When it comes to bending cosmetically sensitive parts, we often deal with prefinished materials like repolished, preprinted, coated, or laminated sheet metals. These materials, along with softer ones like copper and brass, or those with unique patterns such as tread plate and texture-finished surfaces, are prone to marring or cosmetic damage. To prevent such issues, cosmetic press brake tools play a crucial role, offering solutions to avoid surface imperfections during bending. You can find such scenarios in various industries, from architectural metal and appliance manufacturing to medical, pharmaceutical, lighting, and ornamental fabrication.
What is the culprit behind this marring, scratching, and distortion? It all boils down to the very nature of bending on the press brake. The most common operation, the right-angle bend, sees the sheet metal being drawn into the V-die over the two top shoulders. And guess what? This is where most of the surface damage occurs, like a battleground where the metal's smooth surface gets scarred (see Figure 1).
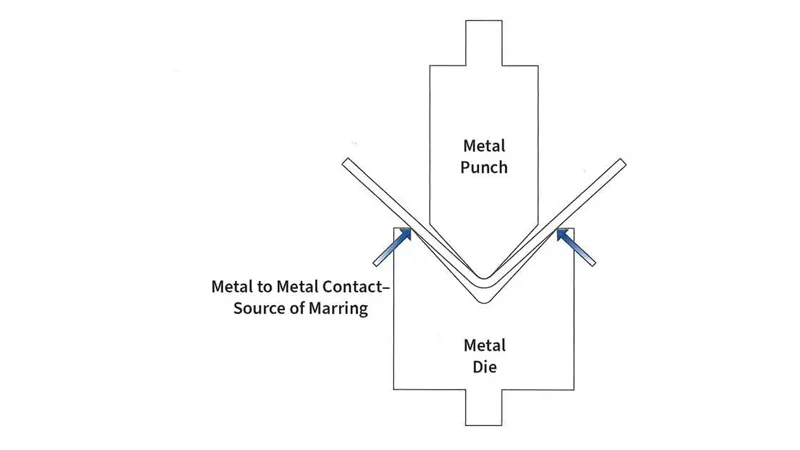
But fear not! We can turn the tables by altering that tool-to-workpiece contact. Here's where polyurethane (or urethane) film and tooling step in as the significant changes.
Urethane Films: The Protective Shield
Urethane tools come in a dazzling array of types, shapes, and sizes, tailored to the production quantity and shape complexity of the part being formed. The most common and budget-friendly option is the trusty urethane film. Acting as a guardian angel, it shields the sheet metal from the steel die during V-bends, preventing any unsightly surface marring.
These films are available in various widths and come in 100-ft.-long rolls of 0.015- or 0.030-in.-thick material, ready to be cut to the perfect length. Placed on top of the V-die and secured with double-face tape, C-clamps, or magnets, they stand as the first line of defense. However, like a delicate flower in a storm, urethane film tends to wear out quickly, demanding frequent replacements from the operators.
To combat this time-consuming task, some operations have turned to high-performance thermoset urethane tape, which lasts about three times longer than its conventional counterpart. Alongside this, many bending setups now feature film holders and positioners that work like a well-oiled machine, dispensing and positioning the film with precision, both lengthwise and front to back (see Figure 2).
