As you browse through fabrication magazines, you'll notice that high power fiber laser cutters dominate the advertisements and press releases. But why is the industry so focused on higher power levels in laser cutting?
Back in 2015, 4kW fiber laser cutters were commonly used in OEMs and job shops across North America. By mid-2019, however, the trend shifted toward machines with 6kW or more. Today, high power fiber laser cutters account for approximately 80 percent of KRRASS's laser-cutting sales. With all the benefits high power brings, it's easy to understand why fabricators are increasingly turning to these advanced laser cutting solutions.
High Power Translates to High Yields
Using higher power levels in laser cutting offers significant productivity and quality benefits, such as an extended cutting range, faster cutting and piercing speeds, and improved edge quality on parts.
Extended High Power Fiber Laser Cutter Range
One common perception is that higher power enables cutting thicker materials, which is true across all material types. For instance, the Smart 12kW laser can cut through 1.00" mild steel, 1.25" stainless steel, and 1.25" aluminum.
Beyond cutting thicker materials, high-power lasers allow for a broader range of cutting applications using nitrogen and high-pressure compressed air. These gases not only speed up cutting but also yield clean, paint-ready parts that eliminate the need for secondary cleaning.
For example, with 12kW power, nitrogen cutting extends the mild steel cut range to ½", and compressed air also yields impressive results. Laser technology application experts at KRRASS, notes, “A 6kW fiber laser can cut ¼" mild steel using compressed air, but a 12kW laser can increase that capacity to 3/8" with compressed air.” High-power air cutting also significantly enhances cut quality.
Additionally, compressed air cutting can reduce consumable costs, as air is much more affordable than nitrogen. Experter explains, “Interest in air cutting has been steady among our 6kW fiber customers, but those purchasing 6kW or higher are all utilizing air.”
An extended cutting range is only one facet of the high-power laser-cutting advantage.
Increased Cutting Speeds and Piercing Speeds
High-power fiber lasers deliver faster cutting speeds, significantly boosting throughput. These speed advantages are especially evident when cutting mid-range materials, such as those between 1/8" and 1/2" thick, using either air or nitrogen.
For example, as shown in Figure 1, a 10kW fiber laser cuts a 3/16" aluminum part 233% faster than a 4kW fiber laser. For those who work with mild steel, see Figure 2 for a similar comparison.
While single-part cutting speed is noteworthy, a more practical reference is the total time required to run a complete sheet (nest). Nesting times include piercing, power ramping around corners, and additional movements that impact the overall cut time. In the 5' x 10' nest of 3/16" aluminum, shown in the right side of the photo, the 4kW laser took 40 minutes and 53 seconds to complete the cut. In contrast, the 10kW laser finished the same nest in just 28 minutes and 57 seconds—nearly enough time saved to cut an additional half sheet compared to the 4kW laser. A similar efficiency boost is observed with mild steel, as illustrated in Figure 2.
Enhanced piercing techniques also maximize the speed of high-power lasers. According to experter, “A 6kW laser pierces 1" mild steel in 3 seconds, but with a 10kW laser, it takes under a second to pierce the same material. This time savings is critical in full-nest cutting, where multiple piercings or feature-rich parts can dramatically reduce total cutting time.”
While speed and throughput are essential, achieving high-quality part edges is equally important.
Enhanced Edge Quality
Since the advent of fiber laser technology, improving edge quality has remained a priority. Fabricators, accustomed to the exceptional edge quality provided by CO₂ laser machines, now expect similar standards from solid-state laser technology.
With higher power levels in fiber lasers, part edge quality is significantly enhanced, approaching the smoothness and cleanliness of CO₂ laser-cut parts. The combination of high power and high speed minimizes dross formation, resulting in smoother, cleaner edges across the entire cutting range.
So, which laser-cutting applications benefit the most from these high-power advantages?
Ideal Applications
With faster cutting speeds in mid-range materials, an extended cutting range, and improved part quality, high-power fiber laser machines are well-suited for high-volume OEM applications and high-performance job shops.
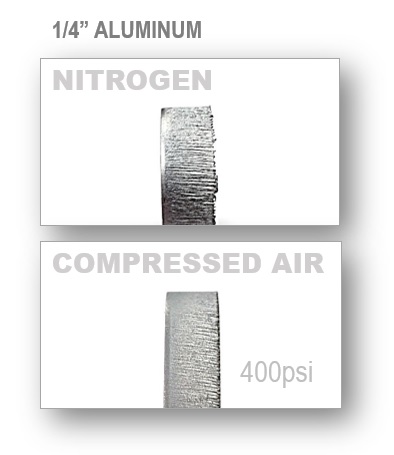
Applications with longer run times particularly benefit from the faster cutting rates of high-power lasers, especially those involving parts with numerous holes or intricate details requiring extensive piercing.
High-power laser cutting also excels with thicker aluminum parts. When combined with compressed air, high-power laser cutting delivers a superior, smoother edge with minimal dross.
For specific application consultation, please consult KRRASS sales consultants and managers.
Conclusion
In summary, high-power lasers deliver an extended cutting range, the capability to cut thicker materials with nitrogen and compressed air, increased cutting speeds, faster piercing, and enhanced part edge quality. These advantages collectively boost laser-cutting throughput and reduce the cost per part.