Navigating the purchase of a CNC press brake USA can be a daunting task due to the variety of options and prices available. Understanding the CNC press brake price USA is crucial for making an informed decision, whether you are a seasoned professional or a newcomer in the field of metal fabrication.
This guide aims to provide comprehensive insights into the factors that influence CNC press brake prices, key features to look for, and how to select the best machine for your specific needs. From evaluating initial costs to considering long-term benefits, this buyer’s guide will help you make a smart investmen
Market Analysis of CNC Press Brake In USA
The development of CNC press brakes in the USA has been marked by significant technological advancements and innovations over the years. Initially introduced as manually operated machines, CNC press brakes have evolved into sophisticated equipment capable of precise bending operations with minimal human intervention. The integration of computer numerical control (CNC) technology revolutionized the industry by enabling automated programming, enhanced accuracy, and increased productivity.
Over time, manufacturers in the USA have continuously refined CNC press brakes, incorporating advanced features such as hydraulic systems, servo-electric drives, adaptive bending technology, and sophisticated software interfaces. These developments have not only improved operational efficiency and bending accuracy but also expanded the application capabilities of CNC press brakes across various industries, including aerospace, automotive, electronics, and metal fabrication.
Today, the USA remains at the forefront of CNC press brake innovation, driving forward the evolution of these machines to meet the demands of modern manufacturing practices and emerging technological trends.
1. Market Size and Growth
The CNC press brake market in the USA is currently valued at approximately $3.5 billion, reflecting steady growth driven by the demand in various industries including automotive, aerospace, and construction. Historically, the market has shown an annual growth rate of around 4%, with projections suggesting this trend will continue over the next 5-10 years, potentially reaching $5.2 billion by 2030.
The market can be segmented by type (manual, hydraulic, CNC), with CNC press brakes dominating due to their precision and efficiency. End-user industries such as automotive, aerospace, construction, and electronics have specific needs driving demand. Geographically, regions with high industrial activity, such as the Midwest and Southeast, show the highest demand.
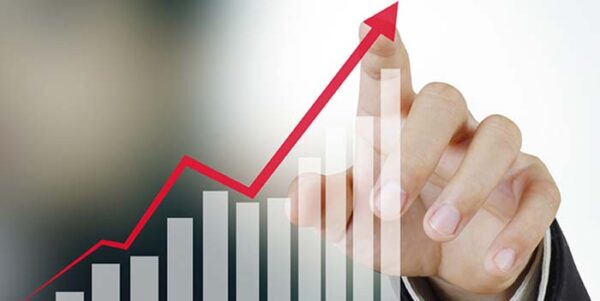
2. Key Market Drivers
Technological advancements drive the CNC press brake market forward with increased adoption of automation and advanced control systems. These technologies enhance productivity and precision, meeting the evolving demands of industries such as automotive, aerospace, and construction.
The need for high-performance CNC press brakes is fueled by the industry's requirement for efficient production processes and high-precision metal bending capabilities. Moreover, stringent government regulations on manufacturing standards and safety push manufacturers towards adopting compliant and technologically advanced machinery.
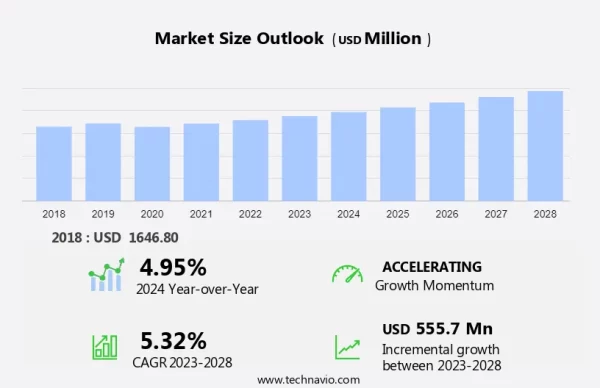
3. Market Challenges
Challenges in the CNC press brake market include the high initial investment required for purchasing and installing these machines, which can be a significant barrier for small and medium-sized enterprises looking to enter or expand within the market. Additionally, there is a growing shortage of skilled labor, particularly operators and technicians capable of handling advanced CNC press brakes.