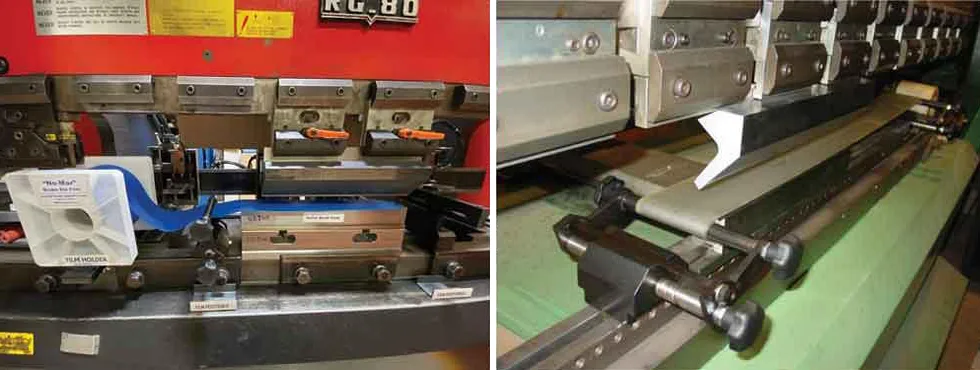
Urethane V-Pad Inserts: The Precision Sculptors
These triangular wonders, the urethane V-pad inserts, are placed into the V-cavity of the steel bottom die, like a custom-fit glove, ensuring no metal-to-metal contact on the outside radius during bending. They come in two forms: solid pads for those sharp V-bends that demand precision, and ones with a molded hole in the middle, reducing the required forming tonnage as if lightening the load on a weary traveler (see Figure 3).
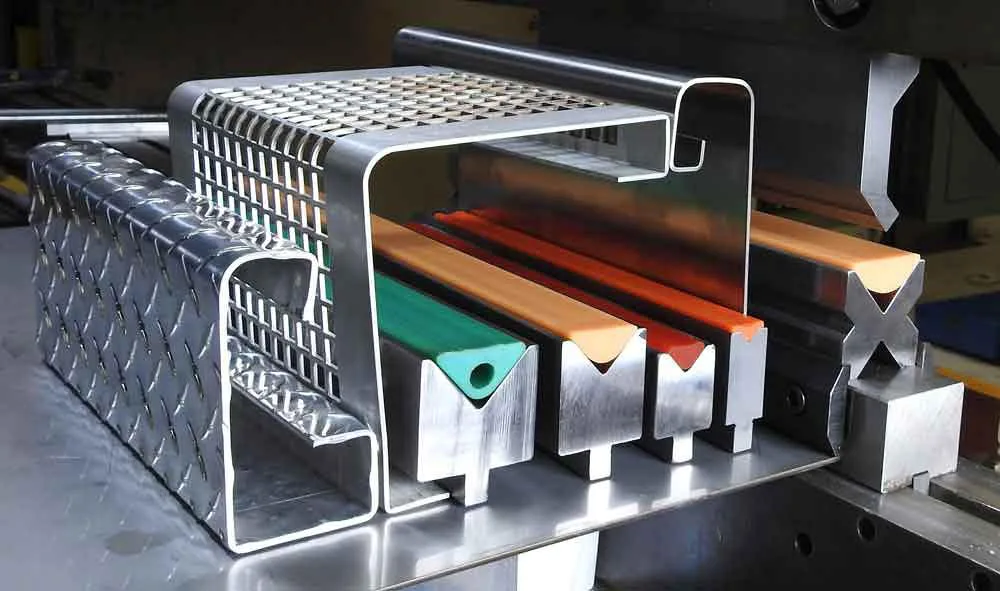
V-pads are the go-to solution for bending challenging materials like perforated sheet and tread plate. They work like a gentle yet firm hand, providing upward pressure to lift the part and wrap it snugly against the punch, ensuring no breaking or distortion at the weak points.
For tread plate bending, certain V-pads with a molded hole for radius bends are like a magic wand, reducing the tonnage needed to deflect. When tread plate meets a conventional V-die, it is like a bumpy ride, with the individual treads dragging along the die shoulders, marring the material, damaging the diamonds, and creating an unstable bending process that is as unpredictable as the wind. But with a urethane V-pad die, the situation transforms. Instead of a chaotic drag, the tread protrusions dig into the urethane pad, creating a harmonious, mar-free bending symphony.
A V-pad filling the cavity of a steel V-die is like a key that unlocks the potential to bend narrow flanges, where the flange widths can be as narrow as two to three times the metal thickness. The punch radius and angle are the conductors, dictating the angle and radius that the workpiece will sing.
Even on older press brakes with a wavy bed or imperfect parallelism to the ram, a perfectly straight bend is within reach if the punch stands tall and straight. The flexible V-pads are like a flexible bridge, filling the gaps and wrapping the sheet metal tightly against the punch.
