Press brake bending machines are very important in manufacturing today. These press brake equipment precisely bend and shape metal sheets, meeting the demands of industries such as automotive, aerospace, and building construction. With the increasing demand for customized metal parts, press brake equipment is becoming more essential and popular than ever.
- The press brake market was worth $568.2 million in 2022.
- It is expected to grow to $995.3 million by 2032.
- The market is growing at a yearly rate of 5.9% from 2023 to 2032.
Press brakes are key tools for shaping metal. They help workers do their jobs faster and better by making precise shapes.
In 2025, new technologies such as CNC press brakes and other high-performance press brakes will make manufacturing processes faster, more accurate, and highly efficient. This positions high-performance press brakes as essential equipment for the future of manufacturing.
Table of Contents
Key Takeaways
- Press brake machines are essential metal fabrication equipment used to bend and shape metal sheets. They play a crucial role in industries such as car-making and airplane manufacturing.
- The press brake market is growing fast and could reach $995.3 million by 2032. This shows more people need custom metal parts.
- Picking the right press brake means knowing what materials it works with, how strong it needs to be, and its safety features.
- Newer press brakes, like CNC ones, have smart tools. These tools make work faster, more accurate, and more efficient.
- Energy-saving press brakes can cut costs by up to 50%. This makes them a good choice for businesses that care about the environment.
- Taking care of press brakes and checking their safety is very important. This helps them last longer and work better.
- Buying good-quality press brakes can save money on repairs. It also helps make production faster and better over time.
- Think about all costs, like energy and downtime, when buying a press brake. This helps you get the most value for your money.
What Are Press Brake Bending Machine?
Definition and Purpose
A press brake bending machine is a tool that bending metal sheets and pipes. It uses a punch and die to shape materials along specific lines. These machines are important for making metal parts used in industries like cars, airplanes, and buildings.
Definition | Purpose |
---|---|
A press brake machine bends pipes or flat metal sheets. | It is used to fold, bend, and shape materials. |
The machine applies force to bend materials along set lines. | It helps make metal parts, pipelines, and industrial products. |
The machine’s power and size determine what it can handle during the bending process. Power (tonnage) shows how thick the material can be. Size (bending length) tells the largest sheet it can bend. For example, a 14-foot machine can only bend sheets shorter than 14 feet. These details help you pick the right machine.
Key Components and How They Work
Press brake machines have parts that work together to bend metal. The main parts are:
- Ram: Moves up and down to press the material.
- Punch and Die: Shapes the material by pressing it into the die.
- Back Gauge: Keeps the material in the right spot for bending.
- Control System: Modern machines use CNC systems for better accuracy.
The ram moves with power to bend the metal using tools. CNC systems make the process faster and more exact. Newer machines also have safety and designs to make them easier and safer to use.
Importance in Manufacturing and Metalworking
Press brake machines are very important in making metal parts. They create exact shapes needed for industries like cars, planes, and buildings.
Year | Market Size (in million USD) | CAGR (%) |
---|---|---|
2022 | 568.2 | N/A |
2032 | 995.3 | 5.9 |
More people want custom metal parts, so these machines are in high demand. They help make work faster and reduce mistakes, ensuring good quality. By using these machines, companies can work better and stay competitive in manufacturing.
Top press brake manufacturers in 2025
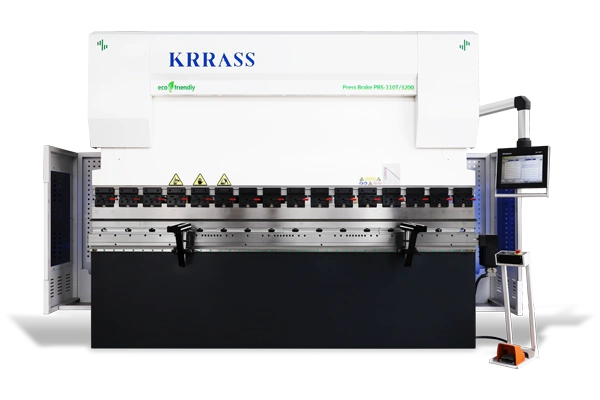
KRRASS: A Top Name in Metalworking
KRRASS has been a trusted name since 1995. Their machines are known for being advanced, energy-saving, and easy to customize. These qualities make KRRASS a favorite for businesses needing dependable tools.
