When it comes to investing in a panel bender machine, understanding the current market prices is crucial. The price of a panel bender machine can vary significantly based on several factors, including brand, features, and technological advancements. In today’s market, prospective buyers need to be well-informed about the different pricing tiers to make an educated purchase that fits their budget and meets their production needs. By examining the factors influencing panel bender machine prices and exploring the available options, businesses can ensure they are making a wise investment that balances cost with performance.
Brief Overview Of Modern Panel Bender
Modern panel benders represent a significant advancement in the field of metal fabrication, offering enhanced precision, efficiency, and versatility. These machines are designed to automate the bending process for metal sheets, providing consistent and accurate results with minimal manual intervention.
Key Features
Advanced CNC Control: Modern panel benders are equipped with sophisticated CNC (Computer Numerical Control) systems that allow for precise control over the bending process. This ensures high accuracy and repeatability, essential for complex and high-volume production tasks.
High Efficiency: The integration of automated feeding systems and quick tool-changing capabilities significantly reduces setup times and increases production speed. This efficiency is critical for meeting tight production schedules and reducing labor costs.
Versatility: These machines can handle a wide range of materials, including aluminum, stainless steel, and other metals, with varying thicknesses. This versatility makes them suitable for diverse applications, from automotive parts to household appliances.
User-Friendly Interface: Modern panel benders feature intuitive touch-screen interfaces and software that simplify programming and operation. This user-friendly design helps reduce the learning curve and improves overall productivity.
Energy Efficiency: Newer models are designed with energy-saving features that minimize power consumption, contributing to lower operational costs and a reduced environmental footprint.
Benefits:
- Precision and Accuracy: With advanced tooling and control systems, modern panel benders deliver precise bends, reducing material waste and ensuring high-quality output.
- Increased Productivity: Automation and efficient design enable higher throughput and consistent performance, allowing manufacturers to meet high production demands.
- Reduced Labor Costs: Automation reduces the need for manual labor, leading to lower labor costs and minimizing the risk of human error.
- Enhanced Safety: Modern panel benders are equipped with safety features such as light curtains, interlocks, and emergency stop buttons, ensuring a safer working environment.
Modern panel benders are indispensable tools in metal fabrication, combining precision, efficiency, and versatility to meet the demands of today’s manufacturing industry. With advanced features and robust performance, they offer significant advantages over traditional bending methods, making them a valuable investment for businesses aiming to enhance their production capabilities.
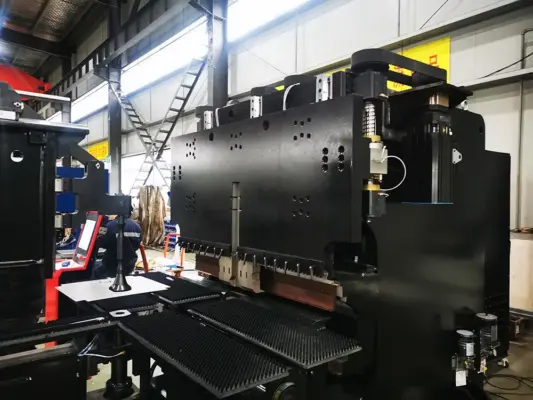
Importance in Today's Manufacturing
Today’s CNC bending machines are advancing rapidly in their application and flexibility, driven by developments in CNC systems, CAD, and CAPP technologies. These machines play a crucial role in the forming and processing of modern sheet metal parts, offering immense development potential and significant importance. As the machine tool industry evolves, CNC bending machines are poised to enhance production efficiency and contribute to industry progress.
With the advent of "Industry 4.0," the potential for growth in my country’s CNC bending machine tool industry is promising, particularly in the area of import substitution. According to the development prospect forecast report of China’s bending machine tool industry, most domestically applied bending machine tools are now produced within the country. This aligns with China’s strategic direction in manufacturing and processing, reinforcing its reputation as the "world factory." Consequently, China’s manufacturing and processing industry is compelled to innovate and adapt.
The CNC panel bender, a high-tech product specifically developed for the sheet metal industry, aims to boost production efficiency, reduce labor intensity, and enhance corporate image. This equipment offers several notable features:
- High Speed and Efficiency: CNC panel benders operate at high speeds, allowing for rapid prototyping of workpieces with exceptional consistency.
- Energy Efficiency: These machines consume low power, making them cost-effective and environmentally friendly.
- Ease of Maintenance: With simple maintenance requirements and low operational costs, CNC panel benders are designed for long-term reliability.
- High Automation: The high degree of automation simplifies operation, reducing labor requirements and enhancing productivity.
- Flexibility in Design: Without the need for tooling, complex shapes, including right angles and non-right angles, can be freely designed and produced at any time.
