When expanding their capabilities, fabrication factories often explore complementary value-added processes to attract more customers and increase their bottom line. Plate rolling is an obvious choice for many, but the key question is: how do you choose the plate rolling machine that best suits your factory’s needs?
Why Plate Rolling Machines Are Essential
Plate rolling machines are some of the most versatile equipment in the metal forming industry. These machines are used to roll metal into cans, cones, and other parts for various sectors, significantly boosting a fabricating factory's ROI. Plate rollers can work with diverse materials, including black steel, stainless steel, high-tensile steels, special steels, and aluminum. Choosing the right machine depends on the specific requirements of your operations.
Almost every factory will need to produce round parts at some point, and many will find themselves outsourcing these tasks—until it makes sense to bring the technology in-house.
Modern Needs for Plate Rolling Machines
Selecting the right configuration of your plate roller will depend on the specific needs of your factory. Today, ease of use and connectivity are increasingly important, as interconnectivity within the factory plays a critical role in production management.
A plate roller should come with an intuitive CNC system and a remote management option. These features enable operators to conduct more tasks with higher precision and improve overall productivity.
At our company, we manufacture two-roll, three-roll, and four-roll plate rollers. However, most factories typically opt for three-roll and four-roll models.
Two-Roll vs. Three-Roll vs. Four-Roll Plate Rollers
Two-roll machines are ideal for large-series production of thin sheet metal (less than 0.2 inches or 5 mm thick). In contrast, three-roll and four-roll machines offer more versatility.
Pyramid-type plate rollers, either with three or four rolls, are divided into two categories based on cost and performance: bending rolls with planetary guides and bending rolls with linear guides. Planetary guides are more affordable, while linear guides offer superior precision due to a shorter distance between the rolls, enhancing rolling accuracy.
Four-Roll Machines: The Go-To Solution
Four-roll plate rollers are usually the preferred choice unless your factory has unique requirements, such as managing very heavy plates. These machines offer greater productivity, enhanced usability, and the ability to be fully automated with numeric controls. They are ideal for producing pieces in both small and large series.
One of the main benefits of a four-roll machine is that it always keeps control of the plate. With three-roll configurations, the material must be released at some point, and once it’s released, the machine cannot track its position. In a four-roll system, the rear roll (opposite to the side where you load the plate) can be raised to the top of its stroke, acting as a back gauge to ensure the plate stays in position. This setup significantly reduces the chances of operator error.
The four-roll machine also ensures constant pinch, which is crucial for safety. Even when working with large, heavy plates, the material is securely held in place, preventing it from slipping or falling. In comparison, three-roll machines rely on wedging the plate between rolls, which lacks the same level of consistent control.
Another advantage of the four-roll machine is that it doesn’t require repositioning of the plate. The plate is inserted, pinched, prevent, and rolled in a single pass. This efficiency results in higher productivity compared to three-roll systems, which require repositioning during the process.
While the first investment in a four-roll machine may be higher, the increased productivity, safety, and control make it an asset for factories engaged in repetitive production, such as wind tower or truck tank manufacturing.
Three-Roll Machines: Versatility and Flexibility
Three-roll plate rollers are known for their flexibility and are available in two categories: pyramid-type (with linear or planetary guides) and plate rolls with variable geometry.
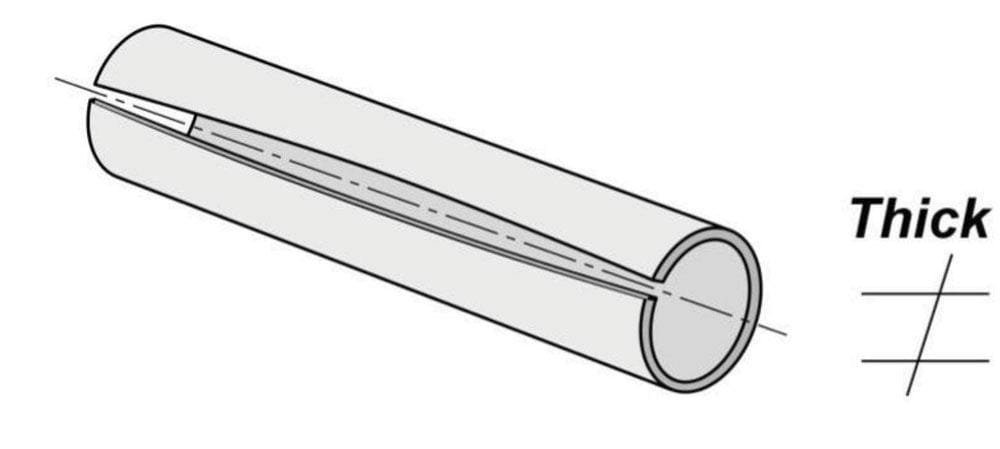
These machines are ideal for factories that don’t require mass production capabilities. Three-roll machines often have a fixed top roll and two bottom rolls that pinch the material. The third roll is used to start the prebinding process. However, three-roll machines generally require the material to be turned around to prebend both ends, which can accept more space and increase operational time.