Key Features of KRRASS Machines
KRRASS machines use modern technology and focus on saving energy. The PBE-Hybrid series cuts energy use by 50%, showing their care for the environment. They also offer many custom options to fit different needs. KRRASS has won many awards, proving they are a leader in the industry.
Feature Type | Details |
---|---|
Smart Automation | KRRASS uses advanced automation for better accuracy. |
Energy Saving | The PBE-Hybrid series saves up to 50% energy. |
Custom Options | They provide machines that can be tailored to your needs. |
Industry Awards | KRRASS has earned awards for its innovative designs. |
Popular Models: MB8, PBS, and PBE Series
KRRASS offers a range of sheet metal processing machinery models suitable for different jobs, with advanced automation solutions available to enhance efficiency. The MB8 Series has CNC controllers like DA-66T for easy use. The PBS Series uses servo motors for quieter work. The PBE Series is great for saving energy and reducing oil use.
Amada: Known for New Ideas
Amada is famous for creating innovative press brake machines. Their tools mix advanced tech with simple designs, making them popular worldwide.
Key Features
Amada’s machines are precise, easy to use, and have smart controls. They include features like hydraulic crowning and automatic tool changers to save time. Amada also offers different drive systems, such as servo-electric and hydraulic, for various tasks.
Popular Models
Amada’s top models include the HG ATC, HFE 3i, and HRB Series. The HG ATC Series has automatic tool changers for faster setups. The HFE 3i Series has touch-screen controls for easy operation. The HRB Series, launched in 2020, has a new frame for better precision.
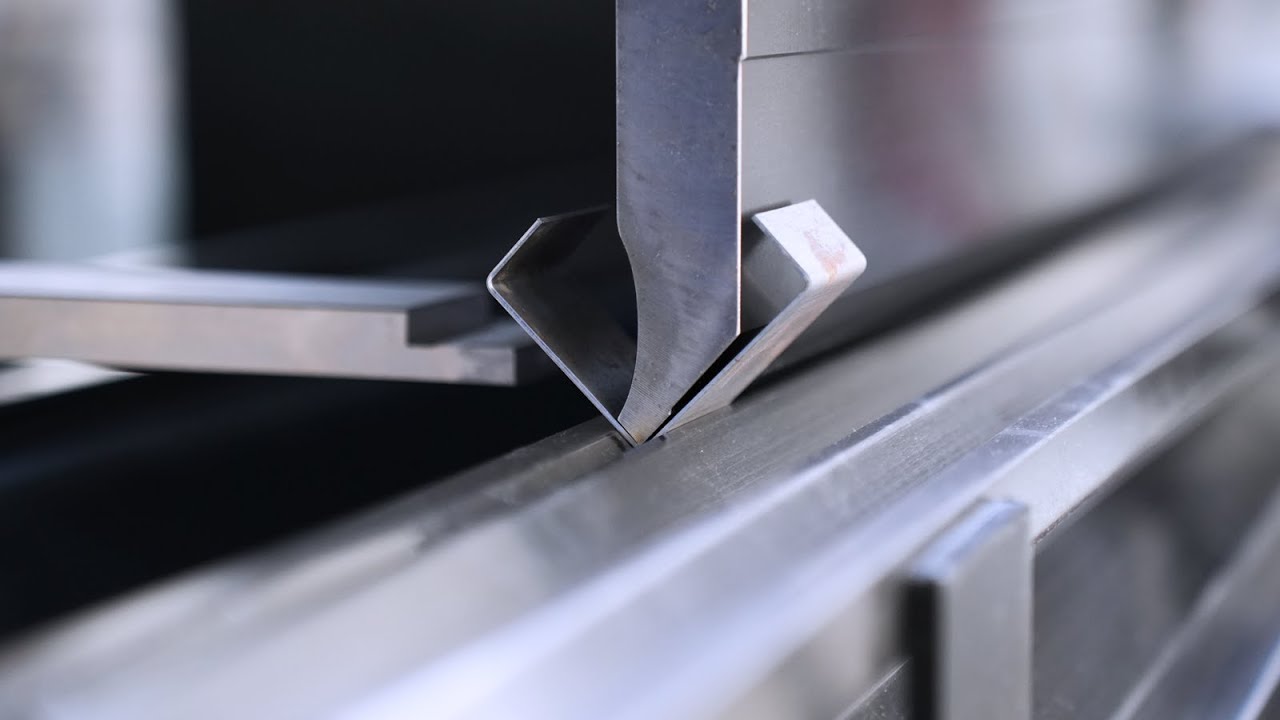
Trumpf: Expert Engineering
Trumpf is known for its high-quality engineering. Their machines combine accuracy, flexibility, and smart software.
