The sheet metal cutting machine has revolutionized the manufacturing industry, offering unparalleled precision and efficiency in cutting various types of metal sheets. These machines, equipped with advanced technology, are essential for producing high-quality components used in automotive, aerospace, construction, and many other industries. By leveraging automation and computer numerical control (CNC), sheet metal cutting machines ensure accuracy, reduce material waste, and significantly speed up production processes.
This article aims to explore the different types of sheet metal cutting machines available today, their technological advancements, and their applications across various industries. By understanding the capabilities and benefits of each type of cutting machine, businesses can make informed decisions to enhance their production processes and achieve higher efficiency and quality in their operations.
What Is Sheet Metal Cutting
Sheet metal cutting is a crucial process in the metalworking industry, involving the precise removal of material from sheet metal stock to create specific parts or components. This process is vital for shaping metal sheets into finished products, using various tools and techniques to ensure accuracy and efficiency.
At its core, sheet metal cutting transforms flat metal sheets into diverse shapes and sizes tailored to meet specific requirements. Whether working with thin aluminum or sturdy steel, understanding the nuances of cutting sheet metal is essential for achieving the desired results.
Cutting methods range from simple tools like tin snips for basic cuts to advanced technologies such as laser cutting for intricate profiles and varying sheet thicknesses. Each method offers unique advantages and is selected based on the project's specific needs.
The essence of sheet metal cutting lies in precision and control. Exploring this process reveals various techniques, each with its own applications and benefits. From straight lines to curved cuts and intricate patterns, the art of cutting sheet metal involves turning a raw, flat metal sheet into a functional and visually appealing product.
Evolution of Metal Cutting Technology
The journey of sheet metal cutting spans centuries, evolving from simple hand tools to sophisticated machinery. Originally, craftsmen relied on basic tools like chisels and hammers to shape metal sheets, a labor-intensive process requiring significant skill and effort. As industries progressed, so did the techniques for cutting sheet metal. The Industrial Revolution marked a pivotal period, introducing power tools and machines that could handle larger pieces of metal with greater precision and efficiency.
A significant milestone was the introduction of the shearing process, where an upper blade and a lower blade precisely cut the metal. This innovation significantly enhanced the efficiency and capabilities of metalworking. The 20th century brought further advancements, including plasma cutting and laser cutting, which revolutionized metal cutting with increased speed, precision, and the ability to cut through thicker materials. The advent of CNC (Computer Numerical Control) technology further transformed sheet metal cutting, enabling highly precise and automated operations.
Exploring the history of sheet metal cutting reveals that each advancement was driven by the need for greater precision, efficiency, and versatility in handling various metals and thicknesses. The evolution from manual to automated processes reflects the broader progress of technology and industry, showcasing human ingenuity in manufacturing.
Introduction To Sheet Metal Cutting Process
Understanding the sheet metal cutting process is crucial for anyone involved in fabrication or metalworking. It begins with selecting the appropriate sheet metal material and determining the desired shape and size for the final product. Once the metal sheet is prepared, the cutting process commences, employing various methods based on the project’s requirements. Common techniques include shearing, laser cutting, water jet cutting, and plasma cutting. Each method has its unique mechanism but shares the goal of removing excess material to achieve the desired shape.
Several factors, such as sheet thickness, cutting speed, and the type of metal, influence the choice of cutting method and the settings of the cutting tool or machine. For instance, thicker sheets might require more powerful methods like plasma cutting, while thinner sheets can be effectively cut with tin snips or a circular saw. Precision and accuracy are paramount throughout the cutting process, achieved through careful planning, proper tool selection, and skilled execution. Whether cutting straight lines, forming curved shapes, or creating complex patterns, success in sheet metal cutting lies in meticulous attention to detail and a deep understanding of the materials and tools involved.
Types of Sheet Metal Cutting Process
Sheet metal cutting, a critical process in the fabrication industry, involves several methods, each tailored to different needs and material types. The choice of method significantly influences the quality, efficiency, and cost-effectiveness of the final product. As you explore this field, understanding the different sheet metal cutting operations becomes vital, whether you are working on a small DIY project or a large industrial task.
