In modern manufacturing, the CNC sheet metal brake has become an essential tool for metal forming and processing. Whether you're an experienced engineer or a newcomer to the sheet metal industry, understanding and mastering CNC technology is crucial for enhancing production efficiency and product quality. This ultimate guide will take you through every aspect of CNC sheet metal brakes, from basic principles to advanced applications, helping you gain comprehensive knowledge of this important equipment.
Introduction
Definition and Purpose of a CNC Sheet Metal Brake
A CNC sheet metal brake is a machine tool used for bending sheet metal with high precision and efficiency. CNC stands for "Computer Numerical Control," which means the machine is operated through programmed instructions encoded into software. This advanced control system allows for automated, accurate, and repeatable bending processes, making CNC sheet metal brakes essential for producing complex and consistent metal components.
The primary purpose of a CNC sheet metal brake is to form sheet metal into various shapes by exerting force along a straight axis. It is widely used in manufacturing industries to create parts for automotive, aerospace, electronics, and construction sectors, among others. The machine's ability to handle a variety of materials and thicknesses with minimal manual intervention makes it indispensable in modern production environments.
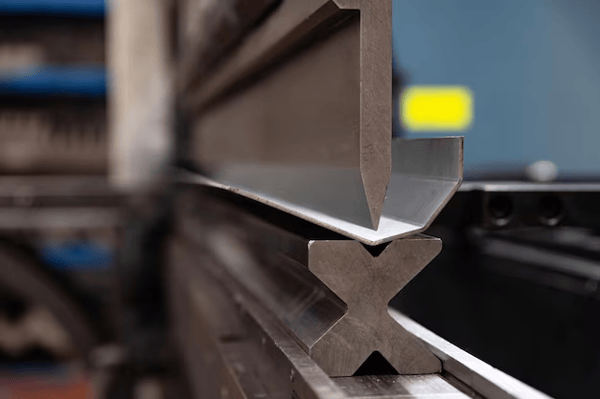
Importance in Modern Manufacturing
In today's competitive manufacturing landscape, precision, efficiency, and consistency are paramount. The CNC sheet metal brake plays a crucial role in meeting these demands. Here are some key reasons why this technology is vital in modern manufacturing:
High Precision and Accuracy: CNC sheet metal brakes offer unmatched precision, allowing manufacturers to produce parts with tight tolerances and intricate designs. This accuracy is essential for industries where the slightest deviation can lead to product failure or safety issues.
Increased Efficiency and Productivity: Automation through CNC technology reduces the need for manual intervention, significantly speeding up the production process. This efficiency leads to higher output rates and shorter lead times, enabling manufacturers to meet tight deadlines and high-volume demands.
Consistency and Repeatability: CNC sheet metal brakes ensure that each bend is executed with the same precision every time, resulting in consistent quality across all produced parts. This repeatability is critical for maintaining product standards and reducing waste due to errors.
Flexibility and Versatility: These machines can be programmed to perform a wide range of bending operations on different materials and thicknesses, making them versatile tools for various applications. This flexibility allows manufacturers to adapt to changing market demands and produce customized solutions.
Cost-Effectiveness: While the initial investment in a CNC sheet metal brake may be high, the long-term benefits include reduced labor costs, minimized material waste, and lower error rates. These advantages translate into significant cost savings over time.
How CNC Sheet Metal Brakes Improve Accuracy and Consistency in Bending
Precision in Bending
Numerical Control Precision: CNC sheet metal brakes operate with high numerical control precision, often achieving bending accuracies within ±0.1 degrees. This level of precision is critical for industries requiring tight tolerances, such as aerospace and electronics.
Material Specific Algorithms: Advanced CNC systems utilize material-specific bending algorithms that optimize bending parameters based on the material's elasticity, thickness, and tensile strength. For instance, these algorithms adjust bending speed and force dynamically to minimize springback.
Tooling and Setup: CNC brakes feature automatic tool changers and tool libraries that store precise settings for different tooling setups. This capability reduces setup time significantly and ensures consistent results across multiple production batches.
Consistency in Production
Automated Bending Sequences: CNC machines execute automated bending sequences with minimal operator intervention. This automation reduces human error and ensures that each part is bent identically, maintaining consistency throughout production runs.
Statistical Process Control (SPC): Many modern CNC systems integrate SPC functionalities that monitor key bending parameters in real-time. Operators can analyze data trends and make adjustments to maintain consistent quality levels and meet strict production standards.
