If you're in the process of purchasing a CNC hydraulic bending machine, it's essential to consider several important factors before making your investment. This article will guide you through key considerations such as angle bending, imprint bending, back gauge adjustment, and stroke adjustments. Additionally, we'll cover the crucial features to look for when selecting a machine. By understanding how to properly use your CNC hydraulic bending machine, you'll be well-equipped to maximize its benefits and enhance your production capabilities.
Introduction to the Function of the Bending Machine
The bending machine is a kind of forging machinery. Its main function is to perform sheet metal processing on sheets, especially large sheets. By matching various molds, sheets can be bent, stretched, Rounded, punched, etc., and widely used in light industry, aviation, shipbuilding, metallurgy, instrumentation, electrical appliances, stainless steel products, steel structure construction, and decoration industries.
The bending machine includes a bracket, a workbench, and a clamping plate. The workbench is placed on the bracket. The workbench is composed of a base and a pressure plate. The base is connected to the clamping plate through a hinge. The base is composed of a seat shell, a coil, and a cover. In the depression of the seat shell, the top of the depression is covered with a cover plate.
When in use, the wire is energized to the coil, and after energization, an attractive force is generated on the pressure plate, to realize the clamping of the thin plate between the pressure plate and the base. Due to the use of electromagnetic force clamping, the pressure plate can be made into a variety of workpiece requirements, and it can also process workpieces with side walls. The bending machine can meet the needs of various workpieces by replacing the bending machine mold.
The hydraulic bending machine adopts a steel plate welding structure; vibration aging eliminates stress, and the frame has good rigidity and stability; it works smoothly, is safe and reliable, and is easy to operate; it achieves the ideal bending effect through coordinated control of the electrical and hydraulic systems.
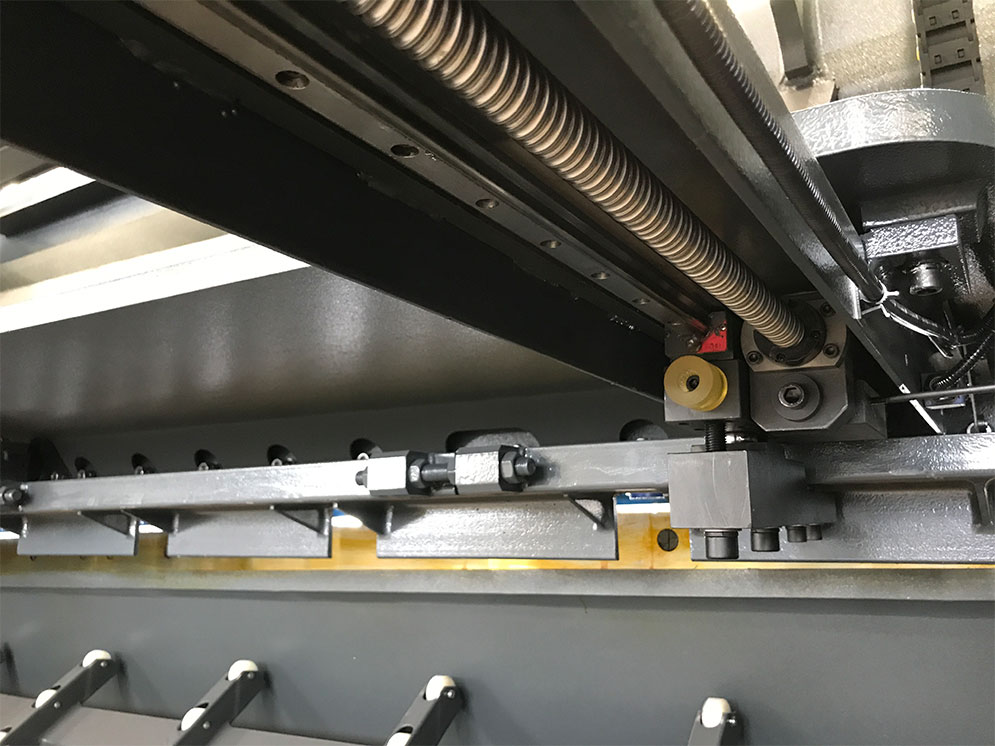
What Are the Types of Bending Machines?