Ongoing maintenance and repair costs also pose financial challenges to manufacturers, impacting the total cost of ownership. Economic fluctuations further exacerbate these challenges by influencing capital expenditure decisions and potentially leading to reduced investments in new machinery.
4. Competitive Landscape
The USA market for CNC press brakes is dominated by major manufacturers and suppliers such as Trumpf, Amada, Bystronic, Cincinnati Incorporated, and Accurpress. These key players hold significant market shares, with leaders like Trumpf and Amada leveraging extensive product offerings and continuous innovation to maintain their positions.
A comparison of their product lines reveals a spectrum of features and innovations tailored to various industry needs, ranging from basic manual presses to highly automated CNC systems. Recent strategic developments, including mergers, acquisitions, partnerships, and expansions, highlight a dynamic market landscape where companies strive to enhance their market position and technological capabilities.
Factors Influencing CNC Press Brake Price USA
1. Machine Size and Capacity
Bending length and tonnage:
The bending length of a press brake significantly influences its price, with longer lengths typically commanding higher prices due to increased capabilities. For instance, a standard 10-foot bending length press brake may be priced at approximately $100,000, while a 16-foot bending length version of the same model could cost around $150,000. This increase reflects the extended range of material sizes and types it can accommodate, making it suitable for larger-scale manufacturing operations.
Tonnage:
Tonnage capacity is another critical factor affecting press brake pricing, as it determines the maximum force the machine can exert during bending operations. Higher tonnage machines are more expensive due to their robust construction and ability to handle thicker and harder materials.
For example, a 100-ton press brake designed for medium-duty applications might be priced around $80,000, whereas a 300-ton press brake capable of bending heavy-duty materials could cost upwards of $200,000. These higher costs are justified by the increased strength and durability required to maintain precision and performance under greater force.
2. Level of Automation and Control
CNC Control:
The sophistication of the CNC (Computer Numerical Control) system is a critical determinant of CNC press brake pricing. Advanced control systems integrate state-of-the-art technology to enhance precision, operational efficiency, and ease of use.
For example, a press brake equipped with a high-end CNC control system like the Delem DA-66T might be priced significantly higher than models with basic controls. These advanced systems not only offer superior programming capabilities but also ensure precise bending angles and faster setup times, which are crucial for meeting stringent manufacturing tolerances.
Studies have shown that investments in advanced CNC controls can increase productivity by up to 30% through reduced setup times and enhanced operator efficiency
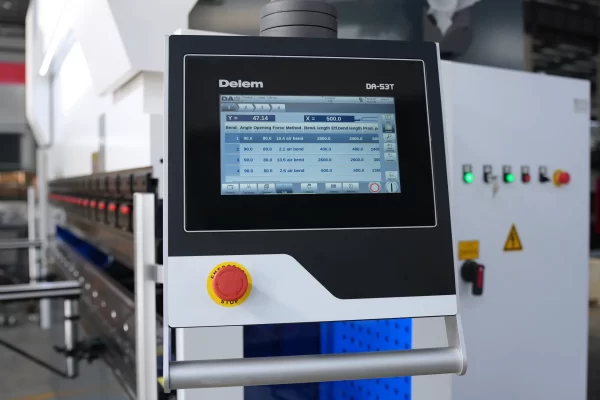
Automation Features:
Automation features play a pivotal role in the pricing of modern press brakes, aimed at improving overall productivity and efficiency in manufacturing operations. Press brakes equipped with robotic arms for material handling, automatic tool changers, and integrated safety systems incur higher costs due to the additional technology and engineering involved. For instance, a model like the Amada HFE3i with robotic automation capabilities not only reduces manual labor but also minimizes setup errors and ensures consistent bending results.
Case studies from automotive assembly plants have demonstrated up to 50% improvement in production throughput with the integration of automated material handling systems and tool changers, illustrating the substantial productivity gains achievable with advanced automation features.
