Tube bending is often referred to as a “black art,” a mysterious process filled with trial and error. But the fundamental principles behind tube bending have still been largely unchanged for decades. While technology has advanced considerably in the methods used to bend tubular workpieces, the underlying physics of the process is still the same. Whether you are working with tube or pipe, the key to achieving the perfect bend comes down to four critical factors: the material, machine, tooling, and lubrication.
Table of Contents
Understanding the Basics of Metal Tube Bending Techniques
Bending begins with understanding the properties of the tube or pipe. Pipes, typically used for transporting fluids or air, are specified by their nominal pipe size (see Figure 1). However, when specifying a bending machine, the centerline radius, outside diameter, and wall thickness of the material are crucial parameters to consider.
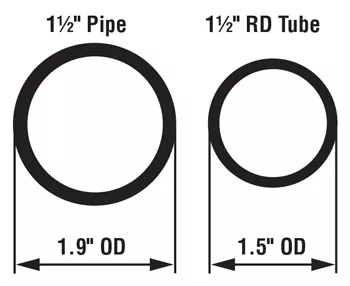
Additionally, every pipe schedule has a nominal wall thickness, but this can vary slightly. These variations should be accounted for, especially in bending processes using tight-fitting tooling on small bend radii. Other important bending variables include the inside bend radius (also known as the intrados), outside bend radius (the extrados), and the centerline radius (also known as the neutral line, where neither compression nor stretching occurs). The bend angle refers to the complementary angle of the bend. For instance, when a tube is bent to “45 degrees,” it’s referred to as a 45-degree complementary bend or a 135-degree included bend (see Figure 2). The distance between bends (DBB) is simply the distance between two tangent points, where a straight section begins to curve, and the bend starts or finishes.
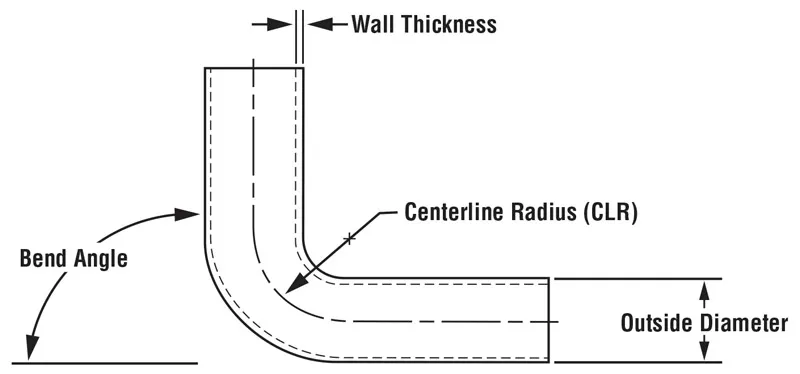
Like in press brake forming, tubes experience spring back after bending, which causes radial growth of the bend. The harder the tube and the smaller the bend’s centerline radius, the greater the spring back and radial growth. For example, copper undergoes less radial growth than steel, and steel experiences less spring back than stainless steel.
Although some tubes are seamless, most are produced with a longitudinal weld. In tube bending, the quality, size, and consistency of the weld seam are crucial factors. If the two edges of the joint are misaligned or if the weld bead is too large or inconsistent, these imperfections can affect the tube’s roundness, causing problems when trying to create a perfect bend.
Elongation occurs during bending as the outside radius stretches, causing wall thinning. The material resists this stretching, and as the outside surface of the bend stretches, it can become distorted, creating ovality or a change in cross-sectional shape. Some ovality may be acceptable for certain applications, but for precision work, even slight distortions can be unacceptable. This is because as the outside stretches, the inside radius compresses, and at a certain point, the inside begins to wrinkle.
Common Tube Bending Processes
The application requirements often dictate the choice of tube bending process. Specialty tube bending processes vary in age and complexity. However, most tubes are bent using one of four main methods: ram-type bending, roll bending, compression bending, and rotary draw bending.
Ram-Type Bending
Ram-type bending is one of the oldest and simplest methods, often seen in muffler shops. The process uses a hydraulically driven ram to push the tube against rollers or pivot blocks, achieving a centerline radius (CLR) of approximately three to four times the outside diameter (OD) of the workpiece (see Figure 3).
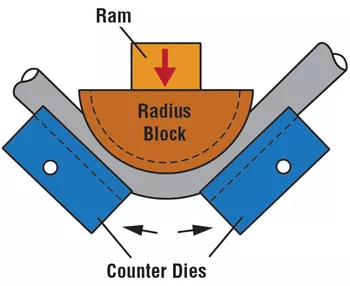
This method does not provide support for the inner diameter (ID) of the tube, resulting in significant stretching on the outside of the bend. This method is often used for square tubing, where the ram tool is intentionally designed to compress and slightly deform the inside bend radius (see Figure 4). This compression helps prevent wrinkling and forces the outside surface of the bend inward, creating a concave surface and minimizing stretching on the outside of the bend.
