Laser cutting machines are integral to precision manufacturing, and proper maintenance is crucial for ensuring consistent performance and preventing costly breakdowns. Regular upkeep not only helps extend the life of your equipment but also ensures it continues delivering optimal cutting quality. In this comprehensive guide, we will discuss laser cutting machine maintenance routines, from daily cleaning tasks to annual servicing, as well as common troubleshooting solutions for typical issues.
Table of Contents
The Importance of Laser Cutting Machine Maintenance
Proper maintenance ensures the laser cutting machine operates at peak efficiency, minimizing downtime and reducing the risk of unexpected repairs. Regularly cleaning components, lubricating moving parts, and checking for issues with the gas system or electrical components can prevent significant disruptions in production. In this guide, we’ll break down maintenance tasks by frequency: daily, weekly, monthly, quarterly, and annually.
I. Daily Maintenance Tasks
Daily maintenance tasks are essential for ensuring the machine operates smoothly and without interruption. These tasks focus on cleaning, inspecting, and preventing common issues that could affect performance.
X, Y-Axis Dustproof Cloth:
- Task: Check and clean dust and slag accumulated on the X and Y-axis areas.
- Why: Dust can affect movement and precision, reducing cutting quality.
Slag Collection Containers:
- Task: Inspect and clean scrap vehicle containers daily.
- Why: Full containers can block airflow and affect cutting performance.
X-Axis Protection Plate:
- Task: Remove slag and dust from the protection plate regularly.
- Why: Prevents heat build-up and ensures smooth cutting operations.
Sheet Metal Appearance:
- Task: Wipe external and internal surfaces to remove dust, grease, and dirt.
- Why: Keeps the machine free from contaminants that could cause malfunctions.
X-Direction Anti-Burning Plate:
- Task: Clean slag and dust from the anti-burning plate.
- Why: This prevents damage to sensitive parts and improves cut quality.
General Equipment Cleaning:
- Task: Clean both the exterior and interior of the machine to maintain hygiene.
- Why: Clean machines perform better and reduce wear and tear.
II. Scheduled Maintenance: Weekly to Quarterly
In addition to daily maintenance, scheduled tasks should be carried out at regular intervals to ensure the machine stays in top condition.
Weekly Maintenance Tasks:
- Head Shell Maintenance: Clean dust and lubricate the guide rail surface to ensure smooth movement and accurate cuts.
Monthly Maintenance Tasks:
- Countertop Blade: Inspect, clean, and replace blades if necessary.
- Self-Lubricating Container: Check, refill, and clean regularly to ensure proper lubrication.
Bi-Monthly Maintenance Tasks:
- Central Square Tube: Check and clean slag and dust in the air vent for improved air circulation.
- Water Cooling Machine: Clean the filter screen to maintain efficient cooling.
- Safety Grating: Wipe and clean the surface to prevent safety hazards.
- Exhaust Duct: Periodically clean to remove dust and slag buildup.
- Drive Chain: Clean, grease, and check for proper tension before tightening.
Quarterly Maintenance Tasks:
- Self-Lubricating Container: Rinse thoroughly and replace the lubricating oil.
- Oil Filter: Clean the filter element of the automatic lubrication system.
Annual Maintenance Tasks:
- Filter Element: Replace the cutting air system filter element to maintain air quality.
- Chiller: Replace and clean circulating cooling water to ensure efficient heat dissipation.
