Hydraulic press brakes have long been the workhorses of metal fabrication, while newer electric press brakes are gaining attention for their efficiency and precision. This outline compares hydraulic vs. electric press brakes from a procurement perspective, examining performance, costs, user experience, and long-term ROI. The goal is to help manufacturing procurement professionals weigh the pros and cons of each technology and make an informed investment decision.
Table of Contents
Understanding Hydraulic vs. Electric Press Brakes
- Hydraulic Press Brakes: Use hydraulic fluid and cylinders to exert force on the metal. They are known for high tonnage capabilities and have decades of proven use in industry.
- Electric (Servo-Electric) Press Brakes: Rely on electric servo motors (and often ball screws or belt drives) to generate bending force instead of hydraulic fluid. They offer a clean operation with no hydraulic oil and precise control through advanced motors.
- Key Difference: Hydraulic machines run a motor and pump continuously to keep pressure, while electric machines only draw power during the bending cycle. This fundamental difference affects their performance, energy use, and maintenance needs.
Performance and Speed Comparison
- Cycle Times: Electric press brakes generally deliver faster cycle times for bending, as the ram can accelerate quickly and decelerate precisely under servo control. This can boost throughput for high-mix or short-run jobs.
- Approach & Bending Speeds: Hydraulic presses often have amazingly fast approach speeds (ram moving into position) but slower bending and return speeds due to fluid flow limits. Electric models may have slightly slower approach, but their consistent high bending speed means quicker overall part processing in many cases.
- High-Volume Production: For continuous operation and heavy forming, hydraulic presses provide steady power. They excel in long runs where their slightly slower cycle is offset by managing thicker materials without strain. Electric presses shine in operations requiring frequent starts/stops or quick job changeovers, thanks to rapid ramp-up and no need for hydraulic pressure buildup.
Precision and Bending Accuracy
- Bending Accuracy: Electric press brakes offer outstanding precision and repeatability. They can achieve positioning accuracy of about 0.000079 inches (about 1 micron) in some models, which is far tighter than typical hydraulic press brakes (around 0.0004 inches or ~10 microns).
- Consistency: Electric systems produce very consistent bending results throughout the day. Hydraulic press brake accuracy can drift as oil temperature and viscosity change over a shift, sometimes causing slight angle variations. This means hydraulic machines may require test bends or adjustments if conditions change, while electrics are less sensitive.
- Repeatability: Both types with CNC controls can repeat programmed bends reliably, but the closed-loop control of servo motors in electric presses often yields better repeatability for ultra-precise work. For most general fabrication tasks, high-quality hydraulic CNC brakes still provide ample accuracy, but precision-focused operations (e.g., electronics enclosures, aerospace parts) often favor electric technology for its micron-level control.
Tonnage Capacity and Size Range
- Force and Size Availability: Hydraulic press brakes come in a wide range of sizes and tonnages. They can be built for extremely high tonnage applications – machines in the hundreds or even thousands of tons are available for heavy plate bending. Electric press brakes, in contrast, are generally limited to lower tonnage ranges (often up to ~80 tons for many standard models, with a few specialized electric presses up to ~300 tons maximum).
- Large Format Bending: For long bend lengths (large bed sizes) and very thick materials, hydraulic presses are usually the only choice because all-electric designs have practical limitations in power transmission for extreme loads. Heavy fabrication industries (e.g., shipbuilding, construction equipment) rely on high-tonnage hydraulic press brakes for this reason.
- Small to Mid-Range Work: In the low-to-medium tonnage range (e.g., ≤100 tons), electric press brakes are more common. They are ideal for smaller parts and thinner materials. If a shop specializes in small precision parts, an electric press brake can manage the workload efficiently, while a hydraulic machine might be oversized for the task.
- Hybrid Options: It’s worth noting there are also hybrid press brakes (electro-hydraulic systems) that use electric servo motors to drive hydraulics. These can achieve energy savings while still delivering higher tonnages, offering a middle ground for those needing more force than pure electric can provide.