- Versatile Material Handling: CNC panel benders are compatible with a wide range of materials, including stainless steel, cold-rolled sheet, and aluminum sheet.
- Loading and Unloading Options: Various methods for loading and unloading are available, including manual, truss robot, and robotic arm options, catering to different production needs.
- Comprehensive Interfaces: These machines feature a wealth of software and hardware interfaces, making them compatible with conventional robotic arms on the market. The selection of specific robotic arms can be tailored to actual requirements.
- Advanced Control System: The control system supports true nine-axis (or 11-axis) concurrent linkage, ensuring smooth bending actions and highly coordinated mechanical operations.
- Protection Systems: Equipped with an eccentric load detection system, eccentric load follow-up system, and thick plate detection system, CNC panel benders effectively protect the machine and workpieces, reducing waste.
- Cloud-Based Management: The cloud operation and maintenance management system allows for real-time monitoring of the machine's operation, enhancing maintenance efficiency.
- User-Friendly Interface: Featuring a friendly human-machine interface, these machines are easy to understand and program flexibly.
- Dimensional Accuracy: For workpieces with non-standard dimensions, different positioning datums can be selected based on the workpiece shape. The shearing error of the sheet is controlled on the first bending edge to ensure dimensional accuracy after forming.
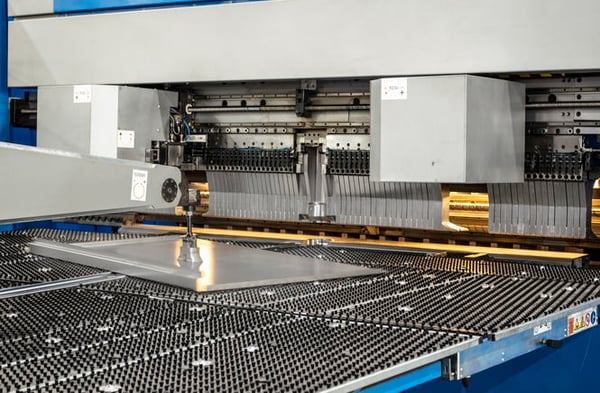
Exploring the Panel Bender Machine Price Range in 2024
The price range of panel bender machines varies significantly based on multiple factors such as brand, features, technology, and production capabilities. Here’s a detailed look at what to expect when budgeting for a panel bender in 2024:
Entry-Level Machines
- Price Range: $50,000 to $100,000
- Key Features:
- Basic CNC control systems
- Limited automation features
- Suitable for small to medium-sized production runs
- Compatible with standard materials and moderate thicknesses
- Ideal For: Small businesses and startups looking to enhance production capabilities without significant investment.
Mid-Range Machines
- Price Range: $100,000 to $250,000
- Key Features:
- Advanced CNC control systems with multi-axis capabilities
- Higher levels of automation, such as automatic tool changers
- Better integration with CAD/CAM software
- Enhanced safety features and improved energy efficiency
- Ideal For: Medium-sized businesses that require higher production volumes and more complex bending operations.
High-End Machines
- Price Range: $250,000 to $500,000+
- Key Features:
- State-of-the-art CNC control systems with real-time monitoring and cloud-based management
- Full automation including robotic integration for loading and unloading
- Capable of handling a wide range of materials and thicknesses with exceptional precision
- Extensive safety features and user-friendly interfaces
- Robust after-sales support and comprehensive warranties
- Ideal For: Large manufacturing facilities and industries with high production demands, such as automotive, aerospace, and large-scale metal fabrication.
Influential Brands and Their Offerings
Trumpf
- Popular Models: TruBend Series 7000
- Pros: High precision, robust build quality, excellent customer support
- Cons: Higher initial investment
- Price Range: $300,000 to $450,000
Amada
- Popular Models: HG-ATC Series
- Pros: Advanced automation, high-speed operations, energy-efficient
- Cons: Requires specialized training for operators
- Price Range: $250,000 to $400,000
Krrass
- Popular Models: PBE Series
- Pros: Competitive pricing, reliable performance, extensive customization options
- Cons: Limited global service centers
- Price Range: $150,000 to $350,000
Salvagnini
- Popular Models: P4lean Series
- Pros: High level of automation, excellent flexibility, suitable for high-mix, low-volume production
- Cons: Higher cost of ownership due to advanced features
- Price Range: $300,000 to $500,000+
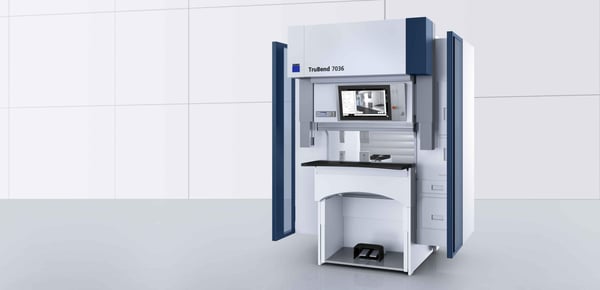
Factors Impacting Panel Bender Prices in 2024
Technological Advancements:
Integration of Industry 4.0 Technologies: Panel bender machines are increasingly incorporating Industry 4.0 principles, such as IoT (Internet of Things) connectivity, data analytics, and AI-driven control systems. These advancements enhance machine capabilities, improve efficiency, and enable predictive maintenance, leading to higher initial costs but significant long-term operational benefits.
