Are you in search of an electric press brake for sale? Investing in the right press brake can significantly enhance your metal bending operations, offering unparalleled precision, efficiency, and versatility. As industries evolve, the demand for high-performance machinery that can handle intricate bending tasks with ease is on the rise. Electric press brakes are at the forefront of this technological advancement, providing businesses with a reliable solution to achieve superior results.
Introduction
Significance of Electric Press Brakes in Modern Manufacturing
In the realm of modern manufacturing, precision and efficiency are paramount. Electric press brakes have emerged as a critical component in achieving these goals. Unlike their hydraulic counterparts, electric press brakes utilize electric servo motors to drive the bending process, ensuring consistent and accurate results. This precision is crucial for industries such as aerospace, automotive, and electronics, where even the slightest deviation can lead to significant quality issues and increased production costs.
Moreover, the adoption of electric press brakes aligns with the industry's shift towards more sustainable and eco-friendly practices. These machines consume less energy compared to hydraulic models, reducing the overall carbon footprint of manufacturing operations. As a result, companies are not only able to enhance their production capabilities but also contribute to environmental conservation efforts.
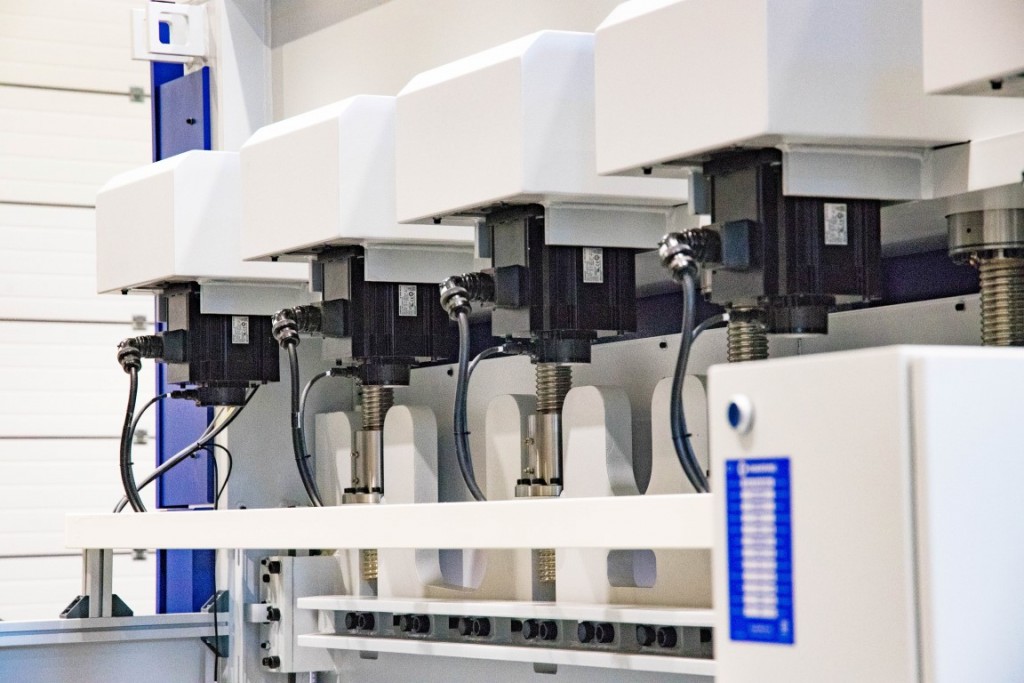
Benefits of Choosing an Electric Press Brake Over Traditional Hydraulic Models
- Precision and Accuracy Electric press brakes deliver unmatched precision in metal bending, thanks to their advanced control systems and servo motor technology. This precision ensures consistent quality in every bend, reducing the need for rework and minimizing material waste.
- Efficiency and Speed The operational speed of electric press brakes is significantly higher than that of hydraulic models. This increased speed translates to higher throughput and shorter production cycles, enabling manufacturers to meet tight deadlines and improve overall productivity.
- Energy Efficiency Electric press brakes are designed to be more energy-efficient, consuming up to 50% less power than hydraulic presses. This energy savings not only reduces operational costs but also supports sustainability initiatives by lowering energy consumption.