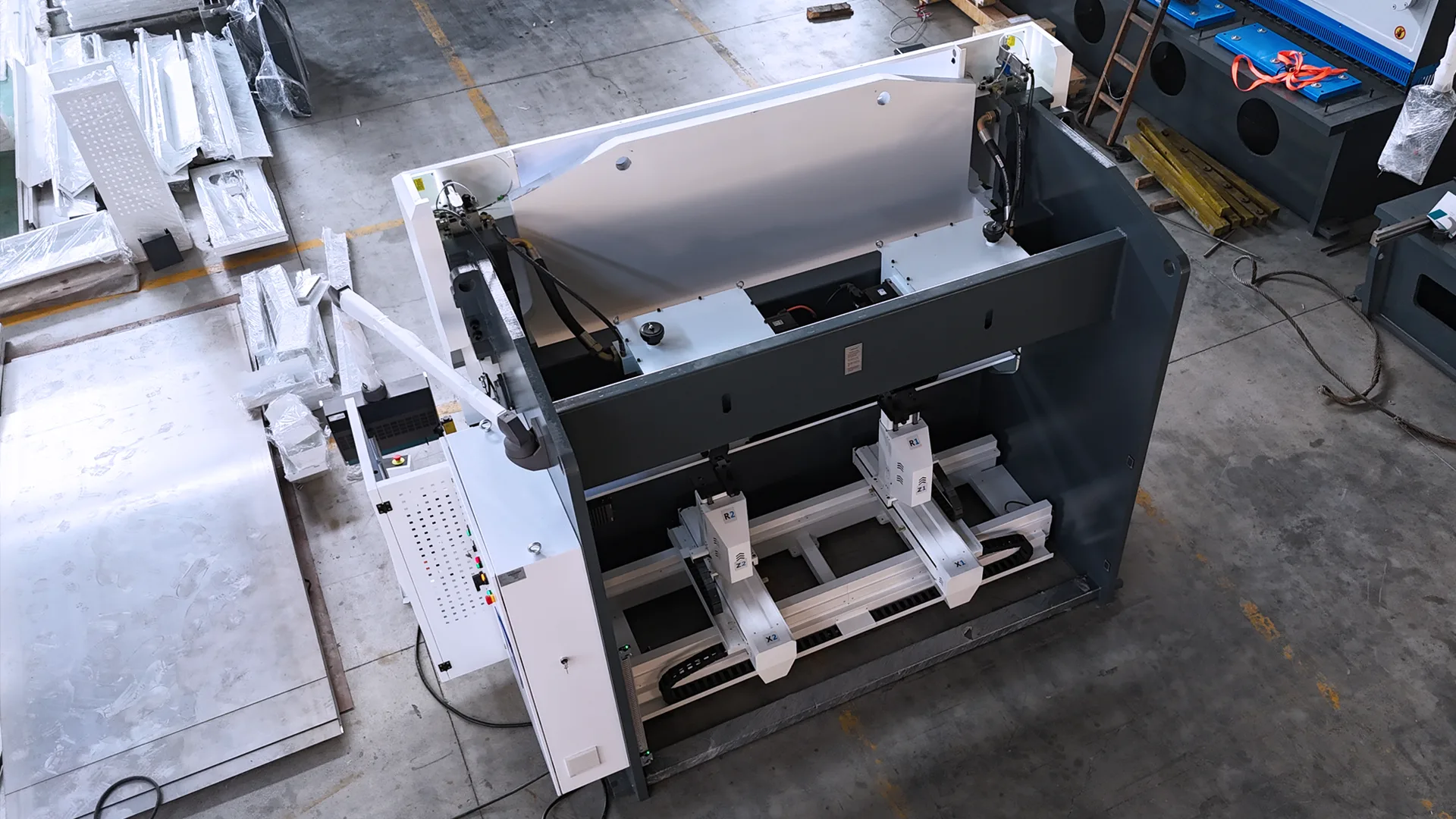
Energy Efficiency and Power Consumption
- Continuous vs. On-Demand Power: Hydraulic press brakes run a hydraulic pump and motor continuously, consuming energy even when idle, to keep pressure available. Electric press brakes use power on-demand – the servo motor only runs when making a bend, and shuts off during idle time, leading to significantly lower energy usage during non-active periods.
- Energy Savings: In practice, modern electric or hybrid press brakes can be 20–30% more energy-efficient than traditional hydraulics under typical operation. Some fully electric models report even greater savings. For example, KRRASS’s all-electric EPP series claims up to 50% lower energy consumption compared to equivalent hydraulic brakes, which can translate to major cost reductions over time.
- Heat and Power Load: Hydraulic systems convert a lot of electrical energy into heat (in the oil and pump), wasting energy especially if the machine sits idle. Electric systems have high-efficiency motors (often >90% efficiency) and minimal energy loss. This not only cuts electricity costs but can also reduce heat output in the shop, indirectly lowering cooling costs or discomfort.
