Hey there! The hydraulic press brake machine is a real workhorse in the sheet metal fabrication world. You've got different kinds, like the manual one, mechanical, CNC, electro-hydraulic synchronous, and electric press brakes. But nowadays, the hydraulic press brake machine, especially the CNC version, also called the electrical hydraulic servo press brake, is stealing the spotlight. Why? Well, its servo system and linear scale team up to keep the machine's accuracy in check during operation. And that CNC control system? It's like a wizard that can set all the bending parameters, making sure your bending program is spot-on every time.
Now, even though there are diverse types of press brakes, including the hydraulic press brake machine, their structure and components are pretty much like family members with similar traits, just with a few differences in driving sources and some sheet metal parts here and there. Let's peek inside the hydraulic press brake machine and get to know its key parts and how they all fit together.
Table of Contents
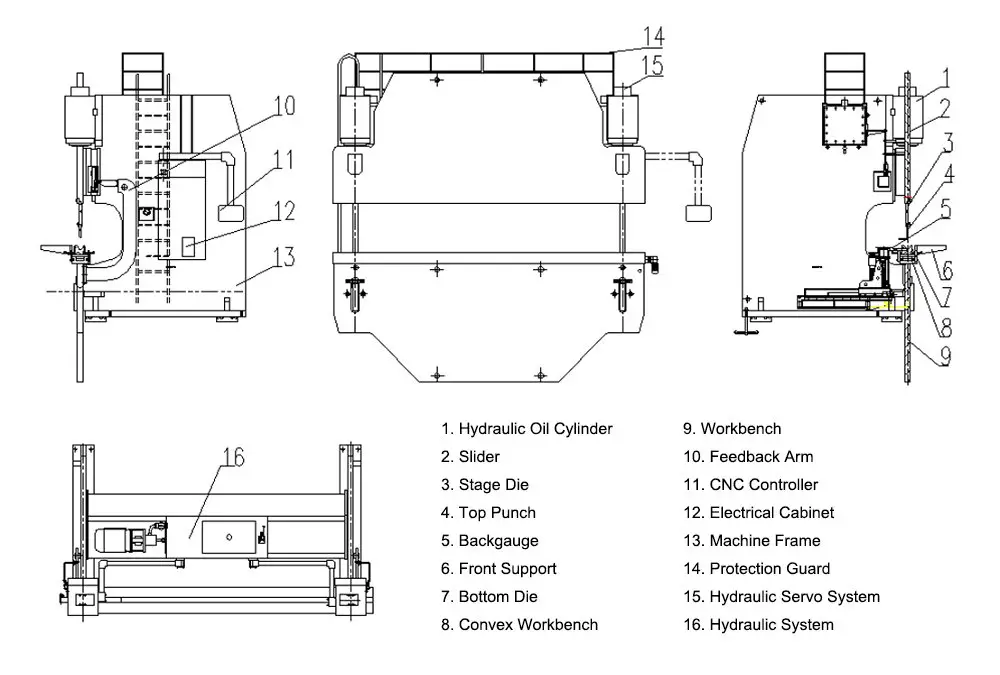
1. Mechanical System
Frame
The frame is the backbone of the whole press brake. It's like a sturdy foundation that gives the machine unwavering stability. Picture a high-strength, fully welded C-shaped structure. It's made up of vertical plates on both sides, a bed (which is the workbench), and the bits that connect them all. The depth of this frame, which is like the throat depth, gives you plenty of space to work your magic on sheet metal bending. And there are these cool monitoring tools on the frame too. They're like little detectives that can spot spring back and keep it to a minimum, so your bends come out just right.
Ram (Upper Beam)
The ram, or upper beam, is the muscle that moves the upper tooling (the punch) up and down. It's like a powerful arm that forces the metal sheet into the die to create those perfect bends. It can get its power from mechanical or hydraulic means. When it presses down on the workpiece against the die on the bed (lower beam), precision is the name of the game. Luckily, modern press brakes have super-smart control systems that make sure the ram moves with pinpoint accuracy.
Bed (Lower Beam)
The bed is the steady platform that holds the die and the workpiece during bending. Made from tough-as-nails high-strength steel, it must be as level as a calm lake to ensure your bends are correct. You'll often see slots or grooves on it, which are like custom-made seats for different die configurations.
Side Housing
The side housing, or side frames, are like the walls that hold everything together. They're vertical structures that connect the bed and ram, creating a rigid and safe enclosure. They make sure the ram moves straight up and down without any wiggling side to side, so your bending process is smooth and correct.
2. Hydraulic System
The hydraulic system is the power controller for the hydraulic cylinder. It's made up of a motor, an oil pump, an oil filling valve, and oil cylinders. You'll find these parts mounted on the press brake's frame, with an oil cylinder on each of the left and right vertical plates.
Power Source
The power source, usually an electric motor or an engine, is the energy giver for the hydraulic pump. It's like the heart that pumps life into the system. Making sure it's the right size and well taken care of is key to keeping the whole hydraulic system reliable and running smoothly.
