When customers purchase a press brake, they often encounter a variety of issues that can affect both the machine’s performance and the quality of their workpieces. Common press brake issues include inaccurate bending angles, misalignment of tooling, inconsistent material positioning, and hydraulic or electrical malfunctions. These issues can result in defective parts, reduced production efficiency, and increased downtime for repairs. Understanding these challenges and having a clear acceptance process in place is crucial for identifying potential problems early, ensuring that the press brake meets quality standards, and ultimately maintaining a smooth and productive operation.
1.Troubleshooting process
- Cleaning back pressure valve
- Cleaning and blowing down valve
- Remove rust from inside the oil cylinder or replace the sealing ring
2.Solution to the cylinder drop problem
If the first two steps of cleaning are ineffective, try swapping the quick-release valve and the back pressure valve on both sides of Y1Y2. If the problem occurs on the other side, it means that one of the quick-release valve and the back pressure valve has a problem. Consider replacing or cleaning the back pressure valve several times. During the cleaning process, be sure to pay attention to surface cleaning. The valve hole after disassembly also needs to be cleaned.
If the cylinder still falls off after the valve group is replaced, you need to check the sealing ring and rust inside the oil cylinder.
Steps: First, lift the machine, then remove the proportional valve assembly. There are four holes on the valve group base. Pay attention to whether the bottom hole has oil gushing out or is always in the state of oil gushing out. If there is still no oil gushing out after waiting for two minutes, it means that there is an internal leak in the oil cylinder. Then remove the oil cylinder for inspection. During the installation and disassembly process, the valve group sealing ring must be installed well!
Note: The cylinder drop of the machine is only related to the internal sealing ring or cleanliness of the cylinder of the quick-down valve back pressure valve. It has nothing to do with the proportional valve.
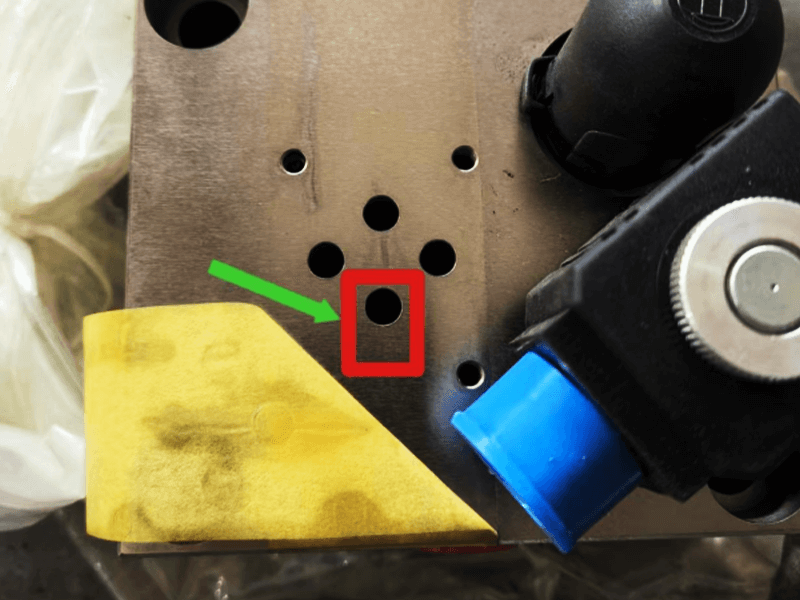
There is no up and down movement when searching for the reference point
When the machine is looking for a reference point and does not move up or down, you can enter the system's diagnostic page, change the left valve offset and the right valve offset to 20%, and then press button No. 2 under the digital signal output to see if the machine can descend. If it does not work, consider cleaning the proportional valve.
Note: Pay attention to the integrated coil circuit on the proportional valve. Remember not to mess up the four blue wires. You need to remove the small plugs on the four blue wires. Do not break the four blue wires during the removal process.
Some troubleshooting of machine startup issues
1.Check whether the thermal protector is tripped
If the oil pump cannot be started, consider checking whether the thermal protector has tripped. There is a small red button and a small gray button on the thermal protector. Press the red reset button first, then press the gray reset button.
