In today's competitive metalworking industry, having the right tools in your workshop can make all the difference. One such essential tool is the ironworker press brake. This versatile machine combines the functionalities of an ironworker and a press brake, offering unparalleled precision, efficiency, and versatility. By incorporating an ironworker press brake into your workshop, you can significantly enhance your production capabilities, reduce downtime, and achieve superior quality in your metal fabrication projects.
Introduction
Brief Overview of the Ironworker Press Brake
The ironworker press brake is a multifunctional piece of equipment designed to perform a variety of metalworking tasks. It integrates the capabilities of an ironworker, which handles tasks such as punching, notching, and shearing, with those of a press brake, which is used for bending and shaping metal sheets. This combination allows for a streamlined workflow and reduces the need for multiple separate machines, making it an invaluable addition to any metalworking shop.
Importance of the Right Tools in Metalworking
In the realm of metalworking, precision and efficiency are paramount. The right tools can drastically impact the quality of the final product, the speed of production, and the overall cost-effectiveness of operations. An ironworker press brake not only ensures high precision and consistent results but also enhances the productivity of your workshop. By investing in such versatile and reliable equipment, metalworking professionals can meet the demands of modern industry standards and stay ahead of the competition.
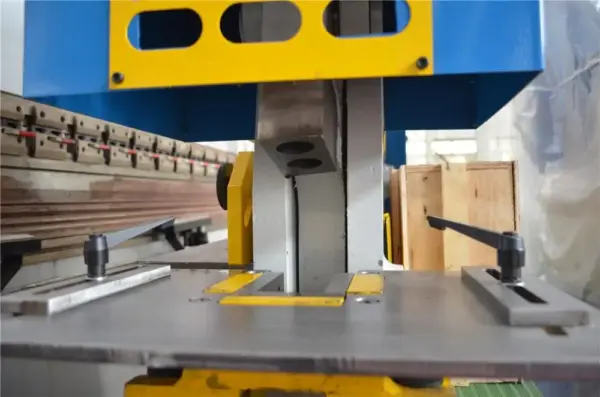
Components of Ironworker Press Brake
Frame: The frame of an ironworker press brake is typically made from heavy-duty steel or cast iron. It serves as the machine's foundation, providing stability and support for the bending operation. The frame is designed to withstand the high forces generated during bending without flexing or deforming, ensuring consistent and accurate bending results.
Hydraulic System: The hydraulic system in a press brake is crucial for generating the force needed to bend metal sheets. It consists of hydraulic cylinders, hydraulic pumps, valves, and a hydraulic reservoir. When activated, the hydraulic cylinders apply force to the ram (or beam), which in turn applies pressure to the metal sheet to perform the bending operation. The hydraulic system allows for precise control over the bending force and speed, essential for achieving accurate bends across different material thicknesses and types.
Bed and Ram: The bed of the press brake is a flat surface where the metal sheet rests during bending operations. It provides support and stability to ensure the material remains in position throughout the bending process. The ram, also known as the beam or slide, moves vertically under hydraulic pressure to apply force to the metal sheet. The alignment and parallelism between the bed and ram are critical for achieving uniform bending angles and maintaining the quality of the finished parts.
Back Gauge: The back gauge is a positioning device that helps operators accurately position the metal sheet for bending. It consists of fingers or stops that can be adjusted to accommodate different part lengths and bending requirements. The back gauge ensures consistent bending dimensions and repeatability, especially when producing multiple parts with identical dimensions.
Control System: Modern ironworker press brakes are equipped with sophisticated control systems that allow operators to input bending parameters and control the machine's operation. The control system typically includes a touch screen or interface where operators can set bending angles, bending force, back gauge positions, and other parameters. Advanced control systems may also feature programmable settings for automated bending sequences and batch production.
Tooling: Tooling refers to the punches and dies mounted on the ram of the press brake. These tools come in various shapes and sizes to accommodate different bending profiles and material thicknesses. The selection of tooling depends on the specific bending requirements, such as V-dies for creating sharp bends or hemming tools for folding edges. Tooling can be customized or exchanged to suit different bending applications and part designs.
Safety Features: Press brakes are equipped with various safety features to protect operators and maintain a safe working environment. Common safety features include emergency stop buttons, light curtains, safety mats, and safety guards. These features help prevent accidents by immediately halting machine operation if an operator enters a hazardous area or if there is a malfunction.
Electrical System: The electrical system of a press brake includes motors, sensors, switches, and wiring that control the operation of hydraulic components and other machine functions. Electrical controls ensure precise synchronization between the hydraulic system, control system, and other mechanical components. Sensors provide feedback on machine position, pressure, and safety status, contributing to safe and efficient operation.
Benefits of Using A Ironworker Press Brake
Enhanced Precision and Accuracy
One of the standout features of the ironworker press brake is its ability to provide exceptionally precise bends and cuts. This machine is designed with advanced control systems and high-quality components that ensure each operation is executed with meticulous accuracy. The integration of precise positioning technology allows for consistent and repeatable results, which is crucial in metalworking projects that demand high levels of exactitude.
