Laser cutting is a precise and versatile process that has revolutionized industries ranging from automotive to aerospace. Achieving high-quality results in laser cutting depends not only on selecting the right laser machine and settings but also on choosing the optimal laser cutting assist gas. Whether you're working with materials like carbon steel, stainless steel, aluminum, or brass, the type of assist gas you use significantly influences cutting speed, quality, and overall efficiency. This extended guide delves deeper into the science of laser cutting assist gases—air, oxygen, and nitrogen—exploring their characteristics, best applications, and how to address common cutting challenges effectively. By understanding the nuances of assist gas selection, you can elevate your laser cutting projects to the next level of precision and cost-efficiency.
Table of Contents
Air: A Flexible, Cost-Effective Option
Compressed air is a versatile, readily available, and low-cost option for laser cutting. It is widely used for cutting thinner materials (up to about 6 mm) such as mild steel, aluminum, and stainless steel. While air is not as effective as nitrogen or oxygen in terms of cutting speed or edge quality, it provides a balance of performance and affordability. Its most significant advantages are:
- Cost-Effective: Air is readily available and does not require pressurized storage tanks. For facilities looking to minimize overhead, compressed air is an ideal solution.
- No Special Handling Required: Since air is freely available, there’s no need for specialized storage or handling systems, unlike oxygen or nitrogen.
- Moderate Cut Quality: While air cutting speeds are faster than nitrogen or oxygen, the resulting edges may have some oxidation and roughness. In particular, when cutting stainless steel, burrs may appear, which may require secondary machining.
Best Applications for Air:
- Thin materials (less than 6 mm)
- Non-critical parts where speed is more important than edge quality
- Applications that prioritize cost-saving over perfect cut edges
Common Challenges:
- Oxidation and Rough Edges: The 21% oxygen content in air can lead to oxidation and rough cuts, especially on stainless steel.
- Burr Formation: When cutting stainless steel or other materials prone to burrs, post-cut deburring or secondary machining may be necessary.
Oxygen: Speed and Efficiency for Steel Cutting
Oxygen is a highly effective assist gas for laser cutting, particularly for carbon steel. The key advantage of oxygen is its exothermic reaction, which accelerates the cutting process by promoting combustion. This results in faster cutting speeds and deeper cuts, but with trade-offs in edge quality. Oxygen performs best when cutting thicker sheets of carbon steel, where the heat generated from the exothermic reaction supports the cutting process.
- Exothermic Reaction: Oxygen accelerates the cutting speed through combustion. The heat from this reaction provides additional energy to the laser, allowing for quicker cuts.
- Faster Cuts: Oxygen-assisted cutting can reduce the time needed to cut thicker sheets, making it an excellent option for high-throughput operations.
- Oxidized Edges: While the cutting speed increases, oxygen can cause oxidation on the cut edges, especially with thinner materials. These oxidized edges may require cleaning or post-processing to improve the surface finish.
Best Applications for Oxygen:
- Thick carbon steel sheets (typically above 6 mm)
- Situations where cutting speed is the top priority
- Applications where some surface oxidation can be tolerated or cleaned
Common Challenges:
- Oxidation on Edges: The oxidized edges may require additional cleaning, and some burrs may form due to the burning process.
- Rough Edges on Thin Steel: On thinner materials, oxygen may burn through too aggressively, resulting in rough or uneven edges.
Pro Tips for Oxygen Cutting:
- Increase Cutting Speed for Thicker Materials: Oxygen-assisted cutting works best with thicker materials as the exothermic reaction provides a natural speed boost.
- Adjust Laser Power: Ensure that your laser power is well-suited to oxygen cutting; too much power may lead to excessive burning, while too little may slow the cutting process.
Nitrogen: Clean, Oxidation-Free Cuts for Stainless Steel and Aluminum
Nitrogen is the preferred assist gas for cutting high-quality materials like stainless steel, aluminum, and non-ferrous metals. Unlike oxygen, nitrogen does not react with the material, preventing oxidation and ensuring a clean, smooth edge. This makes it ideal for applications where edge quality is a primary concern. However, nitrogen is generally more expensive than air and oxygen, especially at high pressures.
- Oxidation-Free Cuts: Nitrogen prevents oxidation during the cutting process, producing clean, high-quality edges. This is crucial for materials like stainless steel, which would otherwise rust if cut with oxygen or air.
- High Pressure for Clean Cuts: Nitrogen can be used at high pressures to ensure a smooth, burr-free edge, making it perfect for sensitive or high-value materials like aerospace-grade stainless steel and aluminum.
- Ideal for Thin to Thick Materials: Nitrogen works well across a range of material thicknesses, from thin sheets to heavy-duty cuts, offering excellent versatility.
Best Applications for Nitrogen:
- Cutting stainless steel, aluminum, and non-ferrous metals
- Applications requiring smooth, burr-free, and oxidation-free edges
- Thin to medium thickness materials (up to 25 mm), though it can also be used for thicker materials with some added cost
Common Challenges:
- Higher Cost: Nitrogen is more expensive than compressed air or oxygen, especially when used at high pressures for thicker materials.
- Slower Cutting Speed: Nitrogen-assisted cutting may not be as fast as oxygen, especially for thicker steel, where the combustion reaction of oxygen would typically boost the cutting speed.
Pro Tips for Nitrogen Cutting:
- Increase Gas Pressure for Better Results on Aluminum and Stainless Steel: Higher pressures provide more effective vaporization of the material, ensuring a clean cut.
- Maintain a Balanced Cutting Speed: While nitrogen ensures clean edges, excessively slow cutting speeds can lead to unnecessary material waste.
