Enter the mini press brake – a compact, yet powerful solution designed to meet the exacting demands of precision bending. These machines offer unparalleled accuracy and versatility in a smaller footprint, making them ideal for small workshops, DIY enthusiasts, and even large-scale operations that require additional precision tools. In this article, we will explore how mini press brakes provide compact solutions for precision bending, highlighting their benefits, applications, and key considerations for choosing the right model.
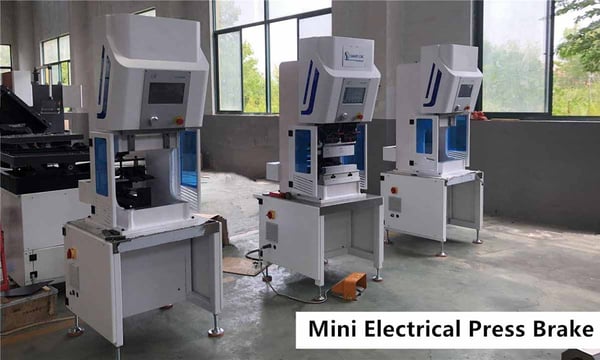
What is A Mini Press Brake
A mini press brake is a scaled-down version of a traditional press brake, specifically designed for precision bending of metal sheets and plates in smaller, more compact settings. Despite its reduced size, a mini press brake offers powerful bending capabilities, making it an essential tool for small workshops, DIY enthusiasts, and professionals who need to perform accurate bends on a smaller scale.
The mini press brake features a compact design with a small footprint, offering high speed and efficiency. It is equipped with advanced controllers from Delem, ESA, and Cybelec, ensuring precise and reliable operation.
This small bending machine utilizes a fully welded structure, with its main parts undergoing annealing treatment to release internal stress. Both the frame and ram are meticulously processed in a single pass using a heavy-duty boring and milling machine, guaranteeing exceptional accuracy and durability.
Features
- Can handle small batch and multi-variety production
- Have a low cost and long lifespan of bending dies
- Can produce complex shapes such as “S” and “Z” bends
- Are made of heavy-duty components that ensure durability and accuracy
- Can save energy, improve safety and reduce noise compared to larger hydraulic press brak
Applications
Small Workshops and Garages: Ideal for small-scale metalworking operations where space is limited, mini press brakes enable efficient bending of sheet metal and small parts.
Prototyping and R&D: Used in prototyping and research environments to quickly fabricate and test new designs without the need for large-scale production setups.
Custom Fabrication: They are employed in creating customized metal components and parts with precise dimensions and shapes, catering to specific customer requirements.
DIY and Hobbyist Projects: Popular among DIY enthusiasts and hobbyists for crafting metal objects and home improvement projects due to their ease of use and compact design.
Educational Institutions: Used in vocational training and educational programs to teach students metalworking techniques and principles of press brake operations.
Small-Batch Production: Suitable for manufacturing small batches of metal components where flexibility, quick setup, and efficient production are critical.
Maintenance and Repair Work: Employed in facilities for repairing and fabricating replacement parts for machinery and equipment, ensuring quick turnaround times and cost-effective solutions.
Electronics and Electrical Enclosures: Used in manufacturing electrical enclosures, panels, and components requiring precise bending of sheet metal for housing electronic equipment.
Automotive Industry: Applied in fabricating parts for vehicles, such as brackets, covers, and structural components that require accurate bending and fitment.
Artistic and Decorative Metalwork: Utilized by artisans and craftsmen for creating decorative metal pieces, sculptures, and artistic installations, leveraging the precision capabilities of mini press brakes.
Mini Press Brake: Small but Strong
The small press brake is a compact and versatile machine, easily moveable by forklift, and designed for bending small, complex parts as well as some larger-sized components when necessary. It can be driven by electric, hydraulic, or hybrid systems and can be fed manually or by robot. Modern models offer a wide range of options, including automatic tool changers, precision bending lasers, superior ergonomic features, and intuitive controllers.