3. Brand and Reputation
Established brands with a reputation for quality and reliability often command premium prices in the USA. Companies like Amada America, Trumpf USA, and Cincinnati Incorporated exemplify this trend. These brands invest heavily in research, development, and comprehensive customer support networks, which significantly contribute to the overall cost of their machines.
Customers value these investments as they ensure long-term reliability and performance, making them willing to pay higher prices for the assurance of quality. This market dynamic underscores the importance of brand reputation and the tangible benefits it brings to CNC press brake buyers in the competitive US market.
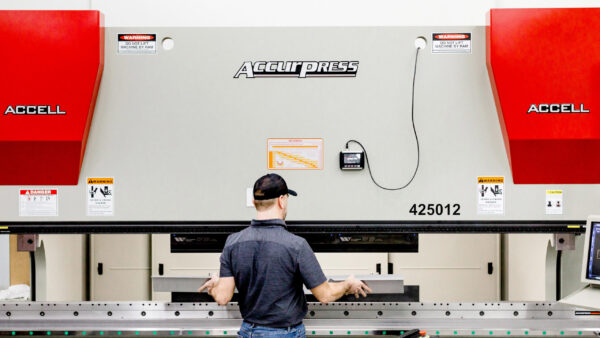
4. Machine Construction and Build Quality
Press brakes made from high-quality materials such as cast iron or heavy-duty steel are known for their durability and precision, but they come at a higher cost. For example, machines from Amada America utilize robust materials like fine grain cast iron, ensuring stability and longevity, which contributes to their premium pricing.
The rigidity and stability of the machine's frame and components are critical for maintaining bending accuracy over time. Research shows that machines with reinforced frames and precision-engineered components exhibit less deformation during operation, thereby sustaining high accuracy levels throughout their lifespan.
5. Tooling and Accessories
The type and quality of tooling, such as punches and dies, significantly impact the price and performance of CNC press brakes. High-precision tooling designed for specific applications ensures better bending results and longer tool life. For instance, Trumpf USA offers a range of tooling solutions crafted from high-grade materials like hardened tool steels, which are engineered to withstand high forces and repetitive use, reducing downtime and enhancing productivity.
Additional accessories like advanced back gauges, safety guards, and bending aids add to the overall cost but are crucial for improving operational efficiency and ensuring operator safety, as demonstrated by studies in manufacturing facilities where safety enhancements have reduced accidents by up to 30%.
6. Service and Support
The quality of service and support offered by manufacturers can significantly impact the total cost of ownership of a CNC press brake. Machines with comprehensive service agreements or local support networks may have higher upfront costs but provide peace of mind and reduce downtime.
Case studies from companies like Cincinnati Incorporated highlight how responsive customer support and readily available spare parts can minimize downtime to less than 2% annually, resulting in substantial cost savings over time due to increased productivity and reduced maintenance costs.
7. Market Demand and Economic Factors
The CNC press brake price USA is influenced by supply and demand dynamics, economic conditions, and currency fluctuations. During periods of high demand, such as the manufacturing boom observed in 2023, prices for CNC machinery increased by an average of 12% due to supply chain constraints and increased material costs.
Economic downturns, like the recession in 2020, led to temporary price reductions as manufacturers sought to stimulate demand through discounts and promotions. These fluctuations underscore the importance of timing and market awareness in procurement decisions.
8. Customization Options
Customization options offered by manufacturers can significantly affect the final price of a CNC press brake. Companies like Bystronic USA provide tailored solutions such as specialized tooling setups and industry-specific configurations. These customizations cater to unique production needs, enhancing efficiency and flexibility on the shop floor.
Case studies from automotive manufacturers show how tailored CNC press brakes have increased production output by up to 20%, highlighting the strategic advantage of investing in customized solutions that align with specific operational requirements.
9. Energy Efficiency and Operational Costs
Modern CNC press brakes designed for energy efficiency offer compelling long-term savings despite higher initial costs. Brands like Haco Atlantic USA have introduced energy-efficient models that reduce power consumption by up to 15% compared to conventional models. Over the machine's lifespan, reduced energy usage translates into substantial operational cost savings, especially in high-volume production environments where energy costs can account for a significant portion of operating expenses.