2.Check whether the phase sequence protector indicator lights are all on
Check if both indicator lights of the phase sequence protector are on. If it fails to start under normal use and only one light is on, consider that the phase sequence protector is overheated and damaged. It needs to be replaced. If the customer needs to use it urgently, you can remove the two wires at the bottom and connect them together, wrap them with insulating tape, and be sure to turn off the power! ! ! Some models or wire numbers are different, but you only need to connect the two wires in the position shown in the figure below.
Inspection process after receiving the machine
1.Check the integrity of the machine
Check the exterior and core parts of the machine body for any damage. If there is any damage, please contact us immediately. This includes: Check whether the main motor, electric cabinet, servo motor of the back gauge and the plug of the machine circuit part are damp and water ingress, and check whether the pipe joints of the oil circuit are loose due to transportation. Check whether the cortex of the high-pressure hose is squeezed or damaged. When installing the valve group, keep the surrounding environment clean, and check whether the sealing ring is installed in place.
2.Check the oil pipe joint and install the sealing ring
When installing the oil pipe, be sure to check the oil pipe joint and install the sealing ring, then connect the oil pipe, and make sure the joint is tight! Any looseness will also cause the oil pipe to rupture because the oil pipe will be unevenly stressed.
3.Check the cleanliness of the inside of the fuel tank
Check the cleanliness of the inside of the oil tank. Due to transportation at sea or on the road, there may be rust inside. You need to open the oil tank for inspection and clean it before filling it with hydraulic oil. The oil level should be above 80 on the level gauge.
4.Check the tightness of the plug and conduct wiring test
Check the tightness of the plug in the electrical cabinet and conduct wiring test without error under dry conditions.
5.Test the back pressure valve pressure
After the machine is started, put the machine in the slow-down state, connect the valve group on the cylinder to test the back pressure valve pressure. When the machine is in the slow-down action, check whether the back pressure is 8 MPa.
6.Carry out lubrication maintenance
The parts of the machine body that need lubrication should be lubricated and maintained with hydraulic oil or lubricating oil.
7.Check whether the machine is running forward
After connecting the power cord and supplying power, check whether the two lights of the phase sequence protector inside the electrical cabinet are always on, which means that the machine is rotating forward.
How to Solve Common Press Brake Bending Issues?
Every product will have issues at one point in its usable lifespan and press brake machines are no different. Some press brake bending problems are more common than others. In this breakdown, we will look at the most common issues that users come across.
Problem 1: Why doesn’t the press brake bending machine move?
The problem:
The oil pump isn’t outputting oil and the Ram will not move.
Cause of the problem:
This issue happens when the pump is in the incorrect rotary direction.
How to fix this issue:
Interchanging the phase of the power supply is a known solution.
Problem 2: How to solve the abnormal oil pump?
The problem:
There could be a few problems here. The pump occurs an abnormal size and the pressure meter is unstable, the oil output pressure has decreased, or there is no output pressure at all.
Cause of the problem:
Four common issues cause this problem:
- The suction filter is blocked.
- More oil is needed in the oil tank.
- Oil is not getting in the pump and pipes.
- The components in the pump are damaged.
How to fix this issue:
This issue can be resolved in many ways.
- Clean the filter.
- Add oil to the level required.
- Replace the seal of the suction at the pipe joint and the end of the pump.
- Replace the component in the pump or replace the pump.
Problem 3: How to deal with oil leakage of press brake hydraulic system?
The problem:
There is leakage from the hydraulic valves, pipe joints, and/or cylinder.
Cause of the problem:
This issue is commonly one of two reasons:
- The connecting screw and pipe connector is loose.
- The seal is bad.
How to fix this issue:
The most common fixes to this issue are:
- Tighten the screw and connecter.
- Replace the seal.
Problem 4: Why is there no bending pressure in the hydraulic system?
The problem:
There isn’t pressure in the hydraulic system.
Cause of the problem:
This problem usually occurs for two reasons:
- The orifice and the core of the valve are blocked.
- The piston seal on the cylinder leaks.
How to fix this issue:
This problem is generally an easy fix in one of these two ways:
- Clean the orifice and the core valve.
- Replace the piston seal.
Problem 5: Why does the ram step down during pressing down?
The problem:
The Ram steps down during pressing down.
Cause of the problem:
This problem can occur for two common reasons:
- The balance pressure in the valve isn’t great enough.
- The guide rail is too tight.