- Peak Power Consideration: One warning – to achieve the same peak tonnage, electric presses may draw a high momentary current, while hydraulic presses use stored hydraulic pressure. However, many electric press brakes manage energy smartly (regenerative drives, capacitor banks, etc.), so overall demand on facility power is usually lower or more evened out than running big hydraulic pumps continuously.
Environmental and Workplace Impact
- Noise Levels: Hydraulic press brakes are typically louder in operation. The hydraulic pump motor runs continuously, emitting noise throughout the day, and the act of moving oil under high pressure can produce a constant hum or whine. In contrast, electric press brakes are incredibly quiet when idle (no motor running) and only emit sound from the servo motors or ball screws during bending, which is generally much quieter than hydraulics. The quieter operation of electric machines can improve the work environment on the shop floor.
- Cleanliness and Leaks: Electric press brakes have a clear advantage in cleanliness – they use no hydraulic oil, so there’s zero risk of oil leaks or spills. Hydraulic press brakes, on the other hand, come with the inherent risk of oil leakage. Over years of use, seals and hoses can wear out, and if a line leaks or a part fails, you may have oil on the floor and a clean-up on your hands. From an environmental standpoint, avoiding hydraulic oil means no waste oil to dispose of and no potential contamination issues.
- Energy and Carbon Footprint: Using less power not only saves money but is also greener. Electric machines that consume less energy (especially during idle times) contribute to a lower carbon footprint for the facility. Additionally, cutting hydraulic oil (which is a petroleum product) is beneficial for sustainability goals – there’s reduced need for oil changes and disposal. Companies focused on environmental compliance or ISO 14000 considerations may lean toward electric presses for their inherently cleaner operation.
- Heat and Ventilation: Hydraulic systems can generate ambient heat from the constantly running motor and warm oil, which may need good ventilation or cooling in the shop. Electric press brakes run cooler by comparison, as energy is not continuously wasted as heat. This can make the immediate work area more comfortable and reduce strain on air conditioning systems.
Cost Considerations (Initial Investment)
- Purchase Price: Typically, an electric press brake has a higher upfront price tag than a similar-capacity hydraulic press brake. The advanced servo motors, controllers, and high-precision components add to cost. Hydraulic press brakes are widely available and come in many configurations, often making them less expensive especially in medium-to-large tonnages. For example, the price of hydraulic brakes can range from a few thousand dollars for small basic models up to six figures for large CNC machines, giving buyers flexibility to match budget and needs.
- Hydraulic vs. Electric Cost Trade-off: At smaller sizes (low tonnage) the price gap between electric and hydraulic may be modest, and buyers might justify the extra cost of electric for the benefits. At higher tonnages, fully electric machines are rare or nonexistent, and the cost of an equivalent hybrid/servo solution can be significantly higher. Procurement must consider capacity needs: if a hydraulic machine can do the job at half the price of an electric, the first savings are substantial – but ongoing costs and benefits (covered below) should also be weighed.
- Tooling and Options: Both types use similar tooling (press brake punches, dies, back gauge systems) and can be equipped with CNC controllers, safety lasers, automation interfaces, etc. However, very high-end electric press brakes might come standard with features (like automatic crowning or sophisticated control software) that would be add-ons in a base hydraulic model. When comparing quotes, it’s important to ensure an apples-to-apples comparison of included features and not just base price.
- Resale Value: While not an immediate cost, consider long-term value. Electric press brakes being newer tech might hold value if demand grows for energy-efficient machines, but they also could become outdated as technology advances. Hydraulic presses, due to their simplicity and wide use, have a well-established secondary market – a well-maintained hydraulic brake can often be resold or traded in. This can offset some first cost if an upgrade is needed in the future.
Operating Cost and Return on Investment (ROI)
- Energy Costs: As noted, electric press brakes save energy by running only on demand. This translates to lower electricity bills over the machine’s life. If your operation runs multiple shifts or keeps machines on all day, the energy cost difference is significant. Many buyers find that the power savings of an electric brake, over years of operation, can meaningfully contribute to ROI. In regions with high electricity costs or where utilities offer rebates for energy-efficient equipment, the savings are even more attractive.
- Maintenance Costs: Hydraulic presses incur ongoing maintenance expenses: periodic oil changes, filter replacements, and the possibility of fixing leaks or replacing seals and valves over time. These costs add up and result in downtime during maintenance. Electric press brakes have fewer fluid power components – no oil to change – and generally require less routine maintenance (mostly keeping the machine clean, lubricating moving parts, and electronics check-ups). The reduction in maintenance labor and parts is a cost advantage for electric brakes.
