In today's rapidly evolving manufacturing landscape, automated press brakes have emerged as pivotal tools driving efficiency and precision in metal fabrication. These advanced machines combine the traditional capabilities of press brakes with sophisticated automation technology, revolutionizing how metal components are bent and formed.
By integrating automated features such as computerized controls, robotic arms, and advanced sensors, automated press brakes not only streamline production processes but also enhance consistency and accuracy to unprecedented levels. This article delves into the transformative impact of automated press brakes, exploring their key benefits, technological advancements, and applications across various industries.
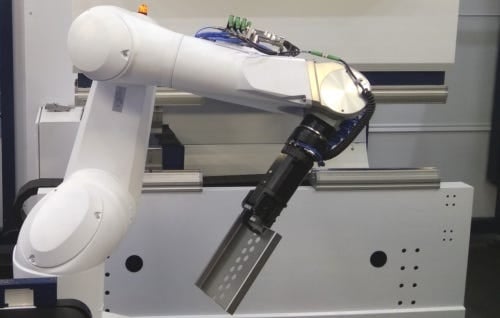
Introduction to Automated Press Brakes
What Is Robotic Automated Press Brake
A robotic automated press brake is a machine that implements a robotic arm to perform various pressing functions. It enables manufacturers to automate pressing processes, which allows them to save time and money. A robotic press brake is a computer-controlled machine that applies force to parts by pressing them between a die and a bed. Robotic press brake manufacture parts for automobiles, aerospace, shipbuilding, and other industrial sectors.
Automated press brakes are advanced metal bending machines that incorporate automation technologies to enhance efficiency, precision, and repeatability in the metal fabrication process. Unlike traditional manual press brakes, which require significant operator intervention and expertise, automated press brakes utilize computer numerical control (CNC) systems to manage and execute bending operations with minimal human input. Key functionalities of automated press brakes include:
- CNC Control Systems: Automated press brakes are equipped with CNC controllers that precisely manage the bending process by following programmed instructions. This ensures consistent and accurate bends, reducing the likelihood of errors.
- Automated Backgauges: These components position the metal sheet accurately before bending, enhancing precision and reducing setup time.
- Robotic Integration: Some advanced automated press brakes incorporate robotic arms for loading, unloading, and handling materials, further streamlining the production process.
- Sensors and Monitoring: Automated press brakes often feature sensors that monitor the bending process in real-time, ensuring quality control and enabling adjustments to be made on the fly.
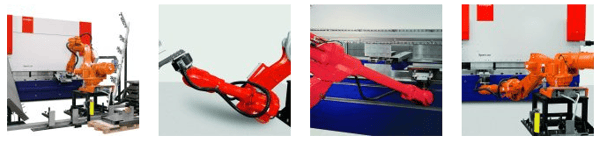
Evolution from Manual to Automated Systems in Metal Fabrication
The transition from manual to automated press brakes marks a significant evolution in the metal fabrication industry. Initially, manual press brakes required skilled operators to perform precise measurements and adjustments, making the process labor-intensive and prone to human error. The introduction of CNC technology revolutionized press brake operations by allowing for programmable control over the bending process.
- Manual Press Brakes: In manual systems, operators manually adjust the backgauge, set the bend angle, and position the metal sheet for each bend. This requires high levels of skill and experience, as well as significant physical effort.
- Hydraulic Press Brakes: The development of hydraulic press brakes improved upon manual systems by providing greater force and control, but still relied heavily on operator expertise for setup and operation.
- CNC Press Brakes: The advent of CNC technology allowed for the automation of many aspects of the bending process. CNC press brakes can store and execute complex bending sequences with high precision, significantly reducing the need for manual adjustments.
- Automated and Robotic Press Brakes: The latest advancements integrate robotic arms and automated systems with CNC press brakes, further enhancing efficiency, precision, and flexibility. These systems can operate continuously with minimal human intervention, making them ideal for high-volume production and complex bending tasks.
This evolution reflects the ongoing pursuit of efficiency and accuracy in metal fabrication, driven by technological advancements and the increasing demand for high-quality, cost-effective manufacturing solutions. Automated press brakes represent the cutting edge of this evolution, offering unparalleled capabilities for modern metalworking applications.
Types of Robotic Automated Press Brakes
PICK-AND-PLACE ROBOTIC PRESS BRAKES
Pick-and-place robotic press brakes are ideal for manufacturing smaller parts. These machines have a vision system and an automated arm that handles small components and allows the robot to view the part.
In addition, these robots include a suction cup, a gripper, and a vacuum table programmed to pick up a part and place it at the required location.
BLIND ROBOTIC PRESS BRAKES
Blind robotic press brakes are used to manufacture larger parts. These presses have vision systems; however, some make smaller parts using blind robotic press brakes.