How to fix this issue:
This problem can usually be solved in two simple ways:
- Increase the balance pressure.
- Loosen the guide rail.
Problem 6: Why does the ram drop down by itself?
The problem:
The ram is dropping on its own.
Cause of the problem:
This problem is caused by one of two different issues:
- The valve has become stuck.
- The piston seal of the cylinder is leaking.
How to fix this issue:
This issue can be fixed with simple cleaning and in some cases a replacement.
- Clean or replace the 1.0300 valve.
- Replace the piston seal.
Problem 7: Why there is pressure in the system as soon as the press brake start running?
The problem:
The press brake contains pressure in the system at the start of the operation.
Cause of the problem:
If you’re experiencing the press brake bending problems, there are two common causes:
- The orifice is stuck.
- There is an electrical fault.
How to fix this issue:
Most commonly this issue has a simple fix.
- Clean the orifice.
- Check the wiring for faults, exposed wires, or out of place wires.
Problem 8: How to solve the high noise in the high-pressure filter?
The problem:
The high-pressure filter gives off high noise.
Cause of the problem:
This is most commonly caused by a blockage in the high-pressure filter.
How to fix this issue:
Unfortunately, this press brake bending problems do not have an easy solution. You will need to replace the core of the high-pressure filter.
Problem 9: Why doesn’t the ram work properly?
The problem:
The ram is not retracting automatically, cannot retract after the upper die press or bottom die press, or the ram cannot move down at certain positions.
Cause of the problem:
The selected tools in the computer are not the actual tools in use.
How to fix this issue:
This press brake bending problem can be solved by verifying that the selected tools and tools in use are the same.
Common press brake faults and maintenance
Most of the faults in CNC press brakes are caused by the prolonged use of the guide rail, improper lubrication of the guide rail, leading to increased clearance due to wear and tear.
Such faults require inspection to determine the cause, repair or replacement of faulty components, and troubleshooting.
Here, the press brake manufacturer will analyze the common mechanical faults and their maintenance for everyone.
Due to the heavy load, inadequate lubrication of the moving parts, and complex working environment, press brakes are prone to wear and tear and damage to the moving parts.
If the damage is severe, replacement is required. The feeder shaft driver, servo motor failure, and upper computer control system failure are common faults.
1. Inconsistent dimensions of the back gauge (big and small ends)
If the error at both ends is small, within 2mm, check and confirm that there are no faults in the X1/X2 mechanical transmission structure. The error can be eliminated by adjusting the stopper finger.
Tin bronze or nodular cast iron should be selected, and the fitting surface should be ground on a surface grinder. The connecting bolts should be lower than the fitting surface, and an inverted V-shaped lubricating oil groove should be provided.
2. Abnormal noise when the slide block moves downward during work feeding
Check the wear degree of the guide rail pressing plate and readjust it to the required clearance.
a. The original pressing plate has a plastic covering. Pay attention to the hardness of the covering, the fitting surface with the guide rail. After scraping, the press brake ensures that the fitting surface is above 85%, and an inverted V-shaped lubricating oil groove is provided.
b. The original pressing plate contains a metal plug. Readjust it within the tolerance range of parallelism and reinstall the synchronous transmission device.
3. No action from the back gauge shaft
The reason for the failure of the rear material stopper shaft transmission may be that the transmission shaft is detached from the timing pulley or key bar, or the timing belt slips.
4. Loose connection between the hydraulic cylinder and the slide block
A loose connection between the hydraulic cylinder and the slide block can cause inaccurate bending angles or the machine not being able to find the reference point.
If there are no faults in the mechanical transmission structure (such as bearings, ball screws, linear guides, transmission wheels, transmission belts, etc.), troubleshoot the fault. Determine whether to replace the guide rail pressing plate based on the degree of wear.
Conclusion
When evaluating the total costs of purchasing, maintaining, and operating sheet metal equipment, KRRASS stands out as the ideal choice for your fabrication needs. Known for its exceptional reputation, KRRASS delivers unparalleled consistency and quality at the most competitive prices. Whether you're looking for a press brake or any other specialized equipment, our team of experts combines deep industry knowledge with cutting-edge tools to provide you with the best solutions available. Additionally, we offer a fully integrated online system that simplifies the process—just share your product requirements, request a quote, and you're on your way.