When it comes to choosing between a CNC brake press and a hydraulic press, understanding the unique advantages and applications of each can help you make an informed decision. Both machines are essential in metalworking and manufacturing, but their capabilities and best-use scenarios differ significantly. Here's a detailed comparison to guide you in selecting the right press for your needs.
Introduction
In the world of metalworking and manufacturing, the choice between a CNC brake press and a hydraulic press is a critical decision that can significantly impact production efficiency, precision, and overall success. Both types of presses play essential roles in various industries, but they operate on different principles and are suited for distinct applications.
A CNC brake press utilizes computer numerical control (CNC) technology to automate the bending and shaping of metal sheets with high precision and repeatability. This advanced machine is ideal for producing complex parts with tight tolerances, making it a preferred choice in industries such as automotive, aerospace, and electronics.
On the other hand, a hydraulic press relies on hydraulic cylinders to generate a compressive force, making it a versatile tool for a wide range of metal forming, molding, and assembly tasks. Its simplicity, high force output, and adaptability to different materials and shapes make it indispensable in sectors like construction, heavy machinery, and general manufacturing.
Selecting the right type of press is crucial for optimizing production processes, ensuring product quality, and achieving cost-effectiveness. Understanding the unique advantages and applications of each type of press can help businesses make informed decisions that align with their specific operational needs and goals.
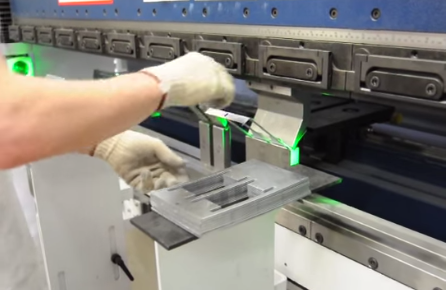
Main Differences Analysis
1. Functionality
CNC Brake Press
Description of CNC Technology and Automated Control: A CNC brake press leverages advanced computer numerical control (CNC) technology to precisely automate bending processes. This technology, typically achieving positioning accuracy within 0.1 mm, controls hydraulic or electric actuators through programmed commands. CNC systems ensure consistent bending angles, depths, and positions, significantly reducing material waste and increasing productivity.
Precision in Bending and Forming Tasks: Renowned for its accuracy, a CNC brake press achieves tight tolerances and intricate geometries reliably across numerous workpieces. This precision is vital in industries demanding high-quality outputs; for instance, in aerospace and automotive sectors, CNC presses ensure exact component dimensions critical for safety and performance.
Suitable for Complex and Repetitive Operations: Automated operation empowers CNC brake presses to excel in handling complex and repetitive tasks. Once programmed, these machines execute bending sequences repeatedly, minimizing variation and ensuring uniformity in production. This capability is pivotal in mass production scenarios, enhancing efficiency and maintaining high standards consistently.
Hydraulic Press
Explanation of Hydraulic Mechanism and Manual or Semi-Automatic Control: Hydraulic presses operate using hydraulic cylinders powered by hydraulic fluid. They offer flexibility, supporting both manual and semi-automatic control. Manual operation involves direct control of pressure and movement using valves and levers. In contrast, semi-automatic mode integrates automated functions with manual intervention, accommodating diverse production requirements.
High Force Generation for Various Forming, Bending, and Molding Tasks: Recognized for their robust force capabilities, hydraulic presses apply immense pressure uniformly across workpieces. They generate forces ranging from a few tons to thousands of tons, making them suitable for shaping metals and materials that demand substantial force. This capability is critical in heavy-duty applications, such as automotive manufacturing and industrial fabrication.
Versatility in Handling Different Materials and Shapes: Hydraulic presses demonstrate versatility by accommodating various materials, including metals, plastics, rubber, and composites. They adapt to different workpiece sizes and geometries, enabling a broad range of forming, molding, and assembly tasks. This adaptability underscores their utility across diverse industries, where flexibility and capability across varied production demands are paramount.
Understanding these operational distinctions and factual insights into CNC brake presses and hydraulic presses aids in selecting appropriate equipment tailored to specific manufacturing needs. This approach ensures optimized performance, enhanced efficiency, and consistent quality in production processes.