Hydraulic Pump
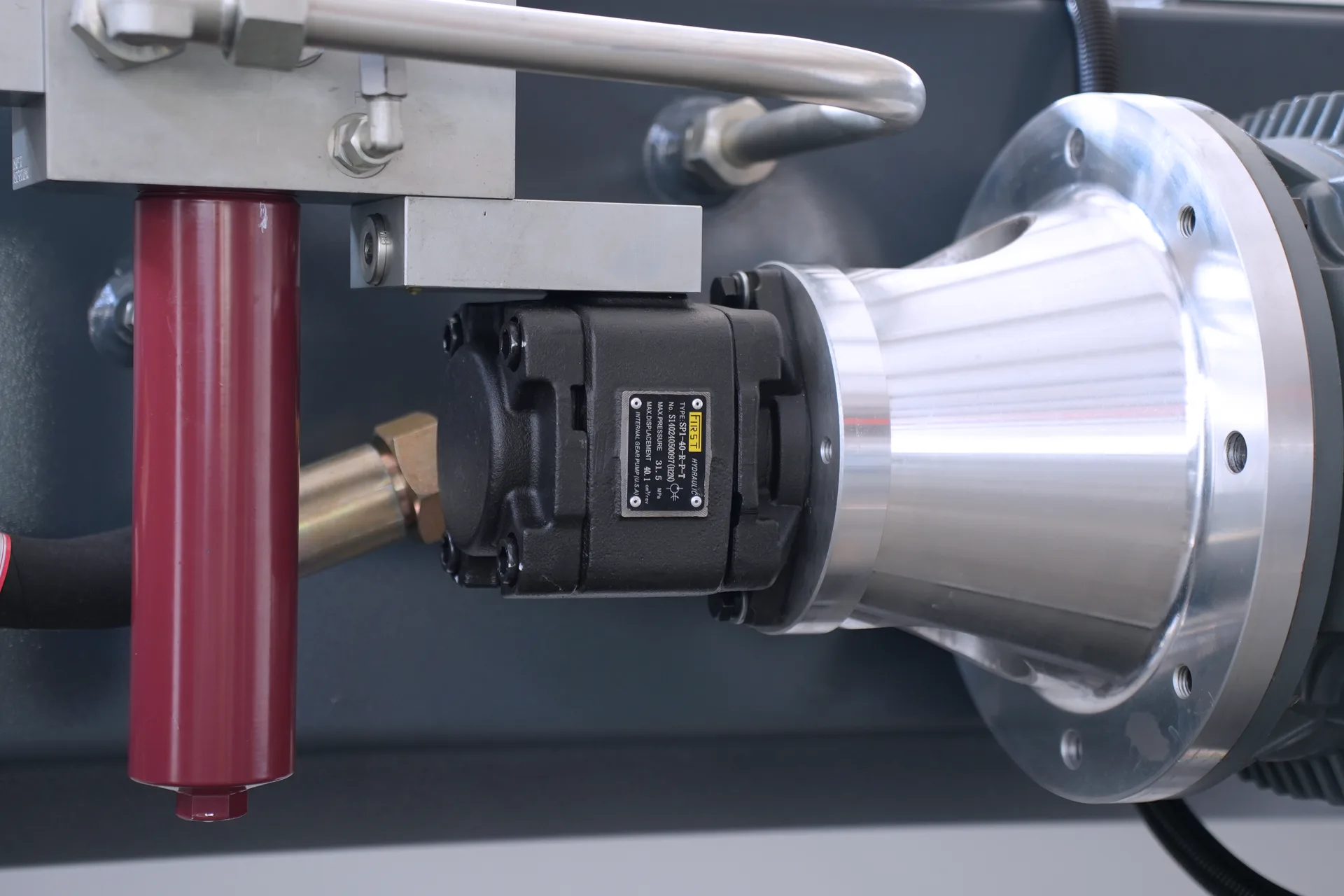
The hydraulic pump is the star of the hydraulic system show. It's the magician that turns mechanical energy into hydraulic power by making the hydraulic fluid flow. There are diverse types of pumps, each with its own superpower:
- Gear pumps are the simple and budget-friendly heroes. They're great for low-pressure jobs, like bending thinner metal sheets in the automotive world.
- Piston pumps are the heavy hitters. They can generate high pressure and are perfect for when you need top-notch quality in press brake operations, like in the aerospace industry where thick metal sheets need precise and powerful bending.
- Vane pumps are the quiet and efficient ones. They're ideal for medium-pressure situations, especially in places where noise is a no-no, like indoor manufacturing facilities.
Reservoir
The reservoir is like the storage tank and the bodyguard of the hydraulic fluid. It keeps the fluid safe, helps get rid of any air or moisture that might sneak in, and adjusts for changes in fluid volume caused by temperature or when the actuators move. Regularly checking the fluid level and keeping it clean is like giving the reservoir a spa day, and it'll keep the system healthy for a long time.
Valves
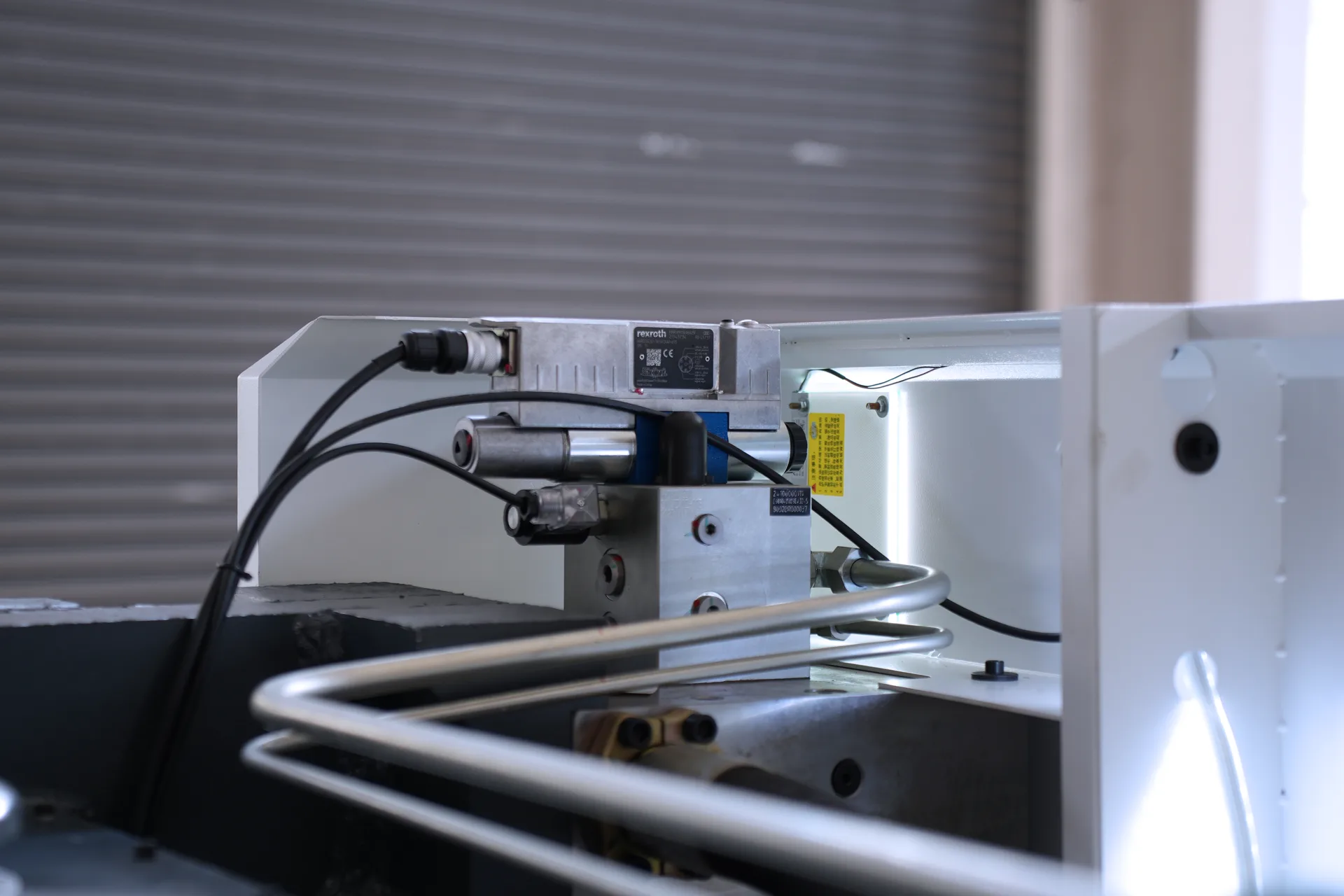
Valves are the traffic police officers of the hydraulic system. They control where the fluid goes, how fast it flows, and how much pressure it has. They're crucial for making sure the press brake works precisely and safely:
- Directional control valves are like the signposts. They direct the fluid to the right places in the system, making the hydraulic cylinders move as needed. They're essential for changing the ram's direction during bending.