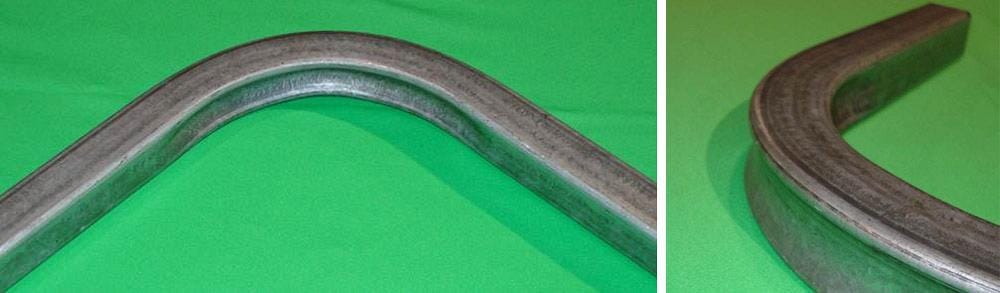
While ram-type bending is inexpensive and commonly used, it is not the most precise method. If workpiece aesthetics or tight bending tolerances are important, this method may not be suitable.
Roll Bending
Roll bending is typically used for large workpieces in industries such as construction. The process involves three rolls arranged in a pyramid-like formation (see Figure 5). The rolls adjust to form specific, often large, radii, making it ideal for creating spirals and coils. One variation of roll bending, the two-roll pinch-style bender, uses an upper and lower roll with adjustable guides to bend the tube. Roll bending offers excellent versatility for creating long, continuous coils, especially in applications like piping or structural elements.
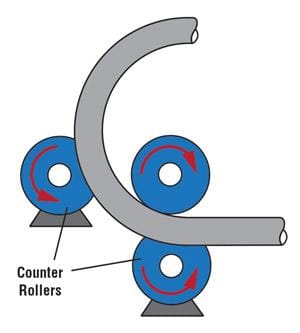
Compression Bending
Compression bending involves bending the tube around a stationary die using a roller or compression die (also called a follow block). The tube is clamped just behind the rear tangent point, and the roller effectively “compresses” the tube against the central bend die (see Figure 6). Compression bending works well for symmetrical workpieces, often used for creating products with identical bends on each side. This method is common for producing items such as towel bars and works best for tubes bent to a CLR that’s at least three times the outside diameter (OD) of the tube.
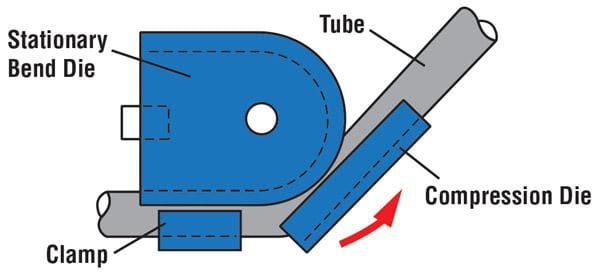
This method may cause slight flattening of the tubes outside surface, as the inner diameter is unsupported. Therefore, compression bending is generally not recommended for tubes with a CLR of less than three times the OD, especially for parts requiring tight tolerances (see Figure 7).
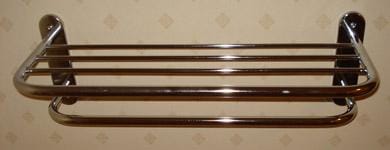
Rotary Draw Bending
For precision work, rotary draw bending is the preferred method, especially for applications requiring tight radii, sometimes as small as a CLR of 0.7 times the tube OD (referred to as less than 1×D). This process provides the greatest control over wall thinning and ovality, which is why it’s often used in highly specialized industries, such as aerospace and automotive. The process involves a mandrel that supports the tube’s inner diameter (ID) during the bend, as well as precise tooling on the outside (OD) (see Figure 8). Rotary draw bending allows for tight radii without compromising the tube’s structural integrity.
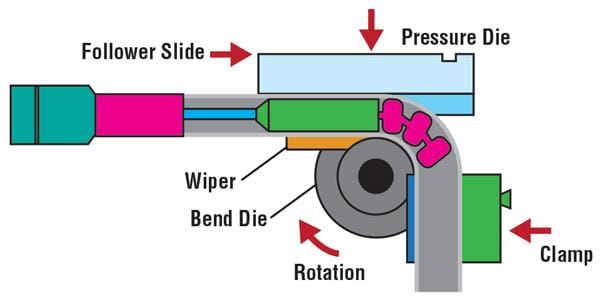
The setup for rotary draw bending includes a pressure die to hold the straight section (the tangent) of the tube, a clamp die to rotate the tube around the bend die, and a mandrel, often equipped with articulating balls, to support the tube’s interior throughout the bend. Additionally, a wiper die ensures that wrinkles do not form on the inside radius by wiping the material just before the tangent point (see Figure 9).