- Scrap and Rework: An often-overlooked cost factor is the consistency of output. Hydraulic press brakes can produce slightly inconsistent bends as the machine warms up or as oil properties shift, which might lead to a higher scrap rate or more trial-and-error, especially at the start of the day. Those wasted materials and extra setup time have a cost. Electric machines hit their exact angles from the first part to the last with minimal variation, potentially reducing scrap and rework costs. Over large production runs, better consistency means less material waste and time savings for adjustments.
- ROI Timeline: When considering ROI, procurement should project the total cost of ownership: first price + operating costs (energy, maintenance, tooling) – resale value, over the machine’s useful life. Often, an electric press brake’s higher price can be justified by lower ongoing costs and improved productivity. For instance, if faster cycle times allow more parts per day or reduced overtime, that productivity gain is an economic benefit. A balanced ROI analysis will include these tangible savings. Many users report that electric brakes pay for themselves over a few years via energy and efficiency gains, while a hydraulic brake may have a lower barrier to entry but slightly higher running costs throughout its life.
Maintenance Requirements and Downtime
- Hydraulic Maintenance: Hydraulic press brakes require diligent maintenance to stay dependable. This includes regular hydraulic oil changes (typically on a schedule of every 6-12 months or a set number of operating hours) and replacement of filters. Operators or maintenance staff must watch for leaks, check hoses and seals, and ensure the hydraulic fluid stays clean. If the oil becomes contaminated or degrades, it can cause erratic behavior and damage components. Fixing hydraulic issues (leaky seals, blown hoses, pump replacements) can lead to unplanned downtime and often requires a trained technician.
- Electric Maintenance: Electric press brakes have a simpler upkeep routine. With no hydraulic circuit, maintenance is largely focused on the mechanical and electrical systems: keeping ball screws or drive systems lubricated, inspecting the belts or drive components, and ensuring the electrical components (motors, controllers) are in good condition. There are fewer moving parts in terms of pumps and valves, so fewer points of potential failure. Routine inspections and calibrations (e.g., back gauge alignment, lubrication) are typically all that’s needed. This can be done during scheduled maintenance windows, and the risk of sudden messes (like a burst hose) is eliminated.
- Downtime Impact: Downtime for maintenance tends to be shorter and less frequent with electric press brakes, since you avoid the messy and time-consuming aspects of hydraulic service (draining oil, replacing parts, bleeding the system). For hydraulic machines, a preventive maintenance stop is necessary to keep them running smoothly – skipping service can lead to bigger failures later. Electric machines can often run longer between service intervals. That said, if an electric machine’s servo motor or control fails, it might require specialist service, but such events are relatively rare, and many electric components are designed for a long service life (servo motors often rated for many millions of cycles).
- Technical Support: It’s important to consider the availability of maintenance ability. Hydraulic systems are well-known to maintenance personnel in the industry – many technicians are familiar with troubleshooting pumps and valves. Electric press brakes involve CNC controls and servo systems; while generally dependable, if something does go wrong, it might need a controls expert or manufacturer support to diagnose issues (especially software or electronics problems). Procurement should ensure that either in-house staff is trained, or a service contract is in place for the chosen machine type to minimize downtime in case of issues.