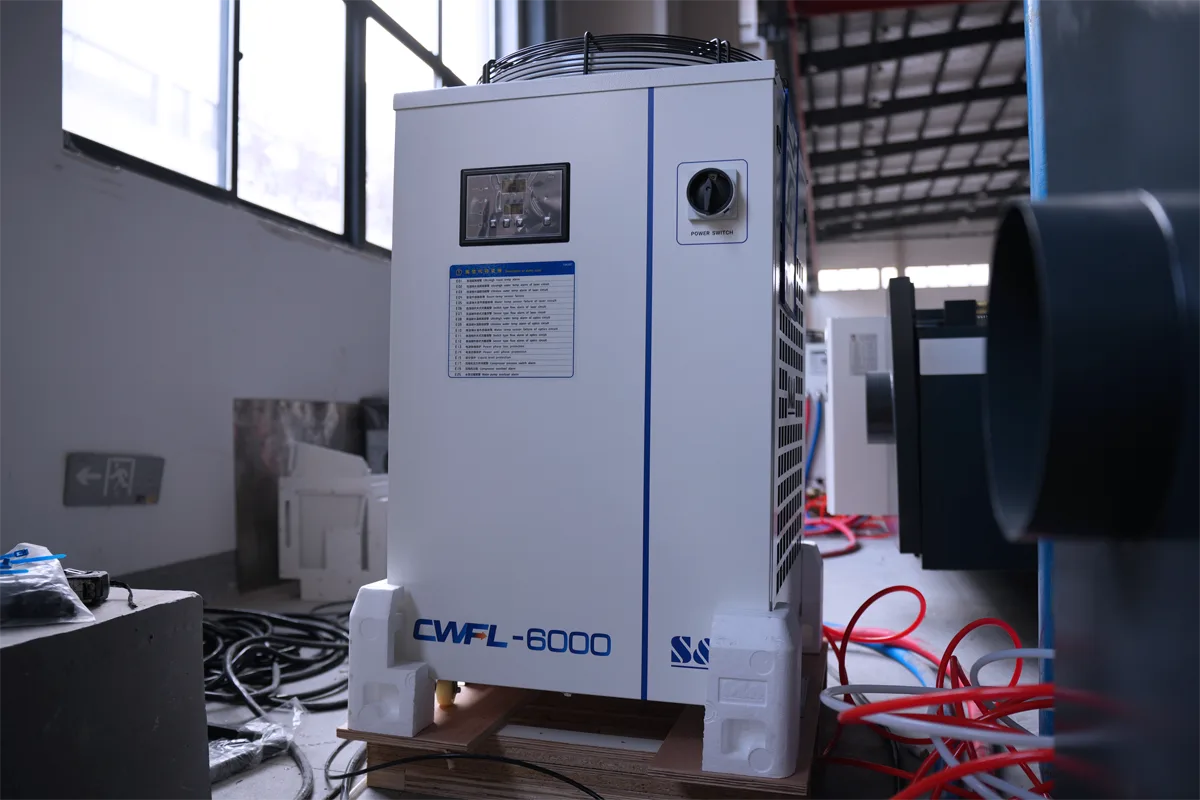
III. Lubrication Maintenance
Lubrication is key to preventing wear and tear on moving parts and ensuring smooth operation. Follow these guidelines for proper lubrication.
X, Y-Axis Guide Rails:
- Interval: As per system configuration.
- Tools: 32# guide oil.
- Steps: Inspect lubricant levels and apply as needed.
Z-Axis Guide Rail and Lead Screw:
- Interval: Every 500 hours.
- Tools: Cleaning cloth, grease gun, No. 1 lithium grease, 32# guide oil.
- Steps: Clean linear guide rails and apply grease.
X, Y-Axis Rack and Gear:
- Interval: Every 500 hours.
- Tools: Cleaning cloth, alcohol, brush, 00# lithium grease.
- Steps: Clean and lubricate the rack, gear, and linear guide.
Automatic Lubricant Pump:
- Interval: Refuel every 14 days; change oil every 6 months.
- Tools: Cleaning cloth, funnel, refueling drum, 32# guide oil.
- Steps: Clean and refill the container, replacing oil as needed.
Oil Filter:
- Interval: Every 1,000 hours.
- Tools: Cleaning cloth, air gun.
- Steps: Clean the filter element with an air gun and reinstall.