- Low Maintenance One of the notable benefits of electric press brakes is their reduced maintenance requirements. Unlike hydraulic systems, which involve complex fluid management and frequent maintenance, electric press brakes have fewer moving parts and require less upkeep, leading to lower maintenance costs and less downtime.
- Versatility and Flexibility Electric press brakes offer greater versatility in handling various materials and thicknesses. Their advanced control systems allow for easy adjustments and customization, making them suitable for a wide range of applications and industries.
What Is An Electric Press Brake
Definition
An electric press brake is a type of machine used in the manufacturing industry for bending sheet metal and plate material. Unlike traditional hydraulic press brakes, which rely on hydraulic fluid to create pressure, electric press brakes use electric servo motors to drive the bending process. This modern approach provides higher precision, speed, and energy efficiency, making electric press brakes a preferred choice for many industrial applications.
Core Components and Their Functions
- Electric Servo Motors
- Function: The electric servo motors are the heart of the electric press brake. They convert electrical energy into mechanical motion, controlling the movement of the ram (the part of the press brake that moves up and down to bend the metal).
- Operation: These motors provide precise control over the position and force of the ram, allowing for consistent and accurate bending operations.
- Ram
- Function: The ram, also known as the punch, is the component that directly interacts with the metal sheet. It moves vertically to press the metal against the die, creating the desired bend.
- Operation: Controlled by the electric servo motors, the ram's movement is highly accurate, ensuring precise bends according to the programmed specifications.
- Die
- Function: The die is a fixed component that the metal is pressed against by the ram. It shapes the metal into the desired angle and form.
- Operation: Dies come in various shapes and sizes, allowing for different types of bends and angles. The die's design determines the final shape of the bent metal.
- CNC Control System
- Function: The CNC (Computer Numerical Control) system is the brain of the electric press brake. It allows operators to program and control the bending process with high precision.
- Operation: Through a user-friendly interface, operators can input specific parameters such as bend angles, material thickness, and bend length. The CNC system then controls the servo motors and other components to execute the programmed bends accurately.
- Back Gauge
- Function: The back gauge is a mechanical stop that positions the metal sheet accurately before bending.
- Operation: It ensures the metal sheet is correctly aligned and positioned for each bend, contributing to the consistency and precision of the bending process.
- Safety Features
- Function: Safety features are integrated to protect operators from potential hazards during the bending process.
- Operation: These may include light curtains, safety doors, and emergency stop buttons, which immediately halt machine operation if a safety risk is detected.
How These Components Work Together
In an electric press brake, the CNC control system orchestrates the entire bending process. Operators program the desired bends into the CNC system, which then directs the servo motors to move the ram with precise force and positioning. The back gauge ensures the metal sheet is correctly aligned, while the ram presses the metal against the die to create the bend. Safety features continuously monitor the operation to protect the operator.
This seamless integration of advanced components allows electric press brakes to deliver high-precision bends with minimal operator intervention, making them an invaluable tool in modern manufacturing environments.
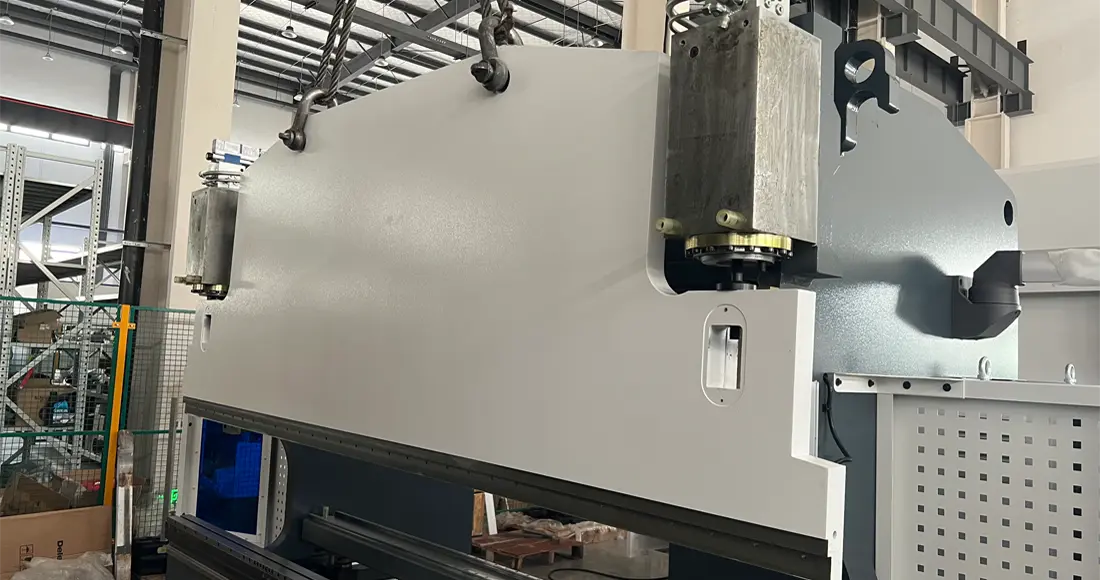
Six Types of Electric Press Brake For Sale On Market
1. Servo-Electric Press Brake:
Overview: Servo-electric press brakes use servo motors to drive the ram, offering precise control and high efficiency.