Key Features
Trumpf machines have unique tools like the Manual ACB Laser system for precise angles. The 5-axis backgauge helps with tricky bends. Their TruTops Boost software automates tasks, saving time. Trumpf also uses Industry 4.0 tech to improve production.
Feature | Details |
---|---|
Manual ACB Laser System | Measures angles without touching, ensuring accuracy. |
Adjustable Support Brackets | Makes handling parts easier with strong support. |
Bar Code Scanner | Quickly loads programs using bar codes. |
5-axis Backgauge | Allows flexible bending for complex shapes. |
TruTops Boost Software | Automates designs and saves time. |
TecZone Bend | Combines programming for faster and smarter suggestions. |
Popular Models
Trumpf’s TruBend Series is well-loved for its quality. The TruBend 5000 Series is fast and precise. The TruBend 7000 Series focuses on comfort and energy savings. These models work for many industries, offering great choices for buyers.
Accurpress: Known for Being Reliable
Accurpress is famous for making dependable press brake machines. Their machines are strong and work well for tough jobs. They are built to last and handle hard tasks easily. Accurpress also lets you customize machines to fit your needs. This makes them a great choice for businesses needing reliable tools.
Key Features
Accurpress machines are well-made and easy to use. Here are some important features:
- Durability: Built to last, they work well under heavy use.
- Customization: You can adjust them to match your specific needs.
- After-Sales Support: They provide great customer service for ongoing help.
- Industrial-Grade Performance: These machines handle tough jobs with consistent results.
These features show why Accurpress is trusted by many businesses for their needs.
Popular Models
Accurpress has models for different industrial tasks. The Accurpress Advantage Series is strong and precise, with CNC controls for accuracy. The Accell Series is fast, making it perfect for quick projects. Both series show Accurpress's focus on quality and new ideas.
Other top press brake fabricator
Other companies also make excellent press brake machines. They offer unique features and options for metalworking.
Quick Look at Other Brands
- Bystronic Inc.: Focuses on creating unique and innovative solutions.
- LVD Company nv: Makes press brakes for many industrial uses.
- MC Machinery Systems, Inc.: Invests in research to make cutting-edge products.
- Salvagnini America, Inc.: Offers custom solutions for specific needs.
- Durma USA: Known for being reliable and working consistently.
- Haco Holding NV: Makes flexible machines for different manufacturing tasks.
- HFE-Asia: Combines good products with strong customer service.
These brands give you many choices for reliable and advanced press brake machines.
