Operating a CNC press brake requires a blend of technical knowledge, precision, and attention to safety. These advanced machines are integral to the metal fabrication industry, offering unparalleled accuracy and efficiency in bending sheet metal and plate material. Whether you're a beginner or looking to refine your skills, understanding the fundamental steps and best practices for operating a CNC press brake is essential. This guide will walk you through the entire process, from preparation and setup to executing bends and performing maintenance, ensuring you achieve optimal results with every use.
What Is CNC Press Brake
CNC press brakes are far more specialised than standard press brakes. They feature a fixed bottom bed with the V block tooling held in place and a top ram that travels under force with the V blade tool. On the largest industrial machinery, CNC brakes, which stand for Computer Numerically Controlled, can bend sheet metal work from a few inches across to portions many feet long. It causes the material between the punch and dies to yield.
Because CNC is programmable, moving between bends, pieces, and even materials is significantly faster. The setup time for a CNC press brake is substantially faster since the controller calculates all of the ram and backgage. It can also check for mistakes, determine the right bend sequence, and repeat the action for production forming. A manually operated press brake would need the operator to reset the machine after each bend is generated.
What is a CNC Press Brake Used For
The principal purpose of a CNC press brake machine is to bend/form sheet metal. They produce specified bends by clamping the sheet metal between the required punch and die.
Press braking is used in a variety of situations when a dimension needs to be added to a flat surface of sheet metal. It applied in various businesses and sectors, but most notably in architectural design, building, engineering, and transportation.
Because of its adaptability, press braking has the potential to take on forming operations that demand profiles for pieces that are smaller than usual and may not be comparable.
Typically, CNC sheet metal press brakes are used to create parts for HVAC (heating, ventilation, or air conditioning) systems and construction components. We may utilise the machines more diversely and creatively for particular purposes with the correct equipment.
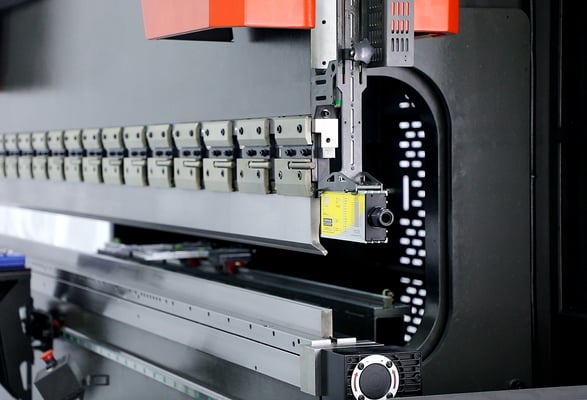
What Is CNC Bending
Computer numerically controlled (CNC) bending is a manufacturing technique performed by CNC press brakes (also known as CNC brake presses). These machines can bend sheet metal work from a few millimeters across to portions many metres long on the larger industrial machinery.
CNC press brakes feature either a fixed bottom bed with the V block tooling fastened in place or a top beam that travels under force with the V blade tools, a process known as down forming.
An up-forming machine is an inverse, with the bottom bend moving and the top beam immovable. Both process methods will provide identical sheet metal components, and there are no constraints on the design of your component to fit either machine.
Components of a CNC Press Brake
There are various parts that make up a press brake machine. The frame of the press brake is welded by the left and right upright plates (or sideframes), worktable (or bed), and vertical moving ram. The ram is made from the whole steel plate and is connected to the hydraulic piston rods the left and right hydraulic oil cylinder (often referred to as Y1 & Y2). The ram uses the hydraulic forces to move it and the upper tool (punch) along a gibbed way system and either a mechanical stop for fine adjustment or the more accurate electronic scale feedback method that provide exact positioning and thus accurate angles of bend.
Some systems are equipped with a mechanical synchronization system consisting of torsion, swing arm, joint bearings, and more. It has a simple structure, stable and reliable performance through machine stiffness, as well as high precision synchronization.
The material being bent upwards is called the “Flange” and it is measured and controlled for accuracy through a device on the press brake mounted in the rear of the machine called the “backgauge”. The backgauge of the CNC press brake utilizes a motor driven gearbox or chain driven gaging system, to output a synchronous movement of two ball or lead screws which in turn move the gaging bar in and out to the exact position required.
