What is sheet metal press brake? This is a common question asked by beginers, although you have may have some exprerince on press brake bendbending, but you still may have details unknown. A sheet metal press brake is a type of brake, a machine used for bending sheet metal and metal plate.It forms predetermined bends by clamping the workpiece between a matching top tool and bottom die. In 2024, advancements in technology have further enhanced the capabilities of press brakes, making them more versatile, user-friendly, and efficient. Whether you're working with thick steel plates or thin aluminum sheets, a modern press brake can handle a wide range of materials and applications, making it an indispensable tool in industries like automotive, aerospace, and construction.
What Is A Sheet Metal Press Brake?
A sheet metal press brake is a machine used to bend and shape sheet metal into various forms and angles. It is a crucial tool in metalworking and fabrication, employed across various industries, including automotive, aerospace, construction, and manufacturing.
What Is Sheet Metal Bending?
Sheet metal bending is the process of shaping metal sheets into various forms by applying force to deform the material. This technique involves bending a thin sheet of metal, either once or multiple times, to achieve the desired geometry. The thickness of the sheet metal used can vary widely. Typically, sheet steel thickness ranges up to 6 mm, while thicker materials may require specialized equipment. A key rule is that the bend radius should be equal to or greater than the thickness of the material.
Other Terms for Sheet Metal Bending:
Sheet metal bending is known by several other terms, including forming, edging, folding, flanging, press braking, and die bending. The term "die bending" refers to bending processes that use a die and punch system, while "press braking" specifically relates to using a press brake machine to achieve the bends.
Purpose of Sheet Metal Bending in Manufacturing:
Sheet metal bending is used to create various features and shapes in metal sheets. This process is ideal for producing components like body panels, reinforcement struts, floor panels, brackets, and doors. It offers a faster, more cost-effective, and efficient alternative to machining for producing thin-walled parts.
Industries That Utilize Sheet Metal Bending:
Sheet metal bending is widely employed across several industries, including construction, automotive, transportation, aerospace, and infrastructure. It is used to fabricate features such as lips, joggles, flanges, and indents. Additionally, bending can enhance the stiffness of sheet metal parts, making it a versatile technique in metalworking.
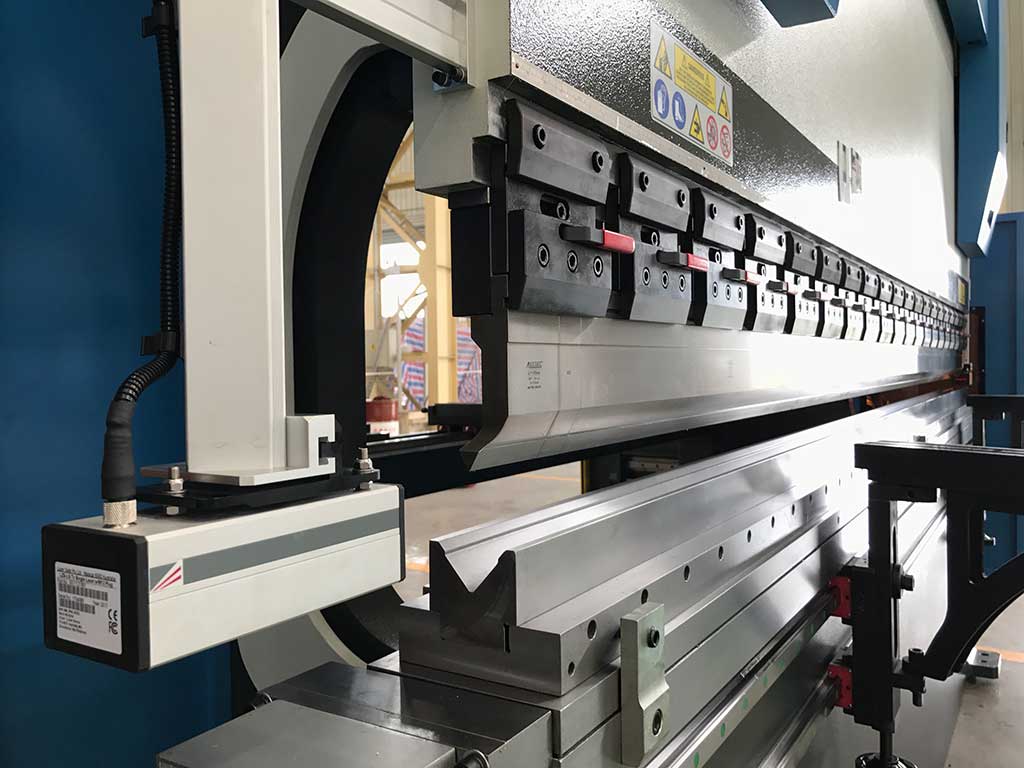
What Are the Types of Sheet Metal Press Brake
A sheet metal press brake can be characterized by several fundamental parameters, including its force or tonnage and working length. Additional key factors include stroke length, the distance between the frame uprights or side housings, the distance to the back gauge, and work height. The upper beam typically operates at speeds ranging from 1 to 15 mm/s.