Comparing Types of press brake equipment
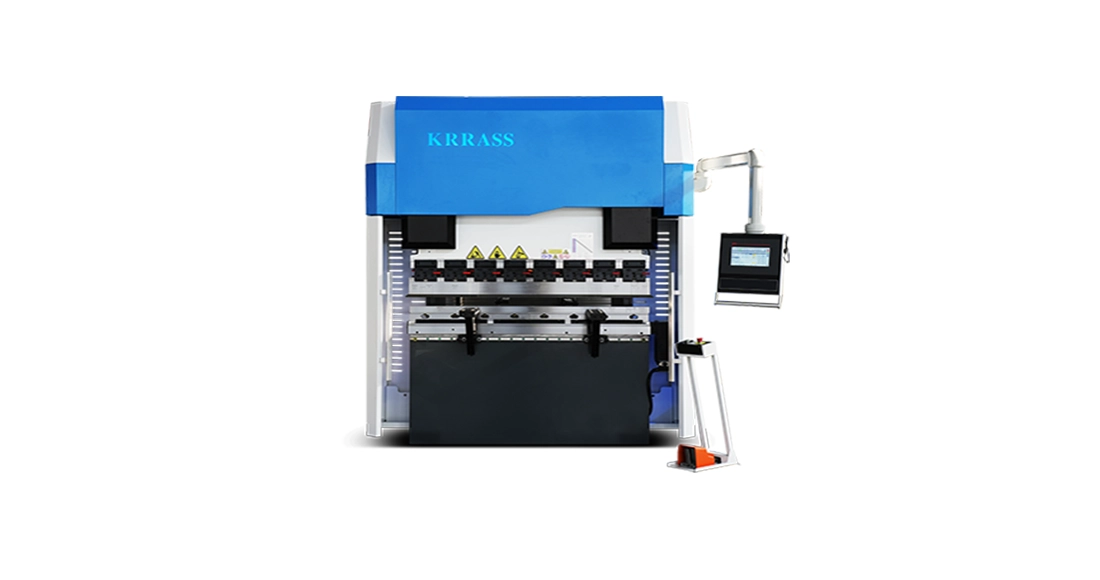
Mechanical Press Brakes
Features and Benefits
Mechanical press brakes are simple machines for bending metal. They use a flywheel to create force, making them strong and affordable. These machines work well for small jobs where exact precision isn’t needed. They are reliable and easy to use, especially for thin materials.
Metric/Statistic | Description |
---|---|
Speed and Precision | Combines quick operation with good accuracy for faster work. |
Cost-Effectiveness | Affordable and simple, great for small businesses. |
High Dynamic Response | Quickly reaches needed force, improving production speed. |
Common Applications
Mechanical press brakes are used in industries like cars and airplanes. They are great for making small parts that don’t need perfect accuracy. If you need a machine for light tasks or small projects, this is a good choice.
Hydraulic Press Brakes
Features and Benefits
Hydraulic press brakes are strong and flexible. They use hydraulic power to bend thick and tough materials. These machines allow you to control speed for accurate bending. They are durable and have safety features to protect workers.
Benefit | Description |
---|---|
High Force Capacity | Can bend thick materials, making them very useful. |
Variable Speed Control | Lets you adjust speed for precise bending. |
Efficiency and Productivity | Speeds up work and improves quality, especially with CNC systems. |
Safety Features | Built-in safety tools help prevent accidents. |
Common Applications
Hydraulic press brakes are used in heavy industries like building and shipmaking. They are great for bending large metal sheets and handling big jobs. If you work with thick materials or need precise results, these machines are a great pick.
CNC Press Brakes
Features and Benefits
CNC press brakes are advanced machines for bending metal. They automate the process, making it faster and more accurate. With sensors and live monitoring, they ensure consistent results. These machines also save time by reducing setup steps.
- Automates bending, making it faster and more precise.
- Ensures consistent results, great for detailed bending tasks.
- Uses sensors to monitor and adjust during work.
- Speeds up production by cutting down setup time.
Common Applications
CNC press brakes are used in industries needing detailed and exact bends, like electronics and aerospace. They are perfect for making many parts quickly and handling complex designs. If you want speed, accuracy, and automation, CNC press brakes are the best choice.
Electric Press Brakes
Features and Benefits
Electric press brakes are great for bending metal quickly and accurately. They use electric motors instead of hydraulic systems. This makes them faster and better for big jobs. If you need reliable results, these machines are a smart choice.
These machines save energy compared to hydraulic ones. Electric motors use less power, cutting costs and helping the environment. Companies wanting to be eco-friendly will like these machines.
Electric press brakes also need less upkeep. Sensors and fault-checking systems keep them running smoothly. This means fewer repairs and lower costs over time. Their accuracy also reduces wasted materials, saving money and resources.
Why choose electric press brakes?
- Quick cycles boost work speed for big projects.
- Energy-saving motors cut costs and help the planet.
- Smart sensors lower maintenance needs.
- Precise bending reduces waste and saves materials.
If you want speed, reliability, and eco-friendly tools, these machines are perfect.
Common Applications
Electric press brakes are used where accuracy and speed matter most. They handle tricky bends well, making them ideal for industries like aerospace, electronics, and cars. If your work needs detailed designs, these machines are a great fit.
