Nowadays, fabricators are more eager than ever to embrace lean production to eliminate waste, streamline workflow, and reduce costs. In the quest for efficiency, one creative approach gaining traction is step bending on press brakes. This technique allows fabricators to achieve large radius bends without the need for costly specialized tooling, offering a cost-effective solution that reduces both tooling inventory and lead times. As customer demands increase, step bending on press brakes becomes a critical method for boosting throughput, providing a competitive edge in the race to meet high demands efficiently.
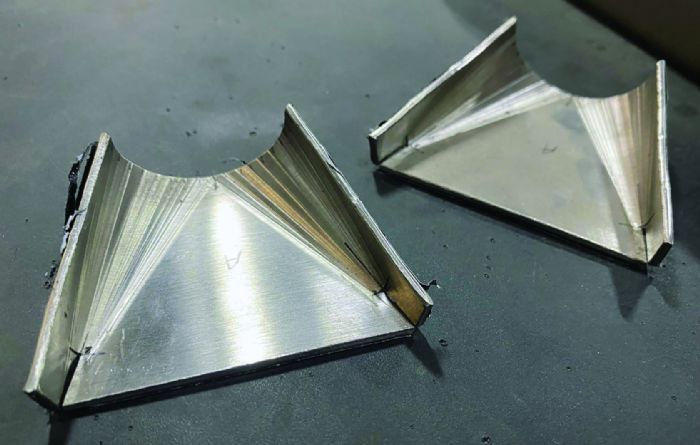
Generally speaking, creating profound radius bends in sheet metal has traditionally required costly and specialized tooling, which is often like a square peg in a round hole when it comes to lean practices. These specialized large-radius tools are like one-trick ponies, only capable of forming large radii and sitting idle on the shelf until a job comes along that requires them, tying up both money and valuable space. Step bending, also known as bump forming or incremental bending, is like a magician's trick that cost-effectively conjures up large bends using common off-the-shelf tooling. It also lays the foundation for crafting the transitional forms commonly seen in the HVAC and food-and-beverage industries. Some forms are as simple as a straight-forward path, like an inline cone; others are more complex, akin to a maze, such as an offset square-to-round, or two intersecting round tubes. What these shapes have in common is the need to guide a product like a ship sailing from one port (opening in one plane) to another. Fabricators can achieve this by adjusting the radius pitch as if they were tuning an instrument, varying it from one side of the step bend to the other, thus altering the achieved radii and shape.
In a job-shop environment that's a bustling mix of high-variety/low-volume jobs and limited tooling options, this process can be a godsend, like a ray of sunshine on a cloudy day. But it's not as effortless as baking a simple cake; it's more like preparing a gourmet meal. Operator skill, the collective wisdom passed down in the shop (tribal shop knowledge), and the product mix all play a role in determining when and where step bending can step in and replace a specialized tool, like a substitute player coming onto the field at just the right moment.
Step Bending Large Radii
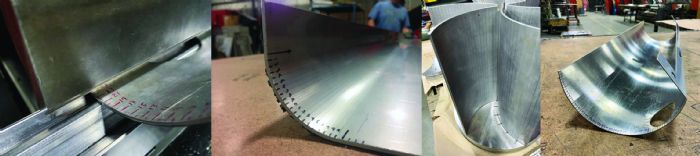
A step bend is like building a staircase, requiring a series of small bends in close proximity. The advantage is that this method doesn't demand specialized tooling, like a hiker who doesn't need fancy gear to climb a small hill. The drawback, however, is that the outcome won't be a perfect, smooth radius. Instead, it resembles a chain of flat links that come together to form what appears to be a radius. These steps will be somewhat visible on the inner surface of the radius where the punch makes contact, like footprints left on a path. The distance between these segments, known as the radius pitch, and each bend angle are like the ingredients that decide the smoothness of the finished radius, much like how the right combination of spices makes a dish delicious. Surface-finish requirements function as the recipe, dictating the choice of angle and pitch. A form with fewer bends will have a larger radius pitch and angle per bend, often leaving a rough, choppy appearance, like a choppy sea. Forms that need to allow liquid or powder to flow smoothly during painting, such as a sleek water slide, often require a very smooth surface. As a result, they'll need more bends to achieve that smoothness, like adding more curves to the slide to ensure a seamless ride.