Data-Driven Quality Assurance: CNC brakes can generate comprehensive bend reports and quality logs automatically. These reports detail parameters such as bend angles, force applied, and material position, providing traceability and aiding in quality assurance audits.
Advantages of Using a CNC Sheet Metal Brake
Reducing Waste
CNC sheet metal brakes offer exceptional precision in metal bending, which significantly reduces waste and rejections. The automated control ensures each bend is accurate, minimizing material scrap and enhancing overall efficiency. This precision is particularly beneficial for high-volume production, where even minor errors can lead to substantial material waste and increased costs.
Smart Technology
Modern CNC sheet metal brakes represent a leap in automation and intelligence within the manufacturing industry. These machines utilize advanced software and sensors to automate the bending process, making them a "smart" technology. This automation not only improves accuracy but also allows for real-time adjustments and monitoring, ensuring optimal performance and quality.
Faster Production
The integration of CNC technology in sheet metal brakes accelerates the production process by combining automated operations with reduced defect rates. This results in shorter cycle times and higher throughput, enabling manufacturers to meet tight deadlines and increase their production capacity without compromising quality.
Easy Operation
One of the significant advantages of CNC sheet metal brakes is their ease of operation. Unlike other complex machinery that requires highly skilled operators, these machines are user-friendly and can be operated with minimal training. The intuitive interfaces and automated features simplify the bending process, making it accessible to a broader range of operators.
Improved Safety
Modern CNC sheet metal brakes come equipped with various safety features, such as laser sensors, that enhance operator safety. These sensors can detect when an operator is in harm's way and immediately halt the bending operation, preventing accidents and injuries. The improved safety measures contribute to a safer working environment and reduce the risk of workplace incidents.
In-House Manufacturing
Traditionally, metal fabrication workshops often outsourced the bending process to third parties. However, with the affordability and efficiency of modern CNC sheet metal brakes, many workshops can now perform the entire manufacturing process in-house. This shift not only reduces outsourcing costs but also provides greater control over production quality and timelines.
Programming
One of the standout features of CNC sheet metal brakes is their programmable nature. Operators can easily make adjustments to the setup using programming, without the need for manual intervention. This flexibility allows for quick changes to bending operations, enhancing productivity and enabling the efficient production of customized parts.
Complex Bends
CNC sheet metal brakes are designed to handle complex bending tasks with ease. By using different types of dies and advanced programming, these machines can create intricate bends, such as cones and other non-standard shapes. This capability expands the range of possible applications and allows manufacturers to produce more complex and detailed components.
Seamless Workflow
CNC sheet metal brakes can be seamlessly integrated into the assembly line of a metal fabrication workshop. Their compatibility with other automated systems and machinery ensures a smooth and continuous workflow, enhancing overall production efficiency and reducing downtime. This seamless integration is crucial for maintaining a high level of productivity in modern manufacturing environments.
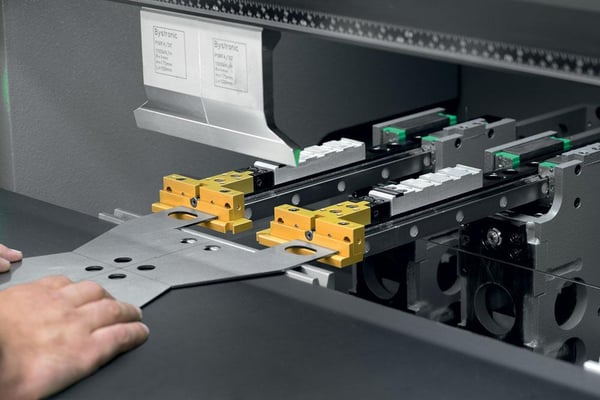
Programming and Operation
Basics of Programming a CNC Sheet Metal Brake
Programming a CNC sheet metal brake involves creating a detailed set of instructions that the machine follows to perform precise bending operations. This process ensures that each part is bent accurately and consistently according to the design specifications. The programming process typically includes several key steps:
Designing the Part
The first step in programming a CNC sheet metal brake is designing the part using CAD (Computer-Aided Design) software. This software allows engineers to create detailed 3D models of the part, specifying dimensions, angles, and other critical features. The CAD model serves as the blueprint for the bending operations, providing a visual and technical representation of the final product. Common CAD software includes AutoCAD, SolidWorks, and CATIA, which offer powerful tools for precise part design.