In aerospace, they shape light materials into exact parts. For electronics, they make tiny, detailed pieces for gadgets. Car makers use them to create panels and frames quickly. They’re also good for custom projects needing precise and repeatable results.
Common uses for electric press brakes:
- Aerospace: Making light and accurate parts.
- Electronics: Creating small, detailed pieces for devices.
- Automotive: Building panels and frames for vehicles.
- Custom Metalworking: Handling special designs with precision.
Whether for high-tech industries or custom tasks, electric press brakes work well. Their speed and accuracy make them a valuable tool for modern factories.
Technological Advancements in Press Brake Machines
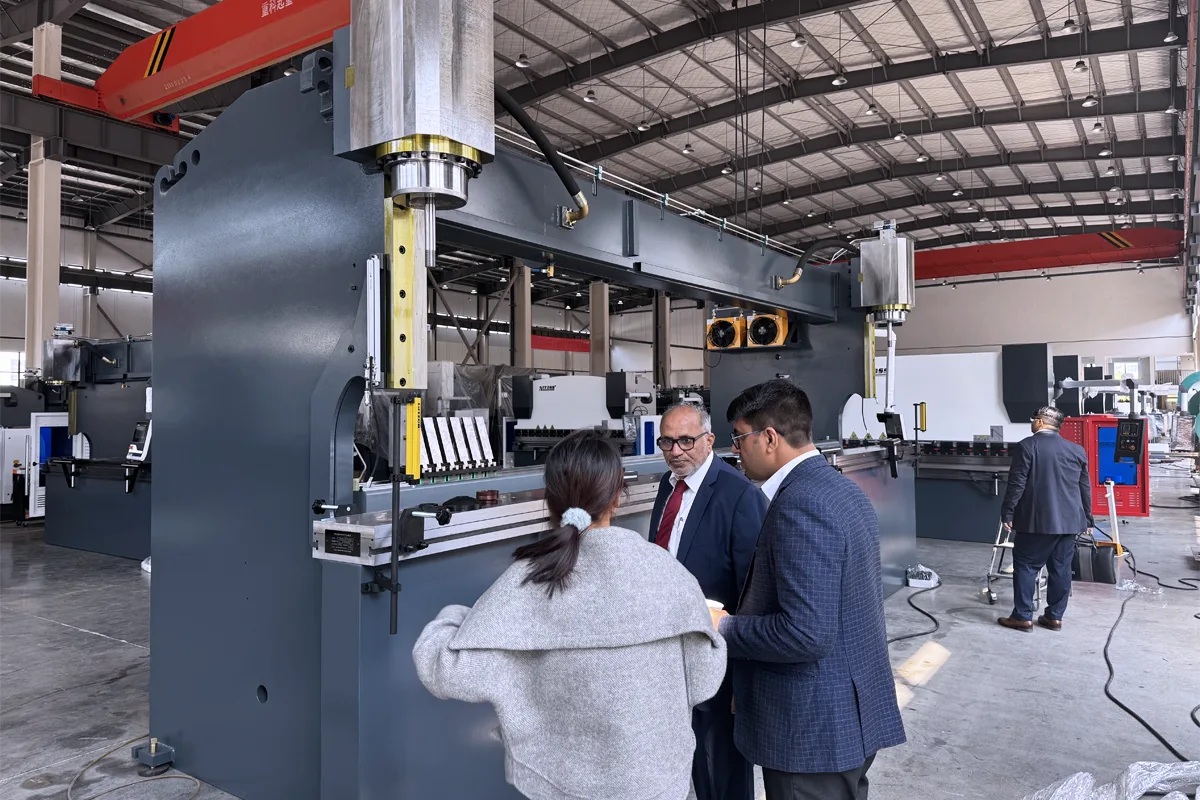
Automation and Smart Features
Today’s press brake machines use automation to work better and faster. These updates cut down on manual work and make tasks easier. For example, CNC systems now handle bending steps automatically. This reduces setup time and mistakes, letting you make more parts quickly. This is very helpful in industries like car manufacturing.
Smart tools, like real-time monitoring, keep results steady even with different materials. Advanced software lets you test bending virtually, helping to improve designs and save materials. Robots and automation also help move materials, making the process smoother and less reliant on skilled workers.