1.Shearing
Shearing is a widely used technique in sheet metal cutting, known for its simplicity and efficiency. This process involves two sharp blades, typically made of high-grade tool steel, positioned one above the other. The upper blade descends to cut the metal sheet placed below, shearing it with precision and minimal waste.
- Applications of Shearing in Sheet Metal Cutting:
- Ideal for making straight-line cuts on flat sheet metal.
- Commonly used in mass production due to its speed and efficiency.
- Suitable for cutting metal sheets of varying thicknesses, though typically used for thinner materials.
- Often employed in preliminary shaping of metal before it undergoes further processing.
2.Laser Cutting
Laser cutting stands out for its precision and versatility. This method uses a high-powered laser focused onto the sheet metal, melting, burning, or vaporizing the material along the desired cut line. Laser cutting machines are typically controlled by CNC systems, allowing for intricate patterns and shapes.
- Applications of Laser Cutting in Sheet Metal Cutting:
- Produces highly accurate and clean cuts, perfect for detailed designs.
- Capable of cutting through various metal types and thicknesses, including steel, aluminum, and titanium.
- Frequently used in industries requiring high precision, such as aerospace and automotive manufacturing.
- Offers flexibility in cutting complex shapes and small, intricate parts.
What Are Main Types of Laser Cutters For Metal Cutting
Laser cutters vary in type, primarily based on the laser source they use. Each type has its distinct advantages and applications.
Fiber Laser Cutters
Fiber laser cutters use a solid-state laser made from a ‘seed’ laser and amplified through special fibers. This technology is known for its energy efficiency, cutting speed, and quality.
- Key Features of Fiber Laser Cutters:
- Exceptional precision, ideal for detailed and intricate cuts.
- High cutting speed, significantly faster than traditional CO2 lasers.
- Energy-efficient, reducing operational costs.
- Versatile in cutting reflective metals like aluminum and copper without back reflections.
CO2 Laser Cutters
CO2 laser cutters, using a gas laser, are among the most common types of laser cutters in the industry. They are versatile and capable of cutting a wide range of materials.
- Key Features of CO2 Laser Cutters:
- Suitable for cutting thicker metal sheets.
- Offers a smooth finish, especially on thicker materials.
- Versatile in handling various materials beyond metals, including plastics and wood.
- Generally more cost-effective in terms of initial investment compared to fiber lasers.
3.Water Jet Cutting
Water jet cutting is a versatile and powerful sheet metal cutting operation that uses a high-pressure stream of water, often mixed with abrasive materials, to cut through metal. This technique is known for its precision and ability to cut a wide range of materials.
- Applications of Water Jet Cutting in Sheet Metal Cutting:
- Ideal for materials sensitive to high temperatures, as it doesn’t generate heat.
- Capable of cutting complex shapes with high precision.
- Suitable for a variety of materials, including metals, glass, and composites.
- Often used for projects requiring minimal material distortion and no heat-affected zone.
4.Plasma Cutting
Plasma cutting is a process that employs a plasma torch to cut through electrically conductive materials like steel, stainless steel, and aluminum. This method is favored for its speed and ability to cut thick materials.
- Applications of Plasma Cutting in Sheet Metal Cutting:
- Efficient for cutting thick metal sheets and plates.
- Used extensively in heavy fabrication, automotive, and industrial applications.
- Capable of producing relatively clean cuts with a small heat-affected zone.
- Ideal for large-scale projects where speed is a critical factor.
5.Punching
Punching, a common sheet metal cutting operation, involves the use of a punch and die to create holes or cut out shapes from the metal sheet. Punching operation is highly efficient for creating repetitive patterns or shapes.
- Applications of Punching in Sheet Metal Cutting:
- Commonly used for creating holes, slots, or shapes in metal sheets.
- Essential in mass production for consistent and rapid production of parts.
- Often combined with other processes like bending or forming.
- Suitable for a range of materials, with varying thicknesses.
6.Blanking
Blanking is a sheet metal cutting process where a punch and die are used to cut out a piece from the main sheet, known as a blank. This method is known for its precision and repeatability.
- Applications of Blanking in Sheet Metal Cutting:
- Ideal for producing flat, uniform parts in large quantities.
- Frequently used in the automotive and appliance industries.
