Sheet Metal Forming Processes are of crucial significance in various industries. These processes involve bending and shaping flat materials of a certain thickness into functional forms that are widely utilized in manufacturing and construction. Understanding the different sheet metal forming processes helps engineers and designers choose the most appropriate method for each project.
Opting for the right Sheet Metal Forming Process enhances production efficiency and leads to the creation of high-quality products. In this blog, we will focus on the following commonly used Sheet Metal Forming Processes, examining their importance and relevance for metallurgical professionals and designers.
Table of Contents
Forming Type 1: Bending
Bending is a fundamental sheet metal working process in which metal sheets are shaped along a linear reference to specific angles. It finds extensive applications in areas such as the automotive and construction industries, mainly for manufacturing brackets and frames.
Techniques
- Air Bending: In this technique, the punch is positioned above the sheet without direct contact with the die face. This allows for flexible angles and minimizes tool wear.
- Bottoming: Here, the sheet is pressed into the die until the required angle is achieved. Although it demands more force, it offers excellent accuracy.
- Coining: This is a highly precise method where the material is forced into the die, resulting in a fine bend with minimal spring back.
Benefits
- Cost-Effectiveness: The process can be conducted rapidly with low tooling costs, making it suitable for both high and low volume production.
- Versatility: It can be applied to various materials like aluminum, stainless steel, and other alloys due to its flexibility.
- Customizability: Bending processes enable the creation of special angles and shapes, making them useful for manufacturing specific parts.
Understanding the bending methods simplifies sheet metal manufacturing, ensuring the final product has a perfect shape and contour. This is essential for efficient operation and keeping a high standard of product quality.
Forming Type 2: Stamping
Stamping is an important sheet metal working operation that uses a die for shaping, forming, or cutting metallic sheets. It is highly preferred in the industry due to its precision, which enables the production of items such as car parts and other equipment.
Techniques
- Progressive Die Stamping: This type of die has multiple stations within one die, and the parts are formed in a single cycle. It can perform both cutting and bending simultaneously and is ideal for high production volumes.
- Deep Drawing: This process involves using flat metal sheets to create hollow shapes by passing them through a die. It is commonly used in industries with designs requiring uniform thickness and other complex details.
Benefits
- High Precision: The use of dies allows for obtaining correct and tightly tolerance shapes, which are necessary when close tolerances are needed.
- Rapid Production Rates: Stamping can produce a large number of parts in a brief time, reducing production time and increasing efficiency.
- Material Efficiency: By carefully planning the cutting area to fit the required parts, stamping helps avoid material wastage, making large production runs economical.
Stamping is essential for industries involved in sheet metal fabrication of products that demand high manufacturing rates. Thanks to its speed, reliability, and flexibility, it has become the standard in mass production.
Forming Type 3: Curling
Curling is a specific sheet metal forming technique aimed at creating rolled edges or flanges. This technique involves flexing the material in a circular motion, which sometimes improves the mechanical properties of the metal, making it useful in automotive and HVAC applications.
Techniques
- Single Curling: In this method, the edge of the sheet metal is curved into a smooth, rounded curvature, mainly to give the metal a less sharp edge.
- Double Curling: The edge is bent twice to form a flush edge, which offers better stability and appearance. This is commonly seen in products such as cans and tubular structures.
Benefits
- Improved Safety: Curling cuts the hazards associated with sharp edges, making it a crucial step in many manufacturing industries.
- Enhanced Strength: Generally, curling increases the stiffness of the sheet metal, making it desirable for use in structures.
- Aesthetic Appeal: From an aesthetic perspective, curling can enhance the surface of metal products, giving them a finished look.
By using curling techniques, manufacturers can produce high-quality sheet metal parts that meet both functional and safety requirements while also improving the product's appearance.
Forming Type 4: Spinning
Spinning is a specialized group of sheet metal working technologies that produce axis-symmetrical parts from a rotating metal disk or blank. It is often used in the fabrication of bowls, cones, or cylindrical components in various industries.
Techniques
- Manual Spinning: In this process, a programmer manipulates the spinning tool to create patterns or shapes or for control purposes. It is commonly used for one-off or small-batch production.
- CNC Spinning: CNC technology offers high accuracy and repeatability of operations. CNC spinning machines are used to produce complex shapes and are essential tools in mass production.
Benefits
- Material Efficiency: The process minimizes material wastage as the entire blank material is used, and it is particularly suitable for creating lightweight parts.