- Pressure relief valves are the safety nets. When the pressure gets too high, they spring into action and divert the fluid to keep the hydraulic parts from getting damaged.
- Flow control valves are the speed regulators. They let you control how fast the ram moves, which is super important when you need different bending speeds for custom metal fabrication.
Hydraulic Cylinders
Hydraulic cylinders are the action takers in the hydraulic system. They turn hydraulic energy into mechanical force and make the ram move up and down. There are two types:
- Single-acting cylinders are the one-way wonders. They're good for simple press brake tasks where the return movement can be handled by gravity or an external force, like in light-duty metal bending.
- Double-acting cylinders are the all-rounders. They can apply force in both directions, giving you more control and flexibility. You'll find them in advanced press brake systems for complex bending operations, like making intricate metal parts for machinery.
Hydraulic Circuit
The hydraulic circuit is like the network of roads that the hydraulic fluid travels on. It includes the pump, valves, cylinders, and all the plumbing (hoses, tubes, and fittings). The way it's designed decides how well the system works. Keeping it in decent shape with regular checks for leaks and tight connections is necessary for top-notch performance.
Lubrication and Cooling
The hydraulic fluid is not just a power carrier but also a lubricant and a coolant. Picking the right fluid is like choosing the perfect pair of shoes – it needs to protect against wear, handle heat, and resist corrosion. Regular fluid checks and changes are like changing your socks – it keeps the system fresh and running smoothly.
Filter Element
The filter element is the cleaner of the hydraulic system. It sits out any dirt or debris in the liquid, making sure the system stays healthy and works as it should.
3. Electrical System of Hydraulic Press Brake Machine
Control System
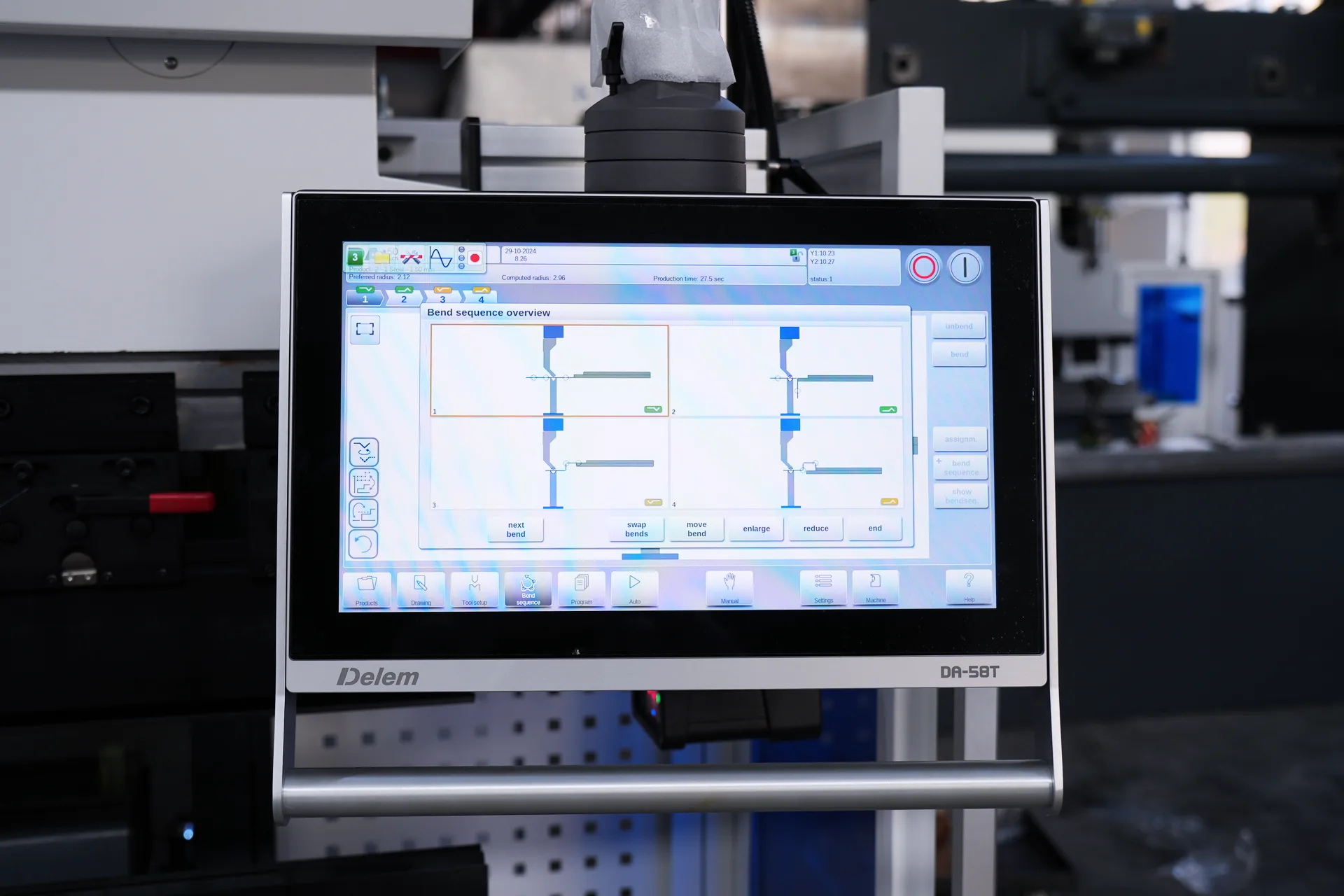
The control system is the brain of the press brake. It's the command center that lets the operator tell the machine what to do through an easy-to-use interface. Modern press brakes come with CNC systems that are like super-smart assistants, offering high precision and the ability to automate tasks.