For lighter capacity applications, “single initial-pinch” three-roll machines are a choice, but they still require physical handling of the material, which introduces safety concerns and the need for more operators.
Lateral Roll Precision: Maximizing Accuracy
The key to maximizing bending accuracy lies in minimizing the distance between the rolls. For example, in press brakes, the V width is a critical factor, while in plate bending rolls, it's the distance between the lateral rolls and the central axis. The closer the lateral rolls are to the machine's central axis, the more precise the rolling process.
Variable-geometry three-roll machines provide a mechanical advantage by allowing the top roll to move up and down, while the lower two rolls adjust horizontally. This configuration enhances bending precision, making it the preferred choice for fabricators who demand high flexibility and maximum force use.
Managing Force and Deflection
Understanding the minimum and maximum thickness of materials you intend to process is essential for selecting the right machine. In plate rolling, bending ability is directly tied to the available force. The force needed to bend a plate depends on the distance between the lateral rolls.
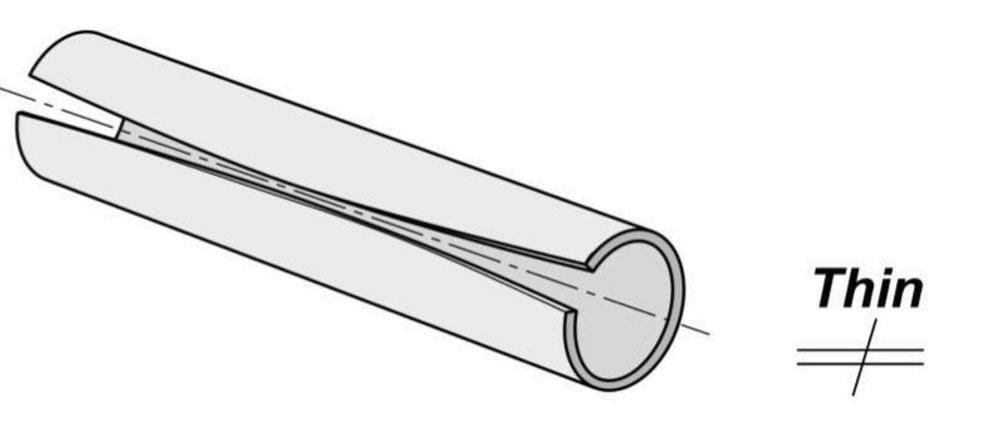
The greater the distance between the rolls, the lower the force exerted due to the leverage effect. This can affect the circularity tolerance of the rolled plate. To address deflection issues, machine builders may design rolls with a slightly larger diameter in the middle to compensate for deflection and keep a consistent sheet thickness.
For factories running a variety of materials, having the option to switch out the top roll can be beneficial, especially when dealing with parts that require tight radii. However, this process can accept to 40 minutes, so it’s important to balance time and flexibility.
Machines equipped with hydraulic crowning support allow for more force without increasing the size of the top roll, providing a solution for factories that require greater bending force without sacrificing space.
Choose the Plate Rolling Machine for Your Factory
The decision to invest in a plate rolling machine requires careful consideration. Key factors include the thickness and material types you plan to process, as well as the size and precision of the parts you need to produce. Consulting with a trusted supplier is essential to ensure that your investment aligns with your factory’s needs.
By working closely with experienced manufacturers, you can find the ideal plate roller configuration that balances versatility, precision, and efficiency, enabling your factory to achieve long-term success.