Smart Manufacturing Solutions: AI-driven algorithms optimize bending processes, reducing setup times, minimizing material waste, and enhancing overall productivity. The integration of such technologies demands sophisticated hardware and software, contributing to the overall cost of the machine.
Material Costs:
Impact of Material Quality: The quality and type of materials used in constructing panel bender machines directly influence their pricing. High-strength steel, durable alloys, and advanced composite materials enhance machine durability, precision, and performance but also raise manufacturing costs. Fluctuations in material prices due to global market conditions can affect the final pricing of panel bender machines.
Customization Requirements:
Tailoring to Specific Production Needs: Industries requiring specialized bending capabilities, unique tooling configurations, or specific software integrations may incur additional costs. Customization ensures that machines meet exact production specifications, whether for complex geometries, varied material thicknesses, or specialized finishing requirements.
Software Integration: Customized CAD/CAM software for programming and simulation enhances precision and flexibility. The development and integration of such software tailored to specific industry requirements can add to the base price of panel bender machines.
Global Supply Chain Dynamics:
Supply Chain Disruptions: Disruptions in the global supply chain, such as shortages or delays in critical components (e.g., motors, sensors, hydraulic systems), impact manufacturing lead times and increase costs. Supply chain resilience and alternative sourcing strategies become crucial in mitigating these risks and maintaining stable pricing.
Localization and Regional Factors: Regional economic policies, tariffs, and local manufacturing capabilities influence the availability and cost of panel bender components. Strategic sourcing decisions and partnerships with reliable suppliers mitigate risks associated with global supply chain dynamics.
Tips for Getting the Best Panel Bender Machine Price
Research and Compare
When shopping for a panel bender machine, it's crucial to explore multiple suppliers and manufacturers to compare prices, features, and after-sales services. Online platforms, trade shows, and industry forums offer valuable insights into current market offerings. Request detailed quotes from different suppliers, including KRRASS, specifying your machine specifications, customization options, and delivery terms.
Use these quotes to negotiate competitive pricing and favorable terms that align with your business needs and budget. This proactive approach ensures you make an informed decision while securing the best possible deal on your panel bender purchase.
Timing and Negotiation
Take advantage of sales promotions and discounts offered by many suppliers during specific times of the year or trade events. Monitor industry news and promotional calendars to capitalize on these opportunities.
Additionally, negotiate with suppliers on pricing, especially when purchasing multiple units or bundling with other equipment. Discuss payment terms, warranties, and after-sales support to optimize the overall deal and ensure it meets your business requirements and budget. This strategic approach helps you maximize savings while securing a panel bender machine that fits your needs..
Consider Total Cost of Ownership
Beyond initial purchase price, consider factors like installation, training, maintenance, and operational costs. Opt for suppliers offering comprehensive service packages or extended warranties that may offset higher upfront costs.
Summary
In conclusion, understanding panel bender machine prices in today's market requires careful consideration of various factors such as brand reputation, technological advancements, and customization options. By staying informed about current industry trends and leveraging opportunities like sales promotions, businesses can make informed decisions.
Whether you're looking for competitive pricing or comprehensive after-sales support, reputable brands like KRRASS offer a range of solutions to meet diverse production needs. Stay proactive and research-driven to navigate the panel bender market effectively, ensuring a smart investment for your operations.
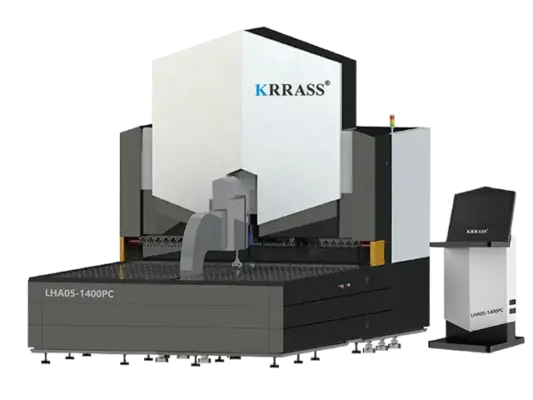