As companies seek ways to streamline operations, reduce costs, and improve production output, modern hydraulic press automation has emerged as a game-changer. By integrating advanced technology with traditional hydraulic presses, manufacturers can unlock new levels of productivity, precision, and safety. This comprehensive guide will explore the benefits, components, and strategies for maximizing efficiency with hydraulic press automation.
Hydraulic Press Definition
A hydraulic press is a machine that uses a hydraulic cylinder to generate a compressive force. It operates on the hydraulic equivalent of a mechanical lever and is often referred to as a Bramah press, named after its inventor, Joseph Bramah, an Englishman who patented the device in 1795. Bramah, also known for his development of the flush toilet, applied his knowledge of fluid dynamics to design this press.
Basic Principle
The operation of a hydraulic press is based on Pascal's principle, which states that pressure is uniform throughout a confined fluid. The system consists of two pistons: one small piston with a small cross-sectional area that applies a moderate force, and a larger piston that generates a much greater force. Because of the way the system works, only small-diameter tubing is necessary for the pump, as it can easily withstand the pressure. The pump is typically separate from the press cylinder.
Applications
Hydraulic presses are widely used in manufacturing processes, including assembly, disassembly, and the shaping of tightly fitting components. They are essential in operations like forging, clinching, molding, blanking, punching, deep drawing, and metal forming. Other uses include stretch forming, rubber pad forming, and powder compacting. Hydraulic presses are valued for their ability to produce intricate shapes efficiently while saving materials. They also require less space compared to mechanical presses of similar capacity.
In geology, tungsten carbide-coated hydraulic presses are employed in rock crushing, especially for preparing samples for geochemical analysis in fields like volcanology.
Ideal for Hand-Fed Work
Mechanical presses are often faster in automatically fed, short-stroke and short-feed-length blanking operations. Despite the automation trend, a majority of jobs are still hand-fed, and the lot sizes of many jobs simply are too small to justify the expense of automatic feeding. With markets changing so rapidly, many manufacturers are reluctant to make large investments in automatic-feeding equipment. Just-In-Time (JIT) manufacturing has further increased the amount of short runs. With hand feeding remaining a primary feed method, hydraulic presses offer competitive advantages on this type of work.
Hydraulic-press users, especially those used to the highly critical job of setting the stroke for a mechanical press, are often amazed at how quickly they can change dies and start a new job. Hydraulic presses eliminate the difficult, time-consuming stroke-setting task. Because a hydraulic press maintains full tonnage throughout the entire length of a stroke, there is no need to determine the exact location of maximum tonnage.
Given such advantages, on hand-fed jobs, the floor-to-floor or bench-to-bench time often is the same for mechanical and hydraulic presses. As a result, their faster setups and increased uptime make hydraulic presses more productive than mechanical presses.
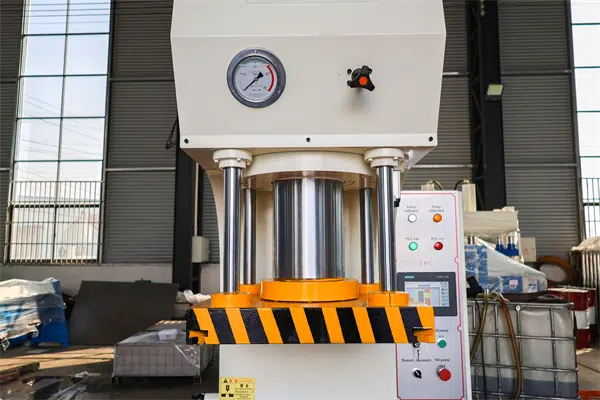
Making Inroads in High-Volume Work
Besides being ideal for lower-volume hand-fed stamping jobs, hydraulic-press lines also are finding increased use on high-volume work, inside and outside of the metal-stamping industry. Examples include:
- Electric-motor manufacturers assemble motor shafts to rotors, compress laminations and press cores into housing.
- Automotive manufacturers press tiny shafts into water pumps, assemble shock absorbers, blank and form diaphragms and stake disc brakes together.
- Jewelers coin Boy Scout and other organization pins.
- Frozen fish blocks are shaped for more efficient processing.
- Aircraft companies form tough titanium housings.