Press brakes come in various types, such as nut-stop hydraulic, synchro hydraulic, electric, and hybrid models. Hydraulic presses function by utilizing two synchronized hydraulic cylinders on the C-frames, which move the upper beam. Servo-electric brakes, on the other hand, employ a servo motor to drive a ballscrew or belt drive, providing the necessary tonnage to the ram.
Historically, mechanical presses dominated the market until the 1950s. These machines operated by storing energy in a flywheel powered by an electric motor, which, when engaged by a clutch, would drive a crank mechanism to move the ram vertically. Mechanical presses offered advantages in accuracy and speed. However, with the advent of advanced hydraulics and computer controls, hydraulic machines have since become the most popular option.
Modern press brakes are typically equipped with either NC (Numeric Controlled) or CNC (Computer Numeric Controlled) systems. NC controllers are more basic, while CNC controllers offer higher-end functionalities. Although CNC systems may have a higher initial cost, they can be more cost-effective in the long run due to their efficiency.
Pneumatic and servo-electric machines are generally used for lower tonnage applications. Hydraulic brakes, known for their accuracy, reliability, energy efficiency, and safety, are favored in many applications. Unlike flywheel-driven presses, the ram motion in hydraulic brakes can be easily halted by safety devices such as light curtains or presence-sensing devices, ensuring safer operation.
Here is a detailed comparison of different types of press brakes (hydraulic, mechanical, CNC) along with their respective advantages and disadvantages:
Type | Advantages | Disadvantages |
Hydraulic Press Brake | High precision and control Suitable for various materials and thicknesses Capable of handling heavy materials Even force distribution | High cost Complex operation Cannot exceed rated tonnage |
Mechanical Press Brake | High precision and consistency Suitable for thin to medium-thickness materials Quick setup and tool change Ideal for forming complex shapes | Requires frequent tool changes and setups May lock into a complete cycle Requires skilled operation |
CNC Press Brake | High precision and automation Easy to operate, reduces labor intensity Suitable for various shapes and angles Increases production speed and efficiency Programmable, suitable for multi-step operations | High cost Limitations with highly reflective or brittle materials Requires specialized training and maintenance |
Backgauge
Recent advancements in press brake technology have largely focused on enhancing the control systems and a device known as the back gauge. A back gauge is crucial for accurately positioning metal pieces, ensuring that bends are placed precisely where needed. Additionally, back gauges can be programmed to move between bends, allowing for the consistent production of complex parts.
Modern press brakes are often equipped with multi-axis, computer-controlled back gauges, enabling operators to position materials accurately and follow a step-by-step sequence for each bend until the part is completed. Optical sensors further enhance this process by providing real-time feedback on the bending angle during the bend cycle. This data is sent to the machine controls, which then automatically adjust the process parameters to ensure precision throughout the bending operation.
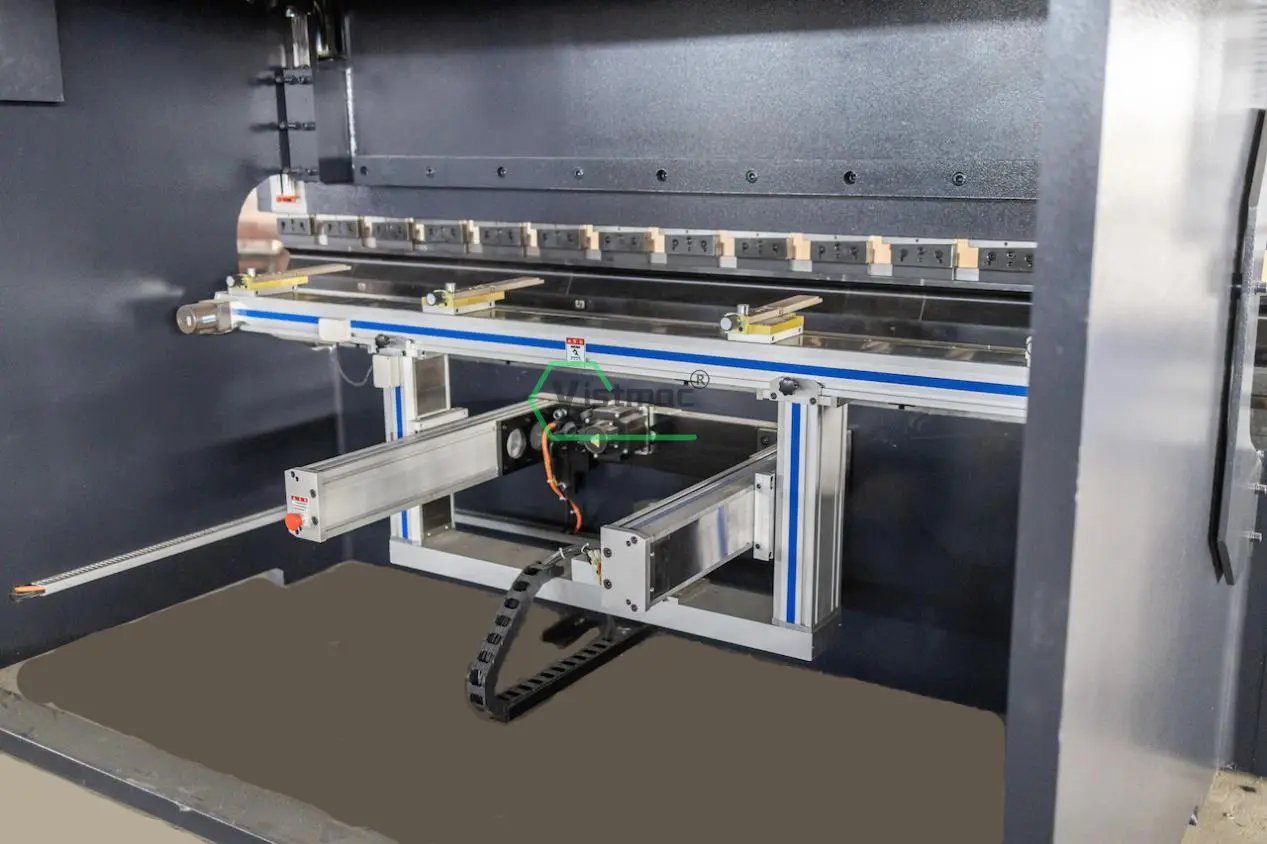
Dies
Press brakes can be utilized for a wide range of forming tasks, provided the appropriate die design is employed. Various types of dies include:
- V-dies: The most commonly used type, featuring bottom dies with different-sized openings to accommodate various materials and bend angles.
- Rotary bending dies: These feature a cylindrical shape with an 88-degree V-notch along the axis, seated in the "saddle" of the punch, with the die acting as an anvil over which the rocker bends the sheet.