However, these types of presses can't be used for precision work.
Technological Advancements
1. Overview of Automation Technologies Integrated into Press Brakes
Automated press brakes have undergone significant advancements with the integration of various automation technologies, each contributing to enhanced efficiency, precision, and flexibility in metal fabrication. These technologies include:
Computer Numerical Control (CNC) Systems: CNC technology is the backbone of automated press brakes, enabling programmable control over bending operations. CNC systems allow for precise execution of complex bending sequences, reducing human error and ensuring consistent quality.
Robotic Arms: Robotic integration allows for automated loading, unloading, and handling of materials. Robotic arms can work in tandem with press brakes to position metal sheets accurately, enhancing productivity and reducing manual labor. These robots can be programmed to handle repetitive tasks with high precision, further increasing the efficiency of the bending process.
Automated Backgauges: These devices are essential for positioning the metal sheet before bending. Automated backgauges move according to programmed instructions, ensuring precise alignment and reducing setup time. They adjust the position of the sheet metal automatically, allowing for quick and accurate adjustments during the bending process.
Sensors and Real-Time Monitoring: Advanced sensors monitor various parameters of the bending process, such as force, angle, and position. Real-time monitoring ensures that any deviations from the desired parameters are quickly corrected, maintaining high-quality output. Sensors can detect issues such as incorrect alignment or material inconsistencies, enabling immediate adjustments to maintain precision.
Human-Machine Interface (HMI): Modern press brakes feature intuitive HMIs that allow operators to easily program and control the machine. Touchscreen interfaces, graphical displays, and user-friendly software simplify the setup and operation processes. HMIs provide visual representations of the bending process, making it easier for operators to understand and manage complex operations.
Automated Tool Changers: These systems automatically switch tools as needed, allowing for seamless transitions between different bending operations without manual intervention. Automated tool changers reduce downtime and increase overall productivity by enabling quick changes between various tooling setups, which is particularly useful for small batch production runs or when dealing with multiple product variations.
Adaptive Bending Systems: These systems use feedback from sensors to make real-time adjustments to the bending process, ensuring optimal performance and precision. Adaptive systems can adjust parameters such as bending speed and force in response to variations in material properties, further enhancing the accuracy and consistency of the final product.
2. Role of Computer Numerical Control (CNC) Systems in Enhancing Precision
CNC systems play a pivotal role in enhancing the precision and efficiency of automated press brakes. The integration of CNC technology brings several advantages to the bending process:
Accurate Programming: CNC systems enable precise programming of bending sequences. Operators can input specific dimensions, angles, and positions, ensuring that each bend is executed exactly as required. This reduces variability and enhances the consistency of the final product. The ability to store and recall complex bending programs also simplifies the production of repeat orders and ensures that all parts meet the same high standards.
Complex Bend Sequences: CNC technology allows for the creation of intricate bend sequences that would be challenging or impossible to achieve manually. Multiple bends can be programmed and executed in a single setup, improving efficiency and reducing the need for rework. This capability is particularly valuable in the production of complex components with tight tolerances.
Repeatability: CNC systems ensure that each part produced is identical to the previous one, maintaining high levels of repeatability. This is particularly important in mass production, where consistent quality is essential. CNC-controlled press brakes can produce thousands of parts with minimal variation, ensuring that all components fit together correctly in the final assembly.
Error Reduction: By automating the bending process, CNC systems minimize the risk of human error. Once programmed, the machine executes the bends with high precision, reducing the likelihood of mistakes and the associated costs. CNC systems also include diagnostic tools that help operators identify and correct errors quickly, further reducing downtime and waste.
Real-Time Adjustments: CNC systems can make real-time adjustments based on feedback from sensors and monitoring systems. If any deviation from the programmed parameters is detected, the CNC system can correct it on the fly, ensuring that the final product meets the required specifications. This capability is crucial for maintaining quality control in high-volume production environments.
Efficiency and Productivity: The speed and accuracy of CNC systems enhance overall productivity. Automated press brakes with CNC technology can operate continuously with minimal downtime, significantly increasing throughput and reducing lead times. The ability to quickly switch between different bending programs and tooling setups also allows manufacturers to respond more rapidly to changing production requirements.
Integration with Other Manufacturing Systems: CNC systems can be integrated with other manufacturing technologies, such as computer-aided design (CAD) and manufacturing (CAM) software, to streamline the entire production process. This integration allows for seamless transfer of design data to the press brake, reducing the time and effort required for programming and setup.
In summary, the integration of CNC systems into automated press brakes revolutionizes the metal fabrication process by enhancing precision, reducing errors, and improving overall efficiency. These technological advancements enable manufacturers to meet the high standards of modern industry demands, providing superior quality and performance in metalworking applications. By combining CNC technology with other advanced automation systems, manufacturers can achieve unprecedented levels of productivity and flexibility, positioning themselves for success in an increasingly competitive market.
