Hey there! If you're in the industry like I am, you know how crucial it is to understand hydraulic guillotine shear blades to maximize the efficiency of your machines. In this article, I’ll share key insights about these essential components, covering everything from their design and material choices to handy maintenance tips. Whether you're a seasoned professional or just starting out, this guide will help you make informed decisions for your projects.
Introduction
The blade material of a shearing machine usually includes T10, 9CrSI, 6CrW2Si, Cr12MoV, H13, alloy steel, and other materials. These blades are widely used in various industries such as light industry, aviation, shipbuilding, metallurgy, instrumentation, electrical appliances, stainless steel products, and steel structure construction and decoration.
A shearing machine works with a moving upper blade and a fixed lower blade. By using the right blade gap, it applies shearing force to metal sheets of different thicknesses, making them break and separate into the desired size. Shearing machines are a type of forging machinery, used in the metal processing industry. Generally, shearing machines can be divided into pedal type (manual), mechanical type, hydraulic swing type, and hydraulic brake type.
They are often used to cut blanks with straight edges. The shearing process should meet the straightness and parallelism requirements of the cut sheet's surface and minimize distortion to get a high-quality workpiece.
Material
The materials for shear blades fall into three main categories: carbon-bonded tool steel, low alloy tool steel, and alloy tool steel.
- Carbon-bonded tool steel: We usually choose 65, 75 steel, T8, T10, etc. for carbon-bonded steel. The heat-treated hardness of blades made from this material is around HRC57 - 59 degrees. It is great for ordinary low-carbon cold-rolled plates and regular A3 plates. And when it comes to recycling and cutting waste materials, it is cost-effective with a reasonable price.
- Low-alloy tools: The common blade materials for low-alloy tool steel are 6Crw2sI, Cr5Mo1V, 9CrSi, Cr12MoV, etc. The blade hardness after heat treatment is in the range of HRC58 - 62 degrees. It is specially designed for cutting stainless steel and is suitable for hot-rolled plates and medium to thick stainless-steel plates.
- Alloy tool steel: The shear blade materials of alloy tool steel include 4Cr5MoSiV1 (H13K), 7Cr7Mo2V2Si9 (LD), W6Mo5Cr4V2 (6542), H13, etc. Blades made of this material are used for hot-rolled steel billets and hot-cutting medium and thick steel plates. They are high-temperature resistant and do not anneal easily, making them perfect for hot rolling and hot shearing processes in steel mills.
Instructions
- Start the shearing machine and let it idle for a few cycles to make sure everything is normal. Then, do some evaluate cuts with different thicknesses, starting from thin to thick. This way, you can get familiar with the blade performance of the hydraulic guillotine shearing machine.
- Remember to adjust the blade gap according to the plate thickness during trial cutting. If you do not, it will affect the blade's durability.
- Turn on the pressure gauge switch while cutting and keep an eye on the oil pressure value. When cutting a 12mm plate, the pressure should be less than 20MPa. The remote pressure regulating valve No9 is set to 20 - 22MPa at the factory, and you must follow this rule. Do not increase the pressure to cut materials beyond the specified surface, or you might damage the machine.
- Listen for a balanced sound during operation. If there's noise from the blades of the hydraulic guillotine shearing machine, stop and check it out.
- When the hydraulic guillotine shear blade is working, make sure the maximum temperature of the oil tank is less than 60 degrees. If it exceeds that, shut down the machine and let it rest.
Safe operating
- Before you start operating, put on tight-fitting protective clothing and fasten your cuffs. Do not leave your jacket hem open. Also, do not wear, take off, or wrap your clothes around the machine to avoid getting twisted. Always wear a safety helmet, and if you have braids, tuck them into the hat. No skirts or slippers allowed!
- The operator of this machine tool must be well-versed in the main structure, performance, and usage of the hydraulic guillotine shear blade.
- This machine tool is designed to cut various steel plates, copper plates, aluminum plates, and non-metallic material plates with the rated thickness of the machine. The materials should be free of hard marks, welding slag, slag inclusions, and welds. Also, do not use materials that are too thick.
- Here is how to use the blades of the hydraulic guillotine shearing machine:
- Adjust the blade gap based on the thickness of the material you are cutting.
- Adjust the profiling or fixture according to the width of the material.
- Make 1 - 3 idle strokes before starting the machine, and then you can start cutting when everything is normal.
- If you notice any abnormal operation during use, immediately cut off the power and shut down the machine for inspection.
- When adjusting the machine tool, always cut off the power supply. And when moving the workpiece, be careful of your hands.
- Keep all parts of the machine tool lubricated regularly. The operator should fill the lubricating oil once per shift, and the mechanic should lubricate the rolling bearing part every six months.