- 90-degree dies: Primarily used for bottoming operations, with the die opening dimension depending on the material thickness.
- Acute angle (air-bending) dies: Used in air bending, capable of producing acute, 90-degree, and obtuse angles by adjusting how deeply the punch enters the die.
- Gooseneck (return-flanging) dies: Designed with a punch that allows clearance for already formed flanges.
- Offset dies: A combination punch and die set that bends two angles in a single stroke to create a Z shape.
- Hemming dies: Two-stage dies that combine an acute angle die with a flattening tool.
- Seaming dies: Dies built for producing seams in sheets and tubes, available in various designs.
- Radius dies: Used to create radiused bends with a rounded punch, with the bottom die potentially being a V-die or featuring a spring or rubber pad.
- Beading dies: These create a bead or "stopped rib" to stiffen the part, with the punch having a rounded head and flat shoulders, and the bottom die being the inverse of the punch.
- Curling dies: Designed to form a curled or coiled edge on a sheet.
- Tube- and pipe-forming dies: Used to bend the edges of a sheet into a tube shape, with an initial operation forming the edges and a die similar to a curling die completing the tube.
- Four-way die blocks: A single die block with a V machined on each of its four sides, allowing for easy changeover for small jobs.
- Channel-forming dies: These press a punch into a die to form two angles at the bottom of the sheet, creating an angular channel.
- U-bend dies: Similar to channel forming but with a rounded bottom, often requiring a method to counter spring back.
- Box-forming dies: Used to form boxes with different side lengths, requiring sectional punches that are tall enough to accommodate the box sides.
- Corrugating dies: Feature a wavy surface and may include spring-loaded punch elements.
- Multiple-bend dies: Built to create several bends in a single stroke, matching the desired profile.
- Rocker-type dies: Include a rocker insert in the punch that allows side-to-side motion, in addition to the press's up-and-down motion.
What You Can Do With A Sheet Metal Press Brake
Sheet metal brakes are incredibly useful tools for anyone who works with metal fabrication or repair. They are designed to bend and create a variety of shapes in metals like aluminum, steel, and copper. The sheet metal brake is a versatile piece of equipment that can create a wide variety of products, from simple bends to complex shapes, so what do you need to know about the solution?
Bend Sheets into Simple Shapes
The simplest task that can be performed with a sheet metal brake is to bend sheets into simple shapes. With precision, straight bends can be made to create angles, boxes, trays, covers, and other shapes. This is a great way to create simple products and items that may have been purchased from a store in the past.
Form Complex Shapes
In addition to creating simple shapes, a sheet metal brake can also be used to form complex shapes. These shapes can include compound folds, curves, cones, and cylinders. By combining the correct angles and folds, you can create pieces that are unique and may have many uses.
Customize Automotive Parts
Sheet metal brakes are also ideal for the creation of custom automotive parts. For example, customizing fender flares, engine components, and frame brackets. With the ability to create complex shapes, a sheet metal brake can create precisely what is needed for a given project. And because you are making it yourself, you can save a bit of cash compared to buying pre-made parts.
Create Decorative Items
Sheet metal folds are also the perfect way to create decorative items. Some examples include candle holders, flowerpot stands, and picture frames. While it may seem difficult to create decorative items like this, with the correct equipment and a clear plan, the sheet metal brake makes the creation of such items very easy.