Benefits of Using Automated Press Brakes
1. Improved Efficiency and Reduced Setup Times
- Automated Adjustments: Automated press brakes can adjust settings and tooling automatically based on pre-programmed instructions, drastically reducing the time needed for manual adjustments. This automation allows for quick changeovers between different bending tasks, minimizing downtime.
- Streamlined Workflow: Integration with CAD/CAM systems enables seamless transfer of design data to the press brake, eliminating the need for manual data entry and reducing the likelihood of errors. This streamlining of workflow leads to faster production cycles.
- Pre-programmed Sequences: Operators can store and recall complex bending sequences, ensuring that setups for repeat orders are quick and accurate. This capability is particularly valuable in high-mix, low-volume production environments where frequent setup changes are required.
- Enhanced Coordination: Automated press brakes can be integrated with other automated systems, such as robotic arms and conveyor belts, to create a fully coordinated production line. This integration further reduces setup times and enhances overall efficiency.
2. Enhanced Accuracy and Repeatability in Bending Operations
One of the most significant advantages of automated press brakes is their ability to consistently produce high-quality bends with exceptional accuracy and repeatability. Key benefits include:
- Precision Control: CNC systems enable precise control over every aspect of the bending process, from the angle and force applied to the exact position of the sheet metal. This precision ensures that each bend meets the required specifications.
- Consistent Quality: Automated press brakes can perform the same bending operations repeatedly with minimal variation. This consistency is crucial in industries where parts must fit together perfectly in assemblies, such as automotive and aerospace manufacturing.
- Reduced Human Error: Automation minimizes the risk of human error, which can lead to costly mistakes and rework. By automating the bending process, manufacturers can ensure that each part is produced to the same high standards.
- Real-Time Feedback: Advanced sensors and monitoring systems provide real-time feedback during the bending process, allowing for immediate adjustments to correct any deviations from the desired parameters. This real-time correction capability ensures that the final product maintains high quality.
3. Minimized Material Waste and Increased Productivity
Automated press brakes contribute to more efficient use of materials and higher overall productivity. Key benefits include:
- Optimized Material Usage: CNC systems can optimize the bending process to minimize material waste. By precisely controlling the bending sequence and force, automated press brakes can reduce the likelihood of material deformation or breakage.
- Efficient Nesting: Integration with CAD/CAM systems allows for efficient nesting of parts on the sheet metal, maximizing material utilization and reducing scrap. This efficient nesting leads to cost savings and a more sustainable manufacturing process.
- Faster Production Cycles: Automated press brakes can operate continuously with minimal downtime, significantly increasing throughput. The ability to quickly switch between different bending programs and tooling setups also enables manufacturers to respond more rapidly to changing production requirements.
- Increased Throughput: The high speed and precision of automated press brakes result in faster production cycles, enabling manufacturers to produce more parts in less time. This increased throughput translates to higher productivity and the ability to meet tight deadlines.
- Lower Operating Costs: By reducing setup times, minimizing material waste, and increasing production speed, automated press brakes help lower overall operating costs. These cost savings can be passed on to customers or reinvested in further process improvements.
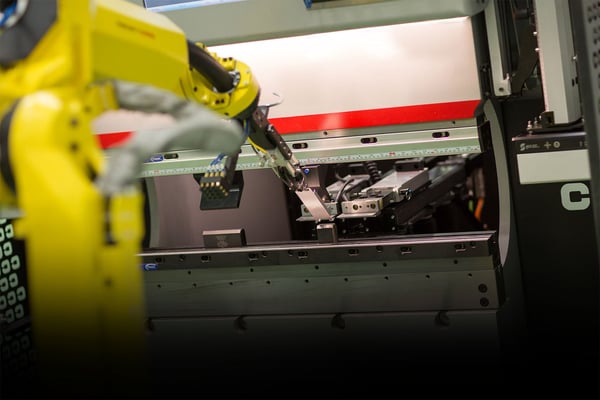
3 Ways A Robotic Automated Brake Helps
REDUCE HUMAN ERROR
The more manual parts of your production process, the more opportunity for human error. A robotic press brake helps to reduce human error in several ways. A robotic press brake is programmable and produces the same part with consistent accuracy. It also adjusts to compensate for operator error.
The machine compensates if the operator accidentally uses too low or too high force.
That means a robotic press brake produces quality parts every time, even if the operator is new or making a mistake.
Robots also don't get tired or distracted. A production line pauses while an operator takes a break, slowing production.
A robotic press brake runs 24 hours by programming, requiring no rest and helping consistently meet production goals
INCREASE PRODUCTIVITY
A robotic press brake dramatically increases your production capabilities. With a press brake, you get one shot at forming each part.