Key Features:
- Precise control over bending operations.
- Energy-efficient operation with reduced power consumption.
- Quiet operation with minimal noise.
- Suitable for applications requiring high accuracy and repeatability.
2. Electro-Hydraulic Press Brake:
Overview: Electro-hydraulic press brakes combine electric and hydraulic systems for bending operations.
Key Features:
- Utilizes electric motors for positioning and hydraulic systems for bending.
- Offers a balance between precision and power.
- Suitable for a wide range of bending applications.
- May require less energy compared to traditional hydraulic press brakes.
3. Hybrid Press Brake:
Overview: Hybrid press brakes combine hydraulic and electric technologies to optimize performance and energy efficiency.
Key Features:
- Combines the precision of electric press brakes with the power of hydraulic systems.
- Offers versatility for various bending applications.
- Can be more energy-efficient compared to traditional hydraulic press brakes.
- Provides a balance between speed, accuracy, and power.
4. Direct Drive Electric Press Brake:
Overview: Direct drive electric press brakes utilize servo motors directly connected to the ram for bending operations.
Key Features:
- Offers high-speed and precise bending operations.
- Direct transmission of force without mechanical components like gears.
- Provides exceptional accuracy and repeatability.
- Energy-efficient operation with reduced maintenance needs.
5. Fully Electric Press Brake:
Overview: Fully electric press brakes rely entirely on electric motors for bending operations, eliminating hydraulic systems.
Key Features:
- Energy-efficient and environmentally friendly operation.
- Precise control over bending processes.
- Minimal maintenance requirements.
- Suitable for applications requiring high-speed and high-precision bending.
6. CNC Electric Press Brake:
Overview: CNC electric press brakes feature computer numeric control for automated bending sequences and precision control.
Key Features:
- Advanced CNC control for programming and automation.
- Precise and repeatable bending operations.
- Suitable for complex bending tasks and high-volume production.
- Offers a wide range of features for enhanced productivity and efficiency.
7. Variable Radius Electric Press Brake:
Overview: Variable radius electric press brakes allow bending at various radii without changing tools.
Key Features:
- Versatile bending capabilities for a wide range of part geometries.
- Eliminates the need for tool changes for different bend radii.
- Suitable for complex and customized bending requirements.
- Offers flexibility and efficiency in production.
Each type of electric press brake has its advantages and is suitable for different applications. Understanding your specific bending needs and production requirements will help you choose the right type of electric press brake for your operations.
10 Reasons For Owning An Electric Press Brake
When considering an electric press brake for your metalworking needs, understanding the various benefits is crucial for making an informed investment. Here are some key advantages of electric press brakes:
1. Lower Overall Cost
While the initial cost of hybrid or all-electric press brakes can be 20-30% higher than standard hydraulic models, the investment pays off in the long run. These machines offer superior efficiency and accuracy, resulting in lower operational and maintenance costs over their lifespan. The savings in energy and reduced downtime make the extra upfront cost worthwhile.