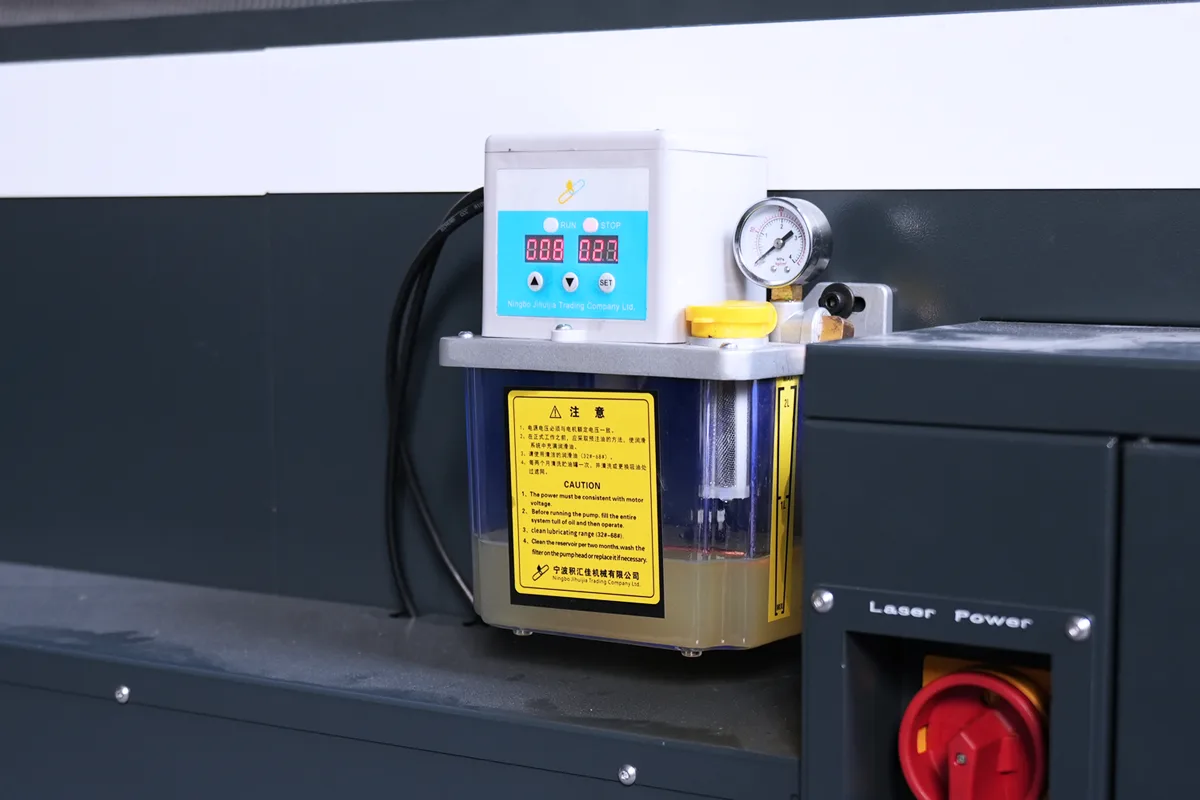
IV. Gas System Maintenance
Maintaining the gas system is crucial for the effective operation of your laser cutting machine.
Filter Element Replacement:
- Interval: Annually.
- Steps: Disassemble the filter, remove the old element, and replace it with a new one.
V. Electrical Maintenance
Electrical maintenance ensures the control system and components remain functional.
Every 1.5 Months:
- Clean the cabinet dust and inspect air filters.
- Replace damaged electrical components.
Every 3 Months:
- Inspect relays, contactors, and switches.
- Test control loops for proper function.
Annually:
- Inspect and clean electrical components, tighten connections, check insulation, and calibrate sensors.
VI. Laser Cutting Machine Maintenance FAQ
- Cause: Contaminated optical lenses, laser aging, or cooling system issues.
- Solution: Replace lenses, check the laser's performance, and maintain coolant quality.
- Cause: Misaligned focus lens, improper cutting parameters, or clogged nozzles.
- Solution: Adjust focus lens, optimize settings, and clean nozzles regularly.
- Cause: Insufficient coolant, clogged filters, or substandard water quality.
- Solution: Replace coolant, clean or replace filters, and use purified water.
- Cause: Lack of lubrication or prolonged high-load operation.
- Solution: Lubricate components and inspect for signs of wear.
- Cause: Sensor malfunctions, loose electrical connections, or user error.
- Solution: Inspect sensors, wiring, and follow the user manual.
- Cause: Errors in programmed paths or sensitivity issues.
- Solution: Optimize cutting paths and recalibrate the sensing system.
- Cause: Unstable power supply or software glitches.
- Solution: Ensure stable power and check the software for issues.
A dry, dust-free environment with stable temperature and power supply is essential.
It extends machine life, improves cutting efficiency, reduces downtime, and minimizes repair costs.
Conclusion
Regular maintenance is critical for keeping your laser cutting machine running smoothly and avoiding costly repairs. By following the outlined daily, weekly, monthly, quarterly, and annual maintenance schedules, you can ensure that your machine remains in excellent condition and provides consistent, high-quality cuts. Proactive maintenance also reduces downtime, improves safety, and enhances overall production efficiency.
If you have any further questions or need assistance with your laser cutting machine, don’t hesitate to contact us now! Our expert team is here to provide professional advice and tailored solutions to ensure your equipment operates at its best.