Urethane Forming Pads: The All-Round Performers
Square or rectangular deflecting-type pads, placed in steel holders that fit snugly on the press brake bed, the urethane forming pads are like chameleons, available in different hardnesses to adapt to bending different gauges of sheet metal. With this setup, an operator can perform sharp or radius bends with the same urethane-pad die, like a magician pulling off different tricks with the same wand.
During the bending cycle, these urethane forming pads behave like a hydraulic fluid bladder, diffusing the press brake's downward force in all directions, like ripples spreading across a calm lake (see Figure 4). Placed in a metal holder or retainer (with bolted tangs to fit most common press brakes), most of the applied load is redirected upward, like a fountain shooting water upwards, wrapping the sheet metal tightly against the descending punch. Whatever angle or radius is on the punch is faithfully reproduced on the sheet metal, allowing for the natural spring back, like a rubber band snapping back to its original shape.
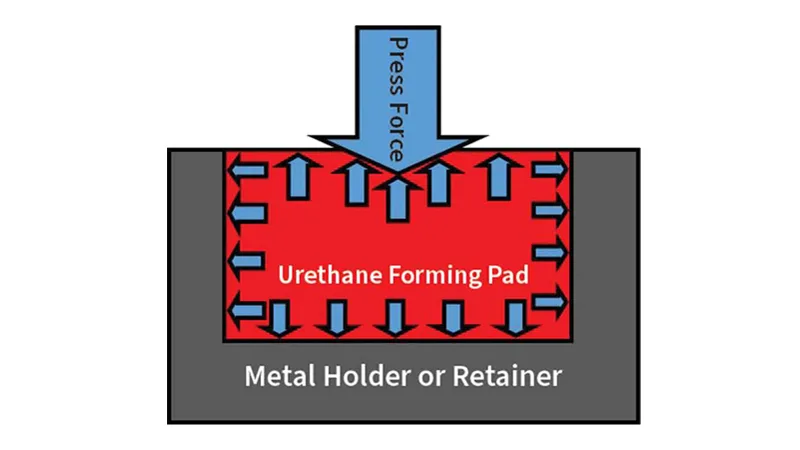
An effective urethane-pad die design is like a maestro, controlling and directing the forming forces to perform the bending ballet without overstressing the urethane. Hysteresis, that annoying internal heat buildup caused by stress, is the Achilles' heel of urethane pads. It takes about three times the tonnage to form with a solid pad compared to steel V-dies, like a heavyweight lifting a much heavier load. Pads with molded holes are not only like a helping hand, reducing the load required to deflect, but also like a cooling breeze, reducing the stress from hysteresis and prolonging the pad's life.
These pads are the stars when it comes to forming 180-degree U-bends. The pad's molded U-shape, combined with molded holes engineered to a specific size and shape, is like a secret recipe for success, enabling overbending by 15 to 20 degrees to account for spring back, like a baker adding a little extra to ensure the perfect rise (see Figure 5).
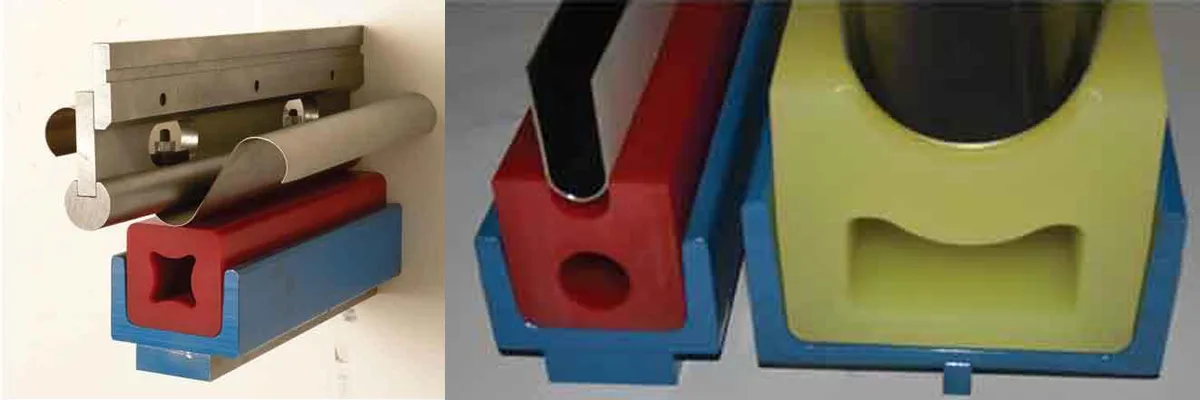
Beyond U-bends, urethane pads are the heroes that save the day when forming large radii into cosmetically critical parts. Take column covers in architectural fabrication, for example. These large and long beauties must be formed uniformly and without a single blemish, like a flawless diamond.