2. Energy Efficiency
Electric and hybrid press brakes are designed to use energy only when needed, unlike traditional hydraulic systems that consume power continuously. This feature is particularly evident in servo motor-driven CNC bending machines, which shut down automatically when not in use. This energy efficiency can lead to substantial savings, making electric or hybrid press brakes an excellent long-term investment.
3. Higher Accuracy
Inaccurate press brakes often require multiple adjustments and test bends, leading to hidden costs and wasted materials. Electric press brakes, known for their high precision, eliminate these issues. For instance, the Krrass electric press brake from China features a "direct-drive system" with servo motors tied to ball screws, offering extreme accuracy of 0.000079 inches. This level of precision reduces scrap and improves overall productivity.
4. Noise Reduction
Noise pollution is a significant concern in machine shops. Electric press brakes operate much quieter than their hydraulic counterparts, providing a more comfortable working environment. This reduction in noise can lead to higher employee satisfaction, fewer sick days, and lower turnover rates, ultimately contributing to better company performance.
5. Environmental Benefits
Electric press brakes consume less energy and eliminate the need for hydraulic oil changes, making them more environmentally friendly. These machines only use electricity when the ram is in motion, reducing energy consumption. Additionally, promoting the use of eco-friendly equipment can enhance a company's image and marketing efforts.
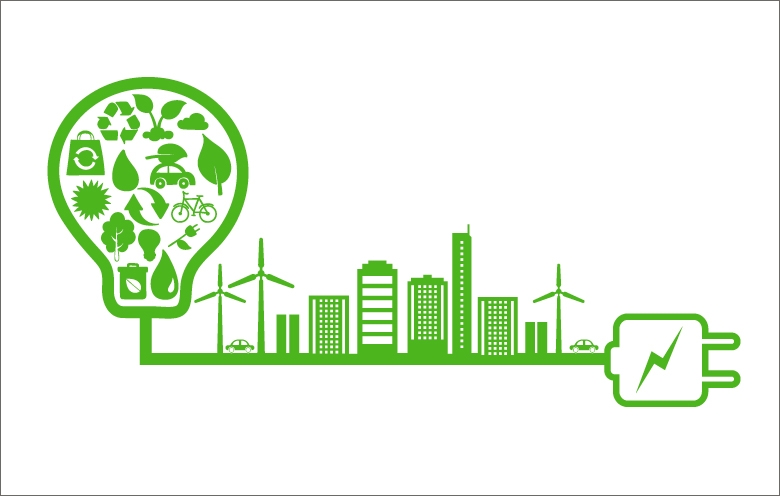
6. Advanced Controls and Automation
Modern electric press brakes, like those from Krrass, feature sophisticated CNC controls and automation, simplifying the bending process. Features such as automatic crowning and multiple ball screws across the ram ensure consistent angles and improved accuracy. These advanced systems eliminate issues like hydraulic viscosity fluctuations, enhancing reliability and ease of use.
7. Enhanced Safety Features
Electric press brakes often incorporate advanced safety systems, such as laser and light curtains, to prevent accidents. For example, Krrass's press brakes have a safety feature that stops the ram and raises it if the operator steps hard on the pedal, preventing potential injuries. These safety features provide a safer working environment for operators.
8. Discrepancy Prevention Systems
Electric press brakes can use algorithms to monitor and control the bending process, ensuring quality and safety. Systems like those from Krrass track each bend’s required force and position, sounding an alarm if discrepancies are detected. This proactive approach helps identify potential hazards or material issues before they become problems.
9. Smaller Footprints
Electric press brakes typically require less space than their hydraulic counterparts, making them ideal for shops with limited space. The smaller footprint allows for greater flexibility in machine placement and can result in cost savings on manufacturing space. This advantage is particularly beneficial for shops needing to handle both large and small parts efficiently.
10. Flexible and Easy Setup
Setting up old hydraulic press brakes can be time-consuming and complex. In contrast, electric press brakes offer quick and easy setup, reducing cycle times and enhancing productivity. This ease of configuration allows operators to quickly switch between tasks and combine multiple machines for longer bending lengths, meeting diverse customer demands efficiently.