- Allows for tight tolerances and clean edges.
- Efficient for processing a variety of metal types and thicknesses.
What Are Commonly Used Sheet Metal Cutting Machines
Mechanical Cutting Machines
- Shearing Machines: Utilize upper and lower blades to cut metal sheets. Suitable for straight cuts and relatively thick sheets.
- Punch Presses: Use a punch and die to create shapes in metal by cutting out sections.
Thermal Cutting Machines
- Laser Cutting Machines: Employ a focused laser beam to melt and cut the metal. Ideal for precise and intricate cuts, suitable for various thicknesses.
- Plasma Cutting Machines: Use a jet of ionized gas (plasma) to cut through electrically conductive materials. Effective for cutting thick sheets and metals like steel and aluminum.
- Oxy-Fuel Cutting Machines: Utilize a combination of oxygen and fuel gases to cut through thick metal sheets. Commonly used for cutting steel.
Water Jet Cutting Machines
- Water Jet Cutters: Utilize high-pressure water, sometimes mixed with abrasive materials, to cut through metal. Suitable for cutting without generating heat, which is beneficial for materials sensitive to high temperatures.
CNC Cutting Machines
- CNC Routers: Computer-controlled machines that use various cutting tools to shape metal sheets. Provide high precision and can handle complex designs.
- CNC Laser Cutters: Similar to standard laser cutters but with enhanced precision and automation capabilities, allowing for intricate and repeatable cuts.
Specialized Cutting Machines
- Band Saws: Use a continuous band of toothed metal to cut through metal sheets. Suitable for straight and curved cuts.
- Tin Snips and Handheld Shears: Manual tools used for cutting thin metal sheets. Ideal for small-scale or detailed work.
Is Sheet Metal Cutting Machine Expensive
The cost of a sheet metal cutting machine can vary widely depending on several factors, including the type of machine, its features, brand, and capacity. Here's a general overview of the price ranges for different types of sheet metal cutting machines:
Mechanical Cutting Machines
- Shearing Machines: Basic manual or hydraulic shearing machines can range from a few thousand dollars to over $20,000 for larger, more advanced models.
- Punch Presses: Smaller, manual punch presses might cost a few thousand dollars, while larger, automated CNC punch presses can range from $50,000 to over $200,000.
Thermal Cutting Machines
- Laser Cutting Machines: Entry-level laser cutters for small-scale operations might start around $20,000 to $50,000. High-end industrial laser cutting machines, especially those with advanced features and higher power, can exceed $500,000.
- Plasma Cutting Machines: Basic plasma cutters can start around $10,000 to $20,000. Advanced CNC plasma cutting systems can range from $50,000 to over $200,000, depending on the cutting capacity and precision.
- Oxy-Fuel Cutting Machines: These are generally more affordable, with prices ranging from a few thousand dollars for basic setups to around $50,000 for more advanced systems.
Water Jet Cutting Machines
- Water Jet Cutters: These machines can be quite expensive due to their advanced technology. Prices typically start around $50,000 for basic models and can exceed $200,000 for high-end, high-precision systems.
CNC Cutting Machines
- CNC Routers: Prices can range from $10,000 for small, basic models to over $100,000 for large, highly automated systems.
- CNC Laser Cutters: Similar to standard laser cutters but typically more expensive due to the added precision and automation, with prices ranging from $50,000 to several hundred thousand dollars.
Specialized Cutting Machines
- Band Saws: These are generally more affordable, with prices ranging from a few hundred dollars for small manual saws to $20,000 or more for large industrial models.
- Tin Snips and Handheld Shears: These are the least expensive, typically costing less than $100.
Factors Affecting Cost
- Size and Capacity: Larger machines with higher cutting capacities are generally more expensive.
- Automation and CNC Capabilities: Machines with advanced automation and CNC controls are typically more costly.
- Precision and Features: Higher precision, faster cutting speeds, and additional features like material handling systems increase the cost.
- Brand and Quality: Well-known brands and high-quality machines tend to be more expensive but offer better reliability and support.