Radius bending is like a treacherous mountain to climb in the world of press brake applications, involving a complex mix of shapes, sizes, and diverse types of metals. With a conventional steel punch and V-die and an advanced CNC press brake, an operator forms a large radius with sequential bumps ¼ to ½ in. apart, leaving behind "bump lines" like unwanted footprints in the material. If the resulting radius is off, it is like a wrong note in a symphony, and the part must be scrapped, starting the process all over again. And if the spring back varies from sheet to sheet, it is like a chaotic dance with no rhythm.
But urethane comes to the rescue once again! A metal radius punch, machined to perfection to allow for spring back, or even something as simple and economical as a heavy-walled steel pipe with a welded tang, can form a large radius into a die with a urethane pad, like a skilled artist painting a smooth curve. This eliminates the need for bumping and all its associated headaches, including those annoying bend-line marks, like erasing the wrong strokes on a canvas (see Figure 6).
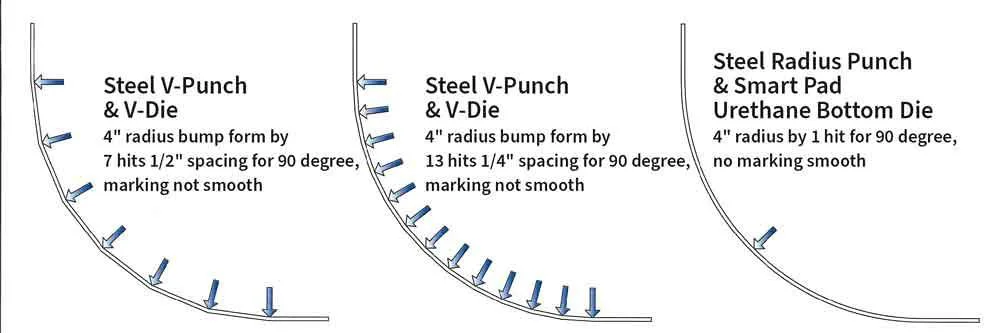
For instance, a 12-in.-wide urethane radius-forming pad is like a powerful wizard, capable of bending an 8-in. arc length to any radius larger than the punch radius, if the setup allows for spring back. Any shape that demands more arc length can be bump-formed with about an inch overlap between bends, leaving the outside as smooth, without any bump lines. Most common U-bends with a radius up to 24 in. can be achieved in three to five hits, like a swift and efficient dance routine.
Such radius bends can be as complex as a labyrinth. Consider the drawing of an architectural panel in Figure 7. Made of 0.125-in.-thick aluminum from a 26- by 120-in. blank, it was bent using one steel punch and a proprietary urethane-pad bottom die system. Two 1.446-in.-radius bends were crafted, and a separate 8-in.-wide punch was developed to bump-form the 18.7264-in. radius (with spring back accounted for) in just three hits, like an expert craftsman creating a work of art. The ends of the large radius blend seamlessly with the two 1.446-in. radii on either end (hence the 1.570-in. intermediate radius marked on the drawing). The entire panel was bent in five hits, emerging without a single bump line or surface mark, like a pristine mirror.