Make Solar Panel Frames
Solar panels require frames that hold them in place. These frames should be sturdy and made of high-quality materials. With a sheet metal brake, you can easily create solar panel frames that are both sturdy and aesthetically pleasing.
As you can see, the sheet metal brake is an incredibly versatile tool. From creating simple shapes to forming complex and decorative items, the possibilities are endless. Its ability to work with a wide range of metals also makes it a valuable tool for anyone in the metalworking trade. So, if you haven't already added a sheet metal brake to your shop, it's time to consider investing in this powerful tool.
Sheet Metal Press Brake Forming: How Does it Work?
If you’ve ever marveled at the intricate bends and folds in a product made of sheet metal, you’ve likely admired the handiwork of a press brake. Looking at the details up close as an amateur can make you wonder how this process is even possible. Well, it’s not magic, it’s science. Here’s how press brake forming works:
The Art of Bending
Simply put, press brake forming is a process used to bend and shape sheet metal. Imagine having a superpower that allowed you bend metal to your will. That’s essentially what you get with the power of this process.
A press brake is a machine pressing tool used for bending sheet and plate material. The process involves placing the sheet metal piece between a punch and a die, which are typically V-shaped. The punch pushes the sheet metal into the die, bending it into a precise shape.
Understanding the Science
So how does this metal-bending process work? It’s all about physics and precision. The key elements here are force and angle. The force applied by the punch causes the metal to bend. The angle of the bend is determined by how deep the punch descends into the die. The result is a precise, clean bend.
Of course, it’s not just about raw power. The precision of press brake forming also depends on factors like the material properties of the metal, the width of the V in the die, and the shape of the punch. Using CNC controls, you can repeat this process over and over again rapidly to efficiently fill a large volume order. Put it all together, and you’ve got a process that combines force, finesse, and a fair bit of science.
Press Brake Forming at Krrass
That’s the magic of press brake forming in a nutshell. This brilliant process has revolutionized the metal fabrication industry, allowing for an astonishing range of shapes and designs, all able to be completed in a more efficient manner when the newest technology is involved.
Ready to see the magic of press brake forming in action? That’s where Krrass in. Our skilled team leverages the power and precision of press brake forming to create tailor-made metal parts for all your commercial needs. If you’re interested in having metal bent to your will, give us a call to learn more.
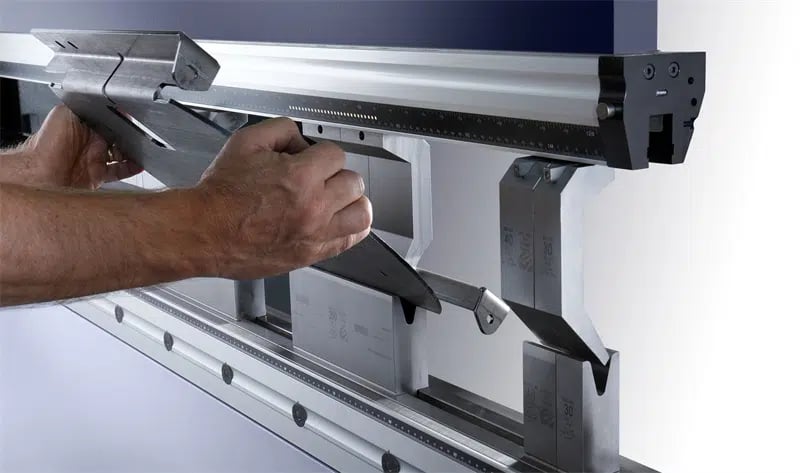
Components and Principles of Press Brake Bending?
The upper or lower die of a press brake machine applies pressure to metal sheets, which causes them to stretch and then shrink. This is called press brake bending.
To understand this technique better, we first need to go through the components and principles involved. Let’s do that!
Basic Components
A press brake is mainly made up of c-shaped frames, a top die or punch, a bottom die, and a hydraulic system. The flow of fluid that moves the top die is controlled by the hydraulic system. This system has tanks, pumps, motors, valves, and pipes. They all work together to move the top die.
The sheet metal press brake’s main body is the c-shaped frame, which holds up the top and bottom dies.
Bending Principles
At the start of bending, the sheet is free to bend. It is put on the bottom die, and the top die bends the metal sheets by applying pressure. The bending force arm and radius of curvature get smaller as the upper or lower die presses on the plate. This makes the plate slowly fit into the V-groove of the lower die.
At the end of the stroke, when the upper and lower dies are fully touching, they make a V-shape. This is basically called bending. Multiple aspects of bending need your attention, and one key principle is checking the straightness and indentation.
To get rid of indentations, operators increase the shoulder radius of the lower die. This process uses an anti-indentation film or an indentation-free lower die. On the other hand, the rigidity of the machine frame (frame design, choice of steel, etc.) determines how straight the bent products are.
Main Press Brake Bending Techniques
Bending metal sheets can be accomplished through four primary techniques: air bending, bottoming, coining, and three-point bending. Each method follows a distinct process and offers unique advantages for different applications. Let's explore these techniques in detail.