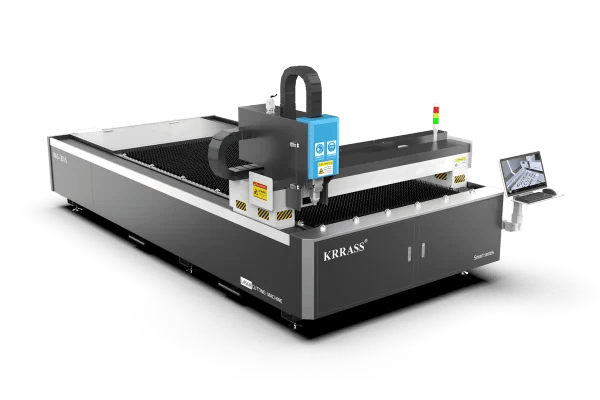
What Are Sheet Metal Cutting Machine Used For
1. Automotive Industry
- Manufacturing Car Components: Cutting and shaping metal sheets for body panels, chassis parts, brackets, and other structural components.
- Prototyping: Creating prototypes for new vehicle models or components.
2. Aerospace Industry
- Aircraft Parts: Cutting high-precision components for aircraft, such as fuselage panels, wings, and support structures.
- Engine Components: Fabricating parts for engines and turbines.
3. Construction Industry
- Building Components: Producing metal roofing, siding, and structural elements like beams and columns.
- HVAC Systems: Cutting and shaping ducts, vents, and other HVAC components.
4. Electronics and Electrical Industry
- Enclosures and Casings: Creating enclosures for electronic devices, control panels, and electrical cabinets.
- Heat Sinks and Circuit Boards: Fabricating heat sinks and cutting circuit boards from metal sheets.
5. Furniture and Appliance Manufacturing
- Metal Furniture: Cutting metal sheets for frames, legs, and decorative elements in furniture.
- Appliances: Manufacturing parts for appliances like refrigerators, ovens, and washing machines.
6. Medical Equipment
- Surgical Instruments: Producing precision parts for surgical instruments and medical devices.
- Equipment Casings: Fabricating enclosures for medical equipment and machinery.
7. Signage and Advertising
- Signboards: Cutting and shaping metal sheets for signboards, billboards, and display stands.
- Decorative Elements: Creating custom metal designs for advertising and branding purposes.
8. Industrial Machinery
- Machine Parts: Fabricating parts for industrial machines, including gears, housings, and support structures.
- Tooling and Fixtures: Creating custom tools and fixtures for manufacturing processes.
9. Art and Sculpture
- Metal Art: Cutting and shaping metal sheets for sculptures, decorative panels, and artistic installations.
10. Shipbuilding
- Hull Construction: Cutting and shaping large metal sheets for the hull and superstructure of ships.
- Marine Components: Fabricating parts for marine equipment and structures.
11. Renewable Energy
- Wind Turbines: Producing parts for wind turbine blades and towers.
- Solar Panels: Cutting frames and supports for solar panel installations.
Main Parameters of Sheet Metal Cutting Machine
In the intricate process of sheet metal cutting, several key parameters play crucial roles in determining the quality, efficiency, and feasibility of the operation. Understanding these parameters is essential for achieving optimal results in your metalworking projects.
- Material Thickness:
- Dictates the amount of force or energy required for cutting.
- Influences the choice of cutting method and tooling.
- Thicker materials often necessitate more robust cutting techniques like plasma or laser cutting.
- Cutting Speed:
- Refers to the rate at which the cutting tool or laser moves across the material.
- A critical factor affecting both productivity and cut quality.
- Optimal speed varies depending on the material type and thickness.
- Power Output (for Laser/Plasma Cutting):
- The power setting of the machine, crucial for effectively cutting through different material thicknesses and types.
- Higher power output is typically required for thicker, harder materials.
- Kerf Width:
- The width of the cut or the amount of material removed during the cutting process.
- Kerf affects the final dimensions of the sheet metal part and overall precision.
- Narrower kerfs lead to more material conservation and less waste.
- Cutting Tolerances:
- Refers to the allowable deviation in the cut dimensions, which is crucial for precision manufacturing.
- Tighter tolerances are often required in high-precision industries.
- Surface Finish:
- The quality of the surface post-cutting, which can vary based on the cutting method.
- A smoother finish is often desirable for aesthetic and functional purposes.