- Versatility: Spinning can be applied to various metals such as aluminum, brass, and stainless steel, proving its versatility.
- Excellent Surface Finish: Spinning can produce surfaces that are as smooth as required and polished, cutting the need for further finishing.
Spinning is a versatile forming technique applicable in many manufacturing industries as it enables the production of correct and balanced parts, allowing designers to combine art and function in their designs.
Forming Type 5: Roll Forming
Roll forming is a process in which a strip is passed through a series of rolls arranged in stations to produce a specific shape. It effectively forms advanced geometries with precise dimensions and is highly suitable for the automotive, construction, and electrical gadget industries.
Techniques
- Custom Roll Designs: In roll forming, a metal strip passes through a series of rollers that continuously shape it. Each roller contributes to forming a part of the desired profile.
- Adjustable Rollers: The rollers used in the machines can be easily adjusted or replaced to create different profiles according to various applications.
Benefits
- High Production Efficiency: Once installed, roll forming can generate a large number of parts in a brief time with minimal wastage, making it ideal for large-scale production.
- Consistent Quality: Since the process is continuous, it offers consistent dimensions and shapes, reducing the need for post-processing.
- Strength and Durability: The cold working process involved in roll forming often results in stronger parts of a given material.
Manufacturers can obtain precision-engineered products by applying roll forming, which helps various industries. This method also enhances production efficiency and is thus incredibly useful in manufacturing processes.
Forming Type 6: Stretch Forming
Stretch forming is a unique forming technique in which a metal sheet is placed over a die and stretched to larger shapes. It is highly valued in industries such as aerospace and automotive for manufacturing correct and lightweight parts.