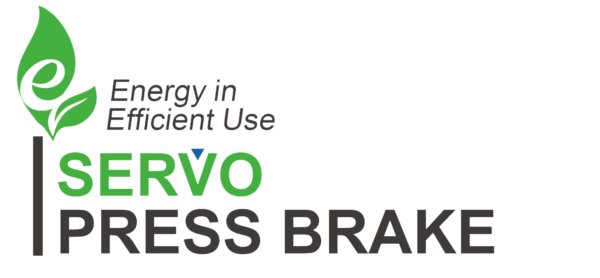
CNC Press Brake Price Ranges in the USA
Understanding the price ranges of CNC press brakes in the USA is crucial for buyers looking to make informed purchasing decisions. The prices can vary significantly based on several key factors, including machine specifications, technological features, brand reputation, and market dynamics. Here's an overview of typical price ranges for different configurations:
Entry-Level Manual CNC Press Brakes
- Description: Basic models suitable for light to moderate bending tasks.
- Typical Price Range: $50,000 to $100,000
- Features: Basic automation, lower tonnage capacity, and simpler control systems.
Hydraulic CNC Press Brakes
- Description: Mid-range machines offering higher precision and versatility.
- Typical Price Range: $100,000 to $300,000
- Features: Increased tonnage capacity, improved bending length, and hydraulic systems for better control.
Advanced CNC Press Brakes with CNC Controls
- Description: High-end models equipped with advanced CNC controls.
- Typical Price Range: $300,000 to $1,000,000+
- Features: Enhanced automation capabilities, multiple axes, sophisticated control systems for complex bending operations.
Robotic Integrated CNC Press Brakes
- Description: State-of-the-art machines integrating robotics for automation.
- Typical Price Range: $500,000 to $2,000,000+
- Features: High level of automation, advanced tooling options, and customization capabilities for specialized applications.
Best CNC Press Brake Suppliers In USA
Trumpf
- Main Products: Offers a range of CNC press brakes, including the TruBend Series.
- Popular Models: TruBend 7000, TruBend 8000, known for their precision and versatility.
- Price Range: Mid to high-end market, with various configuration options.
- Features: High precision, automation capabilities, and robust construction.
Amada
- Main Products: Provides comprehensive CNC press brake solutions, such as the HFE Series and HG Series.
- Popular Models: HFE M2, HG ATC, known for their speed, accuracy, and advanced tooling options.
- Price Range: Mid to high-end market, offering a range of configurations to suit different needs.
- Features: Innovative control technology, automatic tool changers, and ergonomic designs.
Bystronic
- Main Products: Offers high-precision CNC press brakes, including the Xpert Series and Xcite Series.
- Popular Models: Xpert 40, Xcite 80, known for their speed, flexibility, and energy efficiency.
- Price Range: Mid to high-end market, featuring advanced automation and software solutions.
- Features: Swiss precision engineering, dynamic bending technology, and intelligent software control.
Cincinnati Incorporated
- Main Products: Provides a variety of CNC press brakes, including the Maxform Series and Proform Series.
- Popular Models: Maxform 250, Proform 400, known for their durability, accuracy, and ease of use.
- Price Range: Mid to high-end market, suitable for a range of metalworking applications.
- Features: Customizable options, heavy-duty construction, and advanced bending capabilities.
Accurpress
- Main Products: Specializes in precision CNC press brakes, such as the Accurpress Edge Series and Accell Series.
- Popular Models: Accurpress Edge 412010, Accell E, known for their reliability, affordability, and user-friendly controls.
- Price Range: Mid-market positioning, offering a balance of performance and cost-effectiveness.
- Features: Innovative bending technology, modular tooling systems, and low maintenance requirements.
These brands are well-regarded in the USA market, known for their technological advancements, reliability, and ability to meet diverse manufacturing and processing needs. Buyers can choose based on their specific requirements and budget, ensuring they meet production and quality standards effectively.