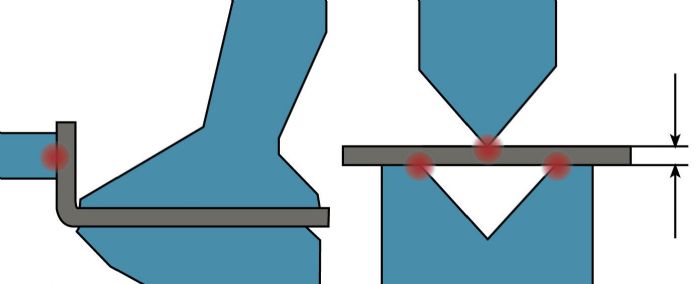
There are numerous ways to calculate a step bend, but the form's requirements are like the compass guiding the way, dictating the method chosen. To calculate the length of each bend segment:
Arc Length/Radius Pitch = Number of bends.
Another formula often used is:
Total Degrees/Degrees per Bend = Number of Bends.
Both formulas are like different tools in a toolbox, attacking the job from different angles. Calculating by dividing the arc length by the radius pitch is often used to ensure that the workpiece crosses the die opening, like a ship sailing through a narrow channel. Whereas, calculating based on the angle can guarantee a soft angle for each bend, like a gentle turn on a winding road. For a smooth finish on most materials less than or equal to 12-gauge stainless steel, a 2-deg. bend or a radius pitch of 0.125 in. should do the trick, like the perfect amount of sugar in a recipe. Thick materials or extremely large radii will change these guidelines, like a different climate requiring a different wardrobe.
Folding or Press Brake Forming
A difficult bending challenge is like a high mountain to climb, involving achieving the small-radius pitch needed for a smooth finish. Sheet folders and press brakes are like two different mountaineering tools that can manage bumped radii, but they go about the task in different ways.
Folding machines are like a pair of strong hands that clamp the workpiece in a stationary position, and a blade or wing bends the flange as if it were bending a thin piece of wire. This creates a bend between a fulcrum and a leverage point, like a seesaw moving up and down. With only two points of contact, the radius pitch can be as small as 0.001 in., like a tiny crack in a wall.
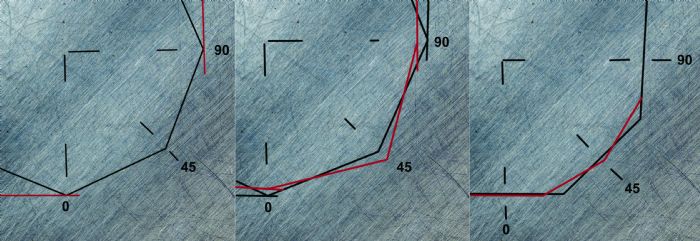
On a press brake, the workpiece slides across three points of contact - the punch-nose radius, and the two shoulder radii of the die opening, like a sled gliding over three bumps. The bend's elongation occurs between the die's shoulder radii - half in front of the punch's contact point and half behind, like stretching a rubber band in the middle. The minimum-radius pitch must be half of the width of the die opening to bridge the gap, like building a bridge across a small stream. This creates a chopped appearance - certainly not the best way to achieve a smooth bend, more like a rough sketch instead of a polished painting. But some simple workarounds can come to the rescue, like a knight in shining armor.
Avoiding Choppiness
The first workaround choice is like walking a tightrope, allowing the workpiece's earlier bends to fall within the die opening. This can be tricky because the depth of penetration into the die is a moving target, like trying to hit a moving bullseye. The first bend is business as usual, like taking the first step on a familiar path. Form, check, adjust, and remit, if necessary, like a golfer adjusting their swing. However, if the operator keeps the same depth of penetration on the second bend, the bend will fall short, like a runner tripping before the finish line. This is because the workpiece no longer lies flat across the die, creating uneven pressure, like an unbalanced scale. The third and all successive hits will follow this same pattern of falling further into the die and under-bending, like a domino effect. This will require more depth corrections until the steps have fully traversed the die opening and begin to equalize (bridging the gap), like leveling a wobbly table.