Techniques
- Contour Stretching: In this technique, a sheet is placed over a male die to buy a specific contour. It is particularly useful when shaping designs and curves with high accuracy.
- Flat Stretching: The metal sheet is flattened at its edges and pulled down with even force. It is also an effective way to produce larger but thinner parts.
Benefits
- Excellent Surface Finish: The stretching process provides a certain degree of matte finish, reducing the need for secondary finishing operations.
- Strength and Durability: The stretching process enhances the mechanical properties of the metal, making the part lightweight yet strong.
- Complex Shapes: Compared to regular forming techniques, stretch forming offers more opportunities to create unique patterns and is ideal for custom high-performance parts.
Stretch forming is used by manufacturers aiming to produce intricate and high-precision metal parts. This process meets the standards of modern engineering and design, being correct and durable in various applications.
Tools and Equipment for Sheet Metal Forming
Proper tools and machinery are essential for achieving the best results in any forming process, especially sheet metal forming. In this section, we will describe different forming tools in relation to various forming processes.
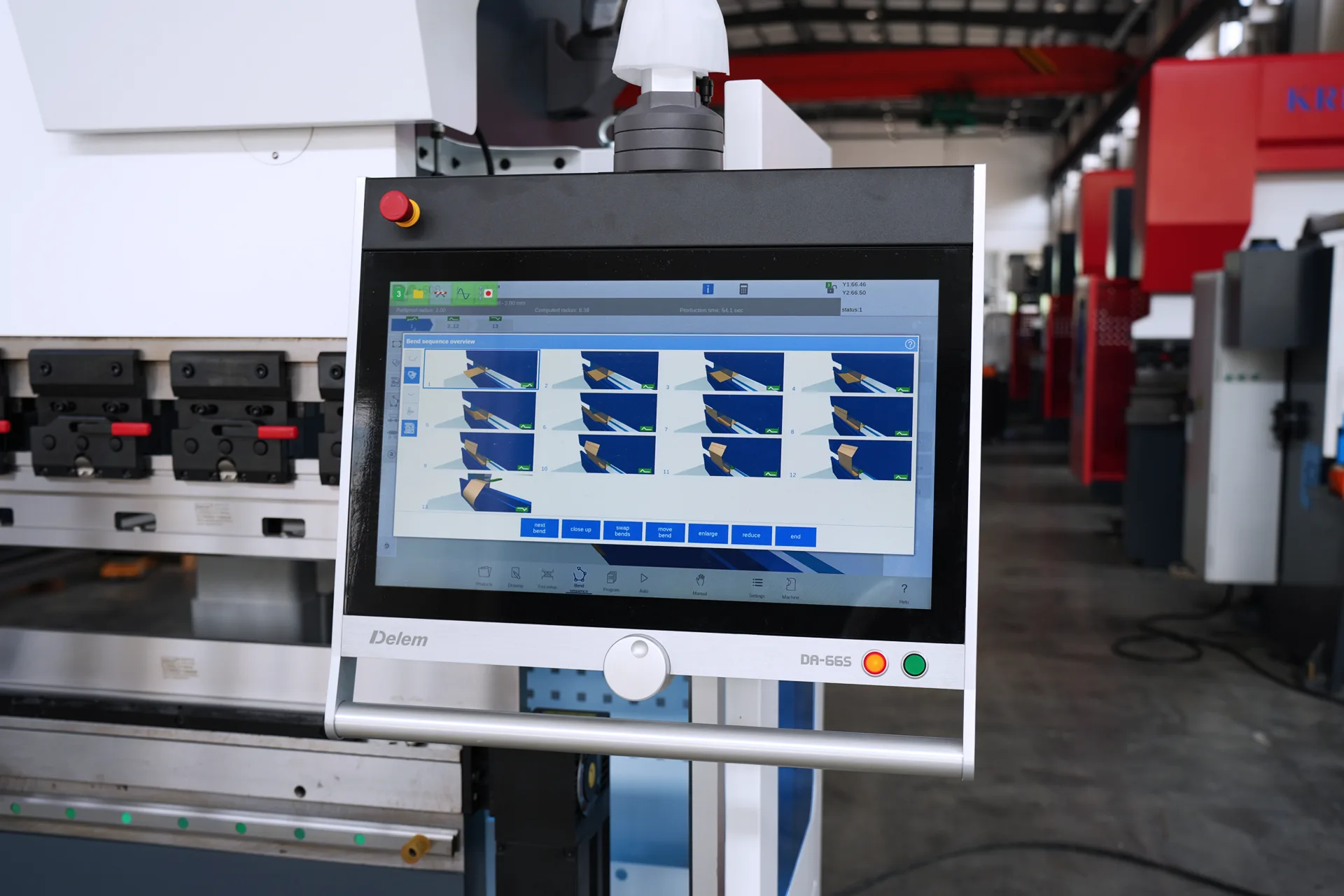
Press Brake
- Function: Machine forming requires a punch to shape sheet metal by hammering, resulting in sharp edges or corners. It ensures high accuracy and reliability in the outcome.
- Types: Hydraulic, mechanical, and electric press brakes are available, each with its own advantages. These types differ in power and control capabilities according to specific manufacturing requirements.
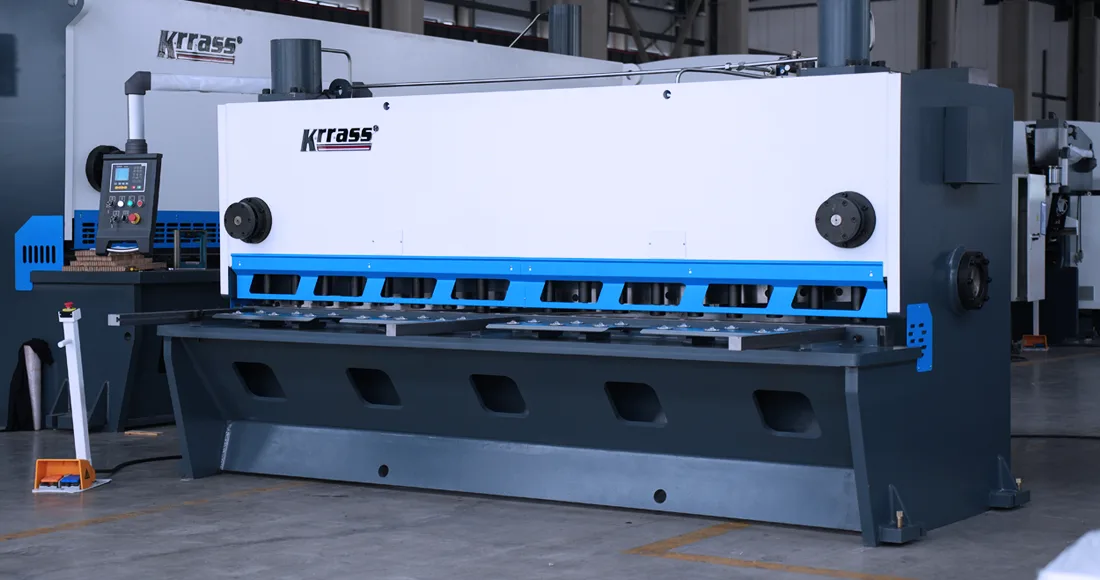
Shears
- Function: Shears are extremely useful tools for cutting metal sheets into the desired dimensions. They play a crucial role in preparing materials before the forming process.