- CNC controllers, like the Delem DA-66T or CybTouch 12 PS, are loaded with advanced programming tricks, real-time monitoring, and diagnostic tools. They let operators create complex bending sequences, save programs, and always get correct bends.
- Sensors and feedback devices are the eyes and ears of the press brake. They include position sensors, pressure sensors, and safety sensors, all working together to keep the accuracy and safety on point.
Motors and Drives
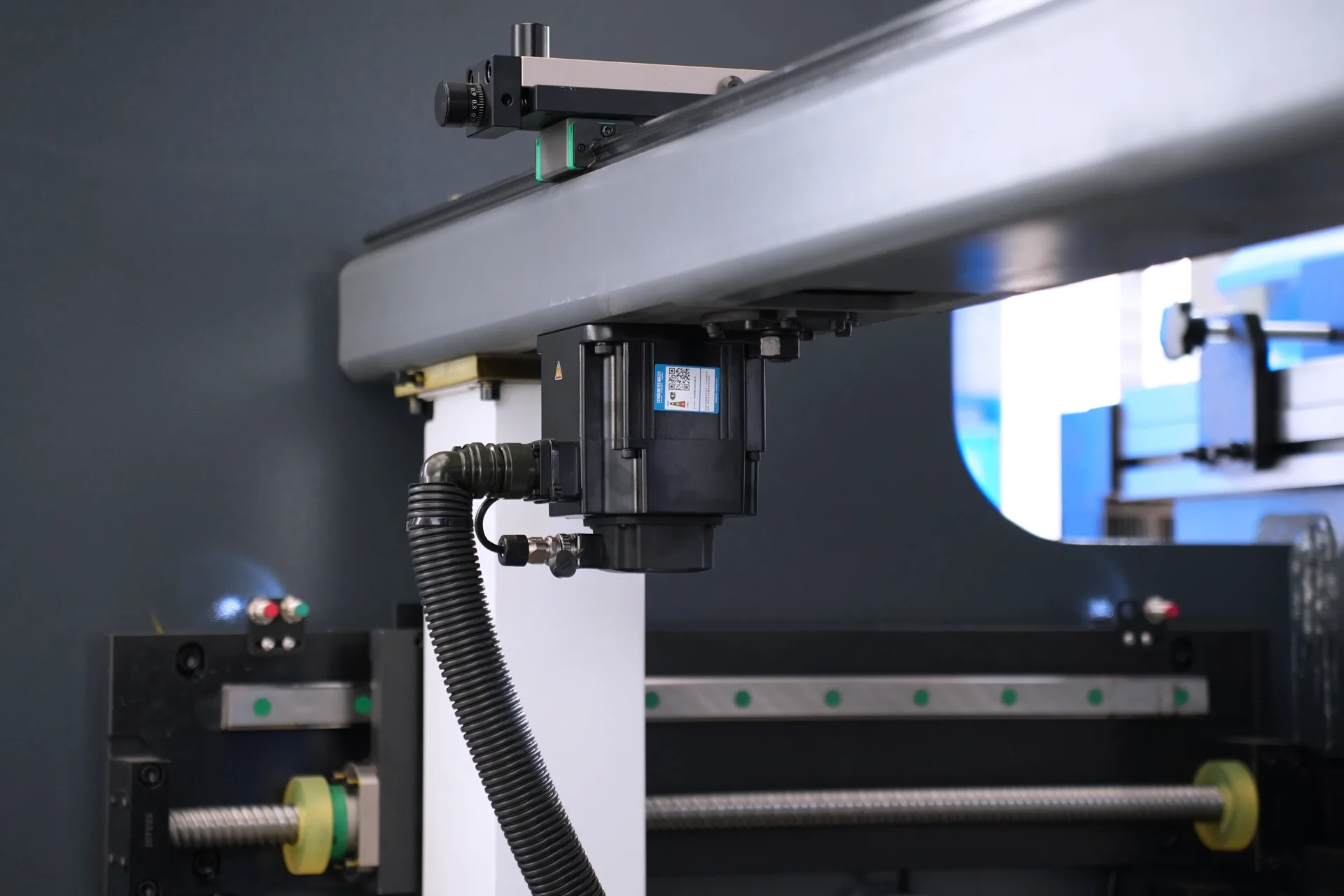
Motors and drives are the powerhouses that make the ram, back gauge, and other parts move. They turn electrical energy into mechanical motion, giving you precise control over the bending process:
- Servo motors are the stars of modern press brakes. They're super precise and reliable, like a sharpshooter hitting the bullseye every time. They control position, speed, and torque with ease, making them perfect for jobs that need fine adjustments. Compared to regular motors, they are faster and more efficient, giving the press brake a real performance boost.
- Variable frequency drives (VFDs) are the speed wizards. They control the speed of AC motors by changing the frequency and voltage of the power. They make the press brake accelerate and decelerate smoothly, reducing stress on the parts. They also save energy and make the motor last longer than old-school drives.
Electrical Panels and Wiring
The electrical panels are like the control hubs that hold all the important bits, like circuit breakers, relays, and contactors. Keeping them organized and clearly labeled is like having a well-kept toolbox – it makes maintenance and fixing problems a breeze.
Human-Machine Interface (HMI)
The Human-Machine Interface (HMI) is the friendly face that lets operators chat with the press brake. It usually has a touchscreen, buttons, and other input toys that make it easy to control the machine.
Safety Features
Safety is the top priority in the electrical system of press brakes. There are some cool safety features to keep everyone and the machine safe:
- Emergency stop buttons are like the panic buttons. They're strategically placed around the press brake so the operator can quickly hit the brakes in an emergency. One press, and the power's off, and all movements stop dead in their tracks.