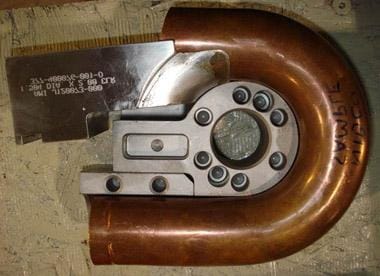
The Role of Tube Bending Tooling
The tooling setup is critical for achieving high-quality bends, particularly with rotary draw bending. Tooling considerations include the hardness of the mandrel, which should be chosen to match the tube material. A soft mandrel is used for harder tubes, while a harder mandrel is needed for softer tubes to ensure a smooth bending process.
Radial growth during bending can cause the radius at the start of the bend to differ from the radius at the end of the bend. This is especially important when bending hard materials with a CLR greater than 3×D. A smaller bend die radius may be needed to compensate for excessive radial growth (see Figure 10).
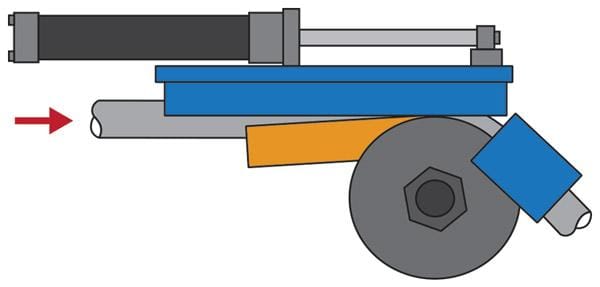
Lubrication: Ensuring Optimal Performance
Proper lubrication is essential to reduce friction and wear during tube bending. (see Figure 11) This is especially true when using mandrels with articulating balls inside the tube. Nonpetroleum-based synthetic lubricants, often supplied in gel or paste form, are commonly used in tube bending operations. The lubrication's viscosity should be adjusted based on the material and the bending requirements. For heavy-duty bending, thicker lubricants are used to ensure smooth operation, reduce wear on critical tooling components like the wiper die, and improve overall performance.
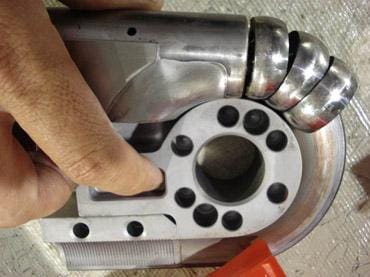
Choosing the Right Machine for Tube Bending
Modern tube bending machines, particularly CNC-controlled machines, offer a high degree of precision, often with multiple axes of control. A typical CNC tube bender may feature up to 10 axes that control various aspects of the bending process, such as the distance between bends (Y), the plane of bend rotation (B), the bend angle (C), the horizontal and vertical shifts (X and Z), and the mandrel motion (YM) (see Figure 12). The axes are described as follows:
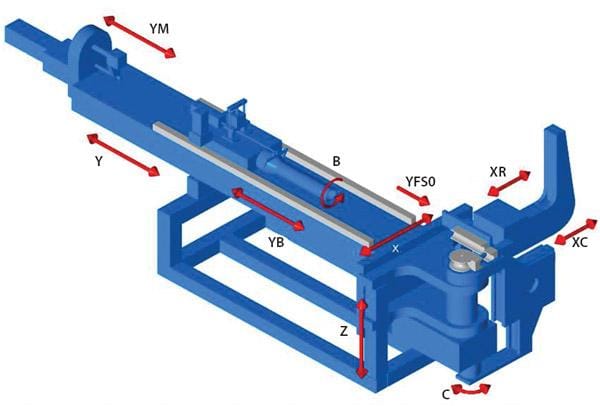
- Y: Distance between bends
- B: Plane of bend rotation
- C: Bend angle
- X: Horizontal shift of the workpiece
- Z: Vertical shift of the workpiece
- XR: Reaction slide
- XC: Clamping motion.
- YB: Boost motion
- YM: Mandrel motion
- YSFO: Follower pressure dies motion.
Some advanced machines combine multiple bending processes, such as both roll bending and rotary draw bending in a single unit, to improve versatility and efficiency for complex parts requiring different bend radii.
Conclusion: The Art and Science of Tube Bending
The combination of modern machine capabilities, advanced software, and precision tooling has transformed tube bending into a highly controlled, dependable, and efficient process. While material variability and application-specific challenges can add complexity, the right combination of material, tooling, lubrication, and machine ensures that perfect bends can be achieved consistently. With the ability of skilled operators and the right technology, tube bender machine has become an essential industries for industries like automotive, aerospace, and construction. The precision, versatility, and reliability offered by tube bending systems make them indispensable in producing high-quality components for a variety of applications.