Generating the Bending Sequence
Once the CAD model is complete, the next step is to generate the bending sequence using CAM (Computer-Aided Manufacturing) software. This software converts the CAD model into a series of instructions that the CNC machine can understand. The bending sequence includes detailed information about each bend, such as the angle, length, and order of operations. CAM software like Mastercam, SolidCAM, and Autodesk Inventor CAM are commonly used for this purpose. They allow users to optimize the bending sequence for efficiency and accuracy, taking into account factors like material properties and machine capabilities.
Setting Up the Machine
After generating the bending sequence, the next step is to set up the CNC sheet metal brake. This setup involves several critical tasks:
Tool Selection: Choose the appropriate tools and dies for the specific bending operations. The selection depends on the material type, thickness, and desired bend radius.
Machine Configuration: Configure the machine parameters, such as bend speed, pressure, and back gauge settings, to match the requirements of the bending sequence.
Material Loading: Load the sheet metal into the machine, ensuring it is properly aligned and secured. Accurate material handling is essential to prevent misalignments and defects during the bending process.
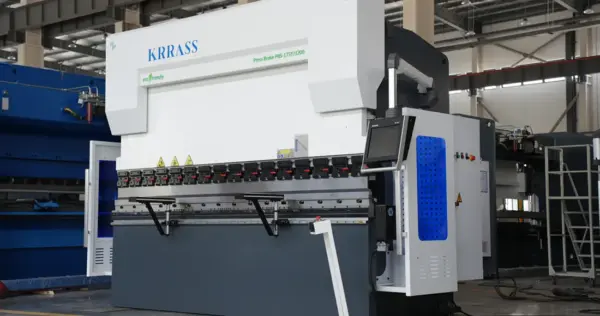
Simulating the Process
Many CNC systems offer simulation capabilities that allow users to visualize and test the bending process before actual production. This simulation helps identify potential issues, such as collisions, incorrect bends, or material deformation. By running a virtual simulation, operators can make necessary adjustments to the program or setup, reducing the risk of errors and ensuring that the program will produce the desired part accurately. Simulation software like CNC Simulator Pro and SolidWorks Simulation are useful tools for this step.
Executing the Program
Program Execution: The machine follows the programmed instructions, automatically performing the bending operations with high precision. The CNC control system ensures that each bend is executed accurately according to the specified sequence.
Real-Time Monitoring: Operators monitor the process in real-time, watching for any anomalies or deviations from the expected results. Advanced CNC systems may include sensors and feedback mechanisms that provide continuous updates on the bending process, allowing for immediate adjustments if needed.
Common Programming Software and Tools
Several software and tools are commonly used for programming CNC sheet metal brakes, each serving a specific purpose in the design, simulation, and execution of bending operations. Here is a detailed look at the key software and tools involved:
CAD Software
CAD (Computer-Aided Design) software is essential for creating detailed 3D models of the parts to be bent. These programs allow engineers to define precise dimensions, angles, and other critical features of the part. CAD software helps visualize the final product and provides a comprehensive blueprint for the bending operations. Some of the most widely used CAD software includes:
AutoCAD: Known for its versatility and precision, AutoCAD is a staple in many industries for 2D and 3D design. It offers a wide range of tools for drafting, modeling, and annotating designs.
SolidWorks: Popular for its user-friendly interface and powerful modeling capabilities, SolidWorks is extensively used in mechanical and sheet metal design. It allows for the creation of complex geometries and assemblies.
CATIA: Developed by Dassault Systèmes, CATIA is known for its advanced surface modeling and complex shape design capabilities. It is often used in automotive, aerospace, and other high-tech industries.
CAM Software
CAM (Computer-Aided Manufacturing) software is used to convert the CAD model into a set of instructions that the CNC machine can execute. This involves generating the bending sequence, specifying the angles, lengths, and order of bends. CAM software helps optimize the bending process for efficiency and accuracy. Key CAM software includes:
Mastercam: A leading CAM software, Mastercam provides comprehensive solutions for milling, turning, and sheet metal bending. It offers powerful tools for toolpath generation and process optimization.
SolidCAM: Integrated directly into SolidWorks, SolidCAM offers seamless workflow from design to manufacturing. It supports advanced features like iMachining for efficient and precise machining.
Autodesk Inventor CAM: Part of the Autodesk suite, this software integrates with Inventor and Fusion 360, providing robust tools for CNC programming and simulation.