Feature/Benefit | Description |
---|---|
Speed and Precision | Makes more parts faster, great for car-making industries. |
Automation Capabilities | Programmable settings reduce manual work and speed up tasks. |
Real-time Monitoring | Sensors check bends instantly, ensuring accuracy and cutting down waste. |
These tools boost productivity and help businesses stay competitive in fast-moving industries.
Energy Efficiency Improvements
Saving energy is now a big focus for press brake machines. Hybrid models can use 50% less energy than older hydraulic ones. This helps lower costs and supports eco-friendly goals.
Electric press brakes also save energy by using electric motors instead of hydraulics. These motors use less power and are quieter, making them great for green-minded companies. Plus, energy-efficient machines waste less material by bending more precisely, saving money and resources.
Using energy-saving press brakes lowers bills and helps the planet. These updates match today’s focus on being sustainable while keeping performance high.
Enhanced Safety Features
Safety is very important in manufacturing, and new press brake machines have better safety tools. Laser systems, like MSD and DSP, use sensors to stop accidents. These systems meet strict EU safety rules, keeping workers safe even during busy production.
Modern machines also have motorized guards and light curtains to protect operators without slowing work. Dual-hand controls prevent accidental starts, making operations safer.
Tip: Pick a press brake machine with safety features to protect workers and keep productivity high.
These safety tools not only protect people but also help meet safety laws, creating a safer and more efficient workplace.
Integration with Industry 4.0
Industry 4.0 has transformed how press brake machines, metal cutting machines, and other metal fabrication equipment operate. By linking machines to central systems, manufacturing becomes smarter and faster. This connection helps track performance, plan maintenance, and improve workflows.
Real-Time Connectivity and Monitoring
Modern press brake equipment with Industry 4.0 share data instantly. They connect to control systems, giving quick access to important details. For example:
- You can see production rates and fix problems quickly.
- Remote monitoring lets you check machine health from anywhere.
- Operators can change settings easily, making work more accurate.
This connection keeps your operations smooth and avoids delays.
Predictive Maintenance for Reduced Downtime
A big advantage of Industry 4.0 is predictive maintenance. Instead of waiting for breakdowns, machines use data to predict repairs. This reduces downtime and keeps production on schedule.
Here’s how it works:
- Sensors gather data while the machine runs.
- The system checks this data for early signs of problems.
- Alerts are sent before issues get worse, saving time and money.
Fixing problems early makes machines last longer and keeps quality high.
Enhanced Efficiency Through Smart Manufacturing
Industry 4.0 brings smart tools to your factory. These tools automate tasks, simplify workflows, and boost productivity. For example:
- Machines adjust bending settings based on material type.
- Virtual tests check designs before production, saving materials.
- Software links machines for better teamwork on the shop floor.
This smart system improves efficiency and helps you stay competitive.
Tip: Using Industry 4.0 tools can transform your manufacturing process. It’s a smart step for better results and future success.
Adding Industry 4.0 to your press brake machines gives you more control, lowers costs, and improves product quality. This technology is shaping the future, so adopting it now keeps you ahead.