The press brake brings the metal sheet down onto the part to be formed, finishing the part.
However, robotic press brakes are programmed to move metal sheets without continually forming them.
This process allows the machine to form multiple parts, making no adjustments to the machine after the first part is formed.
Thus, a robotic press brake forms multiple parts while only taking up the same amount of space as one press brake.
Just like a robotic press brake runs 24 hours a day, it can also be programmed to run as quickly as possible, forming parts to meet production schedules.
PRODUCE TIGHTER TOLERANCES
Consistent tolerances are essential when manufacturing parts. If different parts have different tolerances, they may not work together correctly, reducing durability.
A robotic press brake allows you to set the exact pressure that forms each part, meaning you set tighter tolerances for each part.
If you're manufacturing something that must fit together perfectly, having tighter tolerances is critical.
A robotic press brake also reads the thickness of the sheet of metal and makes minor adjustments to compensate for any thickness variations: even if your sheet metal supplier has some slightly thicker or thinner sheets than others, the robotic press brake compensates.
Applications Across Industries
1. Automotive Sector: Tailored Manufacturing Solutions for Complex Parts
In the automotive sector, automated press brakes provide tailored manufacturing solutions that meet the industry's high demands for precision, efficiency, and adaptability. Key applications include:
- Complex Component Fabrication: Automotive parts often require complex bends and intricate shapes. Automated press brakes, with their CNC-controlled precision and ability to handle complex bend sequences, are ideal for producing these parts with high accuracy.
- High-Volume Production: The automotive industry often requires the production of large quantities of parts within tight timeframes. Automated press brakes enhance productivity through quick setup times and high-speed operations, ensuring that production schedules are met without compromising quality.
- Customization and Flexibility: Automated press brakes can easily switch between different bending programs and tooling setups, allowing manufacturers to produce customized parts for various vehicle models and designs. This flexibility is crucial for meeting the diverse needs of automotive manufacturers and their clients.
- Consistency and Repeatability: The automotive industry demands consistency and repeatability in every part produced. Automated press brakes ensure that each component meets the required specifications, reducing the risk of defects and improving overall vehicle quality.
- Integration with Robotic Systems: In automotive manufacturing, automated press brakes can be integrated with robotic arms for material handling and assembly processes. This integration streamlines production lines, reduces manual labor, and increases overall efficiency.
2. Aerospace Industry: Meeting Stringent Quality Standards with Automated Precision
The aerospace industry requires components that meet stringent quality standards and precise tolerances. Automated press brakes are well-suited to meet these demands through:
- High Precision and Accuracy: Aerospace components often have complex geometries and require exacting precision. Automated press brakes, with their advanced CNC systems and real-time monitoring capabilities, ensure that every bend is executed with the utmost accuracy.
- Material Compatibility: Aerospace manufacturing often involves working with high-strength materials such as titanium and aluminum. Automated press brakes are capable of handling these materials with precision, ensuring that the final components meet the industry's rigorous standards.
- Quality Control: The aerospace industry has zero tolerance for defects. Automated press brakes, equipped with sensors and real-time feedback systems, provide continuous quality control throughout the bending process, ensuring that each part meets the necessary specifications.
- Traceability and Documentation: Aerospace manufacturing requires detailed documentation and traceability for every component. Automated press brakes can integrate with data management systems to record and track each bending operation, providing a comprehensive audit trail for quality assurance purposes.
- Efficiency in Low-Volume Production: While some aerospace components are produced in large quantities, others are made in low volumes. Automated press brakes offer the flexibility to efficiently handle both high-volume and low-volume production runs, making them ideal for the diverse needs of the aerospace industry.
In summary, automated press brakes play a critical role across various industries by providing tailored solutions for complex parts, meeting stringent quality standards, and offering versatility in handling diverse materials and batch sizes. Their integration into manufacturing processes enhances precision, efficiency, and productivity, making them a valuable asset for automotive, aerospace, and general manufacturing applications.
Who Should Use Robotic Automated Press Brakes?
Manufacturers looking to improve operational efficiency and boost production should invest in robotic press brakes. Robotic press brakes manufacture a wide range of parts, including small and large components.
Robotic press brakes perform various tasks, including loading, unloading, and palletizing, which help manufacturers improve accuracy and save time, which conventional presses can't do.
Robotic automated press brakes have emerged as one of the most promising solutions for manufacturers. They manufacture various parts, including small and large components, helping manufacturers improve operational efficiency and boost production.
These press brakes are valuable equipment for any manufacturing company. They reduce human error, increase productivity, and produce tighter tolerances. As the manufacturing industry becomes more competitive, staying on top of production is crucial.
A robotic press brake helps you do just that.