- Types: Both manual and powered shears are used in sheet metal cutting. Powered shears offer added features of effectiveness and accuracy for more extensive operations.
CNC Machines
- Function: CNC machines are used for running cutting and shaping tools. They can create overly complex designs while keeping high tolerances.
- Applications: CNC machines are central to laser cutting and punching processes and significantly improve production ability and efficiency.
Dies and Punches
- Function: Specialized tools like dies and punches are needed in applications such as stamping and coining for forming and cutting metal. They enhance the accuracy and speed of the work.
- Considerations: Maintenance of dies and punches is of immense importance, and careful design is also necessary. They help keep product quality and extend the lifespan of the tools.
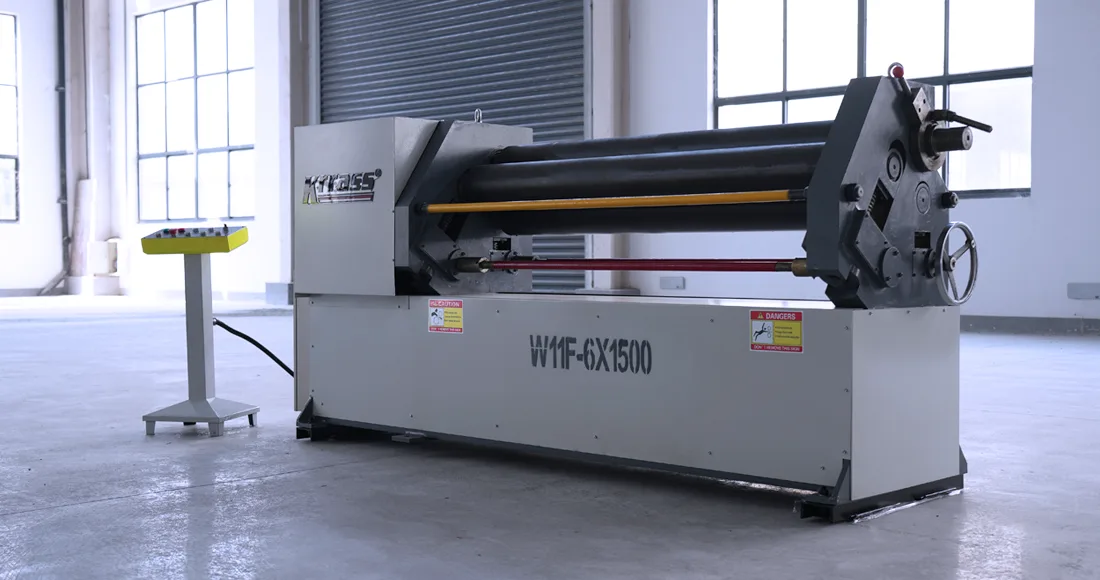
Roll Forming Machines
- Function: Roll forming involves using several machines to create continuous metal formations. When a metal strip passes through a series of rollers, the desired shape is formed.
- Advantages: This method is highly suitable for producing long lengths of profiles with constant shapes, ensuring product uniformity and high production rates.
Welding Equipment
- Function: Welding is used to join the parts of metals after forming. It ensures strong and reliable joints, enhancing the structural integrity of the product.
- Types: MIG, TIG, and spot welding are commonly used processes for joining formed metal parts and guarantee reliable connections.
Safety Equipment
- Function: Safety equipment such as gloves, goggles, and face shields are essential to protect operators during the forming operations. They effectively prevent injuries.
- Importance: Safety equipment meets the priority standards of safeguarding employees from potential harm in the workplace, minimizing the occurrence of accidents.
The use of proper machinery and tools for sheet metal forming is crucial for improving production rates and product quality. Knowledge of available tools enables manufacturers to perfect their processes and achieve better results.
Safety Measures in Sheet Metal Shaping
Safety is of utmost importance in sheet metal forming procedures as the handling of sheets and machinery poses significant risks. Implementing proper safety measures not only protects the lives of workers but also reduces the incidence of accidents.
Personal Protective Equipment (PPE)
- Gloves: Wear gloves that can protect hands from metal slices and shavings. This basic protection reduces the risk of injury.
- Safety Goggles: Safety goggles must be worn during the cutting and shaping of sheets to protect the eyes from flying debris.