At Fabtech 2016, numerous small press brakes were showcased, many of which featured electric or servo-driven technology. According to engineer of Krrass Machinery, the industry is increasingly favoring electric press brakes over traditional hydraulic systems for small part bending due to their speed. Electric press brakes typically operate faster, making them ideal for small parts.
Concurs, noting that the primary advantages of electric-drive technology are acceleration and speed potential. However, the benefits diminish with larger parts, where the weight and handling become the main challenges. Consequently, the required component sizes in production often guide buyers toward either electric or hydraulic-drive brakes.
In production environments, where the press brake supports other processes, speed is also crucial. Higher stroke rates enable press brakes to keep pace with upstream machines, such as lasers or punching machines, explains from Krrass Machinery expert.
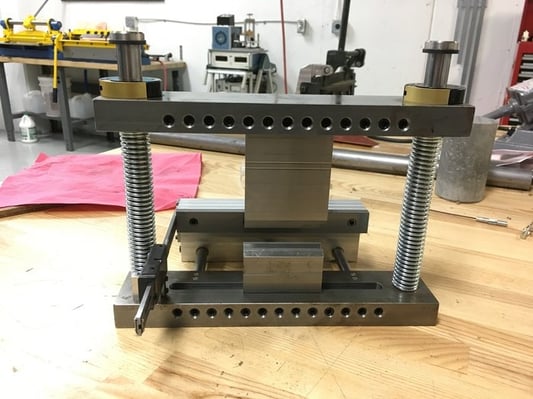
What 's Main Types of the Mini Press Brake
There are two primary types of Small Press Brakes: hydraulic and Electro-Hydraulic systems.
A small hydraulic press brake operates using oil cylinders to drive the bending process, with synchronization controlled by torsion bars positioned on both sides. This mechanism ensures that the upper and lower beams move up and down in a synchronized manner, maintaining precise alignment throughout the bending operation. Hydraulic press brakes are known for their robust performance and reliability in handling various bending tasks.
In contrast, an Electro-Hydraulic servo bending machine utilizes advanced servo proportional valves and a grating ruler for synchronization. This system integrates a separate CNC control unit dedicated to managing synchronization, ensuring the slider operates with pinpoint accuracy.
By continuously feeding back and adjusting data in real-time, Electro-Hydraulic servo bending machines achieve exceptional precision, making them ideal for applications requiring intricate and high-precision bending operations. This technology not only enhances operational efficiency but also allows for the customization and optimization of bending parameters to meet specific production requirements.
Advantages of Mini Type Over Lager Presses
Compact Size and Portability:
Mini press brakes typically occupy significantly less floor space than larger counterparts, with some models having a compact footprint as small as 1.5 meters by 1.5 meters. In contrast, large press brakes can require spaces exceeding 10 meters in length. This compact size enables mini press brakes to fit into smaller workshops or production areas, optimizing space utilization. Studies suggest that mini press brakes can reduce spatial requirements by up to 50% compared to traditional models, making them ideal for maximizing floor space efficiency in manufacturing environments.
Cost-Effectiveness:
Initial investment in a mini press brake is generally much lower compared to large press brakes. Mini press brakes can range in cost from $20,000 to $50,000 on average, whereas large press brakes often start at $100,000 and can exceed $1 million for high-capacity models. This significant cost difference makes mini press brakes more accessible to small and medium-sized enterprises looking to invest in bending equipment. Additionally, mini press brakes offer reduced operating costs due to their lower energy consumption. Their efficient design requires less power to operate, resulting in lower electricity bills over time and contributing to overall cost savings for manufacturers.
Versatility:
Despite their compact size, mini press brakes exhibit remarkable versatility in handling a diverse range of materials and thicknesses. These machines are capable of efficiently bending materials ranging from delicate 0.5 mm thin sheets to robust 6 mm thick plates, catering to a broad spectrum of manufacturing needs across different industries.
Their adaptability extends beyond material versatility to various sectors such as automotive, aerospace, and electronics. In these industries, mini press brakes play a crucial role in prototyping, custom fabrication, and small-batch production. Their ability to achieve precise bends with consistent quality makes them indispensable tools for manufacturers seeking flexibility and efficiency in their production processes.