Air Bending
Air bending is a widely used technique in metalworking where the metal sheet doesn’t make full contact with the die. Instead, the punch pushes the metal into the die, creating a bend without the sheet touching the bottom of the die.
This method uses an air gap beneath the sheet, with the punch pressing the metal into a V-shaped die. The depth of the punch determines the bend angle. Due to the leverage involved, air bending requires less force compared to other methods.
One of the key advantages of air bending is its adaptability. The same set of tools can be used to create varying bend angles, reducing tool change times and enhancing productivity. Additionally, the lower power requirement extends the life of the machinery.
Air bending is especially popular in hydraulic press brakes due to its flexibility, making it ideal for applications requiring different types of bends. This technique is commonly used in industries like aerospace and automotive, where the ability to quickly switch between different component designs without changing tools is highly valued.
Bottom Bending
Bottom bending involves pressing the metal sheet completely into the bottom of a V-shaped die. The punch forces the metal to conform to the die's shape by fully pressing it against the sides and bottom of the die.
Unlike air bending, bottom bending requires full contact between the metal and the die, though it uses less pressure than coining. This can make achieving the exact bend angle of the die more challenging.
A significant factor in bottom bending is “springback,” where the metal slightly returns to its original shape after being released from the punch. This can affect precision, so operators may need to overbend the material or use specially designed dies with sharper angles to achieve the desired final bend.
Bottom bending is ideal for producing uniform parts with minimal variation, making it a preferred method for projects requiring consistent outcomes and precise dimensions, such as those found in electronics manufacturing.
Coining
Coining is a high-pressure bending technique that deforms, bends, and thins the metal sheet to fit the die perfectly. Originally developed for minting coins, this method requires powerful machinery and precisely designed tools to create high-precision parts.
In coining, the metal is placed between two dies and subjected to intense pressure, which imprints the die's design onto the metal. This process allows for the accurate transfer of intricate patterns and details onto the sheet, making it ideal for applications requiring detailed and precise shapes.
Due to the intense pressure applied, coining creates highly accurate bends with minimal springback, making it suitable for applications where precision is paramount.
Three-Point Bending
Three-point bending is a more recent technique, often considered a specialized form of air bending. This method requires a unique die equipped with a servo motor that allows for precise adjustments to the height of the bottom tool.
During the process, the sheet bends over the radii of the die until it touches the bottom. The bend angle changes as the die's depth is adjusted. To account for variations in sheet thickness, a hydraulic cushion is used between the ram and the upper tool, enabling precise adjustments to within ±0.01 mm. This precision allows for bending angles with an accuracy of less than 0.25 degrees.
While three-point bending offers exceptional flexibility and precision, it is also associated with high costs and limited tool availability. As a result, this method is currently used mainly in niche markets where there is a high demand for highly accurate bends.
Each of these press brake bending techniques offers distinct advantages depending on the application. Whether it's the flexibility of air bending, the uniformity of bottom bending, the precision of coining, or the accuracy of three-point bending, understanding these methods is key to optimizing the sheet metal fabrication process.
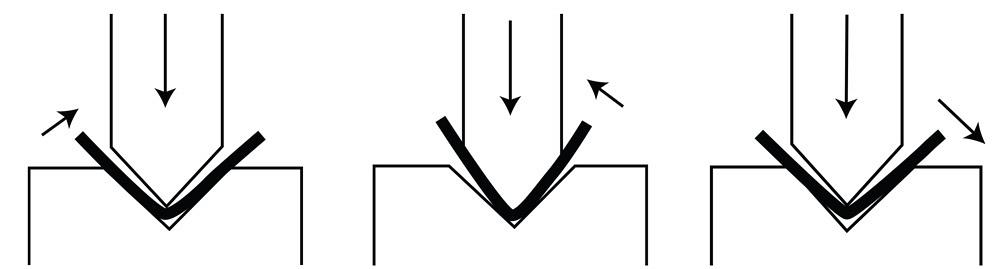
Advanced Technologies in Press Brake Bending
Modern press brakes have incorporated advanced technologies, with CNC (Computer Numerical Control) being a significant innovation. CNC technology minimizes manual operation by allowing tasks to be preprogrammed and controlled via a computer. This advancement offers several key benefits:
Enhanced Accuracy
CNC technology ensures precise control over the bending process, leading to highly accurate and consistent results. The ability to program exact parameters eliminates human error, resulting in superior precision for each bend.
Consistent Repeatability
With CNC, operations are programmed and automated, ensuring uniform outcomes across multiple production runs. This repeatability is crucial for maintaining high-quality standards in manufacturing.
Increased Automation
By automating complex bending tasks, CNC press brakes reduce the need for manual labor. This not only speeds up the production process but also allows for more complex bends to be executed efficiently.
Greater Flexibility
CNC technology allows for easy adjustments to bending settings, accommodating various job requirements without extensive reconfiguration. This flexibility is beneficial for handling diverse production needs and quickly adapting to changes.
Reduced Setup Time
Stored programs in CNC machines streamline setup processes. Instead of reconfiguring the machine for each new piece, operators can load pre-saved programs, significantly shortening setup times and enhancing productivity.