- Tuba bells and cymbals are shaped in huge forming presses.
- Hardened road-grader blades and machine ways are straightened.
- Hollow-ware manufacturers blank and draw brass bowls automatically from coiled stock.
How the Hydraulic Press works
Since the hydraulic press works on the basis of Pascal's Law, its working is similar to the one of the hydraulic system. A hydraulic press consists of basic components used in a hydraulic system that includes the cylinder, pistons, the hydraulic pipes, etc.The working of this press is very simple. The system comprises of two cylinders, the fluid (usually oil) is poured in the cylinder having a small diameter. This cylinder is known as the slave cylinder.
The piston in this cylinder is pushed so that it compresses the fluid in it that flows through a pipe into the larger cylinder. The larger cylinder is known as the master cylinder. The pressure is exerted on the larger cylinder and the piston in the master cylinder pushes the fluid back to the original cylinder.
The force applied on the fluids by the smaller cylinder results in a larger force when pushed in the master cylinder. The hydraulic press is mostly used for industrial purposes where a large pressure is required for compressing metals into thin sheets. An industrial hydraulic press uses the material to be worked upon along with the help of the press plates to crush or punch the material into a thin sheet.
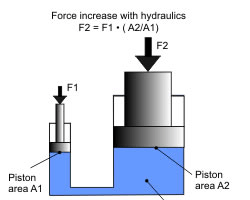
In Popular Culture
The concept of a hydraulic press has made its way into various forms of popular culture. For example, in the film Fermat's Room, a room with a design similar to a hydraulic press plays a key role in the story. Additionally, the artist Boris Artzybasheff created an illustration of a hydraulic press in which the press itself takes the form of a robot.
In 2015, Lauri Vuohensilta, a factory owner from Tampere, Finland, launched the Hydraulic Press Channel on YouTube. The channel, which showcases objects being crushed under a hydraulic press, quickly gained popularity and now boasts over 9 million subscribers. Many other YouTube channels have followed suit, publishing videos of hydraulic presses crushing a wide variety of items, such as bowling balls, soda cans, plastic toys, and metal tools.
The hydraulic press also makes a notable appearance in the Sherlock Holmes story The Adventure of the Engineer's Thumb, where it plays a central role in the plot.
Types Of Hydraulic Press
There are many different types of hydraulic presses catering to the various requirements of industries. Some of them are as follows:
• Arbor presses: These presses are usually used when the work involved is not of a heavy- duty nature. These presses come in a variety of sizes and specifications. But compared to other hydraulic presses, they do not compress large amounts of pressure required to generate more output. Arbor presses are used in processes like piercing holes into metals, stamping, to flatten metals, tearing, marking inscriptions, etc.
• Laminating presses: Unlike other hydraulic presses that are operated automatically, these presses make use of manual labor. Laminating presses have two openings that are known as plates. One is used for heating whereas the other is used for cooling. This makes the lamination process comparatively faster. Through these presses, materials like polymer can be laminated onto paper and metal. In case of laminating presses, the plates are usually heated with oil or through electricity. A laminating press is also used for common uses such as laminating the identity cards, certificates and even book covers. In this way, laminating presses facilitates fast and easy lamination for industrial and domestic needs.
• C- frame presses: These presses have a 'C' like shape, which is specifically designed to maximize the floor space for the workers in order to move around easily at the workplace. Unlike other presses that have multi-processes, the C- frame presses only include a single press application. Its application includes straightening, drawing and mostly includes assembling work. C- frame presses come in a variety of weights. The C- frame presses are also available with extra features such as wheel stands and pressure gauges.
• Pneumatic presses: These presses are the most basic hydraulic presses used in industries because they compress the air to create a pressure in order to gain movement. The advantage of pneumatic presses is that the operations are performed fast whereas the disadvantage of this press is that it cannot create extremely high pressures, as other hydraulic presses are able to create. The pneumatic presses are often used in car and aircraft brakes system. The industrial uses of pneumatic presses would include assembling, drawing, punching, etc. A pneumatic press usually requires a full time operator and for the sake of his safety, additional safety accessories such as electrical safety devices are also included.