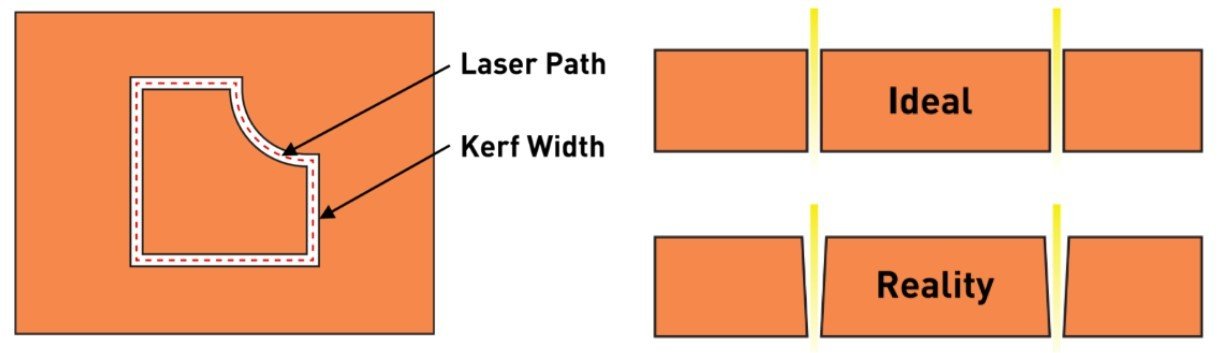
How To Choose A Right Sheet Metal Cutting Machine
To cut metals, you can choose between laser cutting, plasma cutting, electrical discharge machining and oxyacetylene cutting, etc. For rigid materials, metallic or otherwise, you can turn to water-jet cutting which allows you to cut thick materials. If you need to cut softer materials such as fabric, leather, soft plastic, paper or cardboard, you might be interested in knife cutting.
You will find a table below summarizing the compatibility of the different types of technology with the main industrial materials:
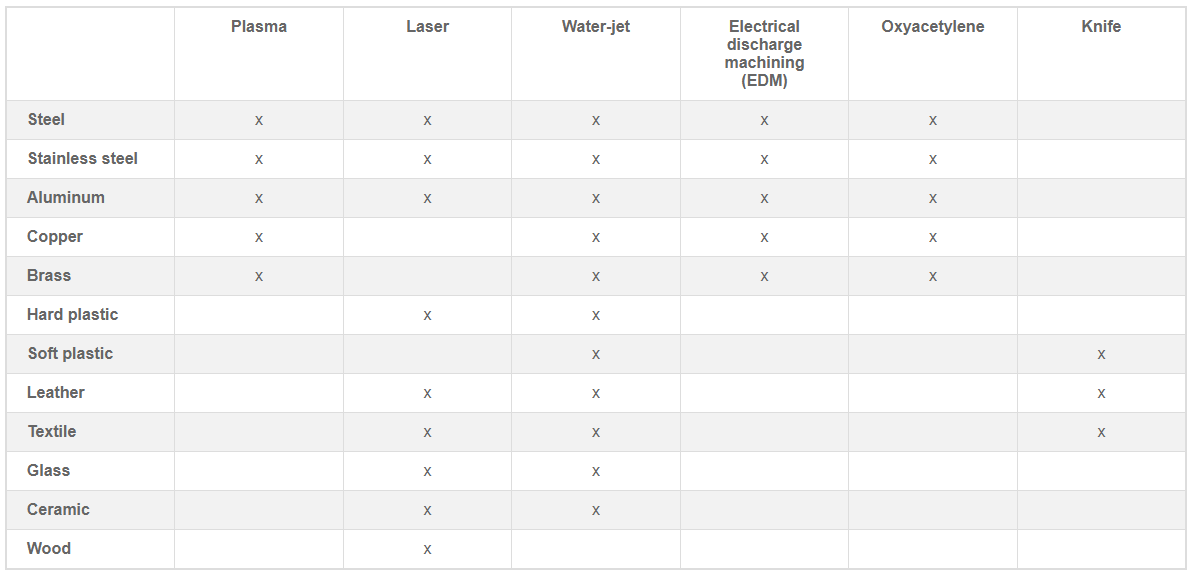
When Should You Choose A Laser Cutter
Laser cutting machines use the heat emitted by a laser beam guided by mirrors or optical fibers. Depending on the type of laser, you can cut different types of materials.