The bending machine is divided into three types: manual bending machine, hydraulic bending machine, and CNC bending machine. Manual bending machine is divided into mechanical manual bending machine and electric manual bending machine. According to the synchronous mode, the hydraulic bending machine can be divided into mechanical synchronous bending machine, torsion axis synchronous bending machine, machine-hydraulic synchronous bending machine, and electro-hydraulic synchronous CNC bending machine.
According to the movement mode, the hydraulic bending machine can be divided into an up-moving type and a down-moving type. The down-moving type is when the workbench and the workpiece on the workbench move upward together, and the slider does not move. At present, it is relatively rare in the domestic market, and most of them are up-moving. The workpiece does not move, and the slider moves downward. According to the control mode, it can be divided into ordinary hydraulic sheet metal bending machine, economical CNC bending machine, and electro-hydraulic synchronous CNC bending machine.
Classification of Hydraulic Bending Machine and Application
Manual Hydraulic Bending Machines
Features and Capabilities of Manual Models
Manual hydraulic bending machines are typically compact and user-friendly. They are designed for simpler operations and can handle lower volume tasks efficiently. These machines require manual input to adjust settings and apply hydraulic pressure. Despite their simplicity, they can achieve precise bends and are often equipped with basic control systems to ensure accuracy. Their portability makes them ideal for on-site jobs and small-scale operations.
Common Applications for Manual Machines
Manual hydraulic bending machines are commonly used in tasks that demand less complexity. They are ideal for custom fabrication, repair, and maintenance work where precision is needed but the volume of work is not substantial. These machines are also prevalent in workshops that handle prototype development or small batch production, providing the necessary flexibility to tweak and modify designs as needed.
Semi-Automatic Hydraulic Bending Machines
Characteristics and Benefits of Semi-Automatic Models
Semi-automatic hydraulic bending machines strike a balance between manual control and automation. These models come with more advanced features than manual versions, such as programmable settings and semi-automated operation modes. The semi-automatic mode minimizes the need for operator intervention, thereby boosting consistency and speed. Additionally, they are outfitted with more sophisticated control systems that enhance ease of use and accuracy.
Use Cases for Semi-Automatic Machines
Semi-automatic hydraulic bending machines are well-suited for medium-scale production and projects requiring a higher degree of precision and repeatability. They are frequently used in automotive, construction, and manufacturing industries where there is a need to balance efficiency with versatility. These machines are ideal for producing components with repetitive bends, reducing production time while maintaining high standards of accuracy.
Fully Automatic CNC Hydraulic Bending Machines
Advanced Features of Fully Automatic Models
Fully automatic hydraulic bending machines represent the pinnacle of bending technology. These models come with advanced computerized controls, enabling precise programming of complex bending sequences. They often include features such as automatic material feeding, real-time monitoring, and adaptive control systems. These features ensure optimal performance and minimize the margin of error, making them suitable for high-precision tasks.
Industrial Applications for Fully Automatic Machines
Fully automatic hydraulic bending machines are essential in large-scale production environments where precision and efficiency are paramount. Industries such as aerospace, automotive, and heavy machinery rely heavily on these machines for mass production of components. They are ideal for situations where complex bends and high throughput are required, significantly improving production rates while maintaining exceptional quality standards.
Core Components of a Hydraulic Bender
Hydraulic Cylinder and Pump System
The hydraulic cylinder and pump system form the core of any Hydraulic Bending Machine. The pump produces the required pressure, which is then conveyed to the hydraulic cylinder. This cylinder applies the force essential for bending the material. The efficiency and dependability of the machine are significantly influenced by the design and quality of these components. Hydraulic cylinders need to be durable and able to endure high pressures, while the pump system must guarantee efficient and smooth operation.