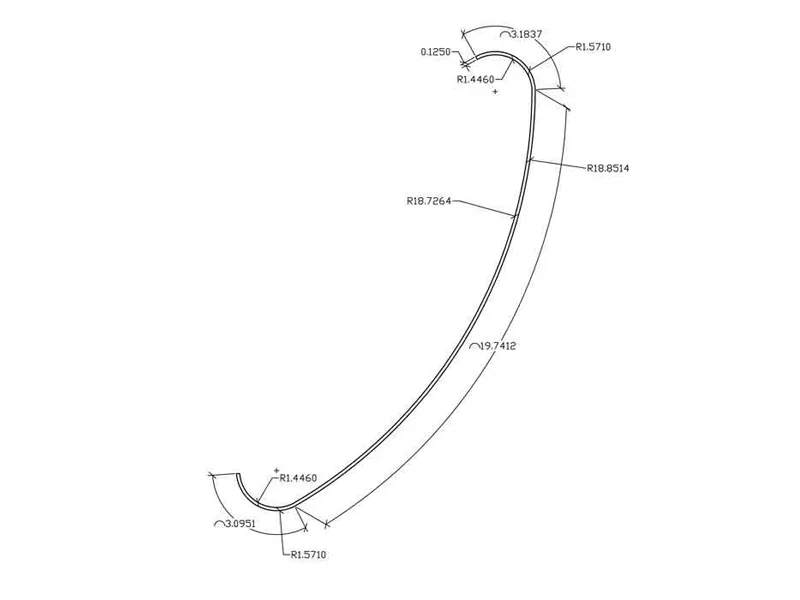
Figure 8 highlights another radius-bending marvel: U-troughs for grain elevators and screw conveyors. Fabricated using a proprietary urethane pad system, the same urethane bottom die is like a versatile toolbox, capable of bending any gauge or type of material to any radius equal to or larger than the steel punch radius (with spring back in mind). The tools in this application can form a U-shape of any size up to a 24-in. radius. Switching to a new product? Just swap out the steel punch, and you are good to go. Bump forming this product used to take forty-four hits spaced ½ in. apart, like a long and arduous journey. But now, with just one urethane-pad die and a large round punch, it is done in three hits, like a quick and easy shortcut.
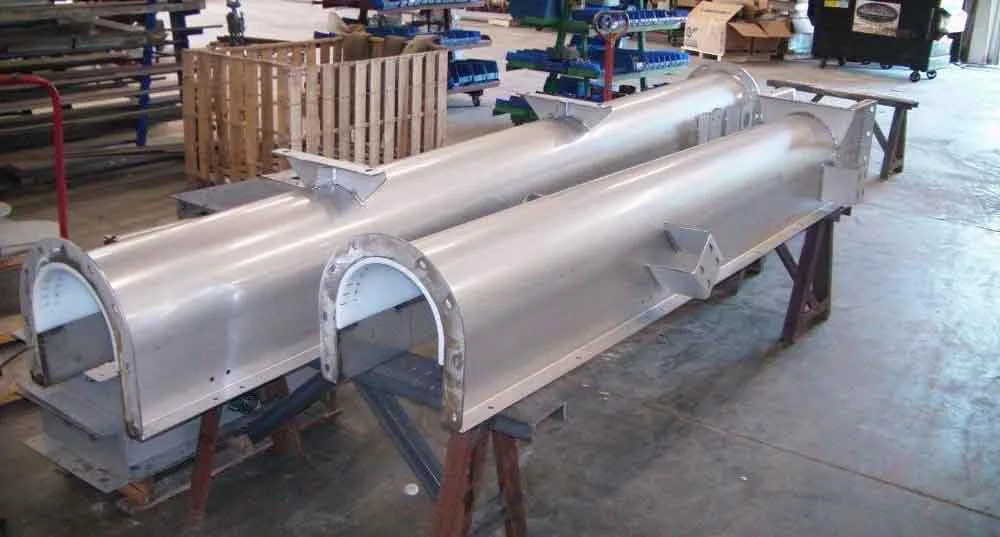
Urethane pads also work their magic when it comes to forming perforated and other hole-intensive sheets. Look at the perforated stainless steel muffler guards in Figure 9. A green urethane pad teams up with an amber wear pad and a step in the steel punch, like a superhero trio, to form the edge hems. The wear pad is like a shield, protecting the main forming pad from the sharp edges of the perforated sheet.