Simulation Software
Simulation software allows users to visualize and test the bending process before actual production. This helps identify potential issues, such as collisions or incorrect bends, and ensures the accuracy of the program. Simulation software plays a crucial role in reducing errors and optimizing the bending sequence. Common simulation software includes:
CNC Simulator Pro: This application provides a realistic simulation of CNC operations, allowing users to test and verify their programs in a virtual environment. It helps detect and correct errors before running the actual machine.
SolidWorks Simulation: An extension of SolidWorks, this software offers comprehensive simulation tools for structural analysis, motion analysis, and thermal analysis. It helps predict how the part will behave under real-world conditions.
Machine Control Software
Machine control software is specific to the CNC sheet metal brake and is used to input and execute the bending programs. Each machine may come with its proprietary control software, designed to interface with the hardware and manage the bending operations. This software ensures that the machine follows the programmed instructions accurately. Examples of machine control software include:
Delem: Delem control systems are known for their user-friendly interfaces and advanced features. They offer precise control over bending operations and support various automation options.
Cybelec: Cybelec provides control solutions for press brakes, offering high flexibility and customization. Their software supports a wide range of machine configurations and integrates seamlessly with other automation systems.
ESA: ESA control systems are designed for ease of use and high productivity. They offer intuitive programming interfaces and advanced features for optimizing bending operations.
Estun: Estun provides advanced control solutions tailored for CNC sheet metal brakes. Their software is renowned for its robust performance and user-friendly interface, making it suitable for both simple and complex bending applications.
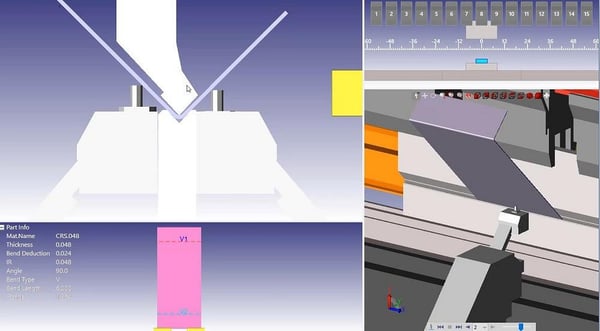
Types of CNC Sheet Metal Press Brakes and Selection Guide
Common Types of CNC Sheet Metal Brakes
When selecting a CNC sheet metal brake, it's essential to consider the type of machine that best suits your specific production requirements. Here are some common types:
Hydraulic CNC Sheet Metal Brake
Description: Hydraulic CNC sheet metal brakes utilize hydraulic cylinders to apply significant force for bending metal sheets. These machines are renowned for their robust power and ability to handle thick and heavy-duty materials with precision.
Advantages:
- Suitable for Heavy-Duty Applications: Hydraulic brakes excel in bending thick materials and handling high-force applications.
- Precise Control Over Bending Force: They offer precise control over the bending force, allowing for accurate shaping of materials.
- Capability for Thick Materials: Ideal for industries requiring bending of thick metals where high force is essential.
Considerations:
- Higher Initial Cost: Hydraulic brakes typically have a higher initial purchase cost compared to other types of CNC brakes.
- Hydraulic Fluid Maintenance: Regular maintenance of hydraulic fluids is required to ensure optimal performance and longevity of the hydraulic system.
Electric CNC Sheet Metal Brake
Description: Electric CNC sheet metal brakes utilize servo-electric motors to drive the bending process. These machines are known for their high precision and energy efficiency.
Advantages:
- Lower Energy Consumption: Electric brakes consume less energy compared to hydraulic counterparts, resulting in reduced operational costs.
- Quiet Operation: They operate more quietly than hydraulic brakes, making them suitable for quieter work environments.
- Precise Control Over Bending Angles: Offers precise control over bending angles and positions, suitable for intricate bends.
- Suitable for Lighter Gauge Materials: Best suited for bending lighter gauge materials efficiently.
Considerations:
- Higher Initial Cost for Larger Machines: Initial costs can be higher, especially for larger machines with higher capacity.
- Limitations on Material Thickness: Limited to lighter materials compared to hydraulic brakes due to capacity constraints.
Hybrid CNC Sheet Metal Brake
Description: Hybrid CNC sheet metal brakes combine hydraulic and electric technologies. They use hydraulic power for bending force and electric motors for precise positioning.
