In the use of the CNC Press Brake, there is likely to be some errors in use, this time you should check and find out the reasons once the Press Brake go wrong. The first step is to check whether the die is worn or damaged. If yes, a die should be replaced
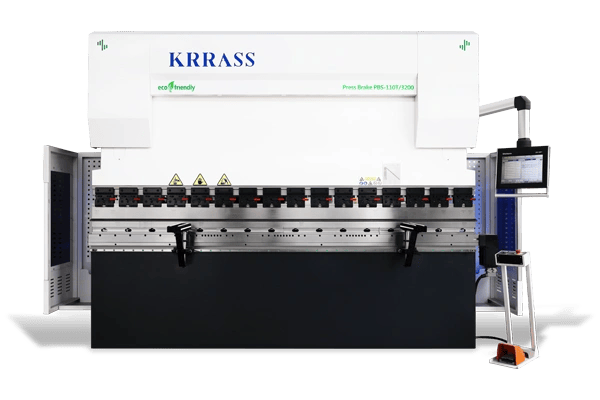
In the process of checking the CNC Press Brake, if there is no damage, check the parallelism between the ram and the worktable. If the use requirements cannot be met, the parallelism can be adjusted according to the relevant standards, so as to maintain the parallelism within the allowable range.
If the bending mechanism angle is still a certain error, it may not be because of the die or the parallelism, it may be in the hydraulic system of the machine, the balance mechanism does not ensure that the hydraulic oil evenly into the left and right cylinders, now you need to adjust the balance mechanism.
At the moment, adjust the working mode of the Press Brake to the "inching adjustment" state, and then remove the die or some other accessories, so that the ram can stay on the mechanical block, and then adjust the pressure gauge to desired value.
The concrete method is to compress the head of the dial gauge in the Press brake by 3-4 mm, step on the foot switch to boost the system pressure or system load, check the dial gauge clockwise deviation, if the specified value can stop the operation. Of course, except the above way, to emphasize that it is necessary to maintain the Press Brake and let it play its advantage to the most.
Learn more about our products, please visit and subscribe to our Youtube channel