- Face Shields: Face shields are useful for protecting facial skin when using high-temperature tools and equipment, preventing arcs and other potential hazards.
Machine Safety Protocols
- Lockout/Tagout (LOTO): Ensure that LOTO procedures are followed to lock the machines and prevent them from starting during maintenance or repair work.
- Emergency Stops: All equipment should be equipped with easily accessible emergency stop buttons to quickly shut down the machinery in case of an accident.
Training and Awareness
- Operator Training: Provide detailed training to operators on how the machinery functions and the potential hazards involved in its operation.
- Safety Drills: Conduct regular safety drills to remind workers of the correct procedures in case of equipment failure or accidents.
Work Environment Maintenance
- Clear Workspaces: Keep the working areas free of tripping hazards and remove any objects that may obstruct access to tools.
- Proper Lighting: Ensure that workstations are well-lit to prevent accidents caused by poor visibility.
Material Handling Practices
- Ergonomic Lifting Techniques: Train employees on proper lifting techniques to minimize the risk of musculoskeletal disorders when managing large metal sheets.
- Use of Mechanical Aids: Encourage the use of forklifts, hoists, conveyors, and other lifting equipment to safely transfer materials.
Regular Equipment Maintenance
- Routine Inspections: All machines should undergo regular preventive maintenance inspections to check for signs of wear and tear or mechanical problems.
- Maintenance Logs: Keep detailed maintenance logs to ensure the safe operation of the equipment.
Implementing effective safety measures in sheet metal shaping benefits both workers and production. Evaluating safety requirements promotes the implementation of safety measures and ultimately reduces risks in the workplace.
Factors to Consider When Choosing a Right Sheet Metal Forming Processes
Selecting the proper sheet metal forming process is crucial for deciding the outcome, productivity, and cost of most manufacturing processes. In this section, we will discuss the fundamental factors that should not be overlooked when making this decision.
Material Type
- Importance: Varied materials such as aluminum, stainless steel, and copper have unique characteristics. These properties play a significant role in deciding the suitable forming process.
- Considerations: The forming method for a material depends on its strength, flexibility, and thickness. Considering these factors is essential for achieving the desired outcome.
Material Thickness
- Description: The thickness of the sheet metal influences the choice of forming process. Thicker materials may require more force and specific technologies like hydraulic press forming, while thinner materials can be formed using bending or stamping tools.
- Guidelines: It is necessary to ensure that the right technique is selected based on the material thickness to obtain the correct results.
Desired Tolerances and Precision
- Importance: The required tolerances decide the relevance of the forming process choice. Some processes are more precise than others, such as laser cutting compared to bending or stamping.
- Options: Depending on the precision requirements, different forming processes can be chosen.
Complexity of Design
- Description: The complexity of the part to be manufactured dictates the proper forming technique. Complex shapes may require advanced processes like computer numerically controlled machining or stamping, while simpler shapes can be managed by bending or shearing.
- Considerations: Taking the time to carefully select the right technique based on the design complexity is crucial.
Production Volume
- Importance: The production quantity has a significant impact on the choice of forming process and tooling. High-volume production often requires specific equipment and processes.
- Guidelines: For high-volume production, stamping or roll forming with specialized tooling is beneficial. In contrast, for lower volumes, more flexible methods like manual bending are preferred.
Cost Considerations
- Description: The forming process choice is highly dependent on the available budget. Manufacturers need to balance the price and quality of their products.
- Factors: Consider the first cost of tooling, production rates, and the amount of wasted materials to assess the total cost implications of the selected method.
Lead Time and Turnaround
- Importance: The urgency of the project decides the choice of forming process. Some processes are faster, while others may involve longer lead times depending on the complexity of the method.
- Considerations: Quicker processes like laser cutting can complete the job rapidly, but more elaborate techniques may result in longer lead times.
By evaluating these factors, manufacturers can decide the most suitable sheet metal forming process for their projects, maximizing efficiency, cost-effectiveness, and product quality.
Cost Considerations in Sheet Metal Shaping
To ensure proper budgetary control and profitability in the sheet metal shaping business, it is essential to understand the various costs associated with these processes. In this section, we will focus on several cost factors related to sheet metal shaping.
Material Costs
- Overview: The type of material has a major impact on costs. Metals like aluminum and stainless steel are often sold based on thickness, quality, and market price.
- Considerations: Bulk purchasing and negotiating with suppliers can significantly affect material costs. This strategy can help businesses reduce costs and increase profits.
