A V grooving machine is a precision tool used to create V-shaped grooves, notches, or channels on various materials. The V grooving machine price can vary significantly depending on factors like specifications, brand, and features. These grooves are essential in the manufacturing process, particularly when preparing materials for bending or folding. Industries such as aerospace, automotive, electronics, and construction rely on these machines for their high accuracy, ensuring that metal sheets, composite panels, and other materials keep their integrity during bending without distortion. Controlled by CNC (Computer Numerical Control) technology, V grooving machines offer high precision and repeatability, ensuring consistent results across different workpieces.
When exploring the purchase of a V grooving machine, understanding the factors influencing its price is crucial. The cost of these machines can vary significantly depending on several factors, such as machine specifications, brand reputation, and regional market variations. Whether you are looking for a budget-friendly option or a high-end model equipped with advanced features, this guide will help you navigate the market and make an informed decision.
What Is a V Grooving Machine?
A V grooving machine is specialized equipment used to create precise grooves in materials such as metal and wood. The V-shaped groove allows materials to be bent at sharp angles without causing damage, ensuring that the material can bend cleanly and accurately. The machine uses a rotary cutting tool to carve out the groove along a predefined path, with depth and angle precision controlled via CNC programming. This makes the process not only more efficient but also essential for industries requiring high precision, such as architectural metalworking and custom cabinetry.
The precision and depth of the grooves play a significant role in both the bendability and the aesthetic finish of the final product. With the ability to create sharp, clean angles, the CNC V grooving process ensures that the final product meets both structural and visual standards. The ability to control the groove’s depth and angle with high accuracy has made it indispensable in high-end metal fabrication.
Applications of V Grooving Machines
Manufacturing Applications
In manufacturing environments where precision is critical, V grooving machines are commonly used to process metal components, precision instruments, and casings. Their ability to control cutting angles and depth during the grooving process ensures product quality and assembly accuracy. This makes them indispensable in industries that require fine machining and engraving, especially in applications requiring meticulous surface detail.
Architectural Decoration
In the field of architectural decoration, CNC V grooving machines are used to process various decorative materials, including aluminum and stainless-steel plates. Horizontal models are often favored in this field due to their ability for deeper cuts and ease of operation. Additionally, vertical V grooving machines are also used for fine engraving and detailing, especially for creating decorative panels with intricate patterns.
Understanding V Grooving Technology
The process of V grooving begins with the creation of a digital design, typically using CAD (Computer-Aided Design) software. Once the groove pattern is designed, CAM (Computer-Aided Manufacturing) software converts the design into a set of instructions known as G-code. These instructions are loaded into the machine’s CNC controller, which drives the machine to cut the grooves as per the specifications.
The workpiece is mounted on a motorized table, and the cutting tools follow the programmed path to carve out the grooves with precision. The machine runs along multiple axes, ensuring that the groove is cut exactly to the design specifications, producing consistent results across different batches.
V Grooving vs. Traditional Grooving Methods
Compared to traditional manual grooving methods or less advanced machines, CNC V grooving technology offers superior precision and consistency. Traditional methods may result in irregular grooves due to human error or mechanical limitations, while CNC technology ensures that every groove is cut according to precise specifications. Furthermore, CNC V grooving allows to produce more complex patterns and intricate designs that would be difficult to achieve with conventional methods, giving manufacturers a greater degree of flexibility and efficiency.
Advantages of V Grooving Technology
- Precision Cutting: CNC technology ensures that V-shaped grooves are cut with consistent depth and angle accuracy, allowing for sharp, clean bends and better material integrity.
- Enhanced Bendability: The grooves ease cleaner and more correct bends along the grooved lines, preventing material deformation like bulging or warping.
- Material Versatility: V grooving applies to a wide range of materials, including various metals such as aluminum, stainless steel, and copper.
- CNC Integration: Automated control ensures precision in the grooving process, reducing human error and increasing operational efficiency.
Classification of V Grooving Machines
V grooving machines can be classified based on their operational features, design, and the applications they serve.
Based on Operation
- Manual Machines: Require direct operator input for each cut.
- Semi-Automatic Machines: Combine manual operation with some automation, such as power feed.
- Fully Automatic CNC Machines: Feature complete automation, allowing for precise, programmable grooving operations.
Based on Design
- Vertical Grooving Machines: Typically designed for tasks requiring fine control of depth and angle, ideal for thicker materials.
- Horizontal Grooving Machines: Suitable for applications requiring effortless operation and higher production speed, often used for materials with smaller thickness.
Horizontal vs. Vertical V Grooving Machines
Both horizontal and vertical V grooving machines offer unique advantages and are suited to different applications.