Control Systems: Manual, Semi-Automatic, and Fully Automatic
Control systems vary across different types of hydraulic bending machines. Manual machines typically have basic control mechanisms, while semi-automatic and fully automatic machines feature more sophisticated controls. These systems can include programmable logic controllers (PLCs), human-machine interfaces (HMIs), and other digital interfaces that allow precise control over the bending process. Advanced control systems enhance operational efficiency and ensure consistent quality.
Supporting Structures: Frames and Dies
Supporting structures, including frames and dies, are critical to the machine’s function. The frame provides the necessary stability and support, ensuring that the machine can handle the pressure exerted during the bending process. Dies are used to shape the material as it is bent, and they must be designed to meet specific bend requirements. The quality and maintenance of these structures are vital to the machine’s longevity and performance.
The Operational Workflow of a Hydraulic Bending Machine
The operational workflow of a hydraulic bending machine starts with the preparation of the material, which is securely clamped into place. The operator or automated system then sets the desired bending parameters. Once the settings are confirmed, the hydraulic system is engaged, and the pump generates the necessary pressure to the cylinder. The cylinder pushes the material into the die, achieving the specified bend. Upon completion, the material is released, and the cycle repeats as needed. This process ensures accurate, repeatable bends with minimal human intervention.
How to Correctly Use CNC Hydraulic Bending Machine
CNC Hydraulic Bending Machine for Angle Bending
A CNC hydraulic bending machine for angle forming allows the user to specify the exact length of a bend without the need for a reference. The machine features two bending bolds that rotate during the bending process, giving a signal to the computer that determines the final stroke required. This system compensates for the spring back of each bend and provides high angle accuracy of +/ 0.2o, instantly after the first workpiece is inserted. The machine reduces the material waste compared to manual adjustment.
The CNC bending machine for angle forming comes with many features. One of these is its ability to bend aluminum in different orientations. The machine comes with up to fifteen independent servo axes, allowing the operator to control the bending process in a three-dimensional manner. Another feature is the ability to fine-tune roll positions to minimize unbent flat sections. By using the BIT angle roller, operators can reconfigure the machine to bend smaller workpieces without wasting material.
CNC Bending Machine for Imprint Bending
A CNC Bending Machine for imprint bending is the ideal machine for a wide range of applications. The machine has all the benefits of CNC technology, including a modern touchscreen colour display and two axes of control. Programming is easy and intuitive, with the user interface enabling 200 different programs to be stored and swapped at any time. Stroke settings can be changed in steps of +/-0.1deg. The machine is easy to operate using a foot switch or a special manual control cable. It can be run in automatic or jogging modes.
The software allows the operator to program bends by dragging and dropping bend steps. It is error-proof thanks to the scanning of the part ID code. The graphical tool mapping displays provide information on tooling locations and types, allowing the operator to load the correct part program. The upper ram is equipped with LED mapping for accurate tooling positions. A CNC Bending Machine for imprint bending can also be fitted with spiral bending devices for heat exchanger production.
Back Gauge Adjustment
During a CNC bending job, a back gauge must be adjusted on a CNC bending machine to accurately gauge the material bending. The bend line is set at the nose of the punch, and a half of the material elongation goes to either side of the center. The backgauge location can be determined after performing the calculations. The backgauge position must be set from the front face of the die, a distance one-half of the width of the die body.
The back gauge adjustment is used to position the sheet in the length direction during the bending process. The adjustment value is obtained by pushing a button on the front button box. The table shows the conversion value of the adjustment value, and the machine also has a hand wheel for fine adjustments. A typical CNC bending machine comes with a hand wheel and an electric quick-adjustment lever for the backgauge.