Advantages:
- Balance Between Power and Precision: Offers the power of hydraulic systems for bending force combined with the precision of electric systems for positioning.
- Energy Efficiency: More energy-efficient compared to traditional hydraulic brakes, contributing to cost savings.
- Versatility: Suitable for a wide range of applications and materials, providing flexibility in production.
Considerations:
- Hydraulic Fluid Maintenance: Like hydraulic brakes, hybrid systems require regular maintenance of hydraulic fluids.
- Varied Initial Cost: Costs can vary depending on the size and capabilities of the hybrid system.
Pneumatic CNC Sheet Metal Brake
Description: Pneumatic CNC sheet metal brakes use compressed air to apply force for bending. They are typically used for bending lighter gauge materials and specific applications.
Advantages:
- Simple Operation: Easy to operate and maintain, suitable for applications where simplicity is key.
- Lower Initial Cost: Generally more affordable upfront compared to hydraulic and electric brakes.
- Suitable for Thin and Soft Materials: Ideal for bending thin and soft materials effectively.
Considerations:
- Limited Bending Force: Compared to hydraulic brakes, pneumatic brakes have limitations in bending force, restricting their use to lighter applications.
- Not Suitable for Heavy-Duty Applications: They may not be suitable for applications requiring high force and bending thick materials.
By understanding the characteristics, advantages, and considerations of each type of CNC sheet metal brake, manufacturers can make informed decisions based on their specific production needs, material requirements, and budget constraints. Each type offers distinct capabilities suited to different applications and operational environments.
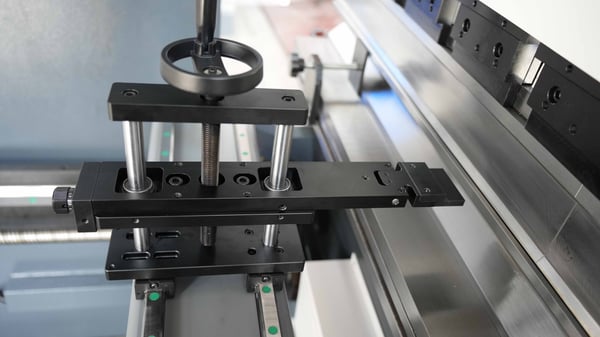
CNC Sheet Metal Brake vs. Hydraulic Brake: Which is Right for You?
Difference Overview
The CNC press brake machine represents an advanced iteration of the traditional hydraulic press brake, integrating a numerical control operating system for enhanced functionality. This upgrade significantly reduces the operator's workload by automating frequent process changes. However, it demands higher operational skills compared to conventional hydraulic models.
Unlike hydraulic press brakes, the CNC variant is distinguished primarily by its CNC operating system. This technological leap enhances processing efficiency and reduces manual labor. Yet, it necessitates more complex operational knowledge and skills. The CNC press brake machine features multi-step programming capabilities, enabling automated execution of complex bending sequences in a single operation.
In contrast, a hydraulic press brake machine utilizes electrical energy to energize a coil, generating gravitational force on the pressure plate. This mechanism facilitates secure clamping of thin plates between the pressure plate and the base. The electromagnetic force enables versatile shaping capabilities, accommodating various workpiece requirements including those with sidewalls.
How to Choose
Hydraulic Brake
Description:
A CNC (Computer Numerical Control) sheet metal brake refers to any bending machine controlled by a computer, offering precise control over bending operations. It encompasses various types such as electric, hybrid, and pneumatic, each with specific advantages.
Advantages:
- Precision: CNC brakes provide accurate control over bending angles and dimensions, crucial for complex geometries and high-quality finishes.
- Versatility: They can handle a wide range of materials and thicknesses, depending on the specific type (electric, hybrid, pneumatic).
- Automation: CNC technology allows for automated bending sequences, reducing labor costs and ensuring consistent results.
Considerations:
- Initial Cost: Depending on the type and size, CNC brakes can have a higher initial investment, especially for larger or more advanced models.
- Complexity: Requires skilled operators and programming knowledge to maximize efficiency and accuracy.
- Material Limitations: Some types may be limited in the thickness or type of materials they can effectively bend compared to hydraulic systems.
Hydraulic Brake
Description:
Hydraulic brakes use hydraulic fluid and cylinders to apply force for bending metal sheets, known for their high power and capability for heavy-duty applications.