• Power presses: These presses are used in large industries that demand the use of heavy machinery and equipments. There are 2 kinds of power presses on the basis of the type of clutch used. They are full revolution and part revolution clutch. In case of a full revolution clutch, the clutch cannot be disrupted until and unless the crankshaft makes a full revolution. In case of part revolution, the clutch can be disrupted at any time, before or after the full revolution. Power presses involve a lot of danger because of the heavy operations associated with it. A lot of safety measures are taken while using power presses.
• Assembly presses: These presses use the extreme pressure generated by the pistons and the hydraulic fluids to assemble and maintain the parts.
• H- frame presses: These presses have a peculiar 'H' shape and are capable of handling more that one press application.
Safety Measures
As of today, hydraulic presses are available in both the categories, i.e., automatic and manually operated. In case of manually operated hydraulic presses, many safety measures have to be taken such as using interlocking and barrier guards.
Benefits Of the Hydraulic Press
Unlike their mechanical counterparts, hydraulic presses can compress any material to a full extent. Also, hydraulic presses take only half of the space that the mechanical ones take because they have the ability to compress a large pressure in a cylinder having a less diameter.
Understanding Hydraulic Press Automation
Hydraulic presses have long been a staple in industries that require heavy-duty material processing, from metal forming to plastic molding. Traditional presses rely on manual or semi-automated controls, which can limit efficiency and introduce variability. However, automation takes these machines to the next level by integrating cutting-edge technology to handle repetitive tasks, optimize processes, and improve output accuracy.
Modern hydraulic press automation refers to the use of programmable systems, sensors, and robotics to control the operation of the press. Automated presses can be tailored to perform specific tasks with greater speed and consistency, making them ideal for high-volume production environments.
Benefits of Hydraulic Press Automation
Integrating automation into hydraulic presses offers numerous advantages that translate to improved operational efficiency:
a. Increased Production Speed
Automated hydraulic presses can operate faster than manually controlled machines, drastically reducing cycle times. Automation eliminates the need for human intervention in repetitive processes, allowing the machine to continuously operate at its maximum capacity.
b. Improved Accuracy and Precision
Automation reduces human error, resulting in more consistent and precise outputs. With programmable logic controllers (PLCs) and computer numerical control (CNC) systems, the press can be finely tuned to perform the same task with exact precision every time, which is critical in industries like aerospace, automotive, and electronics.
c. Enhanced Safety
Safety is a top priority in any manufacturing environment, and hydraulic press automation reduces the risk of injury by removing operators from hazardous areas. Automated presses are equipped with sensors, safety guards, and emergency stop functions that ensure safe operation and prevent accidents.
d. Lower Operational Costs
Although the initial investment in automation may be significant, it ultimately leads to reduced labor costs, fewer material wastages, and minimized downtime. Automated presses require less human intervention, which allows workers to focus on higher-value tasks, thus improving overall operational efficiency.
e. Better Data Collection and Monitoring
Automated systems allow for real-time data collection and monitoring of press operations. Sensors and software provide insights into performance metrics like cycle time, tonnage, and machine wear, enabling proactive maintenance and reducing the risk of unplanned downtime.
Key Components of Hydraulic Press Automation
To fully understand how automation maximizes efficiency in hydraulic presses, it’s important to break down the key components that make it possible.
a. Programmable Logic Controllers (PLCs)
PLCs are the brains behind hydraulic press automation. These digital computers control and monitor the machine’s operations by receiving input from sensors and executing pre-programmed instructions. PLCs can be programmed to manage various press functions, such as adjusting pressure, regulating cycle time, and ensuring safety protocols.
b. Human-Machine Interface (HMI)
An HMI is the visual interface through which operators can interact with the hydraulic press. Modern HMIs provide intuitive touchscreens where operators can monitor the machine’s status, configure settings, and access real-time data. The HMI simplifies machine control and enhances operator convenience.
c. CNC Systems
Computer Numerical Control (CNC) technology is often integrated with hydraulic presses to provide precise control over the machine’s movements and operations. CNC systems ensure that tasks like metal bending or stamping are performed with high accuracy, reducing waste and ensuring consistent results.
d. Sensors and Actuators
Sensors play a crucial role in monitoring machine performance, detecting anomalies, and ensuring the safety of the press. Common sensors include pressure transducers, proximity sensors, and limit switches. Actuators are responsible for converting electrical signals into mechanical movements, ensuring that the press operates smoothly and precisely.
e. Robotics and Material Handling Systems
Robotics can be integrated into hydraulic press automation to handle tasks such as loading and unloading materials. Automated material handling systems reduce manual labor, speeding up the production process and minimizing the risk of injury. Robots are particularly useful in high-volume production environments where consistency and speed are critical.
f. Safety Systems
Automated hydraulic presses come with advanced safety systems, including light curtains, safety mats, and emergency stop buttons. These systems prevent the press from operating when an operator is in a dangerous position and can halt the machine instantly in case of an emergency.