Stroke Adjustment
In order to adjust the stroke, a CNC bending machine should have an oil pump. Start the machine and press the button to activate the pump. After starting the machine, adjust the stroke and make sure the plates are lined up with the bottom mold. You must remember that the upper die must have sufficient clearance, or you will end up damaging the mold. The machine’s stroke adjustment features manual fine tuning as well as electric quick adjustment.
When adjusting the stroke on a CNC bending machine, you should know the open height and closed height of the bending machine. The open height is the height of the upper and lower beams when the upper beam is fully opened. The closed height is the height of the upper and lower beams when closed. You must remember that some of the materials in the machine will come in contact with the variable die when changing the opening. For safety reasons, you should not stand behind the CNC bending machine while working.
CNC Hydraulic Bending Machine for Bending Prisms with Electronic Angle Measurement
The CNC Bending machine for prisms with angular measurement features electronic angular measurement and two flattened bending bars. It has high accuracy of +/ 0.1o, and it is a popular choice for small batches and single pieces. The bending tool rotates while the material is being bent, allowing the operator to set the required final stroke. The system also has an impact system, which allows the user to define the angle of rotation from which the stroke is calculated.
The manufacturing process of glass prisms begins with a block of glass called a “blank” that is ground by a metal diamond bonded wheel. During this step, the majority of the glass is removed quickly, leaving flat but coarse surfaces. Once the prism-to-be is close to the desired dimensions, the machine will perform a fine grinding process to remove scratches and subsurface breaks. The smoothened glass surface should appear cloudy.
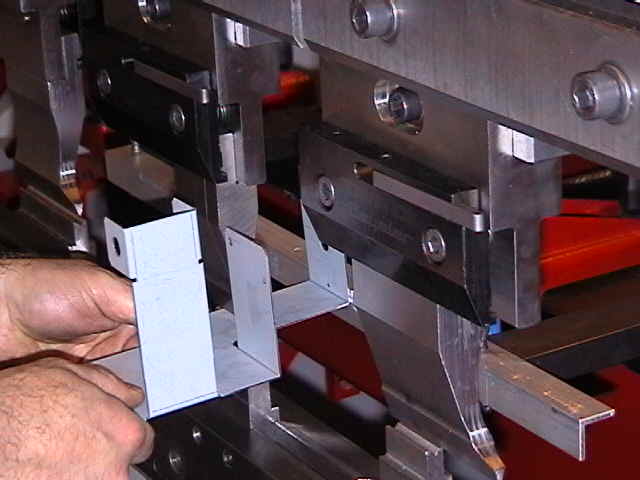
How Does Hydraulic System in CNC Machines
The hydraulic system in CNC machines, including CNC bending machines, plays a crucial role in providing the force necessary to carry out precision operations. Hydraulic systems are commonly used in CNC machines for their ability to generate high amounts of force while maintaining smooth, controlled movements. Here’s an overview of how the hydraulic system works in CNC machines:
1. Hydraulic Power Source
The hydraulic system is powered by a hydraulic pump, which is typically driven by an electric motor. The pump takes hydraulic fluid (usually oil) from a reservoir and pressurizes it, creating the force needed to operate the machine's various components.
2. Hydraulic Fluid
The hydraulic fluid (oil) is the medium that transmits the force within the system. The fluid travels through a network of hoses, valves, and cylinders to transfer power and enable precise movements of machine components. The choice of fluid is critical as it needs to have proper viscosity and lubricating properties to ensure smooth operation and to prevent wear on the system.
3. Hydraulic Cylinder
The hydraulic cylinder is one of the core components. It's responsible for converting hydraulic pressure into linear motion. Inside the cylinder, a piston moves back and forth depending on the direction of hydraulic fluid flow. The piston movement generates the force needed to perform tasks such as bending, pressing, or lifting on a CNC machine.
- In CNC bending machines, hydraulic cylinders control the motion of the ram that holds the tooling (die and punch). The force exerted by the hydraulic cylinder bends the material with great precision.