Lower Costs and Reduced Waste
Precision provided by CNC technology minimizes errors, leading to reduced material waste and lower production costs. Accurate bends result in fewer defective parts and less need for rework.
Overall, the integration of CNC technology into press brakes enhances accuracy, efficiency, and flexibility, making it an invaluable tool in modern metal fabrication.
What Material Thickness Can Be Put On a Sheet Metal Brake?
0.2mm to 12mm is the range of thickness but tonnage restricts the length of form the thicker the material.
Advantages of Press Brake Forming
- The CNC press brake is easy to program and operate
- The CNC press brake can be set very quickly from one job to the next.
- It is an ideal process for batch work.
- Very complicated forms and profiles are achievable using standard tooling.
- Replacement/additional tooling is readily available and not costly compared to power press tooling.
- Modern press brake tools are also becoming lighter and simpler to install to speed up manufacturing even more.
- Current machines are also able to produce more unique pieces because of the variety of software designs that can be run through the CNC system.
- 3D graphic representations of the metal bending process allow workers to visualize the process and reorder the machine’s sequence if necessary, without manually refitting all the tools, previously a highly skilled worker’s job.
Disadvantages of Press Brake Forming
- Can only produce one form at a time.
- Not as cost-effective on high volume, regular running work although modern press brakes create better bends much faster with current technology.
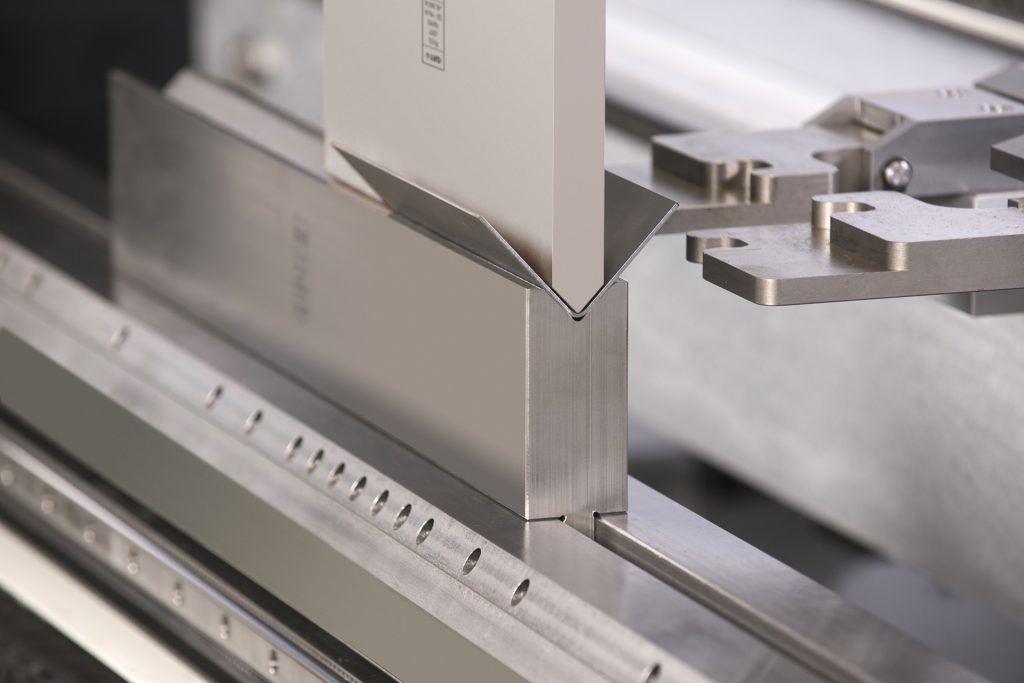
2024 Top 5 Sheet Metal Press Brake Models Recommend
When choosing a sheet metal press brake, you’ll encounter various types, including torsion shaft, electro-hydraulic, hybrid, and electronic models. They also come in different configurations such as CNC, fully automatic robotic systems, and standard variations suited for various scales of production—small, large, and everything in between.
To help you navigate these options, here are the top 5 sheet metal press brakes recommended for 2024, featuring the most popular and high-performing models on the market. These models stand out for their advanced features, reliability, and ability to meet diverse bending needs efficiently.
Model 1: Servo Hybrid Press Brake
With the deep awareness of energy conservation and environmental protection, energy-saving bending machine has attracted much attention. In 2024, the most popular energy-saving bending machine is CNC hybrid servo press brake for sheet metal.
Features and Working Principle
The advanced press brake operates based on the following principles:
- Main Servo Motor: Drives the oil pump, which is crucial for controlling the bending process.
- Numerical Control System: Regulates the flow and pressure of the Y1 and Y2 cylinders via two separate servo bidirectional pump systems.
- Servo Pump Control: Each set of servo pumps manages the oil flow between the upper and lower chambers of the oil cylinders. This setup facilitates the lifting of the upper die and the bending of the sheet metal.
- Bending Operation: When the oil pump reverses, it transfers oil from the lower chamber to the upper chamber, enabling the bending action.