Precision and Accuracy:
Advanced control systems like those offered by Delem, ESA, and Cybelec play a pivotal role in ensuring precise bending operations with minimal deviation. Mini press brakes equipped with these controllers can achieve angular accuracies within ±0.1 degrees, which is essential for maintaining consistent quality in metalworking projects.
Furthermore, Electro-Hydraulic mini press brakes leverage servo motors and digital feedback systems to enhance accuracy further. These systems enable real-time adjustment of bending parameters, ensuring that each bend meets exact specifications with high precision. This technological integration not only improves the overall quality of bends but also enhances the machine's efficiency and reliability in diverse manufacturing environments.
Efficiency:
Advanced control systems from Delem, ESA, and Cybelec ensure precise bending operations with minimal deviation in mini press brakes. These controllers enable angular accuracies within ±0.1 degrees, crucial for maintaining consistent quality in metalworking projects. Additionally, Electro-Hydraulic mini press brakes utilize servo motors and digital feedback systems to adjust bending parameters in real-time, further enhancing accuracy and ensuring that each bend meets exact specifications with high precision. This integrated technology improves overall efficiency and reliability, making mini press brakes suitable for a wide range of demanding manufacturing applications.
Adaptability
Mini press brakes provide remarkable flexibility in production environments by seamlessly integrating into existing workflows or operating alongside other equipment, thereby enhancing overall production flexibility. Their modular designs and optional accessories, such as tool changers and advanced safety systems, further enhance adaptability to diverse manufacturing needs and regulatory requirements. This adaptability ensures that mini press brakes can efficiently meet varying production demands while maintaining high standards of safety and operational efficiency across different industrial settings.

Small vs. Large Press Brakes: How to Choose?
Selecting the right press brake depends on your shop's specific needs and requirements. Opting for a small press brake may be ideal if your operations involve:
Handling Small, Complex Parts: Whether you're bending intricate components or larger-sized parts, a small press brake offers the precision and flexibility required for diverse bending tasks.
Ensuring Precision and Minimizing Waste: By bending metal with high accuracy, small press brakes help reduce material waste and eliminate rejections, ensuring efficient production processes.
Versatility Across Materials and Parts: Small press brakes can efficiently bend a wide range of materials and parts using a single set of punch and die, enhancing production versatility and reducing setup times.
Cost-Effective Die Management: They help save costs and extend the lifespan of bending dies, making them economical for businesses aiming to optimize operational expenses.
Capability to Produce Various Shapes: From standard bends to complex shapes like S, U, and polygons, small press brakes offer the capability to handle diverse bending requirements effectively.
Ease of Setup and Tooling: With straightforward setup procedures and adaptable tooling options, small press brakes enable quick adjustments between different bending applications, enhancing workflow efficiency.
Mobility and Accessibility: Their compact size allows for easy maneuverability using forklifts, facilitating operational flexibility and adaptability in dynamic manufacturing environments.
How to Biuld A Mini Press Brake
Materials and Tools Needed:
- Steel or aluminum for frame and components
- Hydraulic or pneumatic components (cylinders, valves)
- Bending die and punch
- Hydraulic or manual control system
- Welding equipment
- Cutting tools (saw, grinder)
- Measuring and marking tools (tape measure, square)
- Safety equipment (gloves, goggles)
Step-by-Step Guide:
Design and Planning:
Begin by designing the mini press brake, considering the size, capacity (maximum bending force and length), and intended use.
Plan the structure, including the frame, bending mechanism, and control system. Ensure the design includes safety features and adheres to safety standards.
Frame Construction:
Cut and weld steel or aluminum components to create the frame of the mini press brake. The frame should be sturdy and stable to withstand bending forces.
Ensure the frame is leveled and square to maintain accuracy during operation.
Bending Mechanism:
Install the bending die and punch mechanism. This includes mounting the die holder on the ram and securing the punch holder on the bed or table of the press brake.