4. Control Valves
The hydraulic system is equipped with control valves that direct the flow of hydraulic fluid into the cylinders. These valves can be manually or electronically controlled, depending on the CNC machine. The valves regulate the pressure, speed, and direction of fluid flow, which in turn controls the movement of machine parts like the ram or the back gauge.
In CNC machines, the hydraulic valves are often operated through the machine’s programmable logic controller (PLC), allowing the machine to perform automated sequences with high precision.
5. Hydraulic Pressure and Force Control
The hydraulic pressure is adjustable, typically controlled by a pressure relief valve. This ensures the system operates within safe limits and prevents overloading. For CNC machines, the pressure can be precisely set to achieve the desired force for bending or pressing the material.
- For example, in a CNC hydraulic bending machine, the force applied by the ram needs to be adjusted based on the material thickness, bend angle, and tooling configuration.
6. Hydraulic Accumulators
Some CNC machines use hydraulic accumulators to store pressurized fluid. This helps to maintain steady pressure and smooth operation, even if there are fluctuations in the system's demand for power. Accumulators can provide additional pressure during moments of high demand, which is useful for tasks requiring rapid or heavy movements.
7. Maintenance of the Hydraulic System
Hydraulic systems in CNC machines require regular maintenance to ensure efficiency and longevity. This includes:
- Monitoring fluid levels: Ensuring there is enough hydraulic fluid for proper operation.
- Changing the fluid: Periodically replacing the hydraulic oil to prevent contamination.
- Inspecting hoses and seals: Checking for leaks, cracks, or wear.
- Cleaning the filters: Keeping the hydraulic filters clean to avoid contamination of the fluid.
How the Hydraulic System Works in a CNC Bending Machine:
- Ram Movement: In CNC hydraulic bending machines, the ram that holds the bending tool is moved by hydraulic cylinders. The pressure of the hydraulic fluid determines the force applied to the material being bent. The system allows for precise adjustments to the ram's speed and position.
- Back Gauge Adjustment: The back gauge, which positions the material accurately before bending, is often adjusted hydraulically to ensure the proper placement of the material for every bend. The hydraulic system provides the necessary force for quick and accurate back gauge movements.
- Bending Force: The machine’s hydraulic system is designed to apply a controlled bending force, depending on factors like material thickness, type, and desired bend angle. The CNC controller typically adjusts the pressure of the hydraulic system to match these requirements for optimal results.
- Automatic Stroke Control: The stroke of the hydraulic cylinder can also be adjusted, allowing for the fine-tuning of the bending process. This helps the machine achieve different types of bends, from shallow angles to more complex shapes.
Automated CNC Bending Machine
An Automated CNC bending machine is a modern manufacturing solution that can produce parts with high accuracy. It combines dedicated equipment with flexibility, such as mandrels, compression tooling, and a workbench. The machine is equipped with a hopper, a coil feed, and a bending modulus. The machine can also be equipped with robots and transfer units. These features enable the user to program parts easily and increase productivity.
The bending process began thousands of years ago with manually operated hammers and other hand tools. As metal sheets became abundant, this manufacturing process was quickly mechanised. The first bending machines, called “sheet metal bending brakes,” were large, heavy, and heavy. Eventually, the advent of hydraulics helped make work easier. Hydraulics powered the bending tool and a lever valve. At first, shears were powered solely by momentum. Similarly, the position of the bend was defined by a folding rule or a template.
The first generation of automatic benders came about when the steel rule became a common feature. These steel rules were hardened to maintain their shape even after undergoing several processes. Today, automatic benders are capable of several innovations, including side broaching and perforating rules.
CNC bending machines are used for the manufacturing of metal parts. These machines are equipped with three rolls – one fixed and two adjustable. The rotary part manipulator will move the workpiece to the desired position and bend the metal sheet into the desired shape. These CNC bending machines can also produce truncated cones and coils. This means that the price of CNC bending machines is highly competitive, as long as a qualified team is employed to perform the process.