The position of the backgage is critical as it gages the length of every flange being formed and as such is controlled by the CNC controller. Through a program input by the operator, it controls the position of itself and the attached material stops, called “fingers” on the gage bar itself.
Benefits of Using A CNC Press Brake
Better Efficiency
There’s no denying the fact that CNC press brake machines are better when it comes to efficiency. Older machines usually produce 600 bends per hour, but the modern press brake with CNC is known for producing about 900 bends which is tremendous. You turn the machine on, and it will run until you change the tools for a new design. Previously, this was done manually, but now it is done with a touch screen, limiting the hard manual tasks.
To speed up manufacturing, these machines are much easier to install as they are lighter and easy to use. There are a variety of software programs that enable you to produce unique designs in no time. Old machines required extensive piping, which was always vulnerable to breaking down, but the CNC press brake machines do not require this, making them more efficient.
Who doesn’t want an industry with machines that would save their labor cost? In this 21st century, the target is to enhance productivity with minimum investment. When comparing CNC press brake with other machines, it works much faster and thus cuts the cost of extra electricity. Moreover, it is known for producing less waste during operations, which saves much of the cost.
Complex Designs
Numerous industries around the world rely on sheet metal fabrication, such as construction companies, food and beverage, and much more. If we talk about construction companies, they require structural material, which needs to be remarkable for better development. Moreover, the food & beveragescompanies need metal fabricated parts for creating equipment such as mixers, metal weighing scales, and whatnot.
Older machines were tasked to create very limited designs. However, as CNC press brake machines are introduced in the market, they have paved the path for unique and complex designs. The best part is that the machine comes with many customizable parts and components which you can use to manipulate the operations as you want.
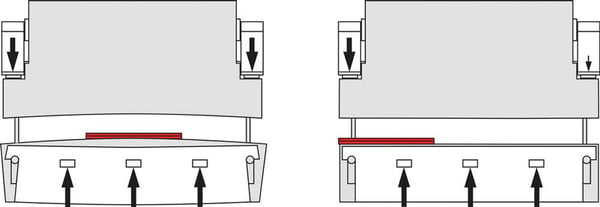
Automation & Safety
One of the key benefits of CNC press brake machines is automation for sure. Automation is known for increased accuracy. As they have decreased labor costs, automation is also credited for faster completion of tasks, boosting overall productivity. They can speed up the fabrication as well as reduce the lead times. Previously, meeting the demands of the customers was ahead, but with the inclusion of CNC press brake machines, demands are met flawlessly, as this century is all about consumerism as this is the age of mass consumption.
One of the key benefits of CNC press brake machines is automation for sure. Automation is known for increased accuracy. As they have decreased labor costs, automation is also credited for faster completion of tasks, boosting overall productivity. They can speed up the fabrication as well as reduce the lead times. Previously, meeting the demands of the customers was ahead, but with the inclusion of CNC press brake machines, demands are met flawlessly, as this century is all about consumerism as this is the age of mass consumption.
Operating Procedures for a CNC Press Brake
Now that we have discussed the different components of a CNC press brake, let's dive into the operating procedures. Operating a CNC press brake requires a combination of technical knowledge and practical experience. It is essential to follow the manufacturer's instructions and adhere to safety guidelines to avoid accidents and injuries.
Setup:
The first step in operating a CNC press brake is to set up the machine. This involves selecting the appropriate tooling, adjusting the backgauge, and programming the machine. The setup process will vary depending on the type of sheet metal being used and the desired bending angle.
The following are the steps for setting up a CNC press brake:
Choose the right location: The CNC press brake should be placed in an area that is large enough to accommodate the machine, and with enough clearance for the operator to move around comfortably. The location should also be equipped with proper electrical and ventilation systems.
Install the machine: The CNC press brake should be installed by a professional technician. The machine should be level and securely bolted to the floor to prevent any movement during operation.
Connect the Power: The machine should be connected to a dedicated electrical circuit that is able to provide the necessary power requirements for the machine. The power supply should also be equipped with proper grounding and protection devices.
Install the Tooling: The CNC press brake comes with a variety of tooling options, such as punch and die sets. The appropriate tooling should be selected and installed according to the requirements of the job.