Ensure proper alignment and clearance between the die and punch for efficient bending.
Hydraulic or Manual Control System:
If using a hydraulic system, install hydraulic cylinders, valves, and hoses according to the design specifications.
Ensure the control system allows for precise adjustment and control of bending operations.
Assembly and Integration:
Assemble all components together, including the frame, bending mechanism, and control system.
Test fit and adjust components as needed to ensure smooth operation and alignment.
Safety and Testing:
Install safety guards and emergency stop mechanisms to prevent accidents during operation.
Conduct thorough testing of the mini press brake to verify functionality, including bending accuracy and maximum capacity.
Perform safety checks to ensure all components are secure and operating correctly.
Fine-tuning and Calibration:
Fine-tune the control system and adjust settings for optimal bending performance.
Calibrate the bending mechanism to achieve precise bends according to the desired specifications.
Documentation and Maintenance:
Document the assembly process, including diagrams, component lists, and operational instructions.
Establish a maintenance schedule to ensure the mini press brake remains in good working condition, including regular lubrication and inspection of components.
Mini Press Brake Buying Guide
1. Understand Your Needs
Before diving into the features and specifications, it’s crucial to clearly define your requirements:
- Type of Material: Identify the types of metals you will be working with (e.g., aluminum, steel, stainless steel). Different materials have varying bending properties.
- Thickness of Material: Determine the maximum thickness of the materials you will be bending. Thicker materials require more force, influencing the choice of press brake.
- Production Volume: Consider whether you need the press brake for high-volume production or smaller, custom jobs. High-volume production may necessitate more automation and faster cycle times.
2. Types of Mini Press Brakes
Mini press brakes come in various types, each with its own set of advantages:
- Electric Press Brakes: These are known for their speed and precision, making them ideal for small, intricate parts. They are energy-efficient and provide consistent bending results.
- Hydraulic Press Brakes: Generally more powerful, these machines are suitable for a wider range of materials and thicknesses. They offer high tonnage and can handle heavy-duty bending tasks.
- Hybrid Press Brakes: Combining the benefits of both electric and hydraulic systems, hybrid press brakes offer versatility, efficiency, and reduced energy consumption.
3. Key Features to Consider
- Drive System: Choose between electric, hydraulic, or hybrid systems based on your specific speed, power, and efficiency requirements.
- Size and Portability: Ensure the machine fits your workspace and can be moved easily if necessary. Compact designs are beneficial for smaller workshops or production floors with limited space.
- Automation: Features like automatic tool changers and robot feeding can significantly increase efficiency, reduce setup times, and enhance precision.
- Precision: Look for models with lasers and intuitive controllers that offer high precision and ease of use. Advanced CNC controllers can simplify programming and improve accuracy.
- Ergonomics: Superior ergonomic options, such as adjustable work heights and user-friendly interfaces, can reduce operator fatigue and increase productivity.
4. Technical Specifications
- Tonnage: Determine the maximum tonnage required for your bending needs. This will depend on the material type and thickness.
- Bending Length: Ensure the machine can handle the maximum length of the parts you need to bend. Consider both the overall bending length and the length of individual bends.
- Stroke Rate: Higher stroke rates can improve productivity, especially in high-volume production settings. Faster cycle times mean more parts can be produced in less time.
5. Consider the Brand and Model
- Reputation: Opt for reputable brands known for reliability and quality, such as Amada, Trumpf, and LVD Strippit. Established brands often offer better customer support and more reliable machines.
- Reviews and Testimonials: Look for reviews from other users to gauge the performance, durability, and ease of use of the machine. User experiences can provide valuable insights into potential issues and benefits.
Conclusion
Investing in a mini press brake offers a range of compact solutions that deliver precision bending for small, complex parts and some larger components. By carefully considering your specific material needs, production volume, and desired features, you can select the right type of press brake—whether electric, hydraulic, or hybrid—that best suits your operations. Opting for reputable brands and models ensures reliability and quality, while advanced features like automation and ergonomic design can significantly enhance efficiency and ease of use.