- Light curtains and safety guards are like the protective shields. The light curtains use infrared beams to sense if anything gets in the way. If the beams are broken, the press brake stops to avoid any ouches. Safety guards are the physical barriers that keep the operator a safe distance from the danger zone during operation.
4. Tooling System
Punch and Die
- There are diverse types of punches: the straight punch, the gooseneck punch, and the offset punch. Each one has its own special job.
- And for the dies, you've got V-dies, radius dies, acute angle dies, gooseneck dies, and bottoming dies. They all work together with the punches to create different shapes and angles.
Tool Holding Systems
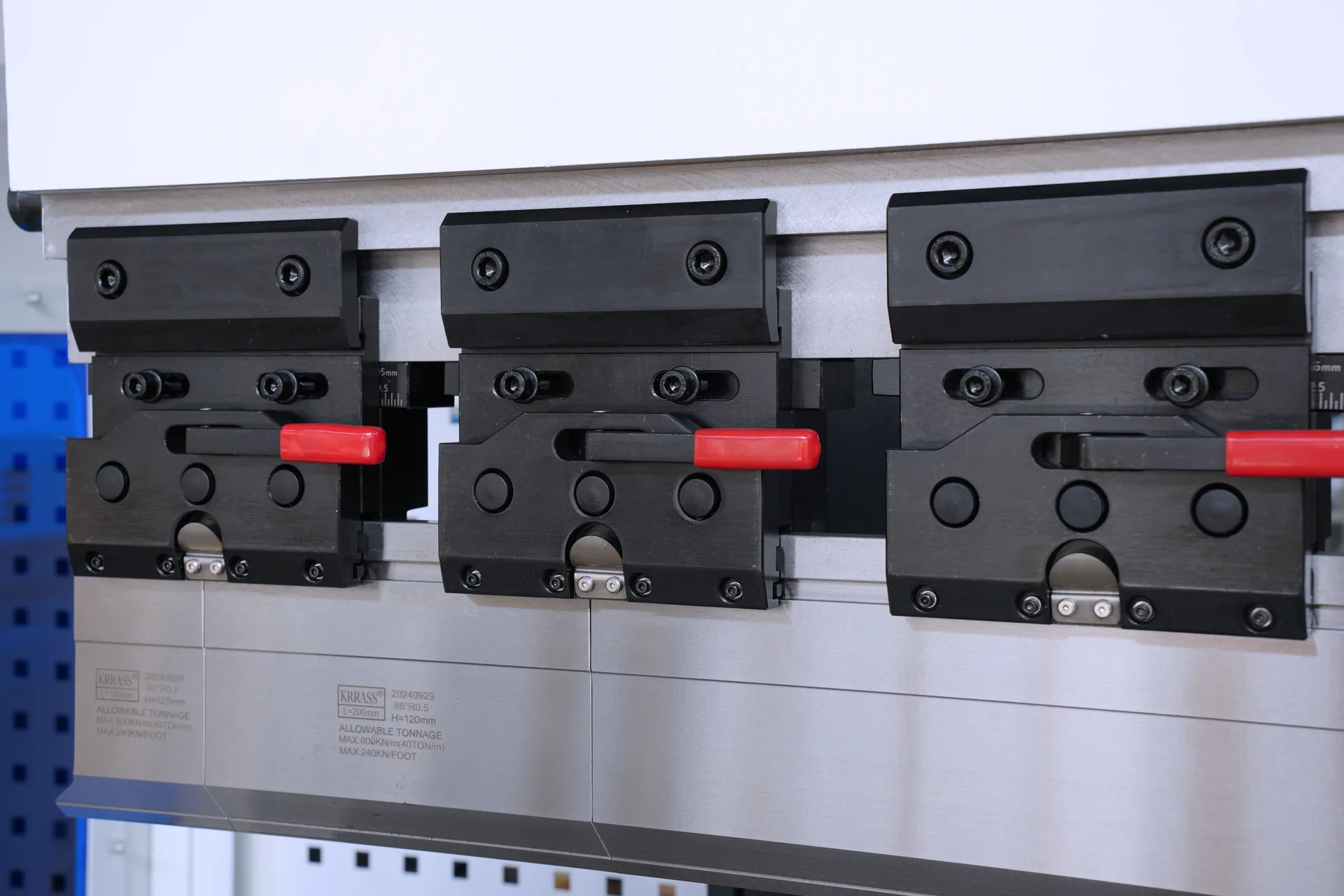
Press brake clamps are the tool holders. There are upper clamps and ones on the workbench. The upper clamps are smart – they can automatically line up the center when clamping. Clamps come in two flavors: ordinary and fast tool clamps.
The fast clamp is a nifty gadget for quickly clamping and unclamping the top punch. It sits on the ram and can adjust the die for even force. This keeps the ram happy and makes sure your workpiece is machined with pinpoint accuracy.
Tool Alignment Systems
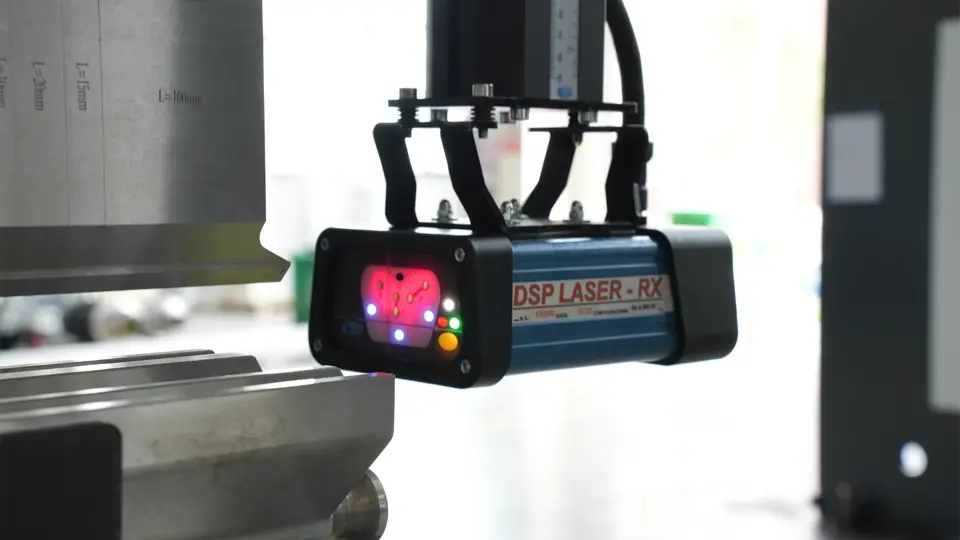
- Laser Alignment: This high-tech method uses lasers to make sure the punch and die are perfectly lined up. It's super accurate and cuts down setup time, especially in jobs where precision is king.