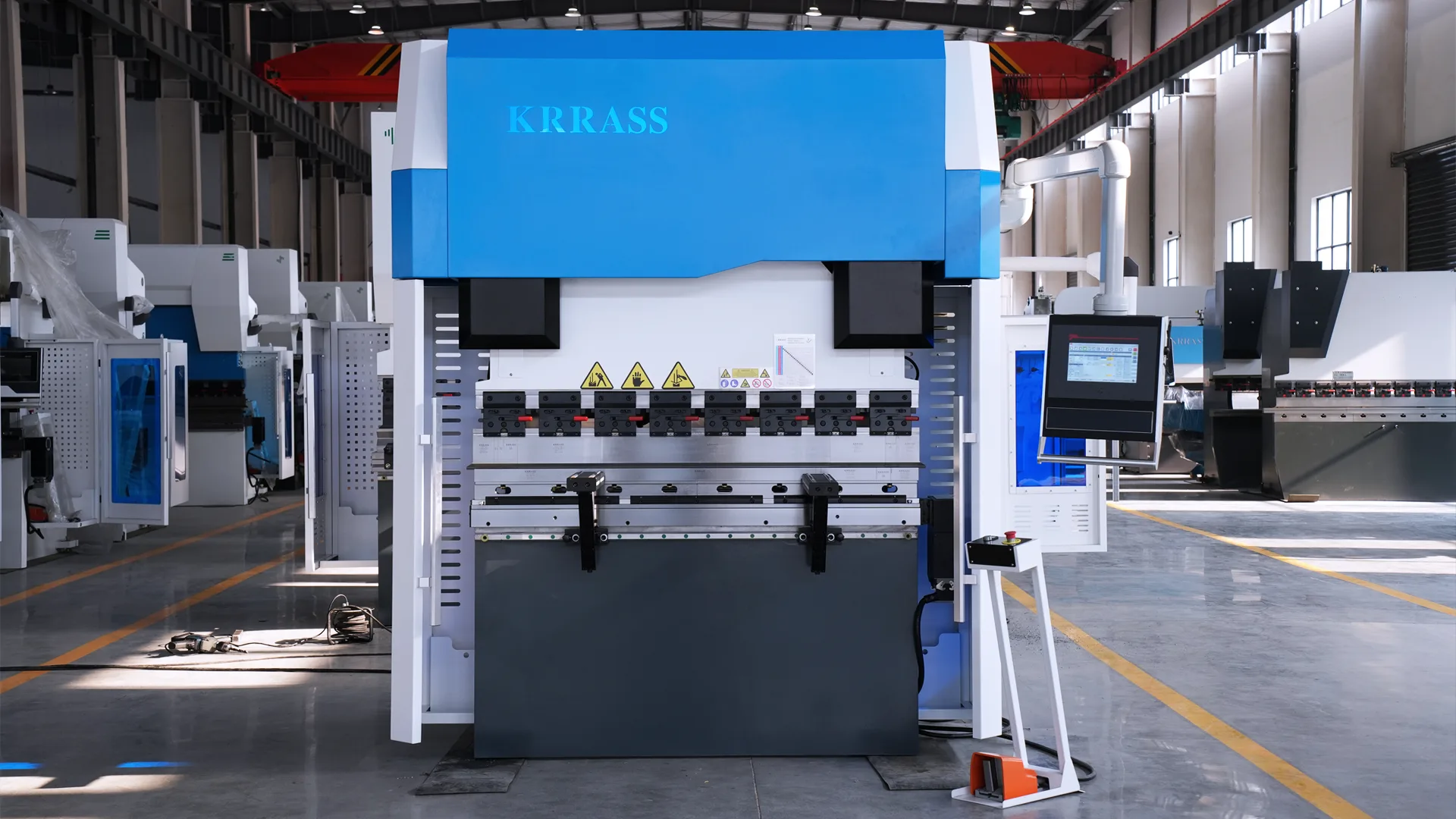
Reliability and Technical Maturity
- Proven Technology: Hydraulic press brake technology is mature and time-tested. These machines have been refined over decades, and their core mechanisms are well understood. For buyers, this means a history of reliability – a quality hydraulic press brake from a reputable brand can reliably serve for many years if it’s kept. The long history also means any “teething issues” in design were solved long ago, and spare parts or ability are readily available if something goes wrong.
- Emerging Technology: Electric press brakes are a newer innovation (though they have been around for over a decade, they’ve only recently become more common as servo motor tech advanced). While many users have had remarkable success with them, the technology is not as time proven as hydraulics in heavy industrial environments. Early-generation electric models have improved over time, but some procurement professionals may view them as having a bit more risk due to the shorter history.
- Reliability Factors: Each technology has different failure modes. Hydraulic presses might leak or have hydraulic part failures, but these are usually straightforward to fix. Electric presses cut those failure modes but instead rely on complex electronics and motors – failures there are rarer but can be more complex to address. Manufacturers like KRRASS, Trumpf, and others producing electric press brakes have proved solid reliability, but it’s crucial to choose a well-supported brand. As one source suggests, going with established electric press brake manufacturers is wise to ensure you get a machine built for reliability and backed by support.
- Stability in Operation: Hydraulic machines offer very stable, consistent force due to the incompressibility of fluid and robust frames; they manage off-center loads and continuous use well. Electric machines provide precise control and are quite stable for intended workloads but pushing them near their tonnage limits continuously isn’t as well documented for decades as it is with hydraulics. In practice, both types from reputable manufacturers are dependable – the difference lies more in feeling and the confidence that comes with a long-established design (for hydraulic) versus adopting a newer technology (electric). Many companies are now comfortable that servo-electric brakes are dependable for production use, but industry veterans sometimes stick with hydraulics for peace of mind in heavy-duty scenarios.