The ironworker press brake achieves this precision through a combination of robust construction, state-of-the-art hydraulic or servo-electric systems, and sophisticated software controls. These elements work together to minimize errors and variations, allowing operators to produce intricate and complex shapes with ease. Additionally, the machine's versatility in handling various materials and thicknesses further enhances its precision capabilities.
Projects That Benefit from Enhanced Precision
Aerospace Components: The aerospace industry requires parts that meet stringent quality standards and exact specifications. The precise bending and cutting capabilities of the ironworker press brake ensure that each component fits perfectly, reducing the risk of mechanical failure.
Architectural Metalwork: Creating detailed architectural elements, such as custom facades, railings, and decorative panels, demands high precision to achieve the desired aesthetic and structural integrity. The ironworker press brake allows for the creation of intricate designs with flawless execution.
Automotive Parts: In the automotive industry, components must adhere to tight tolerances to ensure proper assembly and function. The ironworker press brake's accuracy in producing parts such as brackets, frames, and panels helps maintain the quality and performance of vehicles.
Medical Devices: Medical device manufacturing often involves the fabrication of small, complex parts that require precise bends and cuts. The ironworker press brake provides the accuracy needed to produce reliable and safe medical instruments and equipment.
By delivering enhanced precision and accuracy, the ironworker press brake enables metalworking professionals to take on a wide range of projects with confidence, ensuring that the final products meet or exceed industry standards.
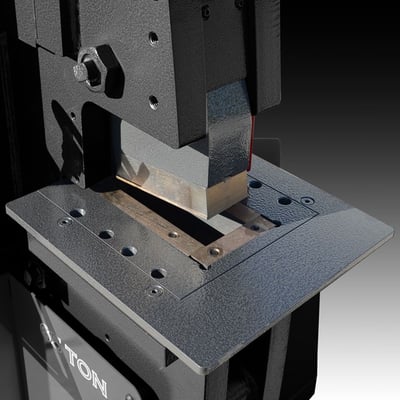
Increased Efficiency and Productivity
One of the most significant advantages of the ironworker press brake is its ability to perform multiple functions, making it an indispensable tool in any metalworking workshop. This machine combines the capabilities of an ironworker—such as punching, notching, and shearing—with those of a press brake, which is used for bending and shaping metal sheets. This multifunctionality allows metalworkers to complete various tasks without the need for multiple machines, streamlining the workflow and reducing the time spent on setup and changeovers.
Ability to Perform Multiple Functions
The ironworker press brake's design integrates several metalworking operations into one machine, eliminating the need to move materials between different stations or machines. It can quickly switch between tasks such as punching holes, cutting metal sheets, and bending parts, which enhances the overall efficiency of the production process. This consolidation of functions not only saves space in the workshop but also reduces the complexity of managing multiple machines and their maintenance schedules.
How This Versatility Leads to Time and Cost Savings
The versatility of the ironworker press brake translates directly into time and cost savings in several ways:
Reduced Setup Time: With the ability to perform multiple functions, operators spend less time setting up and calibrating different machines for various tasks. This leads to faster project turnaround times.
Lower Labor Costs: Since one machine can handle several operations, fewer workers are needed to operate multiple machines. This reduction in labor requirements lowers overall operational costs.
Decreased Material Handling: Minimizing the movement of materials between different machines reduces the risk of damage and loss, ensuring more efficient use of raw materials.
Less Maintenance and Downtime: Managing and maintaining one versatile machine is easier and less costly than maintaining multiple specialized machines. This results in lower maintenance expenses and less downtime due to equipment failure.
Real-World Examples of Efficiency Improvements
Fabrication Shops: In a busy fabrication shop, the ironworker press brake allows for seamless transitions between cutting, punching, and bending tasks. This improves the shop's ability to handle high-volume orders with tight deadlines, boosting overall productivity.
Custom Metalworking Projects: For custom metalworking projects, where unique designs and specifications are required, the ironworker press brake's flexibility ensures that complex parts can be produced quickly and accurately without the need for multiple machines.
Manufacturing Plants: In manufacturing environments where efficiency and cost control are paramount, the ironworker press brake's ability to perform multiple functions reduces the need for additional equipment and personnel, leading to significant cost savings and increased production capacity.
Small Workshops: Smaller workshops benefit greatly from the ironworker press brake's space-saving design and multifunctionality. It enables them to take on a wider variety of projects without investing in multiple machines, enhancing their competitiveness and profitability.
By incorporating an ironworker press brake into their operations, metalworking professionals can achieve significant improvements in efficiency and productivity, leading to better resource utilization and cost savings. This versatile machine is a valuable asset for any workshop looking to optimize its workflow and enhance its production capabilities.
Versatility in Metal Fabrication
Overview of the Various Tasks the Ironworker Press Brake Can Handle
The ironworker press brake is designed to perform a wide range of metalworking tasks, making it an incredibly versatile tool in any workshop. Here are some of the key functions it can handle:
Punching: Creating precise holes in metal sheets for fasteners or other purposes.
Notching: Cutting out sections from the edges or corners of metal sheets, useful for fitting parts together or for creating custom shapes.
Shearing: Cutting large sheets of metal into smaller pieces with clean, straight edges.