Functions and Applications of Electric Press Brake
Electric press brakes are widely used in the metalworking industry due to their versatility and efficiency. They offer precise control and high-speed operation, making them suitable for a variety of applications. Here are some common uses of electric press brakes:
Sheet Metal Bending
Electric press brakes are essential tools for bending sheet metal, accommodating a wide range of thicknesses and materials such as steel, aluminum, and stainless steel. With their advanced programmable controls, operators can set precise bending angles, ensuring accurate and repeatable bends. This makes them invaluable in producing high-quality components for various industries.
Plate Bending
Beyond sheet metal, electric press brakes are also adept at bending thicker plates. These machines generate sufficient force to bend heavy plates accurately, making them ideal for industries like shipbuilding, construction, and heavy machinery manufacturing. In these fields, large plates often need to be shaped into complex forms, and electric press brakes provide the necessary power and precision to achieve these shapes.
Box and Pan Folding
Electric press brakes excel at folding boxes and pans by bending multiple sides of a sheet metal piece to create a box or pan shape. The precise control of electric press brakes ensures that all sides are folded at the exact angles needed, resulting in a precise fit and seamless finished product. This capability is crucial for manufacturing enclosures, housings, and containers.
Automotive Industry
In the automotive industry, electric press brakes are indispensable for a variety of applications, including bending car body panels, forming exhaust components, and shaping brackets and supports. The high precision provided by electric press brakes ensures that automotive parts meet stringent quality standards, essential for safety and performance in vehicles.
Architectural Metalwork
Electric press brakes are widely used in architectural metalwork to create intricate and decorative metal elements. They can bend metal sheets and plates into complex shapes, facilitating the fabrication of unique designs for building facades, staircases, handrails, and other architectural features. This precision and flexibility allow architects and designers to bring innovative and aesthetically pleasing structures to life.
What Makes Electric Press Brakes Eco-Friendly
The perception of metalworking shops as dirty and noisy is outdated. Modern metal fabrication has transformed into a high-tech industry, characterized by advanced CNC machines, robotics, and a strong focus on waste reduction and environmental responsibility. Many of today's metalworking machines are designed with eco-friendliness in mind, aiming to reduce energy consumption and reliance on fossil fuels.
Press brakes, essential for bending sheet metal into desired shapes and angles, have evolved significantly. Traditional hydraulic press brakes use pressurized liquid to move a punch and die for bending metal. In contrast, electric press brakes perform the same function using an electric motor instead of a hydraulic system. Here’s why electric press brakes are considered eco-friendly.
Less Power Consumption
One of the primary eco-friendly aspects of electric press brakes is their reduced power consumption. Electric press brake motors only operate when actively bending metal. Although they require substantial power during operation, they do not consume energy when idle. This efficiency contrasts sharply with hydraulic press brakes, which must continuously circulate fluid, consuming energy even when not in use. This significant difference in energy consumption makes electric press brakes a greener choice.
Noise Reduction
Another advantage of electric press brakes is their quieter operation compared to hydraulic models. Noise pollution is a significant concern in metalworking environments, affecting workers' health and the surrounding community. Electric press brakes produce less noise and vibration, contributing to a more pleasant and safer work environment.
At Krrass, we offer a comprehensive collection of electric press brakes tailored for your metalworking needs. Our experts are available to help you select and maintain machinery, ensuring reduced downtime and efficient operation of your metal fabrication business.
By investing in electric press brakes, metal fabricators can significantly enhance their operations, aligning with modern standards of productivity, quality, and sustainability.
Factors To Consider When Choosing An Electric Press Brake For Sale
Selecting the right electric press brake for your metalworking operations is crucial for achieving optimal performance and efficiency. Here are some essential factors to consider:
Bending Capacity
The bending capacity is a primary consideration when choosing an electric press brake. This refers to the maximum thickness and length of metal sheets or plates the machine can handle. Ensure the press brake you select can accommodate the size and thickness of the materials you most frequently work with.
Tonnage
Tonnage is the amount of force the press brake applies during the bending process. It’s vital to choose a machine with appropriate tonnage for your materials. Insufficient tonnage can lead to incomplete or uneven bends, while excessive tonnage might cause damage or deformation of the metal. Matching the tonnage to your specific needs ensures optimal bending results.