- Mechanical Alignment: The press brake uses mechanical guides and stops to get the tools in the right place. It's not as fancy as the laser system but still does a great job, especially in manual and semi-automatic press brakes.
5. Additional Components
Back Gauge
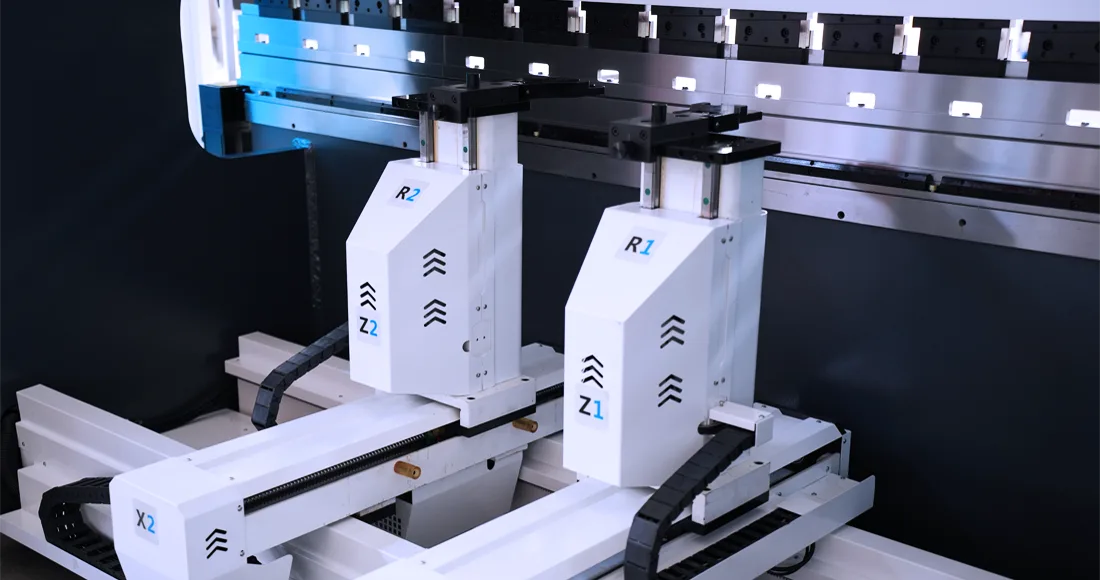
The back gauge is a crucial player in the press brake game. It controls and tweaks the position and length of the workpiece during bending. It hangs out at the back of the press brake and gets the workpiece in just the right spot before the bending fun begins.
It's powered by different motors and can move on different axes. The ball screw and timing belt make sure it all moves coordinated. Controlled by the CNC controller, it can dance on 6 different axes:
- The R-axis is for up and down moves.
- The X-axis is for forward and backward steps.
- The Z-axis is for left and right shuffles. When it's time to bend, the workpiece sits on the die, and the back gauge's stop fingers hold it in place.
The back gauge's main job is to keep the workpiece from going rogue during bending and make sure it bends in the right spot. You can control and adjust it with a motor, servo motor, or cylinder. The operator can set its position and length through the press brake's control system to manage different workpiece bending needs. - Stop finger: This little guy shows the size of the workpiece when the front and back gauges move. It slides smoothly on the linear guide rail and can be adjusted up and down. You can have as many as you need, and they're great for bending different lengths of sheet metal parts without any straightness issues.