How to Choose the Right Press Brake for Your Needs
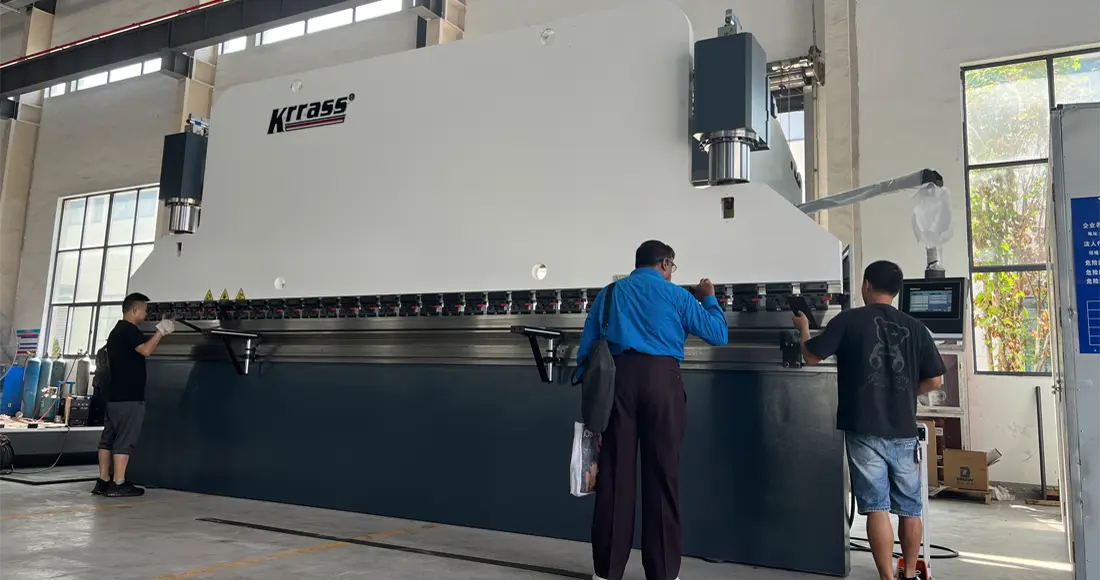
Understanding Material Compatibility
Picking the right press brake starts with knowing your materials. Each material bends differently based on its properties. For example, steel is strong and flexible, but high-strength steel needs careful handling to avoid cracks. Aluminum is light but can crack if not bent properly. Stainless steel is strong and resists rust but needs special tools and more force to bend.
Material | Traits | Things to Consider |
---|---|---|
Steel | Strong and flexible; mild steel bends easily. | High-strength steel needs more force and careful handling to avoid cracks. |
Aluminum | Lightweight and resists rust; weaker than steel. | Can crack easily; needs precise tools and careful bending. |
Stainless Steel | Strong and rust-resistant; harder to bend than mild steel. | Needs special tools and higher force for proper bending. |
Copper and Alloys | Great for electricity; easy to bend. | Needs the right tools to avoid scratches and ensure accuracy. |
Think about thickness, edge smoothness, and material type when choosing. Smooth edges help prevent cracks, while rough edges can cause problems. Matching the press brake to your material improves results and reduces waste.
Figuring Out Tonnage Needs
Tonnage is the force needed to bend metal. Calculating this correctly avoids damage to the machine and ensures good bends. Material thickness, bending length, and die width affect tonnage. For example, doubling the thickness of metal means you need four times the force.
- Use this formula to find tonnage:
- Thickness × Bending length × Die opening width.
- Thicker materials need much more force.
Modern machines, like electric or hybrid press brakes, save energy while offering high force. These machines are great for tough jobs and lower energy costs.
Tip: Pick a press brake with slightly more tonnage than you calculate. This gives flexibility for future projects and protects the machine.
Checking Safety Features
Safety is very important when choosing a press brake. Newer machines have advanced safety tools to protect workers and meet rules. Important features include guards, light curtains, and emergency stop buttons. Two-handed controls stop accidental starts, and sensors check operations as they happen.
Safety Tools | Maintenance Tips |
---|---|
Guards | Inspect daily and weekly. |
Light curtains | Check for loose or broken parts. |
Emergency stop buttons | Look for leaks or strange noises. |
Two-handed controls | Lubricate moving parts regularly. |
Tighten hydraulic hoses securely. |
Regular maintenance keeps safety tools working well. Check for leaks, oil moving parts, and secure hydraulic hoses. By focusing on safety, you protect workers and keep production running smoothly.
Considering Maintenance and Longevity
When picking a press brake, think about maintenance and its effect on lifespan. Regular care keeps the machine running well and avoids expensive repairs. Simple tasks like checking hydraulic fluid and inspecting tools for wear are important. These steps help the machine last longer and work better.
Newer press brakes often include warranties. Warranties cover defects and allow quick fixes, reducing delays. Good customer service is also very helpful. Fast support solves problems quickly, keeping your work on track.