Steps to Maximizing Efficiency with Hydraulic Press Automation
To fully benefit from hydraulic press automation, manufacturers should implement the following strategies to optimize efficiency:
a. Evaluate Your Production Needs
The first step in maximizing efficiency is understanding your production requirements. Analyze your current operations to identify bottlenecks, inefficiencies, and opportunities for improvement. Consider factors such as production volume, material type, and cycle time when determining the level of automation required.
b. Choose the Right Automation Technology
Not all hydraulic presses are created equal, and the level of automation needed will vary depending on your specific application. For instance, a CNC press brake may be ideal for precision bending tasks, while a fully automated stamping press may be better suited for high-speed production. Work with your machine provider to select the right automation solution for your needs.
c. Integrate Data Monitoring and Analytics
Data collection and analysis are key to maximizing efficiency. Equip your automated press with sensors and software that can provide real-time data on performance metrics such as cycle time, pressure, and wear. Use this data to identify trends, optimize machine settings, and schedule preventive maintenance.
d. Train Operators on Automation Systems
Even though automated presses require less human intervention, operators still need to understand how to interact with the machine’s systems. Ensure that your team is properly trained on how to use the HMI, monitor the PLC, and troubleshoot common issues. Well-trained operators can quickly identify and resolve potential problems before they lead to costly downtime.
e. Prioritize Preventive Maintenance
Automation doesn’t eliminate the need for regular machine maintenance. In fact, with the increased speed and precision of automated presses, maintenance becomes even more critical. Implement a preventive maintenance schedule based on the data collected from sensors and analytics to reduce wear and tear on components and extend the lifespan of the press.
f. Focus on Safety
While automation improves safety by reducing human interaction with the press, it’s still essential to prioritize safety protocols. Regularly inspect and test safety systems, ensure that emergency stop functions are in place, and conduct periodic safety training for operators.
Common Challenges and Solutions in Hydraulic Press Automation
While hydraulic press automation brings numerous benefits, it also comes with its challenges. Understanding these challenges and knowing how to address them can further enhance efficiency.
a. High Initial Investment
Automating a hydraulic press can involve significant upfront costs, including the purchase of new equipment, software, and integration services. However, the long-term benefits of increased productivity, reduced labor costs, and improved output quality often outweigh the initial investment.
b. Integration with Existing Systems
For manufacturers with legacy equipment, integrating new automation technology with existing hydraulic presses can be challenging. Working with a knowledgeable automation provider can help ensure a smooth transition, and in some cases, retrofitting older machines with modern automation systems is a viable option.
c. Downtime During Implementation
Implementing automation may require temporary downtime as the new system is installed, programmed, and tested. Proper planning, training, and testing can minimize this downtime and ensure a smooth rollout.
The Future of Hydraulic Press Automation
As industries continue to embrace Industry 4.0, the future of hydraulic press automation looks promising. Innovations such as IoT integration, AI-driven predictive maintenance, and energy-efficient designs are poised to further enhance the performance of automated hydraulic presses. By adopting these technologies, manufacturers can stay ahead of the competition and continue to push the boundaries of efficiency.
Conclusion
Hydraulic press automation represents a significant leap forward for manufacturers seeking to maximize efficiency, improve output quality, and enhance safety. By integrating PLCs, CNC systems, sensors, and robotics into hydraulic presses, businesses can streamline their production processes and achieve higher levels of consistency and precision. Although there are challenges in implementing automation, the long-term benefits are clear. With proper planning, training, and maintenance, manufacturers can unlock the full potential of modern hydraulic press automation and position themselves for success in an increasingly competitive market.