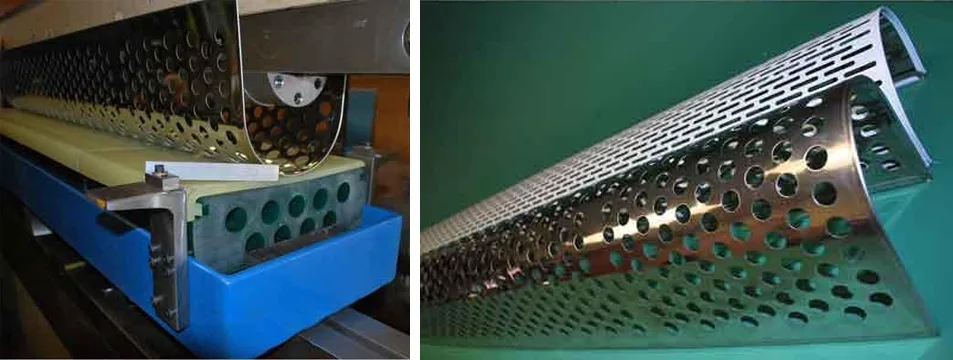
Urethane Dies: The Durable Transformers
Molded from a hard and durable urethane grade, urethane V-dies are like the dependable workhorses of the bending world, functioning just like their steel counterparts. With a lifespan of up to 50,000 bends, they are the ideal choice for high-volume 90-degree bends, like a marathon runner with endurance for the long haul. Solid urethane V-dies are widely used in various sectors, especially in high-end appliance manufacturing, where precision and durability are the name of the game.
These nondefecting tools are designed with air bending in mind, like a precision instrument tuned for a specific task. Like the best practices with steel dies, the openings in urethane V-dies should be eight to ten times the metal thickness, depending on whether you are bending mild or stainless steel, like a carefully calibrated recipe.
Their lightweight nature is like a feather, making tool changes a breeze. Some dies come with two V-openings that can be flipped front to back, like a two-sided coin, for bending different material thicknesses (see Figure 10).
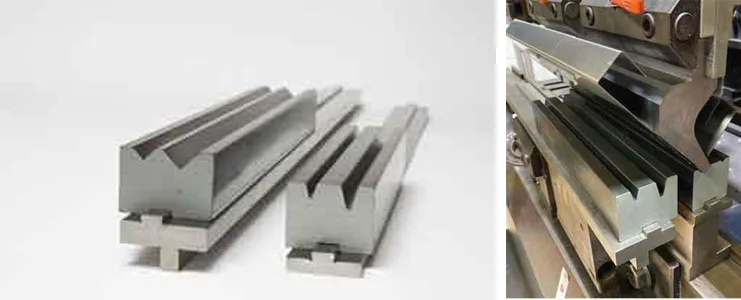
Modern designs of composite urethane V-dies, molded with single or multiple V’s across the width of the tool body and sitting in machined steel holders that fit various press brake styles, are like a technological upgrade. Depending on the application requirements, these tools can bend up to 10-ga. stainless steel, like a powerful machine ready to take on any challenge (see Figure 11).