Evidence Type | Description |
---|---|
High-Quality Manufacturing | KRRASS machines are built for tough jobs, ensuring they last long. |
Customization Options | Machines can be adjusted to fit specific needs, making them last longer. |
After-Sales Service | Great support helps fix issues fast, reducing downtime and improving reliability. |
Check the machine’s build quality too. Strong materials make it last longer, especially for heavy work. Customizing the machine for your tasks can also improve its lifespan. By choosing a durable press brake and doing regular maintenance, you can make it more reliable and long-lasting.
Tip: Plan regular check-ups to avoid sudden problems. This saves time and money over time.
Budget and Cost Considerations
Buying a press brake costs more than just the price tag. Think about the total cost, including upkeep, energy use, and downtime. High-quality machines may cost more upfront but save up to 30% yearly on maintenance compared to cheaper ones.
Key Considerations | Evidence |
---|---|
Total Cost of Ownership (TCO) | Better press brakes save 30% yearly on maintenance costs. |
Return on Investment (ROI) | High-capacity machines can pay for themselves in 18-24 months. |
Resale Value | Well-kept hydraulic machines can sell for 70% of their price after five years. |
Financing Options | Leasing lowers upfront costs by 30% compared to buying outright. |
Spending more on a high-capacity press brake often pays off fast. It can increase production and pay for itself in 18 to 24 months. Well-maintained machines also keep their value. For example, hydraulic press brakes can sell for 70% of their original price after five years.
If the initial cost is too high, leasing can cut upfront expenses by 30%. Training workers to use the machine properly reduces mistakes, saving time and materials. Energy-efficient models are popular and can lower electricity bills by 30%, helping your budget.
Note: Balancing cost, quality, and efficiency gives you the best value for your money.
By thinking about these points, you can pick a press brake that fits your budget and offers long-term benefits.
Picking the best press brake machine in 2025 depends on what your factory needs. Each brand has its own strengths. KRRASS is great for saving energy and offering custom options. Amada focuses on new ideas and easy-to-use designs. Trumpf is known for precise engineering, while Accurpress is trusted for being strong and reliable.
Think about things like speed, cost, and automation when choosing. New machines help make more parts faster and waste less material. This is especially useful for industries like cars and airplanes. The table below shows important features to help you decide:
Feature | Benefit |
---|---|
Speed | Makes more parts quickly, perfect for busy industries. |
Cost-effectiveness | Cuts energy use and saves materials, lowering costs. |
Operational Benefits | Boosts work speed and keeps workers safe with smart designs. |
Automation Capabilities | Keeps quality steady and simplifies production steps. |
Flexibility | Handles different tasks with easy setup changes. |
Choose a machine that matches your goals. This will improve your work and help your business grow over time.
FAQ
What’s the difference between hydraulic and electric press brakes?
Hydraulic press brakes use fluid power to bend metal. They are strong and great for heavy tasks. Electric press brakes use motors, making them faster and saving energy. Pick hydraulic for strength or electric for speed and eco-friendliness.
How do you figure out the tonnage needed for a press brake?
To find tonnage, multiply the material’s thickness by its bending length. Then, divide by the die opening width. Use a tonnage chart for better accuracy. Always choose a machine with slightly more tonnage than needed for flexibility.
Can press brakes work with different materials?
Yes, press brakes can bend materials like steel, aluminum, and stainless steel. Each material needs special tools and settings. For example, aluminum needs gentle handling to avoid cracks, while stainless steel needs more force.
How often should you take care of a press brake?
Check your press brake weekly or monthly, depending on how much you use it. Look at hydraulic fluid, check tools for wear, and oil moving parts. Regular care keeps it working well and lasting longer.
What safety features should a press brake have?
Look for safety tools like light curtains, emergency stop buttons, and two-hand controls. These features keep workers safe and prevent accidents. Modern machines also have sensors to monitor work in real-time.
Are CNC press brakes better than NC press brakes?
CNC press brakes are faster and more accurate because they automate bending. NC press brakes need more manual work and skill. If you want precision and speed, CNC models are the best choice.
How do you pick the right press brake for your needs?
Think about the material type, thickness, and tonnage you need. Check for safety tools, energy-saving features, and automation. Match the machine’s abilities to your work for the best results.
Which industries use press brake machines the most?
Industries like cars, airplanes, buildings, and electronics use press brakes a lot. These machines make exact metal parts for vehicles, planes, structures, and gadgets. They are very important for modern factories.