Control System
The control system is integral to the press brake’s performance and user-friendliness. Look for a machine equipped with an intuitive control interface that facilitates precise and efficient operation. Features such as programmable bending sequences and automatic back gauge adjustment can significantly enhance productivity and accuracy, making complex tasks easier to manage.
Speed and Accuracy
Speed and accuracy are critical for maintaining productivity and product quality. Choose a press brake that offers high-speed operation without compromising precision. Advanced servo-electric technology is particularly effective in providing fast and accurate bending, leading to improved overall performance.
Energy Efficiency
With the growing emphasis on sustainability, considering the energy efficiency of the press brake is increasingly important. Opt for a machine that incorporates energy-saving features like variable speed motors and regenerative braking systems. These features not only help reduce your carbon footprint but also offer long-term cost savings through reduced energy consumption.
Electric Press Brake Cost: What to Expect
The cost of electric press brakes can vary significantly depending on various factors such as type, capabilities, and manufacturer. Here's a general price range you can expect:
- Servo-Electric Press Brake: $50,000 – $200,000
- Electro-Hydraulic Press Brake: $70,000 – $250,000
- Hybrid Press Brake: $90,000 – $300,000
- Direct Drive Electric Press Brake: $100,000 – $350,000
It's important to note that these are average price ranges, and the actual cost may vary based on factors such as:
- Bending Capacity: Machines with higher tonnage and bending capabilities tend to be more expensive.
- Control System: Press brakes with advanced CNC controls and automation features may have higher costs.
- Brand and Model: Well-known brands or models with advanced features may be priced at the higher end of the range.
- Additional Features: Additional features like safety systems, tooling options, and automation capabilities can impact the overall cost.
- Size and Configuration: Larger machines or those with special configurations may have higher prices.
Keep in mind that while upfront costs are important, considering long-term operational costs and productivity gains is crucial for evaluating the overall value of the investment.
Top Brands and Models of Electric Press Brake For Sale
When choosing a electric press brake, it's essential to consider reputable brands and popular models that offer reliability, performance, and advanced features. Besides Krass from China, here's an overview of leading manufacturers and some of their popular models:
1. Amada
Popular Models:
- Amada HG Series: Known for high-speed, high-precision bending with advanced servo-hydraulic technology.
- Amada EG Series: All-electric press brakes offering precision bending with reduced energy consumption.
- Amada HDS Series: Hybrid press brakes combining hydraulic and electric technology for versatility and efficiency.
2. Trumpf
Popular Models:
- Trumpf TruBend Series: Features a range of hydraulic, electric, and hybrid press brakes known for their precision and flexibility.
- Trumpf TruBend Center Series: Combines bending and automated part handling in one machine for increased efficiency.
3. Bystronic
Popular Models:
- Bystronic Xpert Series: Offers high-speed bending with advanced features like dynamic crowning for precise results.
- Bystronic Xpert Pro Series: Advanced hydraulic press brakes with ergonomic design and energy-efficient operation.
4. Haco
Popular Models:
- Haco SynchroMaster Series: Hydraulic press brakes with advanced CNC controls for accurate and efficient bending.
- Haco Euromaster Series: Versatile hydraulic press brakes suitable for a wide range of applications.
5. LVD
Popular Models:
- LVD ToolCell Series: Features fully electric press brakes with automatic tool changing systems for high productivity.
- LVD PPEB Series: Hydraulic press brakes known for their reliability, precision, and ease of use.
6. Accurpress
Popular Models:
- Accurpress Accell Series: High-speed hydraulic press brakes with advanced control systems for efficient bending.
- Accurpress Edge Series: Offers versatility and precision with hydraulic and hybrid models.
7. Durma
Popular Models:
- Durma AD-S Series: Hydraulic press brakes with user-friendly controls and high bending accuracy.
- Durma HD-TC Series: Hybrid press brakes combining hydraulic and electric technology for efficiency and precision.