And listed models represent some of the best-selling CNC press brakes from each brand in the USA market, catering to various industries with their advanced features, high precision, and efficiency.
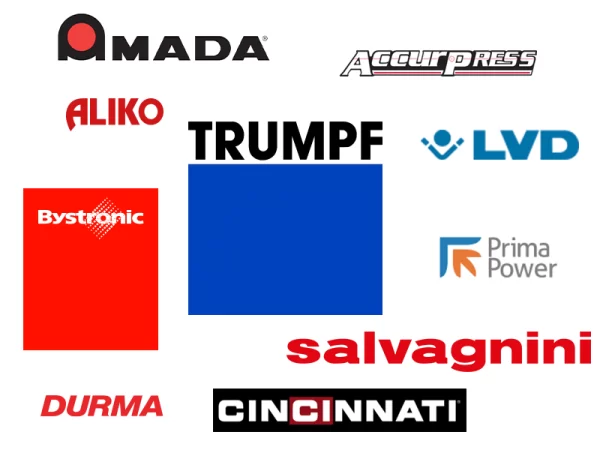
Advantage of USA CNC Press Brake Over Other Countries
Quality and Precision: USA CNC press brakes are often associated with higher quality standards in manufacturing. They are engineered to precise specifications using advanced technologies and quality control measures. This results in machines that offer superior accuracy and consistency in bending operations, critical for industries requiring tight tolerances such as aerospace and automotive.
Innovation and Technology: American manufacturers are at the forefront of technological innovation in CNC press brake design and integration. They continuously invest in research and development to incorporate cutting-edge features like advanced CNC controls, automation, and IoT connectivity. These innovations enhance productivity, reduce setup times, and improve overall operational efficiency.
Customer Support and Service: USA manufacturers typically provide robust customer support and service networks. Local presence ensures prompt assistance, quick resolution of issues, and readily available spare parts. This support infrastructure minimizes downtime, optimizing production uptime and reliability.
Customization and Flexibility: USA-made CNC press brakes often offer extensive customization options to meet specific customer requirements. This flexibility allows manufacturers to tailor machines to fit unique production needs, whether it involves specialized tooling, automation systems, or software integration.
Compliance and Regulatory Standards: Products manufactured in the USA adhere to stringent regulatory standards for safety, environmental impact, and workplace conditions. Compliance with local and international regulations provides assurance of product reliability, operator safety, and legal compliance, which is crucial for industries with strict regulatory requirements.
Industry Reputation and Trust: American CNC press brake manufacturers have built a reputation for reliability, durability, and long-term performance. This reputation is backed by years of experience, adherence to high manufacturing standards, and a commitment to delivering machines that meet or exceed customer expectations.
Economic and Trade Considerations: Purchasing CNC press brakes from USA manufacturers supports the local economy and may offer advantages in terms of trade agreements, tariffs, and logistical considerations. It can also simplify procurement processes and ensure compliance with local content requirements in certain industries.
Overall, the advantages of USA-made CNC press brakes lie in their quality craftsmanship, technological innovation, reliable customer support, customization capabilities, and adherence to rigorous standards. These factors collectively contribute to their competitiveness and appeal in both domestic and global markets.
Key Considerations for Buying a CNC Press Brake in the USA
Investing in a CNC press brake requires thoughtful evaluation of several critical factors to ensure it meets your production needs effectively within the USA market. Here's a comprehensive guide to help you make an informed decision
Machine Specifications
- Tonnage Capacity: Align the press brake's tonnage capacity with the thickness and type of materials you frequently work with. For instance, higher tonnage is necessary for thicker materials like steel.
- Bending Length and Axes: Evaluate the required bending length and the complexity of bends needed. Multiple axes provide greater flexibility for intricate bending operations.
- Back Gauge Systems and Tooling: Consider the accuracy and versatility of back gauge systems and available tooling options for precise and efficient bending.
Brand Reputation and Support
- Manufacturer's Track Record: Opt for brands renowned for quality craftsmanship, reliability, and robust customer support. For example, Trumpf and Amada are well-regarded for their durable machines and responsive service networks.