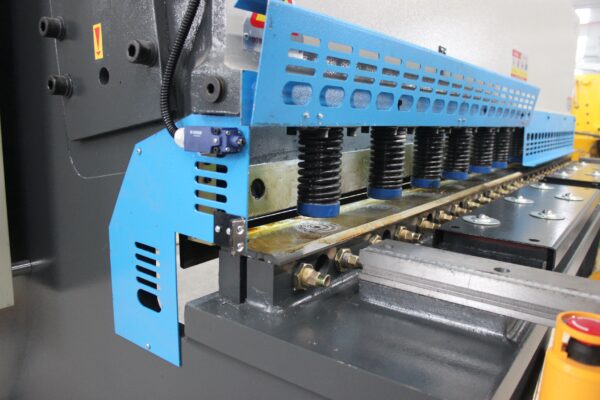
2. Operation
CNC Brake Press
CNC brake presses utilize computer numerical control (CNC) technology, enabling operators to program specific bending instructions using advanced computer software. This system allows precise control over the bending process, ensuring consistent and accurate results across multiple workpieces. Once programmed, CNC brake presses employ servo motors or hydraulic actuators controlled by the CNC system to meticulously position the ram and execute bending operations.
This automated execution minimizes human error, enhances reliability, and facilitates the production of intricate part geometries with tight tolerances, delivering exceptional precision and accuracy capable of achieving bending angles and dimensions within microns (0.001 mm). This level of precision is crucial for industries that demand exact geometries and stringent quality standards, ensuring high-quality finished products.
CNC brake presses streamline operations through automated setup processes, which significantly reduce manual intervention and setup time. Operators can swiftly load programs and adjust settings, optimizing production efficiency and minimizing downtime between production runs. These presses excel in handling complex bending sequences and repetitive tasks, making them highly suitable for mass production environments. Their capability to execute intricate bending operations consistently enhances productivity by ensuring uniformity across large batches of parts, thereby meeting the stringent demands of modern manufacturing.
Hydraulic Press
Hydraulic presses operate on hydraulic principles, utilizing hydraulic fluid pressure to generate force within cylinders. This force is transmitted through the fluid to the pistons, enabling the press to exert significant force on the workpiece. Control mechanisms for hydraulic presses range from manual operation, where operators adjust pressure and movement using valves and levers, to semi-automatic systems that offer some level of automation in controlling press functions. Capable of generating immense force, ranging from a few tons to thousands of tons, hydraulic presses are well-suited for heavy-duty tasks such as forming, molding, and assembly across various industries. This high force output enables them to handle robust manufacturing processes effectively.
Hydraulic presses demonstrate versatility by effectively handling a wide range of materials and shapes, leveraging their capability to uniformly apply high force across the workpiece. This adaptability allows hydraulic presses to accommodate diverse manufacturing needs and processes with efficiency.
In terms of operation, whether operated manually or semi-automatically, hydraulic presses are known for their straightforward setup and maintenance procedures compared to CNC systems. While they may offer slightly lower precision and slower operation speeds, their simplicity in operation makes them highly accessible for a wide array of applications and manufacturing environments. This operational simplicity contributes to their widespread use across industries seeking robust and reliable manufacturing solutions.
3. Control Mechanism
CNC Technology
CNC brake presses utilize advanced CNC systems that integrate computers and software to automate and control bending operations. Operators program these presses using specialized software to input precise commands for bending sequences, specifying angles, depths, and positions. Once programmed, the CNC system orchestrates the movement of hydraulic or electric actuators with high precision, achieving consistent and accurate results across multiple workpieces. This automation ensures that CNC brake presses can achieve precision levels typically within microns (0.001 mm), making them ideal for industries demanding exact geometries and tight tolerances.
CNC technology enables precise control over bending operations, ensuring consistent part dimensions and quality while reducing human error and material waste through automated operation. The flexibility of CNC brake presses allows for quick adjustment of bending programs to accommodate different part designs and production requirements. This capability makes them suitable for complex bending sequences and repetitive tasks, ultimately enhancing productivity in mass production environments.
Hydraulic System
Hydraulic presses operate using hydraulic cylinders powered by hydraulic fluid, typically oil. Control mechanisms vary from manual operation, where operators manually adjust pressure and movement using valves and levers, to semi-automatic or fully automatic systems. Pressure regulation in hydraulic presses is achieved through hydraulic valves and pumps, enabling precise adjustment of the force applied to the workpiece. These presses are capable of generating immense force, ranging from a few tons to thousands of tons, depending on the specific application and press design, making them versatile for various heavy-duty manufacturing tasks.
Hydraulic presses exhibit exceptional versatility across a wide array of industries, adeptly handling forming, molding, and assembly tasks that encompass metals, plastics, rubber, and composites. Their robust force application capabilities enable uniform distribution of high forces crucial for demanding processes like metal forging, stamping, and deep drawing. Moreover, hydraulic presses offer remarkable flexibility by accommodating various sizes and shapes of workpieces, ensuring adaptability to diverse manufacturing requirements with efficiency and precision.