Advantages:
- High Bending Force: Hydraulic systems excel in bending thick and heavy materials that require significant force.
- Durability: Known for their robustness and ability to withstand continuous use in demanding environments.
- Flexibility: Suitable for various bending tasks, including complex shapes and heavy materials.
Considerations:
- Maintenance and Longevity: Requires regular maintenance of hydraulic fluid and components to ensure optimal performance and longevity. This includes monitoring fluid levels, changing filters, and inspecting hydraulic lines.
- Noise Levels: Hydraulic systems can produce noise during operation, which may be a consideration depending on your workspace environment.
- Energy Consumption: Typically consumes more energy compared to electric or hybrid CNC brakes, potentially impacting operational costs over time.
By understanding the characteristics, advantages, and considerations of both CNC sheet metal brakes and hydraulic brakes, manufacturers can make informed decisions based on their specific production needs, material requirements, and operational preferences. Each type offers distinct capabilities suited to different applications and environments, ensuring efficient and effective metal bending operations.
Top 10 CNC Sheet Metal Brakes for Precision Bending in 2024
Creating a list of the top 10 CNC sheet metal brakes for precision bending in 2024 involves highlighting machines known for their accuracy, versatility, and advanced features. Here’s a curated selection based on current market trends and user reviews:
Trumpf TruBend Series
Description: Trumpf TruBend series is synonymous with high precision and reliability in sheet metal bending. They offer a range of models from entry-level to advanced systems, catering to various production scales and complexities.
Features: Advanced bending technology with options for automatic tool changing, laser angle measurement, and intuitive touchscreen controls for precise bending operations.
Applications: Suitable for industries requiring high accuracy in bending angles and dimensions, such as aerospace, automotive, and electronics.
Amada HFE Series
Description: Amada HFE series is known for its high-speed and high-performance capabilities, making it ideal for rapid and complex bending tasks.
Features: Incorporates advanced servo-electric drive technology for fast and accurate bending, along with user-friendly programming interfaces.
Applications: Widely used in industries demanding quick turnaround times and intricate bending requirements, including appliance manufacturing and metal furniture production.
Bystronic Xpert Series
Description: Bystronic Xpert series represents cutting-edge technology in CNC bending machines, designed to optimize productivity and precision.
Features: Features include automatic crowning systems, dynamic hydraulic compensation, and adaptive bending sequences for optimal bend accuracy.
Applications: Suitable for high-volume production environments requiring precise bending of complex geometries in materials ranging from mild steel to high-strength alloys.

Durma AD-S Series
Description: Durma AD-S series combines robust construction with advanced CNC capabilities, ensuring durability and accuracy in heavy-duty bending applications.
Features: Offers a range of bending lengths and tonnages with intuitive CNC controls, hydraulic synchronization, and programmable back gauge systems.
Applications: Ideal for industries dealing with thick and heavy materials, such as shipbuilding, construction equipment manufacturing, and structural steel fabrication.
Accurpress Accell Series
Description: Accurpress Accell series is known for its speed and precision, delivering rapid cycle times and accurate bends across a variety of material thicknesses.
Features: Features include high-speed hydraulic systems, adaptive bending technology, and customizable tooling options for versatile production needs.
Applications: Suitable for job shops and manufacturing facilities requiring efficient production of medium to large-sized parts with consistent bending accuracy.
Haco Euromaster S Series
Description: Haco Euromaster S series offers a blend of versatility and efficiency, designed to handle a wide range of bending applications with ease.
Features: Provides multi-axis CNC control, advanced safety features, and ergonomic design for operator comfort and productivity.
Applications: Used across various industries for bending light to medium-gauge materials with precise control over angles and dimensions, including HVAC, signage, and agricultural equipment.
SafanDarley E-Brake Series
Description: SafanDarley E-Brake series is characterized by innovative bending solutions that prioritize precision, energy efficiency, and ease of use.
Features: Incorporates advanced bending technology with servo-electric drive systems, automatic tool changers, and touch screen interfaces for intuitive operation.
Applications: Suitable for high-mix, low-volume production environments requiring rapid setup and precise bending of complex parts, such as electronics enclosures and medical devices.
KRRASS MB8 Series
Description: The KRRASS MB8 series offers high-performance bending solutions with customizable options for diverse production environments.
Features: CNC control with automatic bending sequences, hydraulic crowning systems, and adaptive bending tools.