Bending: Forming metal sheets into specific angles or shapes, such as brackets, frames, or custom profiles.
Forming: Creating more complex shapes and profiles by manipulating metal sheets.
Cutting: Performing straight or angled cuts on metal sheets or bars
Benefits of Having a Multi-Functional Machine in a Workshop
Combining multiple functions into a single machine saves valuable floor space, allowing for a more organized and efficient workspace. This consolidation not only enhances the overall layout of the workshop but also reduces clutter, making it easier to manage operations. Additionally, investing in one versatile machine is often more cost-effective than purchasing several specialized machines. This approach not only lowers the initial investment but also reduces ongoing costs associated with maintenance and repair, providing significant long-term financial benefits.
The ability to perform multiple tasks without changing machines or setups leads to faster production times and increased throughput. This efficiency boost is critical for meeting tight deadlines and handling large volumes of work. Moreover, training operators to use one multi-functional machine is simpler and more time-efficient than training them on multiple different machines, reducing training costs and improving operational readiness. The ironworker press brake's flexibility in handling a wide variety of projects, from simple cuts to complex forming tasks, makes it ideal for workshops that deal with diverse metalworking requirements. This versatility ensures that the machine can adapt to various production needs, enhancing the workshop's capability to tackle different projects efficiently.
Durability and Longevity
Features That Contribute to the Ironworker Press Brake’s Durability
Constructed from robust materials such as heavy-duty steel, the ironworker press brake is built to endure high levels of stress and repetitive use without compromising its structural integrity. Its frames are reinforced to prevent deformation under heavy loads, ensuring consistent performance over time. These features not only enhance durability but also maintain reliability during demanding metalworking operations.
Components of the ironworker press brake are precisely engineered and machined to fit together perfectly, reducing wear and tear caused by friction and movement. Advanced hydraulics or servo-electric systems are integrated for smooth, reliable operation, with components designed to resist wear and maintain performance over extended periods. This precision engineering and advanced system integration contribute significantly to the machine's longevity and operational efficiency, making it a dependable asset in any metalworking workshop. Additionally, protective coatings and treatments are applied to surfaces to guard against rust and corrosion, further extending the machine's lifespan. Heavy-duty bearings and bushings are also utilized to handle high loads and minimize wear, ensuring robust performance and durability over the machine's lifespan.
Long-Term Cost Benefits Due to the Machine's Robust Construction
The robust construction of the ironworker press brake translates into fewer breakdowns and less frequent maintenance, significantly lowering ongoing repair and upkeep expenses. This durability not only reduces operational disruptions but also extends the machine's operational life, minimizing the need for costly replacements. By requiring less maintenance and demonstrating resilience under heavy use, the ironworker press brake offers substantial savings in operational costs over its lifespan.
High-quality construction ensures consistent performance of the ironworker press brake over time, minimizing downtime and production losses due to equipment failure. This reliability not only enhances operational efficiency but also contributes to a higher resale value. Machines that maintain their structural integrity and performance tend to command better prices in the resale market, offering a better return on investment if the machine is eventually sold. Moreover, advanced systems integrated into durable machines often result in improved energy efficiency, reducing operational costs further over time. This combination of reliability, longevity, and efficiency makes the ironworker press brake a cost-effective investment for metalworking workshops seeking long-term profitability and sustainability.
Ease of Use and Maintenance
User-Friendly Features
The ironworker press brake is designed with several user-friendly features that significantly enhance its usability in metalworking environments. It is equipped with intuitive controls, making setup and operation straightforward for operators. These user-friendly interfaces simplify the process, allowing for efficient handling of various tasks. Built-in safety features ensure operator protection during operation, which not only promotes peace of mind but also ensures compliance with stringent safety standards. Additionally, the machine offers adjustability through flexible settings, enabling operators to customize operations according to specific tasks and materials. This adaptability enhances versatility and ease of use across a wide range of applications, making the ironworker press brake a practical and efficient tool in modern workshops.
Maintenance Tips for Optimal Performance
Regularly inspect critical components such as hydraulics, bearings, and cutting tools to detect wear or damage early on. This proactive approach helps prevent unexpected breakdowns and ensures smooth operation. Additionally, keep all moving parts properly lubricated according to manufacturer recommendations. Proper lubrication minimizes friction and reduces the risk of premature wear, preserving the functionality and longevity of the machine.
Regular cleaning of the ironworker press brake is crucial to remove debris and contaminants that can accumulate and compromise performance. Cleanliness not only enhances operational efficiency but also prevents potential equipment failures. Furthermore, adhere to a scheduled maintenance plan outlined in the machine’s manual. This plan should include tasks such as replacing filters, performing calibration checks, and addressing any specific maintenance requirements recommended by the manufacturer. Following a structured maintenance routine helps optimize performance, minimize downtime, and maximize the lifespan of your ironworker press brake.
Conclusion
In conclusion, incorporating an ironworker press brake into your workshop operations not only expands your capabilities in metalworking but also enhances overall efficiency, reliability, and profitability. It stands as a valuable asset for any workshop looking to elevate their bending capabilities and meet the demands of modern manufacturing and fabrication challenges effectively.