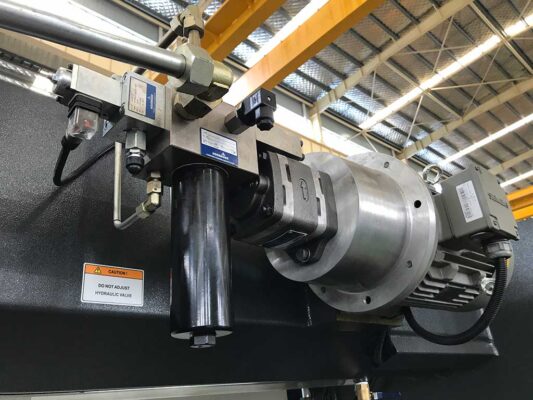
4. Applications
CNC Brake Press
Ideal for Precision Sheet Metal Fabrication: CNC brake presses excel in precision sheet metal fabrication, offering unparalleled accuracy in bending and forming thin sheets of metal. They achieve consistent results with minimal material waste, crucial for industries requiring precise components.
Commonly Used in Automotive, Aerospace, and Electronics Industries: Industries such as automotive, aerospace, and electronics benefit from CNC brake presses due to their ability to produce intricate parts with tight tolerances. These sectors demand high-quality components that meet rigorous standards for safety, performance, and reliability.
Suitable for Producing Complex Parts with Tight Tolerances: CNC brake presses are ideal for manufacturing complex parts requiring precise geometries and tight tolerances. They handle intricate bending sequences efficiently, ensuring uniformity and adherence to design specifications.
Hydraulic Press
Used in Metal Forming, Molding, and Assembly: Hydraulic presses find extensive application in metal forming, molding, and assembly processes. They are capable of shaping and manipulating various metals, including steel, aluminum, and alloys, into desired forms and structures.
Widely Applicable in Automotive, Construction, and Heavy Machinery Industries: The automotive, construction, and heavy machinery industries leverage hydraulic presses for their versatility and robust force capabilities. They are integral to manufacturing components like vehicle frames, construction materials, and large-scale machinery parts.
Effective for Tasks Requiring High Force and Versatility: Hydraulic presses excel in tasks demanding substantial force, such as metal forging, stamping, and deep drawing. Their ability to exert significant pressure uniformly across workpieces makes them indispensable in heavy-duty applications where strength and durability are paramount.
5. Cylinder: The Biggest Difference
The main difference between press brake machinery and hydraulic presses lies in their cylinder designs, which significantly affect their operational characteristics. Press brakes feature cylinders with stroke adjustment capability. For instance, if a cylinder has a stroke of 200mm, it can apply pressure at any point within this range. This adjustability allows for multiple bends to be made in a single setup, as the bending angle can be varied.
In contrast, hydraulic presses typically lack stroke adjustment and require manual alignment for bending angles. They are often used for processing irregularly shaped parts because they can accommodate eccentric loads. Continuous eccentric loading on press brake machinery can lead to cylinder wear and oil leakage, limiting their use for long-term eccentric applications.
Typically, press brake machinery is preferred for regular bends longer than 2000mm, while hydraulic presses are suitable for tasks requiring eccentric loading over extended periods, despite their manual alignment requirement for bending angles.
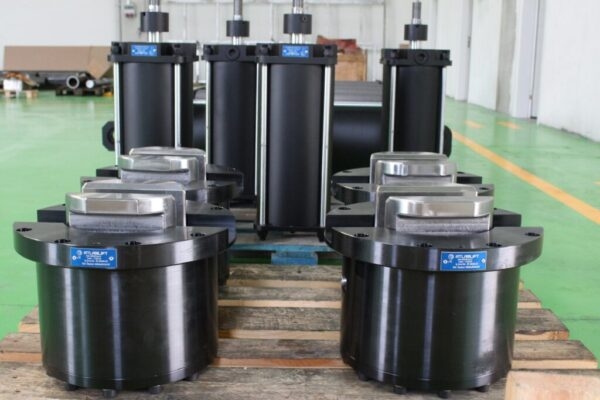
6. Pros and Cons Analysis
CNC Brake Press
Advantages: CNC brake presses excel in achieving high precision and accuracy, reliably bending angles and dimensions within microns (0.001 mm). This capability ensures exact geometries and tight tolerances, crucial for industries requiring stringent quality standards. Moreover, the automation inherent in CNC systems enables consistent repeatability across multiple workpieces, making them ideal for high-volume production environments. By minimizing human error and operator fatigue through automated control, CNC brake presses enhance overall reliability and productivity in manufacturing operations.
