Leading industry forecasts show that the global elevator market will reach USD 183 billion by 2030, driven by rapid urbanization and the construction of high-rise buildings. As smart elevators and energy-efficient designs continue to gain popularity, manufacturers face more stringent safety and precision requirements. Complex elevator components demand high-accuracy fabrication processes, which is exactly where fiber laser cutting delivers standout performance.
Why Elevator Manufacturers Switch to Fiber Laser Cutting
- 50% Faster Production Speeds – Accelerate manufacturing timelines to meet rising demand.
- Higher Edge Quality – Eliminate secondary polishing and reduce finishing processes.
- Greater Design Flexibility – Create modern, customized elevator aesthetics with ease.
- Lower Energy and Material Costs – Optimize operational budgets and reduce scrap.
Challenges with Traditional Cutting Methods (Plasma, Punching, Mechanical Shearing)
- Rough edges often require added finishing or polishing.
- Limited flexibility hampers the creation of custom or complex designs.
- Excess material waste leads to higher production costs and inefficiencies.
Fiber laser cutting cuts these issues with unmatched precision, faster throughput, and lower operational expenses.
Key Elevator Components: Enhanced Precision and Efficiency with Fiber Laser Cutting
Key Elevator Components That Benefit from Fiber Laser Cutting
- Elevator Doors – Demand smooth, burr-free edges for seamless operation.
- Control Panels & Button Panels – Require precise, clean cuts for correct part fitting.
- Frames & Support Structures – Need robust, weld-ready surfaces for superior structural integrity.
- Decorative Stainless-Steel Panels – Call for intricate laser cutting and possible engraving.
Fiber laser cutting significantly increases accuracy and material use across all these applications, minimizing rework and ensuring consistent part quality.
Why Fiber Laser Cutting Is the Best Choice for Elevator Manufacturing
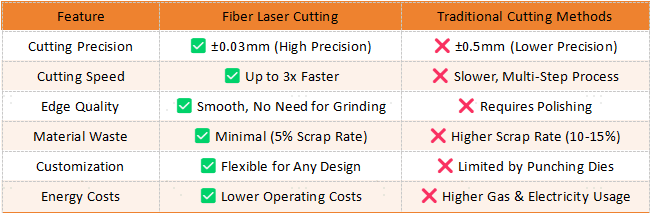
Manufacturers who integrate fiber laser systems see up to 30% savings on material costs and enjoy a 50% boost in production efficiency. KRRASS fiber laser solutions help elevator producers streamline workflows, reduce lead times, and deliver higher-quality final products.
Cutting Capabilities of High-Power Fiber Lasers in Elevator Manufacturing
Experience a major leap in manufacturing productivity with KRRASS’s 12kW laser Cutting Machines.
Increased Cutting Speed
Cut through metal sheets ranging from 1–16 mm thickness at high velocity. This rapid processing accelerates project turnaround, enabling you to complete more orders in less time.
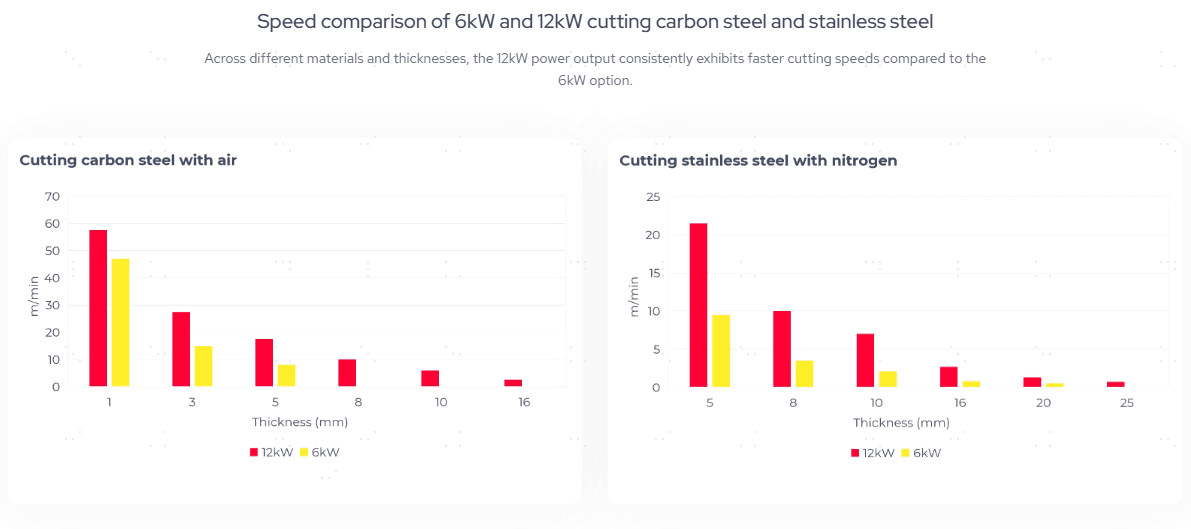
Remarkable Cost Efficiency
KRRASS’s 12kW laser reduces monthly cutting costs by managing more jobs within the same time, which maximizes your operational budget and enhances profitability.