A second method to reach a smooth radius on the second and later bends is to use a strip of urethane like a cushion to accept the volume of the die, avoiding falling into the die entirely. The urethane removes the die width from the equation as the workpiece will be supported continually throughout the bending cycle, like a safety net for a trapeze artist. This reduces the minimum-radius pitch to 0.001 in., though the elongation still occurs on both sides of the punch, like stretching a piece of taffy on both ends. Notably, this method works well up to 12-gauge thickness; with thicker work, the urethane takes a beating, like a boxer facing a stronger opponent.
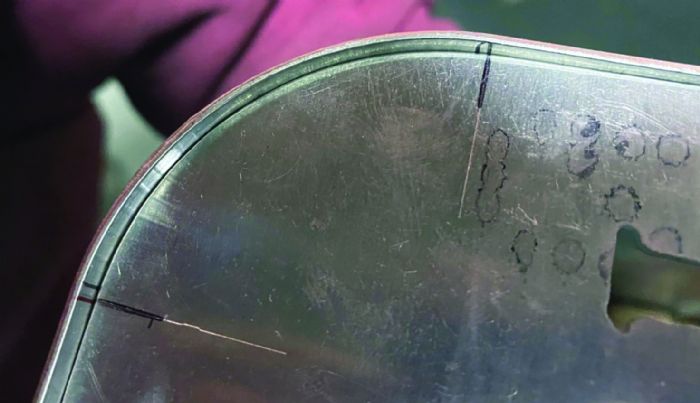
A third approach is bending without a press brake, like finding an alternative route. Folding often gets the nod for step bending because the fulcrum keeps the part clamped and supported throughout the entire forming process, like a mother holding a child's hand. Reinserting an out-of-tolerance, step-bent part on a folder for rework is not really an option because of the clamping beams, like trying to fit a square peg into a round hole. But the concept can be applied when reworking a part slightly out of tolerance outside of a machine, be it a folder or a press brake. If the part is overbent, the operator need only clamp the part down to a worktable and hand-form it open, like unbending a bent wire by hand. Working a part open is much easier than fighting to work the part to a more acute angle, like pushing a boulder uphill versus rolling it downhill.
Dealing With Segments
Layout on a press brake is not as straightforward as it is on a folder, like finding your way through a complex maze instead of a simple garden path. If the operator starts and ends bends using the bend allowance as the arc length, the radius will be too large, like aiming too far and missing the target. This occurs, in part, because in the brake, the material forms between three points of contact, with the punch being a pushing rod in the center, like a car being pushed from the middle. The elongation that occurs in front of the bend line will grow the radius beyond the expected start and end points, like a balloon expanding beyond its intended size. This overshoot will result in a longer arc length, manifesting in either an overbent angle or an enlarged radius, like a crooked picture frame.
This leads to another variable that affects press brakes and folders - segments. Using a gauge cut to the inside radius is like shining a flashlight into a dark corner to reveal areas of the bend that may be too tight or loose. A truly smooth radius will match an inside template perfectly, like a key fitting into a lock. However, a segment will prevent the radius of an inside template from reaching its correct depth, like a barrier blocking the way. The larger the segments, the more the interference, like a traffic jam on a busy road.
Often, operators account for the elongation overshoot and segment interference by cheating the angle of the start and end points, like a clever magician making a small adjustment. Making these two outermost bends at half of the angle of the interior bends may work reasonably well but produces a slightly parabolic shape, like a shallow arch. Moving the start and end points of the arc length inward by half of the radius pitch makes a better result, like adjusting the position of a picture on the wall to make it look just right. This will rotate the interference point of the segments to the desired start and end of the bend's arc, like turning a steering wheel to get on the right track.