Applications: Ideal for industries requiring flexibility and high-speed production of medium to heavy-gauge materials.
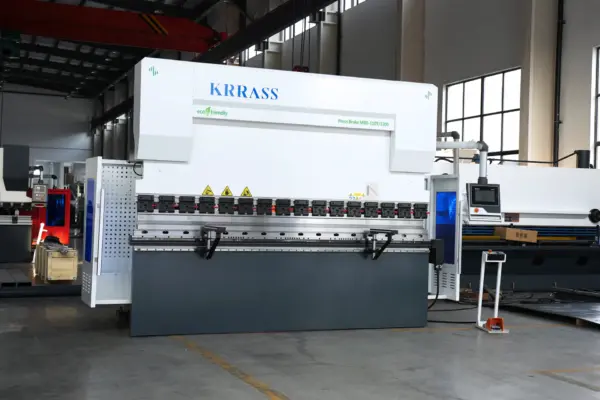
LVD MB8 Series
Description: LVD PPEB series features advanced bending technology with a focus on precision, flexibility, and operator convenience.
Features: Offers customizable tooling options, automatic angle correction, and remote diagnostics for enhanced operational efficiency.
Applications: Suitable for job shops and manufacturing facilities needing reliable bending solutions for a wide range of materials and part sizes, from thin sheet metal to thick plates.
Ermaksan Speed-Bend Series
Description: Ermaksan Speed-Bend series combines speed with accuracy, leveraging CNC technology for efficient and precise bending operations.
Features: Features include rapid tool change systems, dynamic crowning, and user-friendly control interfaces for seamless production flow.
Applications: Ideal for industries requiring high-speed production of complex parts with consistent bending accuracy, such as automotive stamping, aerospace components, and industrial machinery.
How to Select A Right CNC Sheet Metal Brake
Tailoring Machine Choices to Specific Production Needs
Choosing the right bending machine is pivotal in reducing production costs and ensuring optimal efficiency. It involves considering factors like material type, thickness, and required bending force. For instance, machines capable of free bending or bottomed die forming are selected based on the application's demands, balancing operational capabilities and cost-effectiveness.
Importance of Precision in Bending Operations
Precision in bending is critical for maintaining product quality. Factors such as bend angle control and material handling directly impact the final product's integrity. Proper setup and tooling selection are essential to mitigate issues like dimensional inaccuracies, ensuring consistent bend quality throughout production.
Challenges and Advances in CNC Bending Technology
The CNC bending industry faces ongoing challenges and innovations. Advances in CNC systems, including CAD/CAM integration and Computer-Aided Process Planning (CAPP), enhance flexibility and automation in bending operations. However, optimizing tooling for complex shapes or large curvatures remains a challenge, as it can affect tool longevity and rigidity. Despite rapid advancements, continued development is necessary to meet evolving manufacturing demands effectively, particularly in China's growing CNC bending machine sector.
Summary
In conclusion, understanding CNC sheet metal brakes is crucial for modern manufacturing precision and efficiency. These machines, driven by advanced CNC technology, offer unparalleled control over bending operations, ensuring precise angles, consistent quality, and reduced production costs. Whether you're considering a hydraulic, electric, or hybrid model, selecting the right CNC sheet metal brake depends on factors such as material type, thickness, and production volume.
For those looking to invest in CNC sheet metal brakes, KRRASS offers a range of advanced solutions like the MB8 series, known for their robust performance and innovative features. To maximize your investment, consider KRRASS's marketing tips: focus on machine reliability, comprehensive after-sales support, and training programs to optimize operator skills and machine utilization. By leveraging these insights, manufacturers can enhance their bending capabilities and achieve greater success in today's competitive market.
Remember, continuous adaptation to technological advancements and industry trends will further drive the evolution of CNC sheet metal brakes, ensuring they remain indispensable tools in the manufacturing landscape.
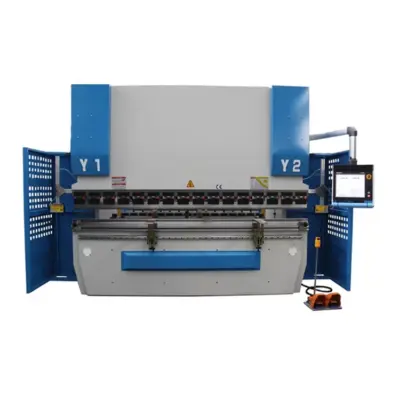