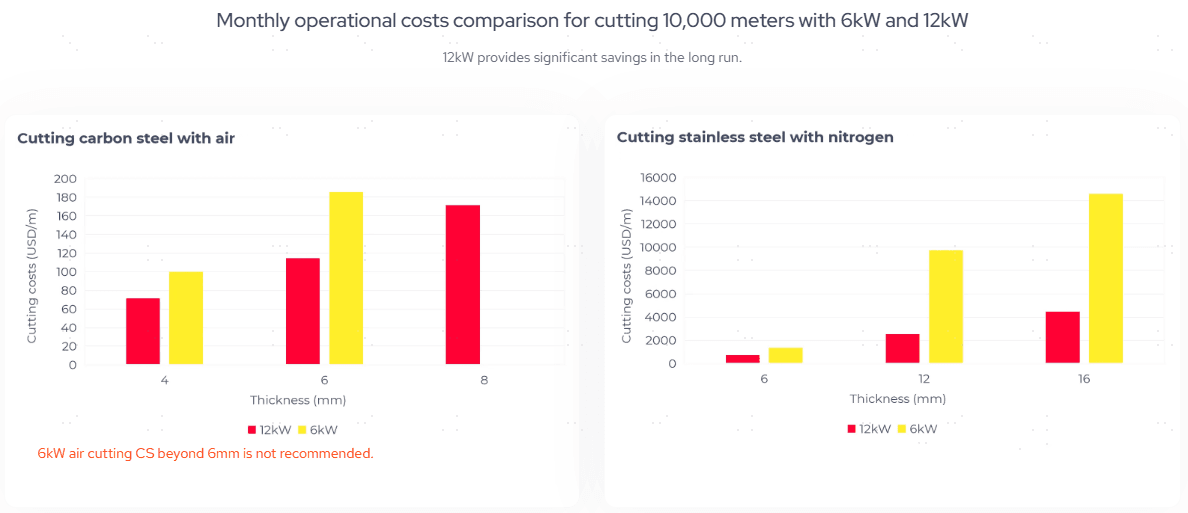
Elevator manufacturers routinely deploy 12kW+ fiber lasers to scale production speed while decreasing overall cutting expenses.
Real-World Success: How an Anonymous Elevator Manufacturer in the UAE Transformed Production with KRRASS Laser
Customer: Anonymous elevator manufacturer in the UAE
This top-tier elevator company needed a high-precision cutting solution to increase production efficiency and reduce post-processing steps. By adopting KRRASS fiber laser cutting machines, they achieved:
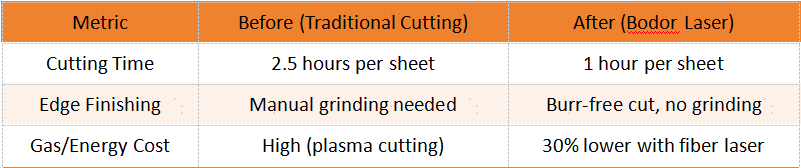
- Remarkable Reduction in Downtime – Streamlined production lines and minimized setup times.
- Enhanced Cut Quality – Consistently smooth edges that virtually cut rework.
- Perfected Operational Costs – Faster turnaround and reduced material waste throughout the manufacturing cycle.
How to Choose the Right Fiber Laser for Elevator Manufacturing
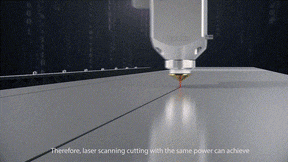
- Material Type & Thickness
Consider stainless steel and aluminum panels. KRRASS’s Scanning Cutting Technology perfects cutting efficiency for reflective materials like aluminum and stainless steel. This advanced approach ensures minimal distortion and preserves surface integrity—ideal for both structural and decorative elevator parts. - Cutting Speed Requirements
Look for high-speed systems when aiming for mass production. The KRRASS Smart Series provides 4G acceleration and ultra-fast piercing, allowing you to reduce cycle times significantly. Intelligent speed optimization keeps cutting consistency across various thicknesses. - Automation Features
Invest in models with automatic loading and unloading systems to keep a seamless workflow. The KRRASS Smart Series supports fully automated material handling, including auto-loading and real-time monitoring. This robust automation lowers labor costs and ensures minimal operator intervention for high-volume production. - Cost-Efficiency
Seek machines with low gas consumption and high energy efficiency. KRRASS’s Remnant Layout Technology uses AI-driven material optimization to maximize sheet use and reduce scrap. Additionally, an advanced nozzle control system helps minimize auxiliary gas consumption, lowering long-term operational expenses.
Looking for high-speed, precise laser cutting for elevator doors and panels?
Contact KRRASS to discover how our fiber laser solutions elevate your manufacturing efficiency.
The Future of Elevator Manufacturing Is Laser-Powered
Fiber laser cutting transforms the elevator industry by offering:
- Faster production and reduced operational expenses.
- Higher precision to improve safety and durability.
- Lower material waste and enhanced energy efficiency
Manufacturers looking to increase productivity, uphold rigorous quality standards, and meet ever-changing market demands choose fiber laser cutting as the ultimate solution.
Future-Proof Your Elevator Manufacturing with KRRASS Laser.