Operator Experience and Operational Feedback
- Noise and Vibration: From an operator’s perspective, electric press brakes create a much more pleasant work environment. As mentioned, they are quiet – operators don’t have to talk over a droning hydraulic pump or wear hearing protection for constant noise. Less vibration is generated without the hydraulic pumps, which can improve comfort during a shift. Hydraulic brakes, especially older ones, can be quite loud and have more machine vibration when the hydraulics engage, contributing to operator fatigue over time.
- Ease of Use: Both hydraulic and electric press brakes today are typically CNC-controlled, with user-friendly interfaces, so running them in terms of programming a bend sequence is similar. However, electric brakes often offer more immediate responsiveness – the ram movement starts and stops very precisely with the pedal, which can give the operator a feeling of control and confidence in the bend. Hydraulic systems might have a tiny lag or need a warm-up to hit full accuracy, which an experienced operator compensates for. Overall, users often appreciate the smooth, exact motion of electric machines.
- Feedback and Consistency: Operators of hydraulic presses learn the quirks of their machine (like knowing to run a couple of test bends in the morning). With electric presses, there's less “personality” to the machine – it either hits the mark or shows an error. This consistency can reduce guesswork and manual tweaking. Some operators accustomed to hydraulics might need a short adjustment period to trust the new system, but generally the feedback is positive when it comes to producing correct parts with less effort.
- Ergonomics and Fatigue: Electric press brakes start and stop quickly, which can reduce the physical strain on operators in high-volume settings. There is less time waiting for the machine to cycle and less repetitive motion in adjusting material if the first bend is right each time. Modern press brakes (both types) often include features like programmable back gauges and even foot pedal controls that move with the operator. In terms of physical operation, neither type requires “backbreaking” labor like old manual brakes did, but the quieter, cooler operation of electric machines can contribute to lower operator fatigue over a full day’s work.
Training and Skill Requirements
- Operational Training: From the operator’s standpoint, running a CNC electric press brake versus a CNC hydraulic press brake is remarkably similar. Both will use a controller (Delem, Cybele, etc., depending on brand) to program angles and sequences. Thus, an experienced operator can transition between the two with minimal retraining on basic operation. The main differences might be in maintenance and troubleshooting training.
- Maintenance Training: Hydraulic machines require training on managing the hydraulic system (how to check/change oil, adjust pressure, fix minor leaks). Electric machines shift the skill requirement towards understanding servo systems and electronics. While day-to-day operation doesn’t demand deep electronic knowledge, maintenance staff might need training from the manufacturer on diagnosing servo drive errors or integrating the machine with software. This means procurement should consider the available skill set in-house: do you have more mechanical/hydraulic ability (favoring hydraulic brakes) or more electrical/CNC ability (which would align well with electric brakes)?
- Troubleshooting and Support: In case of problems, a hydraulic press might show issues via visible signs (oil pressure drops, leaks, strange noises) which a skilled technician can often trace and fix. Electric press brakes might display an error code or simply not run correctly – troubleshooting can require plugging into diagnostic software or calling the manufacturer if the issue isn’t obvious. Thus, training for staff or ensuring strong vendor support is key for electric brakes. Some vendors provide extensive training during installation, and it’s wise to take advantage of that so your team is comfortable with the new system.
- Safety Training: Both types require training on safe operation (using guarding, light curtains, proper use of the foot pedal, etc.). Electric press brakes often come with sophisticated safety systems integrated (like laser safety devices) that operators should be trained on, but these are equally present on modern hydraulic CNC brakes. One difference: because electric machines are so quiet and smooth, operators must be vigilant – just because it’s quiet doesn’t mean it’s not moving with force. Hydraulics give an audible cue when active (pump noise), while electrics might sneak up if one isn’t paying attention, so safety protocols are equally important for both.
Industry Adoption and Trends
- Current Market Trend: The industry is gradually shifting toward more electric and hybrid press brake solutions, especially for small to mid-size machines where energy efficiency and precision are top priorities. Many fabrication shops have started adding one or two electric press brakes to their operations for high-precision tasks or to lower operating costs. However, hydraulic press brakes stay dominant for heavy-duty bending and in many traditional fabrication shops due to their versatility and familiarity.
- Who Uses Hydraulic: Large manufacturing facilities and heavy industries (e.g., automotive stamping plants, appliance manufacturers, structural steel fabricators) continue to rely on hydraulic press brakes for their proven performance in high-tonnage, high-volume applications. If a company is regularly bending thick plate or exceptionally large parts, they likely have multiple big hydraulic press brakes on the floor. Hydraulics are also common in job shops that need a general-purpose machine capable of managing a wide variety of jobs over many years.