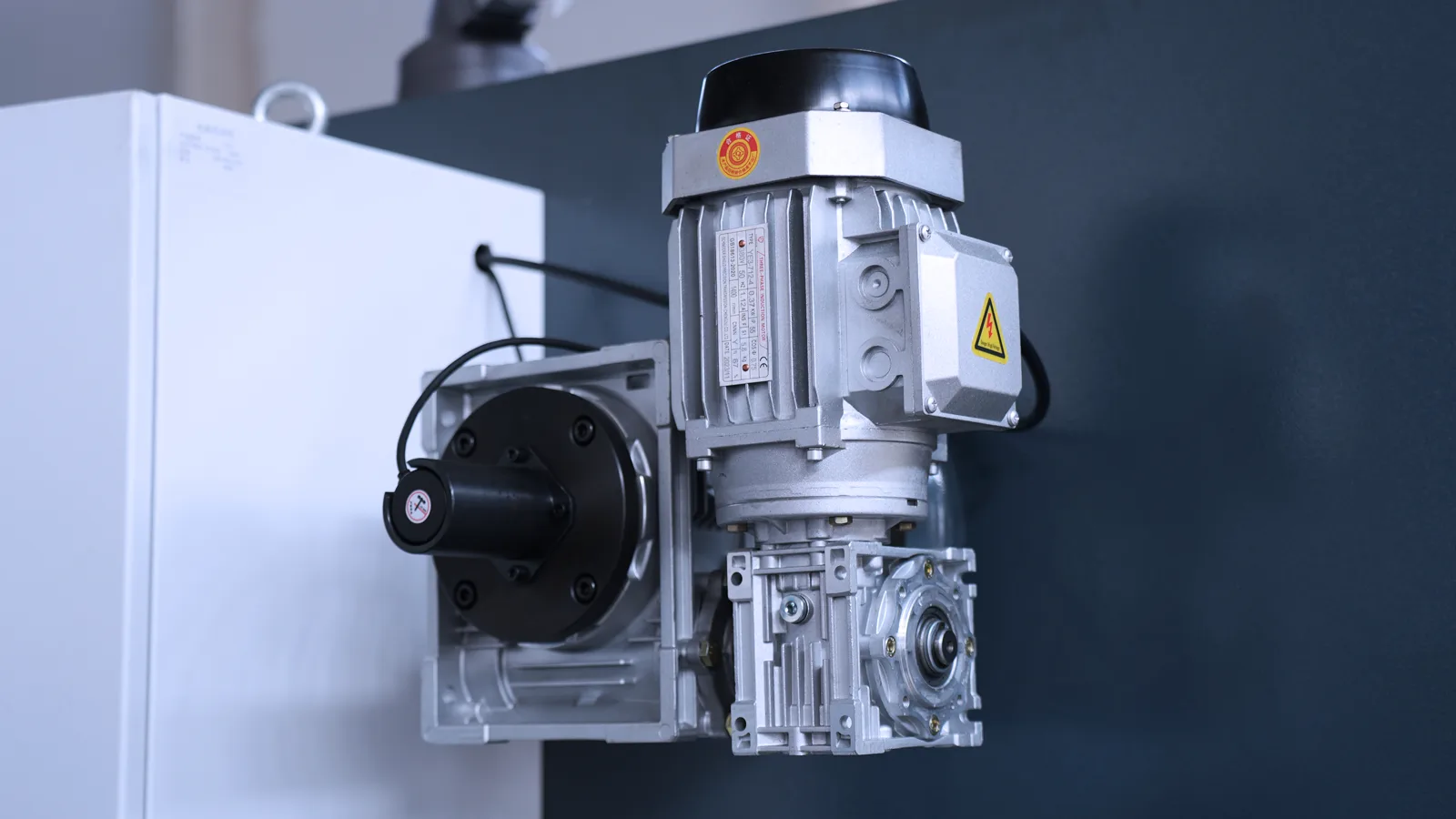
Maintenance
Taking diligent care of the shear blade not only extends its life but also makes your work easier. Here is how to maintain the shear blade:
- Always follow the operating procedures.
- Add lubricating oil as per the lubrication chart before starting the machine each time. Make sure the oil is clean and free of any sediment.
- Keep the shear blades clean regularly. Apply anti-rust grease to the unpainted parts.
- Replace and refill the lubricating oil in the motor bearing regularly. Also, check the electrical part regularly to ensure it operates normally, safely, and reliably.
- Check if the triangle belt, handle, knob, and button of the shearing machine blade are damaged. If the blade is severely worn, replace it in time and report for spare parts.
- Inspect and repair switches, insurances, and manages regularly to ensure reliable operation.
- Lubricate and scrub the machine tool 10 minutes before you finish work every day.
- Only designated personnel are allowed to operate the equipment. And make sure to stop the machine when you are not using it.
- Select the shearing gap wisely according to the board thickness.
- Keep the board free from impurities and hard objects.
- Avoid cutting and welding old boards.
- Do not overdo the shearing of thick plates. Adjust the gap between the upper and lower blades regularly.
Application
Small and medium-sized CNC shearing machine blades are used in hydraulic guillotine shearing machines, hydraulic pendulum shearing machines, mechanical shearing machines, pedal shearing machines, and other forging machine tools. They are commonly used in sheet metal processing, light industry, electrical appliances, metallurgy, instrumentation, shipbuilding, aviation, stainless steel products, steel structure construction, and decoration industries. You can find them widely used in major fields like the metallurgical industry, packaging industry, paper industry, printing industry, carton industry, garden wood industry, rubber and plastic industry, food industry, electronic materials, shipbuilding, construction and repair, automobile manufacturing, and mechanical equipment.