- Local Service Availability: Ensure the manufacturer has a strong presence and readily accessible service centers in the USA to minimize downtime and ensure timely support.
Technological Advancementsre
- CNC Controls: Assess the sophistication of CNC controls. Modern systems offer intuitive interfaces and advanced programming capabilities, reducing setup time and enhancing productivity.
- Automation Integration: Explore automation options such as robotic arms or IoT connectivity. These technologies streamline workflows, improve accuracy, and boost production output.
- Software Compatibility: Verify compatibility with industry-standard CAD/CAM software. Seamless integration facilitates efficient design-to-production workflows and minimizes programming errors.
Operational Efficiency and Costs
- Energy Efficiency: Select models with energy-efficient features to reduce operational costs and environmental impact over time. Bystronic's Xpert series, for instance, integrates energy-saving technologies without compromising performance.
- Maintenance Considerations: Evaluate maintenance requirements and costs. Regular upkeep ensures peak performance and prolongs machine lifespan, contributing to lower total cost of ownership.
Safety and Compliance
- Safety Features: Prioritize press brakes equipped with comprehensive safety features, such as light curtains and interlocks, to safeguard operators and comply with OSHA regulations.
- Regulatory Adherence: Ensure the machine meets local regulatory standards for workplace safety and environmental compliance, enhancing operational legality and safety.
Financial Considerations
- Budget Allocation: Define a realistic budget considering not only initial purchase costs but also long-term expenses such as maintenance, upgrades, and operational consumables.
- ROI Analysis: Conduct a thorough return on investment analysis. Consider factors like increased production efficiency, reduced scrap rates, and enhanced product quality facilitated by advanced press brake technology.
Industry-Specific Requirements
- Application Suitability: Tailor your choice to meet specific industry needs, whether it's high-speed production in automotive manufacturing or precision bending in aerospace applications.
- Customization Options: Look for manufacturers offering customization options to accommodate unique production demands and operational workflows effectively.
Case Studies and Best Practices
- Real-World Examples: Review case studies or testimonials from similar industries to understand how specific press brake models have improved productivity and profitability.
- Expert Advice: Seek guidance from industry experts or consultants who can provide insights based on their experience with various CNC press brake models and applications.
By integrating these considerations into your decision-making process, you can confidently select a CNC press brake that optimizes production efficiency, meets regulatory requirements, and delivers a strong return on investment tailored to your specific needs in the USA market.
Future Price Trend of CNC Press Brakes in the USA
Looking forward, the future cnc press brake price USA is poised to reflect a blend of technological advancements and market dynamics. With a projected annual growth rate of approximately 4.5% in the manufacturing sector, there is a strong push towards automation and efficiency improvements.
This trend is expected to drive down production costs and consequently influence pricing in the CNC press brake market. Moreover, advancements in materials and manufacturing techniques are anticipated to further optimize machine performance while potentially reducing initial acquisition costs by up to 8% over the next five years.
As businesses navigate these evolving trends, staying informed about technological innovations and market shifts will be crucial in making strategic investments that enhance competitiveness and operational efficiency in the manufacturing landscape.
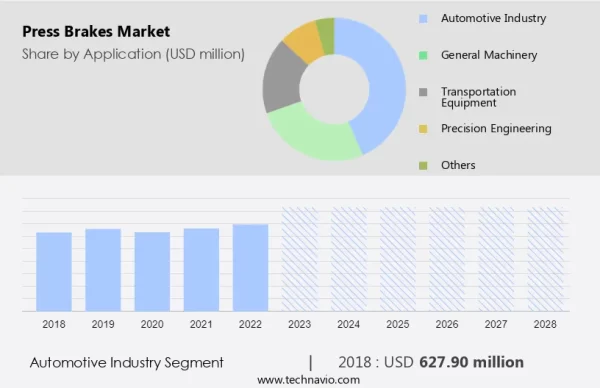
Reviewed by 1 user
press brake
I have seen many KRRASS machines in the US and we are planning to buy some and we will contact you in the near future.