- Who Uses Electric: Electric press brakes are seeing adoption in precision sheet metal shops, such as those making electronics enclosures, medical device components, or other products where tight tolerances and clean operation are important. They are also popular in lean manufacturing setups and among companies with strong sustainability or noise-reduction goals. Small to medium fabrication businesses that focus on thinner materials or short-run, high-mix production may find electric press brakes ideal for quick changeovers and energy savings. In essence, small-scale and high-precision operations are early adopters of electric press brake technology.
- Hybrid Press Brakes: An emerging trend is the use of hybrid press brakes (servo-hydraulic), which try to give the best of both worlds. These are being adopted by companies who want to reduce energy usage and maintenance of hydraulics but still need more tonnage than a purely electric system can offer. As technology evolves, we expect to see more hybrids and more powerful electric press brakes, potentially increasing the range of applications where electric can be used.
- Outlook: In the long term, industry experts expect a growing share of electric press brakes in the market as the technology matures and as companies aim to lower operating costs. Major manufacturers are investing in servo-electric models, and features like automatic tool changing and robotics integration are being more commonly paired with electric press brakes to create highly automated bending cells. For now, hydraulics and electrics each have a firm place – and many shops run both types of side by side, choosing one or the other depending on the job.
Case Study Examples

- Case 1 – Precision Parts Manufacturer: A small aerospace parts supplier upgraded from a hydraulic press brake to an electric press brake for their thin aluminum components. The result was improved bending consistency (fewer rejects due to angle variance) and a reduction in energy consumption in their facility. Operators noted that programming bends was faster without needing to compensate for warm-up, and the company reported energy savings that shaved a noticeable amount off their monthly utility bills. Over a year, the scrap rate reduction and power savings helped justify the higher first cost of the electric machine.
- Case 2 – Heavy Fabrication Shop: A large industrial equipment manufacturer considered electric press brakes but ultimately chose to buy a new hydraulic CNC press brake for heavy steel bending. Their decision was driven by the need for 500+ tons of pressing force, a range only hydraulic machines could provide. The hydraulic machine they bought included modern features like variable-speed pumps and idle shut-off to improve energy efficiency somewhat. In use, the machine managed their thick plate jobs reliably. While it uses more energy and requires oil maintenance, the company decided that for their product line, the throughput and capability of a high-tonnage hydraulic press brake offered the best ROI. They plan to revisit electric options for lighter duty bending tasks in the future as a complement to their hydraulic equipment.
- Case 3 – Mixed-Production Fabricator: A medium-sized job shop invested in a hybrid press brake to replace an aging hydraulic machine. The hybrid provided a compromise: it delivered 30% energy savings compared to their old hydraulic while still offering sufficient tonnage for most jobs. In operation, the shop found the hybrid’s performance close to their earlier fully hydraulic press, but with quieter operation and lower maintenance (hydraulic oil changes became less frequent and the system ran cooler). This case underlines how hybrids can be a steppingstone for companies seeking efficiency without sacrificing ability.
- (These examples illustrate how the choice between hydraulic and electric press brakes can depend on a company's specific production needs and goals. Each scenario – from pursuing ultra-precision and efficiency to requiring brute force – leads to a different ideal solution.)
Return on Investment Analysis
- Upfront vs. Long-Term Trade-off: Procurement professionals will want to perform a total cost of ownership analysis. Electric press brakes often have a higher upfront cost, but you must factor in the long-term savings: lower electricity usage, less spending on oil and parts, and possibly improved productivity. For many, these ongoing savings can yield a strong return on investment over the machine’s life. On the other hand, if a machine will be lightly used or only needed for amazingly simple tasks, a lower-cost hydraulic may make more financial sense.
- ROI Calculation: Calculate the ROI by looking at annual cost savings an electric might provide versus a hydraulic. For example, if an electric press brake saves $5,000 per year in energy and maintenance and produces $5,000 more worth of product due to higher uptime or speed, that’s $10,000/year benefit. Over 10 years that’s $100,000 in gains. If the electric cost $50,000 more to buy than a comparable hydraulic, it effectively pays itself off in 5 years and then continues to provide savings. The exact numbers will vary, but this kind of analysis is crucial.