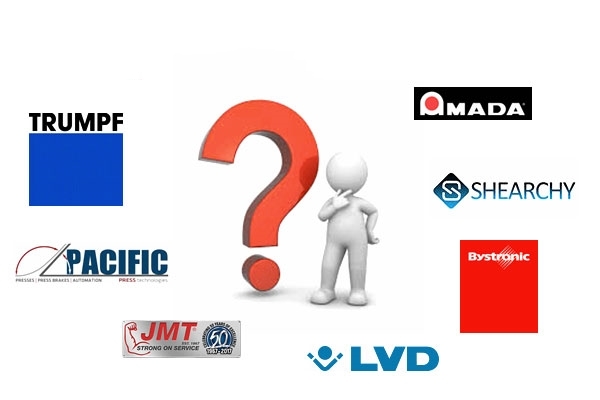
How to Evaluate the Right Electric Press Brake for Your Needs
Choosing the right electric press brake involves assessing your specific requirements, production goals, and budget. Here are steps to help you evaluate and select the most suitable machine:
1. Assess Your Requirements
- Bending Capacity: Determine the maximum thickness and length of metal sheets or plates you'll be working with.
- Production Volume: Evaluate your expected production volume to ensure the press brake can handle your workload efficiently.
- Accuracy Needs: Consider the level of precision required for your applications to avoid unnecessary scrap and rework.
- Space Availability: Measure the available space in your facility to ensure the press brake fits comfortably.
2. Identify Key Features
- Control System: Determine the type of control system you need, such as CNC for precise control over bending sequences.
- Energy Efficiency: Assess energy-saving features like variable speed motors or regenerative braking systems to reduce operational costs.
- Safety Features: Look for modern safety features like laser guards or light curtains to ensure operator safety.
- Automation: Consider automation features such as automatic tool changing or robotic integration for increased productivity.
3. Evaluate Potential Machines
- Research Brands and Models: Explore different brands and models to find ones that match your requirements.
- Compare Specifications: Compare bending capacity, accuracy, speed, energy efficiency, and safety features among potential machines.
- Consider Long-Term Costs: Look beyond the initial price and consider long-term costs such as maintenance, energy consumption, and downtime.
- Read Reviews and Testimonials: Look for reviews from other users and testimonials to gauge reliability and performance.
- Request Demos or Trials: If possible, request demos or trials to see the machine in action and assess its performance firsthand.
4. Consult with Experts
- Talk to Suppliers: Consult with press brake suppliers or manufacturers to discuss your specific needs and get expert advice.
- Get Multiple Quotes: Obtain quotes from different suppliers to compare prices and negotiate the best deal.
- Ask Questions: Don't hesitate to ask questions about features, warranties, and support services.
5. Consider Future Expansion
- Scalability: Choose a press brake that can accommodate your future growth and evolving production needs.
- Flexibility: Opt for a machine that allows for easy upgrades or additions of accessories as your requirements change.
- Training and Support: Ensure the supplier offers training and ongoing support to maximize the machine's efficiency.
6. Stay Within Budget
- Set a Budget: Determine your budget range and stick to it while evaluating options.
- Consider Total Cost of Ownership: Factor in long-term costs to ensure the chosen machine is cost-effective over its lifespan.
By following these steps and considering your specific requirements, production goals, and budget, you can effectively evaluate and select the right electric press brake for your metalworking needs. For expert advice and assistance, you can consult with KRRASS, a leading manufacturer known for their high-quality press brakes. KRRASS offers a wide range of electric press brakes tailored to various applications, and their team can provide detailed information on machine specifications, features, and customization options to help you make an informed decision.
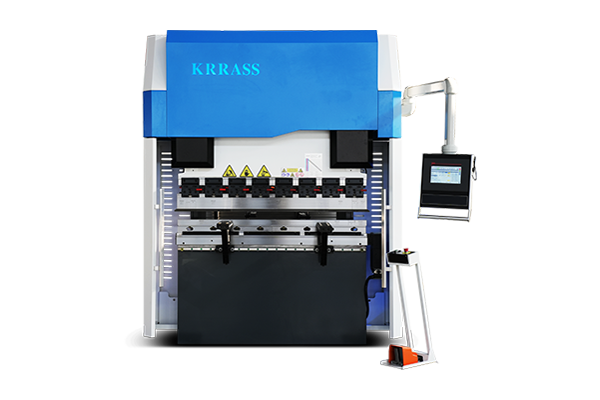