Horizontal V Grooving Machines
These machines are easier to run, require less training, and are often less expensive. They are particularly well-suited for materials that do not exceed 3mm in thickness. Their simpler design makes them ideal for use in architectural decoration, but they may not achieve the same level of precision as vertical models when managing thicker or more complex materials.
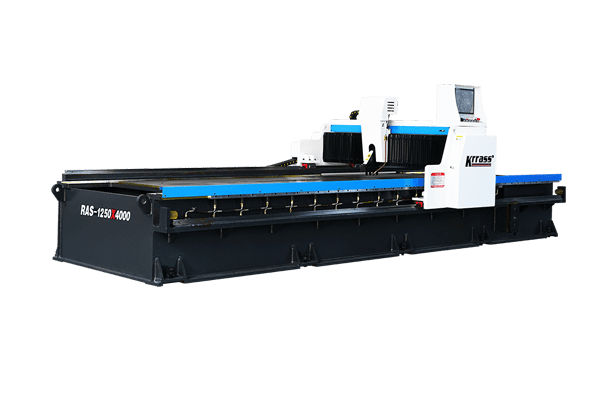
Advantages:
- Low operator skill requirements.
- High cost-efficiency.
- Easy to clean and keep.
Limitations:
- Limited to thinner materials.
- May lack the precision needed for complex tasks.
Vertical V Grooving Machines
These machines are designed for deeper cuts, making them ideal for processing thicker materials. Their vertical structure provides higher stability and precision during operation, ensuring more consistent results.
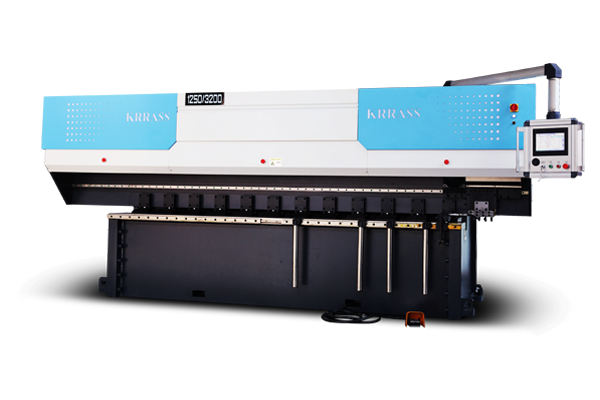
Advantages:
- Capable of handling thicker materials.
- Provides more correct cuts, especially in high-precision applications.
Limitations:
- Higher cost compared to horizontal machines.
- May have cutting depth limitations for certain materials.
Key Components of a CNC V Grooving Machine
To understand how a V grooving machine works, it’s essential to know the key components that contribute to its precision and efficiency:
- CNC Controller: This is the central unit that controls the movements of the machine and the cutting tools. It translates the G-code into machine instructions and allows operators to create complex groove patterns.
- Cutting Tool: Typically made from high-speed steel or carbide, the cutting tool handles creating the V-shaped grooves. The material and sharpness of the tool impact the quality of the groove and the lifespan of the machine.
- Worktable: The motorized table holds the workpiece in place and allows for precise movement during the grooving process. It may include clamping systems for securing the material during operation.
- Spindle: The spindle holds and rotates the cutting tool, and its speed and torque are critical to achieving smooth, correct cuts.
- Clamping System: This part ensures that the material is firmly held in place to prevent movement during machining, which is essential for keeping precision.
- Chip Management System: Efficient chip removal systems, such as conveyors or vacuums, ensure that the work area stays clean and free of obstructions, enhancing the accuracy of the machine’s operation.
- Tool Changer: For increased efficiency, many V grooving machines are equipped with automatic tool changers, allowing for faster transitions between different cutting tools.
Factors Influencing the V Grooving Machine Price
The price of V grooving machine is influenced by several factors, including machine size, technological features, and brand reputation.
- Machine Specifications: Larger machines with greater ability for handling thicker and wider sheets of metal generally command higher prices.
- Material Compatibility: Machines capable of processing a variety of materials, such as stainless steel, aluminum, and copper, are priced higher due to their versatility.
- Precision and Speed: Machines that offer enhanced cutting precision and faster operational speeds are typically more expensive.
- Technological Features: CNC control systems, automation features, and integration capabilities increase the cost of the machine.
- Brand and Manufacturer: Machines from well-known manufacturers with a reputation for quality tend to come at a premium.
Conclusion
Selecting the right CNC V grooving machine is essential for industries that require high precision and efficiency in their fabrication processes. Whether you are considering a budget-friendly choice or an advanced model with extensive capabilities, it is important to weigh factors such as machine specifications, technological features, and overall cost-effectiveness. By understanding these factors, you can make a well-informed decision that aligns with both your immediate production needs and long-term business goals.