- Back gauge bar: This rod-shaped friend works with the stop finger. You can move and adjust it with electricity or hydraulics, and the control system keeps it in line.
- Back gauge sensor: This sensor keeps an eye on the workpiece's position and length. It sends signals to the control system so everything is exactly right.
- Back gauge controller: This electrical wizard controls the back gauge. It listens to the sensor and makes the back gauge bar do its thing to get the workpiece in the perfect position.
- Back gauge guide rails: These guide rails are like the tracks for the back gauge bar. They keep it steady and on the right path as it moves along the bed.
Crowning
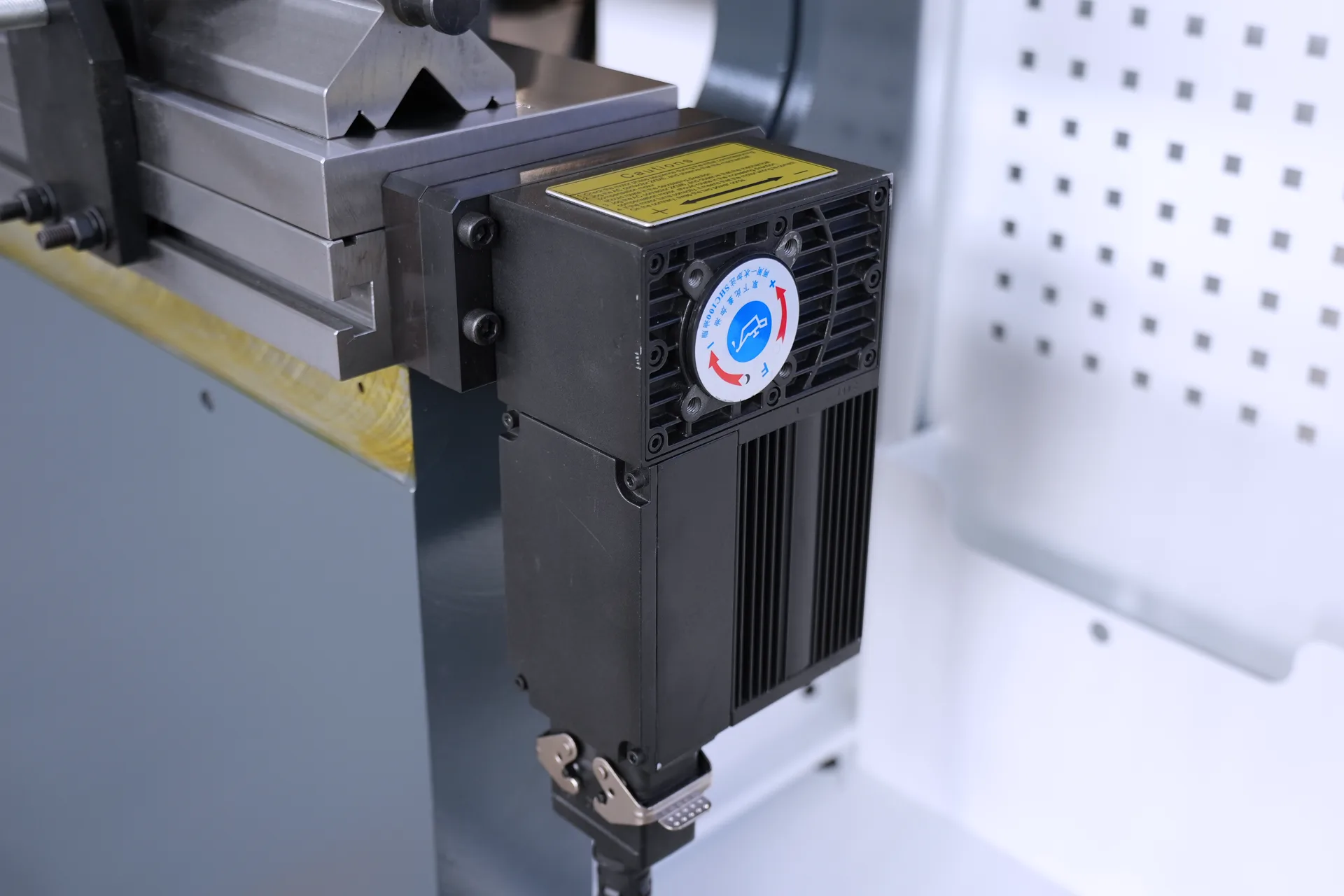
The crowning system is like the magic fixer for any bends or dips in the press brake's bed and ram during bending. It makes sure the angle and bend quality are the same all along the workpiece. It has different tricks up its sleeve, like angle crowning, length crowning, and gap error crowning.
- Hydraulic Crowning: This uses hydraulic power to automatically tweak the bed. It's super accurate and easy to use. In modern press brakes, it's a common sight and can boost bend accuracy by up to 30%. That's a big deal in tough jobs!
- CNC Crowning: The CNC press brake does its own automatic adjustments during bending. It's all about high precision and getting the same great results every time. In industries where precision is everything, this is a must-have.
Front Support
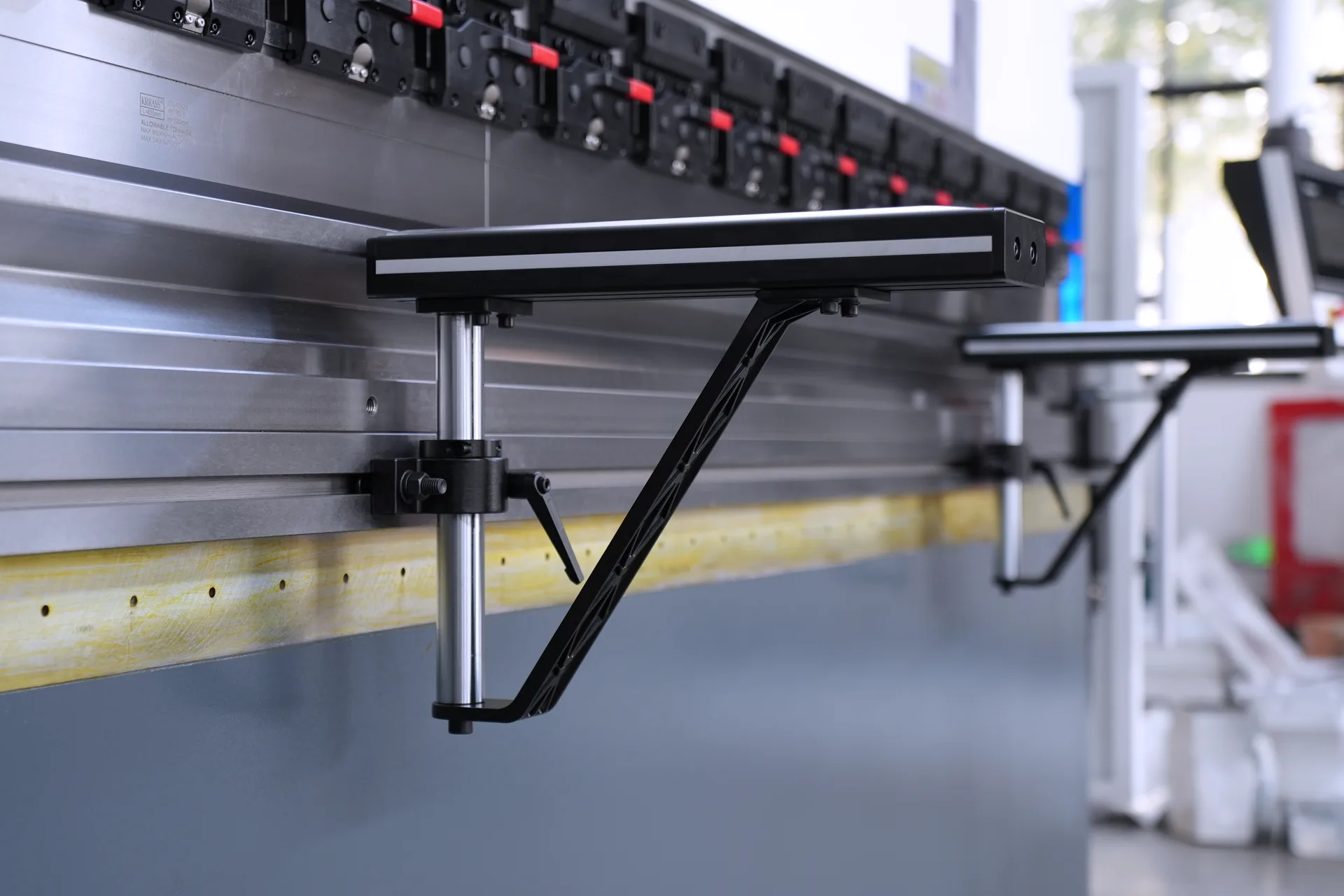
The front support is like a helpful hand for the metal sheet being bent. You can adjust it up and down, and it comes with guide rails so it can move on its own. It's safer and more stable than doing it by hand, giving you better bending results.