Disadvantages: CNC brake presses generally entail a higher initial investment due to their advanced technology and automation capabilities. Additionally, operating and programming these systems demands specialized skills and training, which increase operational costs and complexity. The combination of these factors underscores the importance of thorough planning and investment consideration when integrating CNC brake presses into manufacturing operations.
Hydraulic Press
Lorem ipsum dolor sit amet, consectetur adipiscing elit. Ut elit tellus, luctus nec ullamcorper mattis, pulvinar dapibus leo.
Advantages: Hydraulic presses offer significant advantages in industrial applications: they provide high force output, ranging from a few tons to several thousand tons, making them ideal for heavy-duty tasks like forming, molding, and assembly. Moreover, they generally come at a lower initial purchase cost compared to CNC brake presses, making them a cost-effective choice for businesses with heavy manufacturing needs. Their operation and maintenance, whether manual or semi-automatic, are straightforward, requiring simpler setup and maintenance procedures than more complex CNC systems. These factors collectively contribute to their widespread use across various industries for robust manufacturing processes.
Disadvantages: Hydraulic presses, while powerful for heavy-duty tasks, generally exhibit lower precision compared to CNC brake presses, which can limit their suitability for industries needing extremely accurate parts. Additionally, their manual operation involving pressure and movement adjustments can be time-consuming, contrasting with the automated efficiency of CNC systems. This difference in precision and operational speed underscores the trade-offs between hydraulic and CNC technologies, influencing decisions based on production requirements and efficiency priorities in manufacturing environments.
7. Cost Considerations
CNC Press Brake
CNC brake presses require a higher initial investment due to their advanced technology and automation capabilities. However, this upfront cost can lead to long-term savings through improved production efficiency, reduced material waste, and minimized labor costs. Maintenance costs for CNC brake presses involve regular servicing of components such as hydraulic systems, electrical controls, and software updates. Additionally, operator training is essential due to the specialized skills needed for programming and operating CNC systems, which adds to operational expenses but enhances overall productivity and precision.
Hydraulic Press
Hydraulic presses offer a lower initial purchase cost compared to CNC brake presses, making them accessible for smaller operations or businesses with budget constraints. This affordability enables entry into heavy-duty manufacturing without a substantial upfront investment.
Maintenance costs for hydraulic presses can vary depending on usage intensity, involving periodic inspections, fluid changes, and component replacements to ensure optimal performance. Operational costs encompass energy consumption and labor, particularly for manual or semi-automatic operation, influencing overall cost efficiency. These factors highlight the financial considerations that businesses must weigh when choosing between hydraulic and CNC brake presses based on their production needs and financial capabilities.
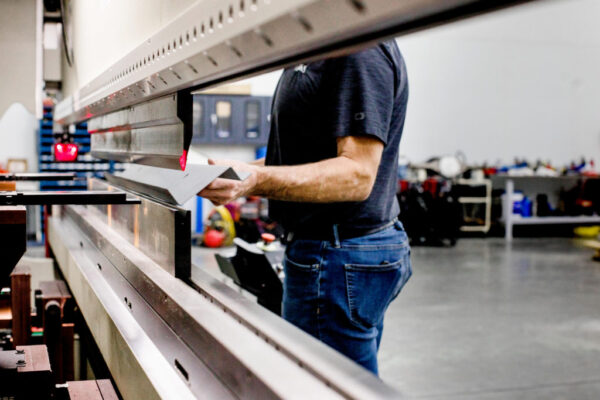
CNC Brake vs. Hydraulic Press: How to Select
When choosing between a CNC brake and a hydraulic press for your application, several factors should be considered to ensure you make the right decision:
Type of Operations
When choosing between a CNC brake and a hydraulic press, consider their distinct strengths. A CNC brake excels in precision bending tasks needing repeatability and complex shapes, with programmable control over bending angles and positions, ideal for high-accuracy production. In contrast, a hydraulic press is better suited for heavy pressing, punching, or forming operations, offering substantial force for tasks such as stamping, bearing pressing, or molding. Each type serves specific manufacturing needs based on precision requirements, material handling, and operational versatility.