Program the Machine: The CNC press brake is programmed through a software interface that controls the machine’s movement and bending operations. The programming should be done by a skilled technician who has experience with CNC machines.
Perform Test Runs: Once the machine has been set up and programmed, a test run should be performed to ensure that the machine is functioning properly and that the tooling is correctly installed. This should be done using a scrap piece of material to avoid wasting valuable material.
Train the Operator: The operator should receive training on how to operate the CNC press brake safely and efficiently. This includes how to load and unload material, set up tooling, program the machine, and perform routine maintenance.
How to Do the Programming of CNC Press Brake?
To see which systems you use, generally simple CNC machine tools can be set if the hydraulic cylinder stroke and back gauge specifications are set. If you want to bend multiple steps, you can set each step according to the operating steps of different systems. Required specifications, system circulation system operation; if it is a full CNC machine tool hydraulic servo motor CNC Press Brake, the left and right molds must be set, the thickness of the raw materials, the material, the length, the bending method, the angle of view also has the back gauge specifications,
According to different requirements, you can set the speed regulation point, the round-trip aspect ratio, and the hold time. There are also stiffness compensation parameters. The actual operation of each system is often different, so it cannot be generalized.
How to Program CNC Press Brake?
Powering On: Begin by switching on the power supply. Turn on the power switch on the operation panel, then restart the oil pump. You should hear the oil pump start to rotate.
Stroke Adjustment: Pay close attention to adjusting the stroke before bending. Ensure there's a plate-thick gap when the lower die descends to the bottom to prevent damage to the equipment. This adjustment is typically done using an electric rapid adjustment system.
Selecting Bending Notches: Choose a slot thickness that is 8 times the material thickness. For example, when bending a 4mm thick plate, select a 32mm notch.
Backgauge Adjustment: Adjust the backgauge using either electric rapid adjustment or manual adjustment, similar to the method used with a hydraulic shearing machine.
Initiating the Bend: To begin bending, press the button switch. Unlike the hydraulic shearing machine, the CNC bending machine tool allows for instant pausing. Release the foot pedal to stop the process, and press it again to resume.
CNC Press Brake Metal Forming Tips
The most important press brake bending tip you can follow is to be aware of the material grade you are forming. The harder the grade, the more springback you should expect. If you use softer material, you will experience far less springback as that material conforms much easier to the angle of the die it is being forced into.
It's also critical to watch out for cracking or spreading, especially with sharp bends. Bottoming out (or bottom bending) can make the material even more prone to fracturing but provide an exact bend through the process of "coining". However, the nearer you can get to a 1-1 radius between the material thickness and the inside bend, the less likely you’ll see cracking on the outside of the bend.
A final press brake metal forming tip is to not compensate for springback by bottom bending but rather by using the appropriate tooling. However when you’re bottom bending, you need to work with the 88-degree punch. Using an 85-degree punch will extend the bend too much, which means you won’t be able to achieve enough spring forward to get the bend back to a 90-degree angle.
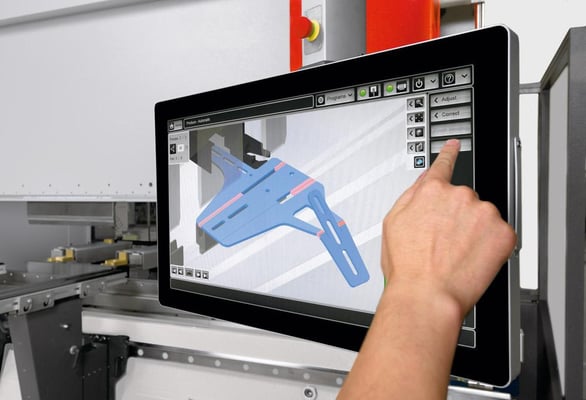
Skills of CNC Press Brake Use
1. Press brake machine is a device used to complete the overall bending and forming of sheet materials. After one stroke of the slider, the sheet is bent into a cross-sectional profile of a certain geometric shape. A relatively simple mold can be used to fold various shapes of workpieces, and multiple bending can also obtain various complex cross-sectional shapes.