Carbon steel | Stainless steel | Aluminum | Brass | |
---|---|---|---|---|
Air | √ | √ | √ | √ |
Oxygen | √ | × | × | × |
Nitrogen | √ | √ | √ | √ |
Choosing the Right Assist Gas Based on Material Thickness, Quality, and Cost
The correct selection of assist gas is highly dependent on material thickness, desired cut quality, and budget constraints. Here’s a quick guide to help you make the right choice:
Material Thickness:
- Thin Materials (up to 6 mm): Air is usually sufficient for basic cutting needs, providing a cost-effective solution with moderate quality.
- Medium Thickness (6 mm to 25 mm): Oxygen works well for cutting carbon steel, offering faster cuts but at the cost of oxidation. Nitrogen is preferred for stainless steel and aluminum to maintain clean edges.
- Thicker Materials (25 mm and above): Oxygen is ideal for carbon steel cutting, but nitrogen may be used for stainless steel and aluminum for quality cuts.
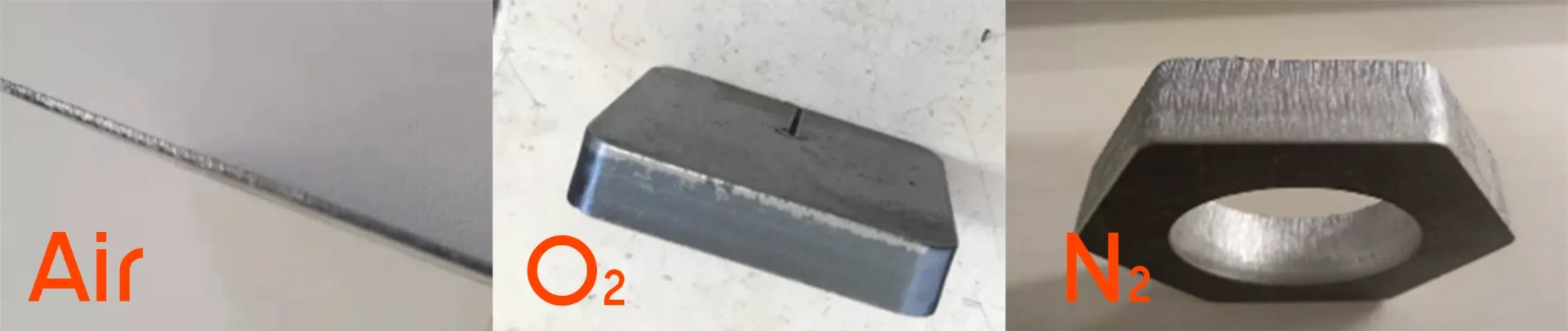
Quality Considerations:
- For Clean, Oxidation-Free Cuts: Nitrogen is the best choice for materials like stainless steel and aluminum, ensuring a high-quality finish without the need for post-processing.
- For Faster Cutting: Oxygen is the best choice for carbon steel, providing high-speed cuts, but with the trade-off of some surface oxidation.
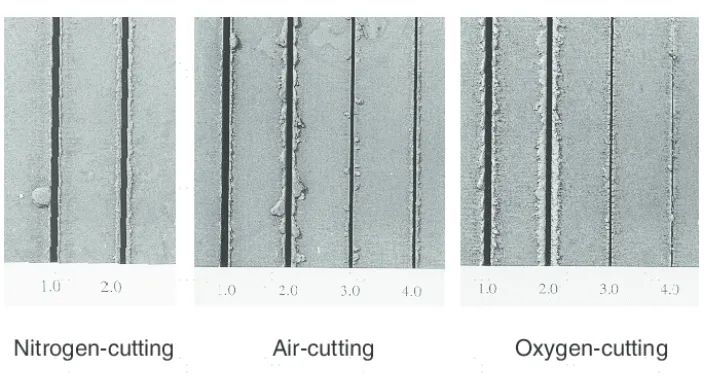
Cost Implications:
- Air: The least expensive option, but results in lower quality edges, especially for stainless steel.
- Oxygen: Relatively inexpensive and ideal for thicker steel, but may require more cleaning of the cut edges.
- Nitrogen: The most expensive but offers the best edge quality, especially for critical applications in stainless steel and aluminum.
Gas Type | Reactive | Speed | Price | Recommend Use |
---|---|---|---|---|
Air | √ | ●●● | $ | Fast, non-aesthetic cuts |
Oxygen | √ | ●○○ | $$ | Thicker materials |
Nitrogen | × | ●●○ | $$$ | High-quality requirement |
Frequently Asked Questions (FAQ)
To improve surface quality, consider:
- Raising the focal point by at least +15 mm for smoother cuts.
- Increasing nozzle height to around 1.4 mm, although this may slightly increase the cut’s taper.
Slag can be minimized by:
- Lowering the cutting speed to reduce excessive oxidation.
- Lowering the focal point and increasing gas pressure for optimal oxidation control.
Minimize burrs by:
- Lowering the focal point to reduce excess material melting at the edge.
- Increasing the nozzle diameter to improve cut cleanliness.
- Reducing the duty cycle to avoid excessive heat buildup.
Blackened surfaces result from prolonged exposure to oxygen in the air. To prevent this:
- Increase the cutting speed to reduce the time the material is exposed to oxygen.
Reviewed by 2 users
A precisão do corte é impressionante, permitindo detalhes finos e acabamentos de alta qualidade em diversos materiais, como madeira, acrílico e metal.
A máquina de corte a laser que adquiri recentemente tem se mostrado uma ferramenta excepcional para o meu negócio.