- Synchronization: The left and right sides of the upper die are controlled separately by two sets of servo bidirectional pumps, ensuring precise synchronization.
- Operational Modes: During standby or fast descent, the servo main motor operates at a reduced speed. In low-speed bending, the motor runs at normal speed, and after unloading, the main servo motor accelerates for a rapid return of the slider.
This sophisticated system ensures precise control, efficient operation, and enhanced performance in sheet metal bending tasks.
Advantages
Environmental Protection: Unlike older hydraulic bending machines that used torsion shaft synchronization or valve control, modern CNC hybrid press brakes utilize real servo pump control, eliminating issues of leakage and ensuring eco-friendly operation. They operate extremely quietly, with noise levels as low as 20 dB.
Energy Efficiency: These machines offer significant energy savings, reducing electricity consumption by more than 80-85%. They feature a new design that minimizes floor space, making them compact and space-efficient.
High Precision: The use of servo pump control eliminates the need for synchronization between left and right cylinders, as each servo motor independently controls its own oil pump and cylinder. This setup ensures maximum accuracy and consistent bending results by maintaining a stable hydraulic oil temperature.
High Efficiency: With speeds reaching up to 300 mm/s without vibrations, these press brakes support continuous operation, capable of functioning 24/7.
Enhanced Performance: The machines are designed for stability, reliability, and safety, with a low failure rate. The stable oil temperature prolongs the lifespan of hydraulic components and improves the working environment. Additionally, they can be equipped with multiple axes—up to 6 or more—to handle various workpieces effectively.
Model 2: Electro-hydraulic Press Brake
This kind of press brake has been the highest sales volume on the market in recent years.
Generally, when it comes to CNC sheet metal press brake machine, we all first think of electro-hydraulic synchronous press brakes. Because the electro-hydraulic numerical control press brake machine is the most representative and the most popular model.
Features and Working Principle
The electro-hydraulic synchronous CNC bending machine operates using a computer to manage the synchronization of the machine tool through an electro-hydraulic proportional servo system.
Standard Configuration (4 + 1 Axis):
- Y1 and Y2 Axes: These axes control the oil cylinders on each side of the machine. Y1 manages the left cylinder, while Y2 manages the right cylinder, ensuring synchronized movement of the slider.
- X Axis: Controls the forward and backward movement of the back gauge.
- R Axis: Manages the up and down movement of the back gauge.
- V Axis: Handles compensation for the workbench.
Additional Multi-Axis Options:
- Available configurations include 4, 5, 6, 7, and 8 axes, offering enhanced flexibility and precision to meet various bending requirements.
Advantages
- Operation: Modern technology enhances comfort and efficiency.
- Hydraulic Transmission: Ensures stable and reliable performance with an upward bending design for low noise.
- Smooth Operation: Features a double guide rail structure for smoother slider movement.
- Precision Control: Electro-hydraulic servo system with closed-loop feedback for accurate synchronization.
- Versatility: Capable of eccentric load bending with separate programming for Y1 and Y2, and includes an anti-deformation system for accuracy.
- Customization: Includes pressure holding time at the bottom dead center and slow return control for better workpiece management.
- Upgrade: Offers higher precision, speed, and improved operation compared to traditional hydraulic press brakes.
Model 3: High-speed Mini Press Brake
Although this high-speed press brake is small, its performance is very excellent. Mini high speed sheet metal press brake is very popular in Europe and North America.
Features and Working Principle
The standard electro-hydraulic CNC press brake features two oil cylinders, whereas the mini press brake is distinguished by having only one cylinder. This single-cylinder design results in a more compact structure, smaller volume, and is particularly well-suited for processing small, thin plates.
Servo Control:
- 4-Axis Operation: Utilizes a Mitsubishi control system for precise control.
- Y Axis: Controls the direction of slider travel.
- X Axis: Manages the forward and backward movement of the back gauge.
- R Axis: Regulates the up and down movement of the back gauge.
- Z Axis: Operates two fingers to control the left and right movement of the back gauge.
Advantages:
- High Speed:
- No Load Speed (Quick Down): 150-400 mm/s
- Working Speed (Slow Down): 5-20 mm/s
- Return Speed: 150 mm/s
- Efficiency: Faster operation with enhanced convenience and productivity.
- Design: Features a novel design with high precision and low noise levels.
- Safety: Includes laser protection installed on both sides of the mold for added security.
Model 4: Large Tandem Press Brake
To address the need for processing oversized plates, manufacturers have developed the Large Tandem Press Brake. This model combines two CNC hydraulic press brakes to work in tandem, making it ideal for heavy-duty sheet metal forming and large equipment manufacturing.
Features and Working Principle
- Dual Operation: The two connected CNC bending machines can operate simultaneously or independently.
- Axis Control:
- Y1, Y2, Y3, Y4 Axes: Manage the synchronous up and down movement of four oil cylinders.
- X1, X2, X3, X4, X5, X6 Axes: Control the forward movement.
- X7, X8, X9, X10, X11, X12 Axes: Regulate the push-back function.
- V1, V2 Axes: Handle worktable deflection compensation.
- Z Axis: Operates the motorized side unloading device.