2. In addition, if equipped with suitable molds, it can also be used for punching, shallow stretching, etc. The machine is widely used in aviation, aerospace, automobile, electronics, construction machinery, shipbuilding, railway vehicles, and other industries.
3. The Krrass bending machine adopts a special CNC system for bending machines. In addition to the basic number of axes Y1, Y2, and X axes, a variety of CNC axis configurations can be combined according to user needs.
4.The CNC system can automatically realize the control of the running depth of the slider, the adjustment of the left and right inclination of the slider, the adjustment of the pressure tonnage, the adjustment of the running speed of the slider, as well as the front and rear adjustment of the back gauge, the left and right adjustment, the up and down adjustment, and so on. The bending machine can easily realize the actions of slide down, work advance, pressure holding, return, jog and stop in the middle, and complete multiple bending of the same angle or different angles in one feeding.
CNC Press Brake Operator Requirements
● Only trained workers should operate the press brake.
● The operator should read the manual carefully.
● Make sure you understand the details, structure, performance, and safety information of the CNC bending machine before you start using it.
● Before starting to use the hydraulic sheet metal press brake, please follow the safety information items.
● The operating manual of the press brake is very important. We need to keep the manual in a safe place so that it can be checked if necessary.
How to Select the Proper CNC Press Brake Provider
Here are a few guidelines and recommendations that will assist in selecting an excellent press brake supplier:
Technical Strength: For optimal press brake solutions and product performance, ensure your facility has access to an experienced research and development team capable of developing them. A strong technical base is an integral component in guaranteeing product quality and performance.
Production Experience: Select an industrial facility with ample experience in production to demonstrate an in-depth knowledge of market trends, customer needs and their capacity for producing top-quality and stable products.
Quality Management Systems: Confirm that your facility has achieved international quality management system certification like ISO 9001. This shows that they have implemented an established quality management system and process in place that can ensure consistent product and dependability.
Equipment Investment: Evaluate the production equipment at your factory with special regard to its technological sophistication and maintenance needs. Modern production equipment is key in producing top-quality press brakes.
Delivery Capabilities: Make sure the factory you select can meet your production and delivery needs quickly by checking its production capacity and time-to-delivery cycle.
After-Sales Service: When choosing a manufacturing facility, ensure they offer comprehensive after-sales services such as installation commissioning training and maintenance for equipment purchased. Having prompt after-sales services provides invaluable support throughout its use.
Cost-Effectiveness and Price Selecting the most economical press brake requires taking into account performance, quality and support factors of each product offered at various manufacturers.
Considerations: Speak directly with the factory and outline all of your specifications and needs clearly so they can best understand them and offer tailored solutions.
Conclusion
If you are planning to invest in a CNC press brake machine, it represents a significant investment. To ensure you make the best choice, it's important to consider several key factors before making your decision. First, determine the types of materials you will be bending, as this will directly influence the type of machine you need.
Additionally, think about the complexity of your designs. Are your requirements simple, or do they involve complex and unique shapes? For intricate designs, opting for a machine with an extra axis, such as those offered by KRRASS, is essential to ensure precision and avoid any bending issues.
Once you've settled on the material and design complexity, consider your production volume. For mass production, CNC press brake machines are unparalleled in efficiency and consistency. Also, take into account the size of the machine in relation to your workspace. It's crucial not to choose a machine that's too large for your available space. KRRASS provides a variety of machine sizes to fit different workspace requirements, ensuring you find the perfect match for your needs.
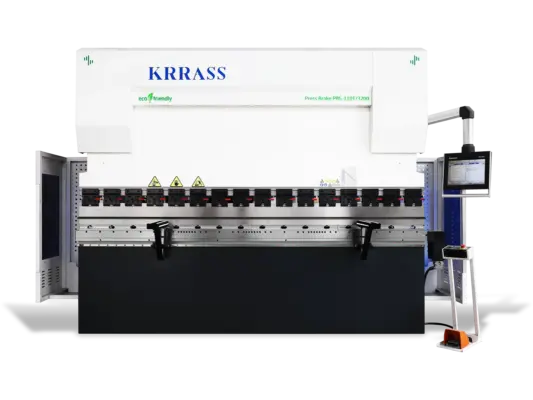