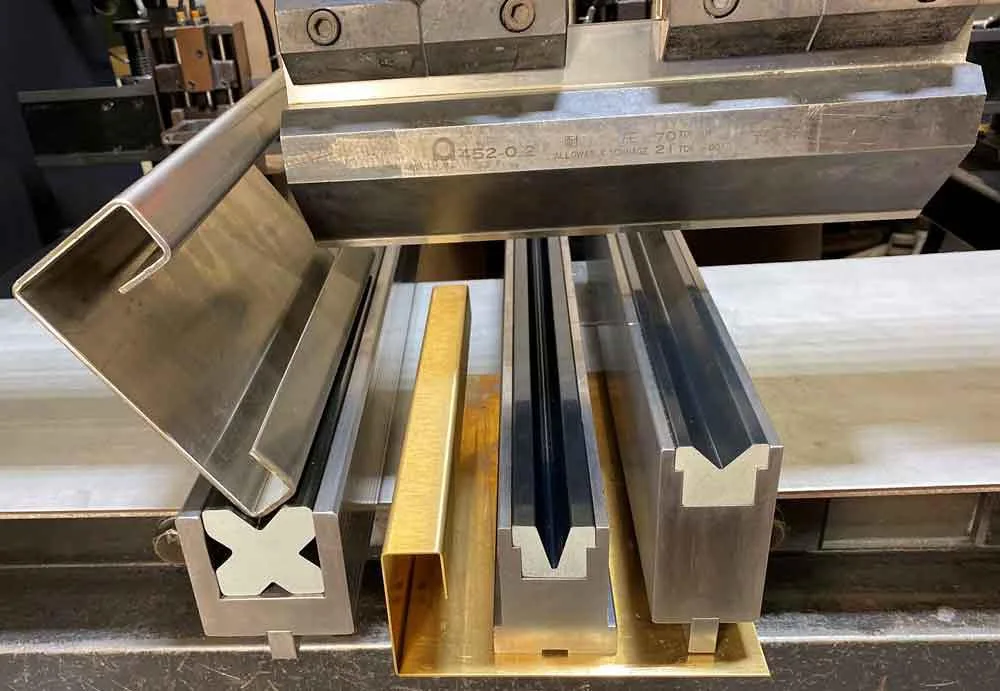
Another type of solid urethane die is like a wizard's wand for forming hems in thin metals. With these tools, operators can perform a single-setup, two-hit hemming and flattening operation, like a seamless dance of precision.
Urethane dies are not limited to just air bending over conventional V’s or hemming. Take the bullnose bending application in Figure 12, for example. The bull-nose bend geometry is like a sculptor's tool, creating radius edges for medical implements, countertops, shelves, tabletops, and other products in the medical, pharmaceutical, and food-service sectors. The 180-degree bend is achieved in two hits with a hard, nondefecting urethane die, like a two-step magic spell. A stop at the edge of the radius portion of the die is like a guiding star, allowing operators to bend the radius right to the very edge of the sheet metal.
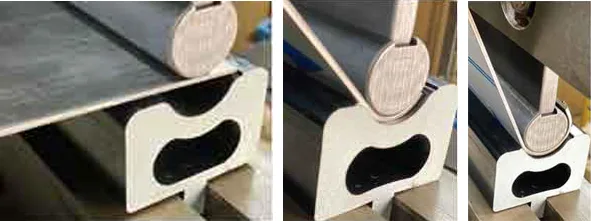
Cosmetic Press Brake Tools: The Urethane Tools
All these examples are just the beginning when it comes to the wonders of urethane press brake tools. They highlight how urethane can achieve mar-free bending and boost productivity, especially when it comes to taming those large-radius bends. Performing a few bumps into a urethane pad is like a lightning-fast shortcut compared to the laborious process of bumping dozens of bend lines with a traditional punch and V-die.
However, surface imperfections in sheet metal do not always stem from the physical force of bending on a press brake. Sometimes, it is a chemical culprit. For instance, bending repolished stainless steel with conventional steel tooling can contaminate the workpiece, like a dark cloud casting a shadow. The bend lines can have ferric particles embedded in the surface, which can later show up as rust lines after prolonged exposure to moisture, like an unwelcome guest that ruins the party. This is an unacceptable flaw in medical or pharmaceutical applications. But fear not, these problems can be avoided by using nonferric punches and dies, including the trusted urethane tools.
Whether the problem is physical or chemical, it all boils down to the nature of contact between the punch, die, and workpiece. This includes what touches the workpiece and how that contact occurs throughout the bending cycle. By mastering this, you can achieve flawless results with cosmetic press brake tools, ensuring a perfect appearance for cosmetically sensitive parts.