Comparing Hydraulic Technology with Other Bending Technologies
Differences Between Hydraulic and Mechanical Bending Machines
Hydraulic and mechanical bending machines have distinct operational principles and use cases. Hydraulic Bending Machines utilize fluid power to apply consistent pressure, enabling them to handle various material types and thicknesses with high precision. This technology ensures smooth and controlled bends, which is essential for intricate designs. On the other hand, mechanical bending machines rely on mechanical force generated through gears and levers. While these machines can be effective for simpler tasks, they often lack the versatility and precision that hydraulic machines offer.
Additionally, mechanical bending machines are generally less adaptable to complex bending requirements and may experience inconsistencies in force application. Hydraulic bending machines work by utilizing fluid power to exert a consistent amount of pressure, allowing them to precisely manage different types of materials and varying thicknesses. This method guarantees smooth, controlled bends that are crucial for detailed designs. Conversely, mechanical bending machines operate using mechanical force produced by gears and levers.
Although these machines can perform well for straightforward tasks, they frequently fall short in versatility and precision compared to hydraulic counterparts. Furthermore, mechanical bending machines tend to be less flexible in meeting complex bending needs and might show variations in force application. Hydraulic Bending Machines employ fluid power to apply steady pressure, making it possible for them to process a wide range of material types and thicknesses with exceptional accuracy. This technology is vital for creating smooth and controlled bends necessary for intricate designs.
In contrast, mechanical bending machines depend on the mechanical force generated by gears and levers. While they can handle simpler tasks effectively, they usually do not match the versatility and precision provided by hydraulic machines. Moreover, mechanical bending machines are typically less suitable for complex bending requirements and can exhibit inconsistencies in applying force.
Efficiency of Hydraulic vs. Pneumatic Benders
Hydraulic Bending Machines are known for their efficiency, particularly when compared to pneumatic benders. Hydraulic machines operate through hydraulic fluid, which allows for greater force application and more precise control over the bending process. This results in higher accuracy and consistency, which is crucial in industries where quality cannot be compromised. Conversely, pneumatic benders use compressed air to generate force. While they can be faster in certain applications due to the quick response of pneumatic systems, they often fall short in delivering the same level of precision and control as hydraulic systems. Additionally, pneumatic machines may be less effective when dealing with thicker or more rigid materials.
Selecting the Right Hydraulic Bending Machine for Your Needs
When selecting a Hydraulic Bending Machine, several factors need to be considered to ensure you choose the right equipment for your specific needs.
Material Type and Thickness
The type and thickness of the material you aim to bend significantly influence the choice of bending machine. Different machines are designed to handle various materials, ranging from thin sheets of metal to thicker, more robust materials. Knowing the specific requirements of your material will help you select a machine with the appropriate pressure capabilities and die configurations. Ensuring the machine can handle the thickness and type of material will prevent operational inefficiencies and potential damage to the machine or material.
Volume and Frequency of Operations
The volume and frequency of your bending operations are also critical factors to consider. For environments with high-volume production, a fully automatic Hydraulic Bending Machine might be the optimal choice due to its advanced features and efficiency. These machines are capable of handling continuous operations with minimal downtime, thereby enhancing productivity. On the other hand, for operations with lower volume and less frequency, a manual or semi-automatic machine may be adequate. These machines provide flexibility and are easier to manage for smaller-scale tasks, avoiding the higher costs associated with fully automated systems.
Evaluating Cost-Benefit Aspects
Cost-benefit analysis is a fundamental aspect of selecting the right Hydraulic Bending Machine. While upfront costs for hydraulic machines tend to be higher, the long-term benefits often justify the investment. These benefits include reduced labor costs, enhanced precision, and higher production efficiency. It is important to weigh the initial investment against the expected return in terms of productivity gains, reduced material wastage, and improved product quality. Additionally, consider the maintenance costs and the lifespan of the machine, as well-built hydraulic systems tend to require less maintenance and have longer operational lives, further adding to their cost-effectiveness.