Labor Costs
- Overview: Professional skills are needed for running machines, controlling the process, and molding activities. Labor costs depend on workers' skills, regional wages, and the difficulty of the design and execution.
- Efficiency: Training and automation can enhance operational productivity and reduce labor costs compared to traditional employment strategies.
Equipment and Tooling Costs
- Overview: The cost of machinery and tools has a significant impact on the shaping costs. This includes the purchase cost as well as the maintenance expenses over the useful life of the assets.
- Long-term Investment: Investing in high-quality equipment may require a high first outlay but can result in lower maintenance costs and higher accuracy overall.
Setup and Production Time
- Overview: The duration needed for setting up some processes affects the cost in terms of labor and time consumption. Longer setup times lead to lower efficiency and higher expenses.
- Optimization: Coordinating and streamlining the processes can reduce the number of setups and cut down on wasted time and costs, improving overall effectiveness.
Waste and Scrap Rates
- Overview: Minimizing the scrap rate is crucial as material wastage can significantly increase production costs.
- Strategies: Using correct cutting methods can greatly reduce wastage. Additionally, perfecting designs can promote resource efficiency and profitability.
Energy Costs
- Overview: Tooling operations are often energy-intensive, and energy consumption has a considerable impact on operational costs. Conserving energy can help reduce costs.
- Efficiency Measures: Employing energy-efficient tools and techniques can make a significant difference in reducing business costs while being environmentally sustainable.
Overhead Costs
- Overview: Expenses such as facility costs and electricity bills are also part of the overall budget. Proper management of these costs is essential to control the total project cost.
- Management: Hiring competent management to analyze and control overhead costs can contribute to achieving overall best cost in the organization.
By evaluating these cost factors, manufacturers can improve profit margins by perfecting resource use, safeguarding financial resources, and increasing the chances of success.
Future Trends in Sheet Metal Forming Processes Techniques
The sheet metal forming industry is seeing contemporary trends that are set to revolutionize the manufacturing sector. In this section, we will explore the future advancements aimed at increasing precision and energy efficiency in the field.
Automation and Robotics
- Overview: The integration of robotics and automation in sheet metal forming is a new technological development. These technologies increase production speed, efficiency, affordability compared to manual production, and safety.
- Impact: Such advancements enable manufacturers to boost production throughput while keeping high quality standards and reducing the influence of human error.
Smart Manufacturing and IoT
- Overview: The Internet of Things (IoT) has been applied in manufacturing, allowing smart sensors and connected machines to provide real-time data for predictive maintenance.
- Benefits: This technology supports decision-making, reduces emergency response time, and perfects resource allocation, thereby boosting competency.
Advanced Materials
- Overview: Materials such as high-strength steel and lightweight alloys are appearing in sheet metal forming techniques and require special processes for the best characteristics.
- Considerations: Manufacturers will thus have to adopt methods that will allow them to use these products for functions in the automobile and air travel industries among others.
Hybrid Forming Processes
- Overview: Integrated additive manufacturing with other forming technologies is on the rise since it allows the fabrication of complex shapes with minimal scrap material.
- Potential: Creating multiple variations of a product diminishes the amount of flexibility that designers have when designing the product and results in long cycle times when creating complex parts.
Sustainability Initiatives
- Overview: The consumption of illustrative sheet metals is growing green and safe and has included more recycled sheet metals and energy-efficient manufacturing processes.
- Outcomes: Eco-friendly manufacturing processes are equally helpful from the commercial perspective as well they carry a positive message to green consumers and authorities.
Simulation and Digital Twin Technology
- Overview: Simulation software and implementation of the digital twin allow the forming processes of the manufacturers to be simulated and perfected without actual physical implementation.
- Advantages: From experience, the use of simulations helps to cut down on development time, as well as mitigate possible mistakes, while at the same time increasing product quality.
The industry advancement of sheet metal forming is backed up by innovation and flexibility. It may be seen that by welcoming these trends, the manufacturers may only improve the various processes, decrease costs, and remain relevant in the market.
Conclusion
Selecting the most proper type of sheet metal forming process is overly critical in production. The strengths and uses of the different manufacturing techniques mean that manufacturers can further perfect their efficiency and minimize wastage and quality in their projects.
Reviewed by 1 user
He estado usando la máquina de doblado recientemente y debo decir que estoy muy impresionado con su rendimiento. La precisión en el doblado es notable; cada pieza se ajusta perfectamente a las especificaciones, lo que ha mejorado la calidad de mi trabajo.