Material and Thickness
Both CNC brakes and hydraulic presses cater to specific material handling requirements. A CNC brake is effective for bending a variety of materials, including sheet metal, aluminum, and stainless steel. It's suitable for medium to thick materials, depending on the machine's tonnage and tooling capabilities. In contrast, a hydraulic press excels in handling thick materials and applications requiring high force. It is particularly ideal for forming operations where material thickness and density demand substantial force application. Each machine type offers distinct advantages based on material characteristics and production needs, ensuring efficient manufacturing processes across different applications.
Accuracy and Precision:
A CNC brake provides exceptional precision through its programmable controls and automated operation, ensuring consistent bending angles and repeatability. This capability is crucial for handling complex parts and maintaining high-volume production efficiency. In contrast, hydraulic presses traditionally offer less precision due to manual operation control. However, modern hydraulic presses have evolved to include digital controls, enhancing accuracy and allowing for more precise operations than before. These advancements make hydraulic presses viable options for applications requiring improved precision alongside their inherent strength in heavy-duty forming and pressing tasks.
Flexibility and Versatility:
A CNC brake is highly versatile, capable of handling a wide range of bending requirements from simple to complex shapes. Its programmable capabilities allow for sequential operations, which significantly enhance productivity in manufacturing settings. On the other hand, a hydraulic press offers versatility beyond bending tasks, including pressing, punching, and various forming operations. It excels in applications requiring high force and is suitable for diverse manufacturing needs where robust capabilities are essential. Both machines provide distinct advantages based on the complexity of tasks and specific production requirements, ensuring efficient operations across different industrial applications.
Cost and Investment:
A CNC brake typically requires a higher initial investment due to its advanced automation and precision capabilities. However, the operational efficiency and reduced setup times it offers can lead to significant long-term cost savings in high-volume production environments. In contrast, hydraulic presses are often more affordable upfront, especially for basic models, although costs can vary widely based on size, tonnage, and additional features such as digital controls. Choosing between them depends on balancing upfront costs with long-term operational efficiencies and specific manufacturing requirements.
Production Volume and Speed:
A CNC brake is well-suited for medium to high-volume production thanks to its automated operation and quick setup times. It excels in batch production scenarios where maintaining consistent quality across parts is crucial. In contrast, a hydraulic press is capable of handling high-volume production due to its robust design and ability to operate continuously. However, it may require longer setup times for tool changes and adjustments compared to CNC brakes. Choosing between the two depends on the specific production needs, including the volume of output required and the flexibility in setup and operation times.
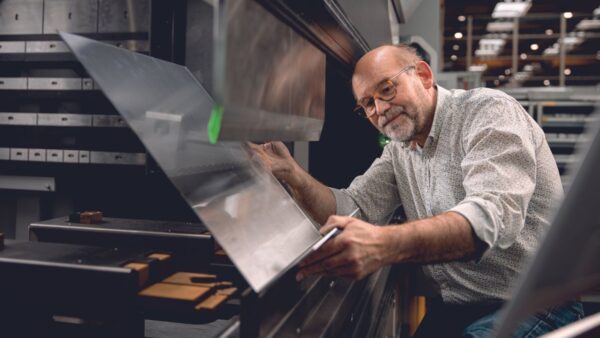
Conclusion
Choosing between a CNC brake press and a hydraulic press depends on your specific manufacturing needs. A CNC brake press, like those offered by KRRASS, offers precision, versatility in handling complex shapes, and efficiency in medium to high-volume production settings. It is ideal for applications requiring automated operation and quick setup times, ensuring consistent quality across batches.
On the other hand, a hydraulic press provides robust capabilities for heavy-duty operations such as pressing, punching, and forming, aligning with KRRASS's focus on durable and high-performance machinery. It excels in applications demanding high force and continuous operation but may require longer setup times. Your choice should consider factors like material handling, precision requirements, production volume, and budget considerations to maximize productivity and profitability in your operations.
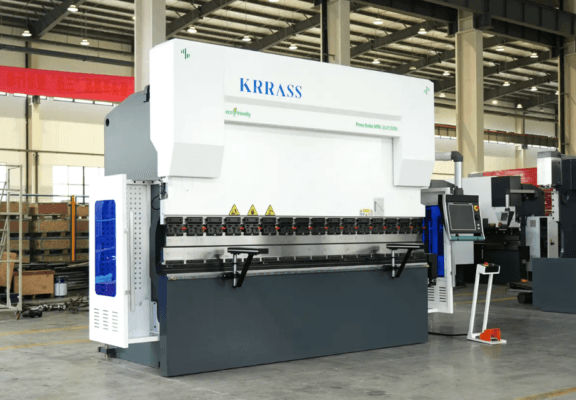