Maintenance Tips for Prolonged Machine Life
Regular Inspection Routines
Regular inspection routines are essential for maintaining the optimal performance of a Hydraulic Bending Machine. Conducting frequent checks on key components such as the hydraulic cylinder, pump system, and control mechanisms ensures that potential issues are identified early. Routine inspections might include examining fluid levels, looking for any signs of wear and tear, and ensuring that all bolts and connections are securely tightened. By integrating these inspections into a scheduled maintenance plan, operators can prevent unexpected breakdowns and extend the machine’s operational lifespan.
Common Troubleshooting Techniques
Understanding common troubleshooting techniques can significantly reduce downtime and improve the efficiency of a Hydraulic Bending Machine. Operators should be familiar with the machine’s manual and its specific error codes, which can help diagnose issues quickly. Common problems might include hydraulic fluid leaks, unusual noises during operation, and difficulty achieving desired bends. Regularly checking for clogged filters and ensuring that the hydraulic fluid is clean and at the appropriate level can mitigate many issues. Troubleshooting should also involve inspecting the control systems to ensure that all digital interfaces are functioning correctly and that there are no software glitches.
Importance of Professional Servicing
While trained operators can manage routine maintenance and troubleshooting, the importance of professional servicing for a Hydraulic Bending Machine cannot be understated. Certified technicians possess the specialized knowledge required to conduct comprehensive inspections and repairs that surpass routine maintenance tasks. Professional servicing encompasses recalibrating control systems, replacing worn-out components, and updating software to the latest versions. By scheduling regular professional servicing, compliance with industry standards is maintained, machine performance and reliability are enhanced, productivity is increased, and long-term maintenance costs are reduced.
Future Trends in Hydraulic Bending Technology
The future of hydraulic bending technology, particularly in CNC bending machines, is shaped by innovations in automation, digitalization, and material science. As manufacturing demands become more complex and industries push for higher precision and efficiency, hydraulic bending technology is evolving to meet these needs. Here are some key trends to watch for in the coming years:
1. Integration of IoT and Industry 4.0
One of the biggest shifts in CNC bending machines is the integration of the Internet of Things (IoT) and Industry 4.0 technologies. This trend enables machines to become smarter, more connected, and capable of self-diagnosing and optimizing their operations.
- Remote Monitoring and Diagnostics: IoT-enabled CNC hydraulic bending machines will allow operators and manufacturers to monitor machine performance, detect issues, and perform maintenance remotely. Sensors on hydraulic systems can track pressure, fluid levels, temperature, and other critical parameters to prevent breakdowns.
- Predictive Maintenance: Advanced data analytics and machine learning algorithms can predict wear and tear in hydraulic components, allowing for predictive maintenance. By analyzing trends in machine behavior, operators can schedule maintenance at the optimal time, reducing downtime and extending the machine's lifespan.
- Real-time Data Feedback: IoT sensors can provide real-time feedback on the bending process, allowing for adjustments on-the-fly. This enables quicker setup times, greater precision, and improved quality control.
2. Increased Automation and Smart Control Systems
Automation is another significant trend. As the demand for precision and speed grows, CNC bending machines are becoming more automated and able to operate with minimal human intervention.
- Autonomous Bending Processes: Modern CNC bending machines are becoming more autonomous, with adaptive control systems that adjust bending parameters automatically based on material thickness, type, and shape. These machines can detect variations in the material during the process and adjust the bending force and angle accordingly.
- Robotic Integration: Robots and robotic arms will be increasingly integrated with CNC hydraulic bending machines to automate material handling, loading/unloading, and even post-processing. This reduces manual labor, improves consistency, and speeds up production.