- Axis Control:
Advantages
Automated Unloading: The CNC-controlled side unloading device simplifies operation and boosts efficiency with automatic discharge functionality.
Enhanced Efficiency: Equipped with front and rear pushing devices to handle large workpieces, reducing labor intensity and improving productivity.
Flexible Operation: Two CNC control systems allow for both simultaneous and independent operation of the press brakes.
Adjustable Components: Features adjustable upper and lower dies with anti-indentation capabilities.
Model 5: Automatic Robotic Press Brake
Robotic press brake machine is also known as unmanned fully automatic bending machine for sheet metal. It realizes the bending forming without manual operation by robot gripper and CNC system programming.
With the continuous rise of labor cost, more and more customers consult robotic bending scheme. Many factories are planning to invest in automation equipment and flexible production lines.
Features and Working Principle
A CNC press brake with more than 6 + 1 axes, when equipped with a robot, transforms into an automatic robotic bending machine. This system includes a centering platform, turning bracket, and other essential accessories to facilitate fully automated bending processes.
Advantages
- Reduced Labor Costs and Intensity: Automation minimizes the need for manual labor, leading to cost savings and decreased physical strain on workers.
- Enhanced Safety: The robotic system eliminates many safety risks associated with manual handling.
- Long-term Continuous Operation: Designed for sustained, uninterrupted operation, making it ideal for high-volume production.
- Improved Work Efficiency: Automation streamlines the bending process, resulting in faster turnaround times and increased productivity.
- Consistent Workpiece Accuracy: Robots ensure precise and uniform bending, enhancing the quality and consistency of the finished products.
- Integration with Automation Systems: The robotic press brake can connect with other automation equipment and communicate with industrial MES systems, supporting a seamless unmanned production line.
The above are the most popular and recommended models. Hope to help you in your purchase. Do not follow blindly, do not follow suit! Don’t buy the most expensive, but the most suitable! Please make a rational purchase according to your sheet parameters, processing requirements and purchase budget.
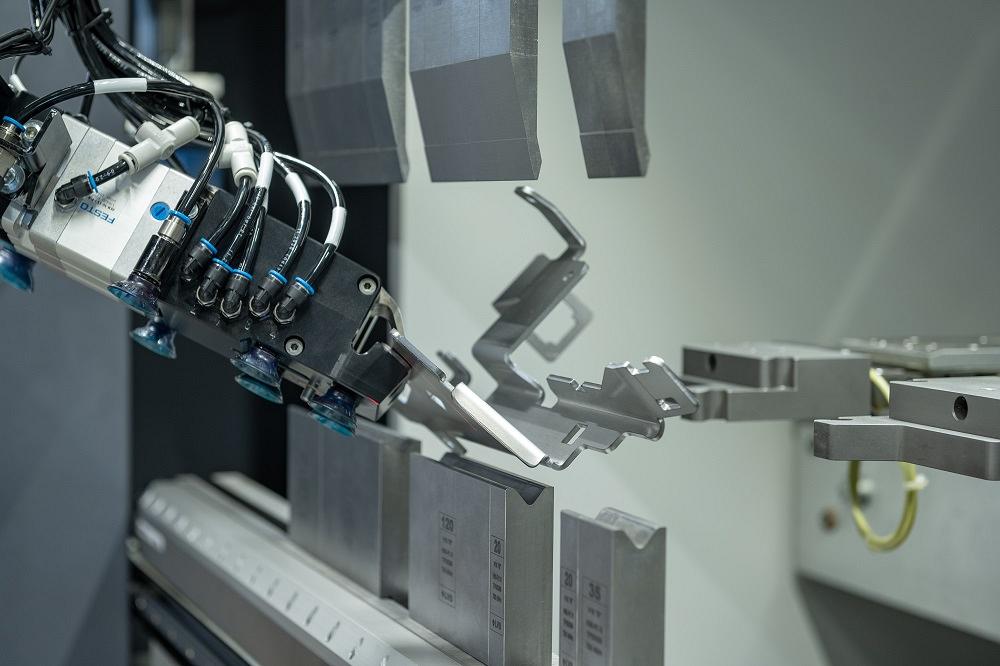
Conclusion
This article presented what is sheet metal press brake, explained it, and discussed purpose and advantages, process and more.In the world of metal fabrication, press brakes are indispensable tools that enable the precise bending and shaping of metal sheets. Understanding the components, types, and working principles of press brakes is crucial for anyone involved in the manufacturing process.
From automotive and aerospace industries to construction and electronics, press brakes play a vital role in shaping the metal components that form the backbone of various products and structures.While challenges such as setup time and operator skill are considerations, the advantages of precision, versatility, and cost-effectiveness make press brakes a valuable asset in the field of metalworking.
As technology continues to advance, press brakes will likely evolve, offering even greater levels of automation, efficiency, and precision in the manufacturing process.
Reviewed by 4 users
I am used to krrass machines. I am not used to other suppliers’ machines.
good quality and best service
Krrass press brake always high quality and professional team support
We have 1 set Servo Hybrid Press Brake and it’s wonderful .