Crane Arm
The crane arm is the strong helper for hanging or supporting the small control box. It can spin around in all directions and is built tough, usually from high-quality aluminum alloy.
Foot Pedal
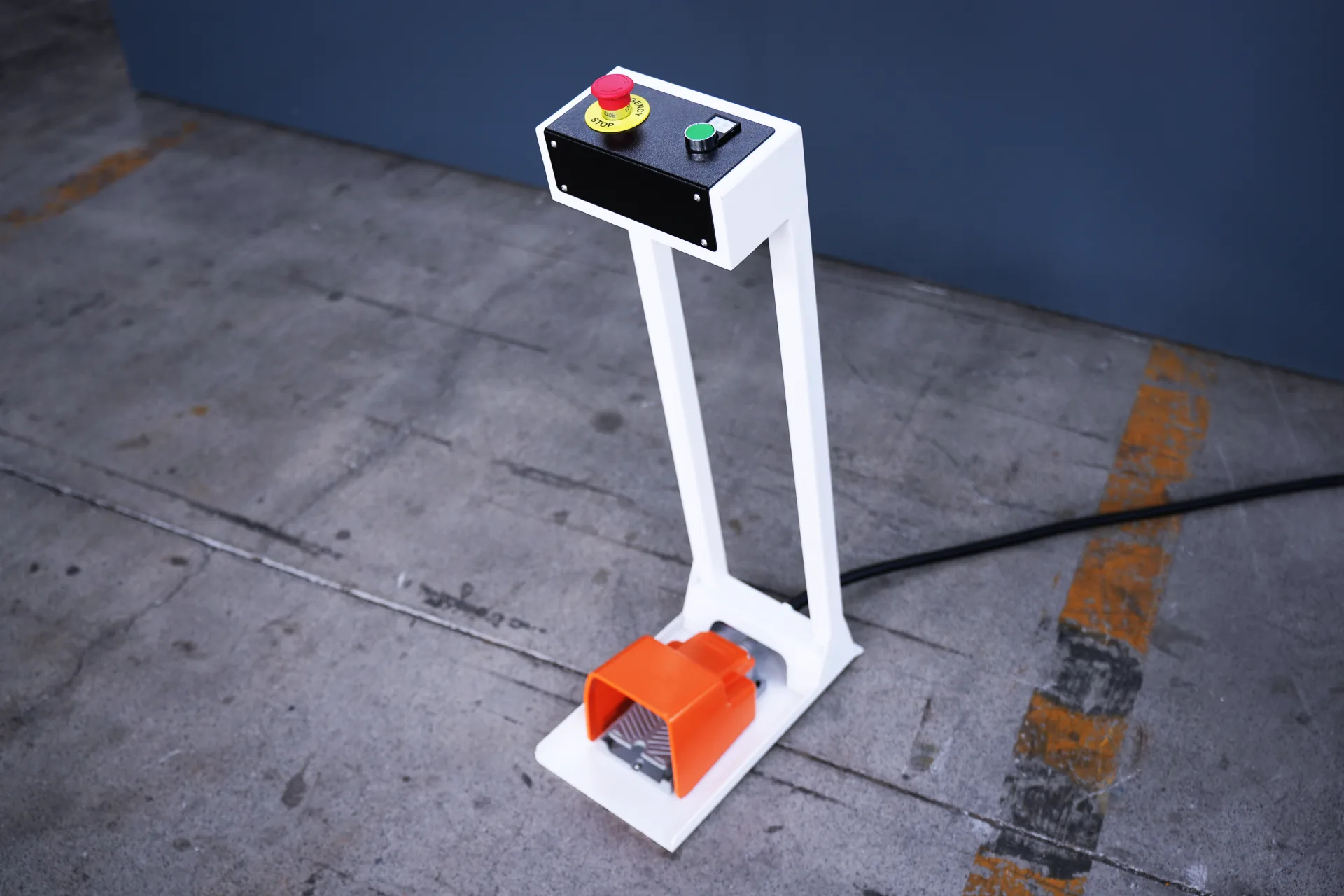
The foot pedal is one of the key players in running the press brake. It's like a multi-tool with emergency stop, cycle start, and single-step remote control powers. You can use it to move the back gauge left and right, start and stop the machine, and even control the whole tool. And if you add a WIFI module, it's like giving the press brake superpowers – you can monitor and manage it from anywhere, making life easier.
Linear Scale
The linear scale is the precision measurer for the position and angle during bending. You can stick it on the top punch or bottom die. It gives you exact measurements and keeps the press brake's motion in check, making your bends more correct and stable.
FAQs
1. What is a press brake, and what is it used for?
A press brake is a trusty tool in the sheet metal world. It's like a giant clamp that bends sheet and plate materials, usually metals. You put the workpiece between a punch and a die, and voila! It's used to make all sorts of parts with specific angles and shapes in the sheet metal fabrication game. Think of things like channels, brackets, and structural parts. It's a big deal in industries like automotive, aerospace, and general manufacturing because it's so precise, can handle different metal thicknesses, and is super versatile.
2. What are the primary components of a press brake?
The main parts of a press brake are the frame, ram, bed, back gauge, punch, and die. The frame is the sturdy base that keeps everything stable. The ram is the mover that presses the punch onto the workpiece over the die. The back gauge is the helper that gets the metal in the right spot for consistent bending. And the control unit – whether it's manual, NC, or CNC – is the boss that runs the show and keeps everything accurate. Knowing these parts and what they do is key to using and taking care of your press brake.
3. What are the differences between hydraulic, mechanical, and electric press brakes?
There are three main types of press brakes: hydraulic, mechanical, and electric. They each have their own style:
Hydraulic press brakes are the powerhouses. They're strong and flexible, can handle different stroke lengths, and are great for thick and heavy materials.
Mechanical press brakes are the speed demons. They're precise and quick, driven by a flywheel, but are better for lighter jobs.
Electric press brakes are the energy savers. They're efficient, speedy, and offer high-precision control. They're perfect for lighter to moderate tasks were saving energy and keeping things quiet matter. Understanding these differences helps you pick the right press brake for whatever you're making.