- Advanced HMI (Human-Machine Interface): With intuitive touchscreen displays and more user-friendly interfaces, operators can quickly set up and adjust bending parameters. Many systems now include graphical interfaces that visually show the bend process, providing real-time feedback and reducing the chance for errors.
3. Energy Efficiency and Green Technology
The need for energy efficiency in hydraulic bending machines is growing as businesses look to reduce operating costs and minimize their environmental impact.
- Energy Recovery Systems: Newer hydraulic bending machines are adopting energy recovery systems, where the energy generated during the bending process (such as when the ram returns to its starting position) is recovered and reused to power the system. This reduces energy consumption and operating costs.
- Eco-friendly Hydraulic Fluids: Manufacturers are also exploring biodegradable and less toxic hydraulic fluids that offer lower environmental impact without compromising the performance or longevity of the hydraulic system.
- Energy-efficient Hydraulic Components: Advances in variable displacement pumps, efficient valves, and other hydraulic components can reduce the energy needed to achieve the same performance, helping to make hydraulic systems more energy-efficient.
4. Enhanced Precision and Customization
Precision is key in bending operations, and future developments will push CNC bending machines to achieve even higher levels of accuracy and flexibility.
- Laser-Assisted Bending: Some machines may incorporate laser technology to assist with bending processes. Laser sensors can measure the exact position and angle of the material during bending, allowing for micro-adjustments to be made in real time, improving the accuracy of bends.
- Hybrid Bending Machines: There’s growing interest in hybrid systems that combine hydraulic and electric drives. Electric drives can offer faster, more precise movements for certain tasks, while hydraulics still provide the high force needed for heavy-duty bending. These hybrid machines offer greater flexibility and improved precision while maintaining the power benefits of hydraulics.
- Adaptive Bending for Complex Materials: As materials become more advanced and diverse (e.g., high-strength alloys, composites), future hydraulic bending machines may feature advanced adaptive algorithms to adjust for changes in material properties, such as elasticity and resistance to deformation. This will allow for more precise bending of increasingly complex materials.
5. Advanced Software and Simulation
As with many other types of CNC machinery, the software used in hydraulic bending machines will continue to evolve, providing manufacturers with even more control over the process.
- Advanced Simulation Software: CAD/CAM software will become more sophisticated, allowing operators to simulate the entire bending process before execution. This reduces the risk of material wastage, errors, and rework. In the future, these simulations could be integrated with the machine’s control system, allowing the machine to automatically adjust the setup based on the virtual model.
- AI-Powered Process Optimization: Artificial intelligence (AI) and machine learning (ML) are expected to play a more prominent role in optimizing the bending process. These algorithms can learn from past production runs to make automatic adjustments for better results, optimizing bending speed, accuracy, and quality.
6. Modular and Scalable Systems
Future hydraulic bending machines will increasingly be designed with modular components, making them more adaptable to various production needs.
- Modular Tooling: CNC bending machines will offer more flexible tooling systems that can easily be swapped out or adjusted to accommodate different materials, thicknesses, and bend types. This makes the machines more versatile and reduces setup times.
- Scalable Automation: Manufacturers will have the option to scale their bending machines' capabilities with add-ons, such as additional hydraulic cylinders or robotic arms, allowing businesses to expand production without investing in entirely new machines.
7. Improved Safety Features
Safety will continue to be a top priority as hydraulic bending machines evolve.
- Automatic Safety Lockouts: Future CNC hydraulic bending machines will feature more sophisticated safety systems, such as automatic lockouts and failsafe mechanisms that prevent accidents in case of malfunction or human error. These features can be integrated into the machine's control system, automatically halting the operation if certain parameters are not met.
- Real-time Collision Detection: Advanced sensors and cameras will allow for real-time collision detection during the bending process. These systems can automatically stop the machine to prevent damage to the machine, tooling, or workpiece.