Bumping the U
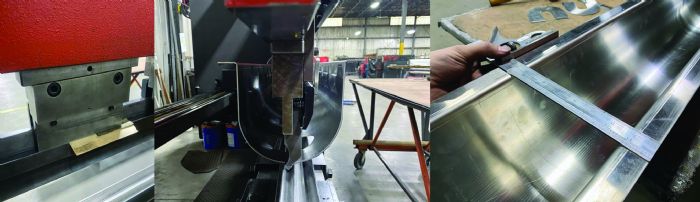
Preventing canoeing is essential to achieving a straight, post-formed part, like keeping a ship sailing on a straight course. Step bending tends to magnify errors, like a magnifying glass making small things look bigger. A 0.5-deg. difference per bend will accumulate to a 5-deg. difference after performing only 10 bends, like small drops of water filling a bucket. However, this may break stride with lean manufacturing rules; using test strips from the drop of the sheet will help ease any sheet-to-sheet variance, like a compass helping to find the right direction. Cutting variability is necessary for a step bend. To do this, the operator performs a 90-deg. bend and checks squareness at multiple locations along the test piece, like a builder checking the corners of a building. This offers the opportunity to adjust, with global crowning and localized shimming on the same material as the workpiece, like adding or subtracting small pieces to make a structure stable. Normal tolerance for sheet metal allows for more variation at the edges of the sheet compared to the center of the sheet, like the edges of a painting being a bit more forgiving. Therefore, the test material should be cut away from the sheet edge, when possible, like trimming the edges of a photo.
Once the machine has been set up and adjusted, the operator forms the outer flanges and begins work on the U section. If the operator forms the U section from the center outward, the part will crash into the ram before completing all of the bends, like a car driving into a wall. Forming from the edges toward the center will ensure clearance between the workpiece and the machine, like a plane flying through a narrow canyon. Care must be taken to verify that the radius is correct near the outer edges before moving toward the center. There will be no choice to remit these bends if the hits are too light, like a missed opportunity that can't be regained.
Often, the operator gauges the workpiece by eye, aligning bend lines with a reference point, like a sailor using the stars to navigate. This can be anything stationary such as the punch nose, the die-shoulder radius, a marker line on the urethane or even a square blade set off the front of the die. This requires great operator skill to move the part by hand to an exacting dimension, like a sculptor carving a detailed statue. They will form a few bends, then check the radius of the workpiece against a template. If the radius is too large, the operator adjusts the machine and remits the workpiece until it falls within specification, like a tailor adjusting a seam. If the radius is too small, the operator will need to either hand-work the part open or flip the part over and use a press to unbend the part slightly, like a mechanic fixing a bent part.
In trying to fix an inconsistent radius by hand, pulling open will lighten and pushing over will tighten, but where the part is held decides which area of the radius changes. Clamping the part down to a worktable, similar to how a folder works, will force the change to occur at a leverage point. Note: This radius manipulation also will affect the finished flange lengths, like a ripple effect.
All of this may lead to more questions:
- What is the smallest punch-nose radius?
- How close must the bends be?
- What size is the lower die opening?
- Should I bridge the gap?
- Is urethane needed?
The answer: That depends, like the outcome of a mystery that unfolds differently each time.
Step Bending on Press Brake Offers Options
Step bending is not limited to small-radius tooling, like a bird that can fly in different directions. Operators also can use large-radius tools to create smooth forms in fewer steps than a small-radius tool, like taking a shortcut on a journey. The smaller the punch radius, the closer the steps must be for a smooth finish, like the closer the stitches on a piece of embroidery for a finer look. A too-small-radius punch-nose will penetrate the material and make the steps more visually pronounced, like a thorn sticking out of a fabric.
Bridging the die width often results in a choppy finish, like a bumpy road. It is possible to choose a smaller-than-usual die opening for step bending because of the reduced penetration into the die space - though tonnage limits still must be seen, like following the rules of a game. Falling within the die opening will produce a smoother finish but urethane is the preferred method because it reduces the radius-pitch requirements, eases gauging, and makes a mar-free finish, like a magic wand that makes everything better.
Despite sharing the press brake operator title, many operators find that the types of jobs they form are completely different, like different actors playing different roles. An operator bumping thick high-tensile-strength AR400 for a construction vehicle has a much different perspective than one bumping 20-gauge, mirror-polished architectural columns. The rules of thumb differ for each, and the tribal knowledge being passed down from generation to generation may work only in the environment for which it was created, like a key that only fits one lock. The best experience is firsthand. Fabricators should grab a piece of test material and explore step bending on press brakes, embracing this technique to enhance their skills and streamline their production process, just like an adventurer setting off on a new journey.