laser beam melts the work material at cutting edges, with an auxiliary gas, usually oxygen, which is used for cutting carbon steel, blowing out the molten metal.
A 3-kW fiber laser compares in speed and cutting power to a 4-5-kW CO2 laser, and generally cuts carbon steel to 0.75 in. thick.
The speeds and capabilities offered by fiber laser cutting translate to a higher initial cost for basic 5 by 10-ft. machines, as their cutting beds require higher motion accuracy than other cutting machines.
Laser cutting delivers the most cost-effective process when processing thinner material. Cutting speed drops as thickness increases.
Expect tolerances of ±0.01 in. on thin material—superior to plasma cutting and comparable to waterjet—with a heat-affected zone slightly smaller than that of plasma. General maintenance of fiber laser cutting machines can be mastered by users, and they are easier to maintain than their CO2 counterparts.
Waterjet Cutting
Waterjet cutting, a long-standing technology, can be used on a variety of materials, from food to granite to metal. Waterjets offer two major advantages over other cutting processes: the absence of a heat-affected zone and the ability to cut almost any material.
Pure water will cut soft materials, via a high-pressure stream (40,000 to 66,000 psi) of water compressed using a nozzle. This increases the flow rate as well as the energy density. Abrasive sand, when added to the water stream, acts as a saw tooth to add cutting capability. State-of-the-art waterjet pumps can produce water streams at pressures to 100,000 psi. Higher pressures, resulting in faster cutting speeds, can translate to increased machine downtime due to more-frequent replacement of pump seals. Waterjet cutting delivers high accuracy, but a relatively slow cutting speed.
These slow cutting speeds can make waterjet cutting machines more expensive to operate than other cutting technologies, but require less-experienced operators than other machine types and offer simple maintenance. Note that waterjet machines cut aluminum more quickly than carbon and stainless steels, and offer precision and accuracy with, again, no heat-affected zones or changes to material metallurgy. Cut-edge quality relates to the grit used and the cutting speed—the slower the cutting speed, the higher the cut quality.
Shears
Numerical Control (NC) shears are primarily designed for straight line cutting and can cut sheets up to 4 meters in length. However, they are limited to cutting only straight lines and are suitable for industrial applications that only require straight line cutting after flattening.
Punch Press
CNC/turret punch presses offer greater versatility in machining curves, as one punch can be equipped with one or more sets of square, round, or other specialized punch molds. They are typically used for specific sheet metal work, most notably in the cabinet industry. The main processing techniques include straight-line cutting, cutting square and round holes, and producing relatively simple and fixed patterns. These presses are mainly used on carbon plates with a thickness of less than 2mm, and the cutting area is typically in the range of 2.5m x 1.25m.
However, the use of punch presses for cutting stainless steel plates with a thickness greater than 1.5mm is not recommended as it leads to high mold consumption due to the high viscosity. Additionally, punch presses are limited in their ability to punch thick steel plates, and the resulting surface may be subject to collapse. The high cost and long mold development cycle, as well as low flexibility, are further disadvantages of this method.
In many countries, cutting steel plates thicker than 2mm is generally done using modern laser cutting, instead of punch presses. This is due to the lower surface quality of thick plate punching and shearing, as well as the need for larger tonnage to punch thicker plates. This is considered a waste of resources and is also not environmentally friendly due to the high noise levels generated by the process.
Why choose laser cutting for sheet metal processing?
Laser cutting is the fastest and most accurate cutting technique-especially for sheet metal manufacturing. However, this level of speed and accuracy comes at a price. Purchasing a laser cutting machine is a major investment which is why this equipment appears almost exclusively in advanced manufacturing environments.
Lasers provide excellent quality and precision, can flexibly cut materials into almost any imaginable shape and have the highest level of detail. We believe that there are four reasons to choose laser cutting as your preferred method of sheet metal manufacturing:
- Smooth cut edges
Using laser cutting technology, the light beam hitting the metal plate is completely focused on a specific point, which generates much less heat to the material. This means that the path of the laser is narrowed, resulting in the cleanest cutting edges. This small HAZ (heat-affected zone) combined with the small cut of the machine enables it to cut complex, highly detailed shapes, including holes and lines. This level of speed and accuracy is the main reason why laser technology should be the preferred cutting method in sheet metal manufacturing.
- Minimum warpage
There is always the possibility of warpage in the metal cutting process, but the use of laser cutting technology can significantly reduce warpage. The combination of processing speed and the heat-affected zone of the laser reduces the chance of sheet metal warping or deformation.
- Unlimited customization
The ability to manufacture sheet metal according to your customers’ exact specifications adds to your company’s value proposition and customer appeal. Laser cutting allows you to cut materials quickly and accurately, regardless of the thickness of the metal plate or the complexity of the desired shape. Using the laser cutting method, you can deliver sheet metal jobs exactly according to the customer’s specifications every time.
- Speed and efficiency
Depending on the complexity of the metal type, tolerances, material thickness, and specifications, the laser speed can be as high as 20-70 inches per minute. Although it takes time and expertise to load sheet metal and program the laser cutting machine, when the laser cutting machine is equipped with dual worktables, it can be automatically calibrated and positioned as needed, which simplifies the setup. Modern lasers ensure that the metal plate is placed flat and the machine is programmed to recalculate the position of the shape being manufactured accordingly while continuing to optimize the available space.
What to Look for in a Laser Metal Cutter
Whether you're cutting metal sheets, pipes, or stainless steel and aluminum rods, there is a laser metal cutter made for the task. There are four key factors to consider when choosing a laser fiber metal cutter: Working area, laser power supply, laser speed, warranty and service offerings:
Warranty and Service: Protect your investment by choosing a reputable company that provides training on its machines and backs up its products with a substantial warranty and expert-level technical support.
Working Area: Also known as bed-size, this is the size of the actual table used for cutting metal. Choose a working area that is large enough to fit the size of the metal you are working with but not so big that it is outsized for your space or needs. Make the most of the cutting surface by choosing an open-faced table model.
Laser Power Supply: The higher the laser's power supply wattage, the more power the laser will have to cut through metal. More powerful fiber laser metal cutters come with higher price tags, so look for one that meets but does not exceed your needs so that you're not paying for more power than you'll actually use.
Laser Speed: Laser speed is important to your productivity when cutting metal, but the laser's speed and power supply must be matched so that one does not outpace the other, which could damage the metal you are cutting.
Making the Right Choice
With so many different sheet metal cutting equioments to cut metal, there are a lot of decisions to be made. You should consider your metal type and thickness, accuracy and precision requirements, special tooling requirements, budget, and floor space. These metal cutting machines can take up a lot of space in your workshop and require very specific safety measures to ensure no one is injured during the cutting process.
For more information about how we can help you choose the right metal cutting option, or to discuss with our experts, contact us to see how Cutting Experts can help.