- CO2 laser cutting machines are generally used for cutting plastic, foam, wood, glass, textile or soft steel. A CO2 laser cannot cut reflective metals such as copper or brass.
- The more powerful fiber laser cutting machines are reserved for cutting sheet metal, steel, stainless steel, aluminum and some plastics.
Laser cutting allows you to cut different materials without having to change tools, simply by setting the laser parameters. It is a very precise process, with a very small notch width allowing for complex contours. Depending on the material to be cut, the cutting speed can be very fast. Laser cutting machines are fully automated and require very little human intervention, which greatly limits the risk of accidents.
The main limitation of laser cutting is its shallow cutting depth of around 25 millimeters. As a result, the main applications of laser cutting are the manufacture of sheet metal (especially for the automotive industry) and frames (for electrical cabinets, computers, etc.). For workpieces thicker than 25 mm, plasma cutting is the most suitable method. The area heated by the laser beam is not very large, but since it is subject to a strong temperature increase, it can become highly deformed.
Laser cutting produces gaseous emissions, so it is important to ensure that the room in which the machine is located is well ventilated.
When Should You Choose A Plasma Cutting Machine
Plasma cutting machines are specifically designed for cutting ferrous metals (such as steel and stainless steel) and non-ferrous metals (including brass, copper, and aluminum) with a maximum thickness of 160 mm. Plasma cutting excels in speed, particularly for medium or thick plates, surpassing laser cutting, and is faster than oxyacetylene cutting for thin or medium plates. Overall, plasma cutting is most suitable for cutting thick metal plates.
The principle behind plasma cutting is somewhat similar to TIG welding. It involves creating an electric arc that ionizes a gas, which is then projected through a nozzle between the electrode and the workpiece to be cut. Common gases used in plasma cutting include air, argon, nitrogen, oxygen, and hydrogen. Regardless of the gas used, it is necessary to regularly replace the nozzle and electrode to maintain optimal performance.
Portable plasma cutting machines are available for spot applications, providing flexibility for various tasks. Due to the significant heat generated and the fumes produced from vaporized metal, plasma cutting must be conducted in very well-ventilated areas or outdoors to ensure safety.
When Should You Choose A Water-jet Cutting Machine
Water-jet cutting machines utilize high-pressure water to cut through various materials, excluding tempered glass which would shatter under the pressure. These machines are capable of cutting materials up to 600 mm thick, but for optimal speed and precision, it is recommended to limit the thickness to 200 mm. For cutting soft materials, pure water can be used, extending the tool life due to the absence of abrasives. Harder materials, on the other hand, require a water and abrasive mixture for effective cutting.
One of the advantages of water-jet cutting is that it does not cause deformation in the workpiece since there is no heat involved, resulting in smooth and shiny cut edges. However, the process is quite noisy. While cutting in a straight line can be relatively quick, the speed decreases significantly when the cutting path changes direction. Although investing in a water-jet cutting machine represents a significant expense, it is generally more affordable compared to laser cutting machines.
When Should You Choose A Knife Cutting Machine
A knife cutting machine is designed to cut soft materials like fabric, leather, and vinyl, with thicknesses up to 50 mm. For thicker materials, a water-jet cutting machine is a better choice. This cutting technique offers high-precision results, though it necessitates regular replacement of the knife to maintain accuracy. Knife cutting machines are also commonly used for packaging materials, including paper and cardboard.
Conclusion
The future of sheet metal cutting machines looks incredibly promising, driven by advancements in technology and increasing demands for precision and efficiency in various industries. Innovations in automation, AI integration, and smart manufacturing are set to revolutionize the way we approach metal cutting, making processes faster, more accurate, and highly customizable.
KRRASS, a leading name in the industry, is at the forefront of this evolution. Their product line showcases cutting-edge technology designed to meet the diverse needs of modern manufacturers. From high-precision laser cutting machines to robust hydraulic shears, KRRASS offers solutions that enhance productivity and ensure top-notch quality.