- Production Volume Matters: ROI is highly dependent on usage. A fabricator running one shift with intermittent use might not see a big advantage in energy savings – the hydraulics’ idle losses are less of an issue if it’s off most of the time. Conversely, a shop running 24/7 will benefit enormously from an electric’s efficient design. Similarly, if precision and scrap reduction are important (expensive materials, tight tolerances), the ROI from quality improvements weighs more heavily.
- Incentives and Green ROI: Consider intangible or indirect returns as well. Adopting energy-efficient equipment could help a company meet sustainability targets or qualify for government/utility incentives. This “green ROI” includes things like energy rebate programs, possible tax benefits for investing in efficient machinery, or simply the marketing value of running a greener facility. Such factors can sometimes tip the scales when justifying the investment to stakeholders.
Upgradeability and Futureproofing
- Automation Integration: Press brakes are increasingly integrated into automated fabrication cells with robotic load/unload systems. It’s important to assess how easily a hydraulic vs. electric press brake can be automated or upgraded. In general, CNC hydraulic press brakes can be outfitted with robotics or automated tool changing systems – this has been done in many advanced factories. Electric press brakes are often designed with automation in mind as well, and their consistent behavior (no hydraulic fluid variables) can simplify robot integration. When choosing, ensure the model has the necessary interfaces or options for future automation upgrades (e.g., robot communication, safety interface for automation, etc.).
- Control and Software Upgrades: Modern press brakes, whether hydraulic or electric, use sophisticated controls. Check if the machine’s CNC controller can be updated or if it supports offline programming software. Electric press brakes being newer might have more modern control platforms that integrate with Industry 4.0 systems for monitoring and data collection. Hydraulics can be retrofitted – for instance, older hydraulic press brakes can often be upgraded with new controllers or back gauge systems to extend their life. If your budget doesn’t allow an immediate leap to a new electric brake, upgrading an existing hydraulic machine’s controls (a retrofit) is a choice some consider gaining productivity at lower cost.
- Modularity: Some electric press brake designs are modular or have plug-and-play components (like drive units) that could be swapped or upgraded in the future as technology improves. Hydraulics are more fixed in design – you won’t, for example, easily convert a purely hydraulic machine to electric, but you might add a power-saving pump or better safety systems to it. Understanding the upgrade path for critical components (will the manufacturer support this machine with upgrades 5-10 years out?) can inform the decision.
- Future Viability: Think about where the industry is headed. Investing in an electric press brake might align with future trends toward digital, automated manufacturing. If you foresee your operation needing the absolute latest tech and connectivity, electric machines are often at the forefront. However, if your priority is a machine that any seasoned press brake technician can fix or tweak in the future, the ubiquity of hydraulic technology provides some assurance there. Being “future-proof” can mean high-tech capabilities, but also the confidence that your investment will remain useful even as new models appear.
Long-Term Usability and Lifecycle
- Machine Lifespan: A well-built hydraulic press brake can last for decades – it’s not uncommon to find 20- or 30-year-old hydraulic presses still in service and producing correct parts (with some maintenance and possible parts replacement over time). Electric press brakes are newer, but they are generally designed for longevity as well. The limiting factors on electric machines might be the electronics (which could become outdated or harder to replace in 15+ years) and mechanical components like ball screws, which do wear over exceptionally extended periods of heavy use. In contrast, the limiting factor for a hydraulic is often the availability of replacement hydraulic components or the integrity of the machine frame after many years.
- Durability: In heavy use, machine durability is critical. Hydraulic presses have massive frames and are built to absorb tons of force; if the frame isn’t overstressed and the cylinders are kept, they hold up well. Electric presses also have robust frames for accuracy, but applying near-largest loads repeatedly can stress motors or screws. Manufacturers typically build them with safety factors, but since they haven’t been in the field for as many decades, long-term data is still accumulating. Buyers should look at warranties and engineering specs – for example, how many cycles is the electric press brake rated for, or what maintenance (like ball screw replacement) is expected after X years.
- Obsolescence and Support: Over a long timeline, consider availability of support. With hydraulic presses, the basic parts (pumps, valves, seals) are standardized; even if the OEM no longer supports an old model, a skilled service provider can often source parts or retrofit a generic hydraulic part to keep it running. Electric press brakes have more proprietary components (servo amplifiers, control boards). Ensure the manufacturer has a good track record of supporting older models or providing upgrade paths for the control system. It’s a good sign if the company offers refurbishment or trade-in programs – this shows they plan for a lifecycle with their equipment.
- Resale or Second Life: If after many years you plan to upgrade, what then? Hydraulic machines, as mentioned, often find second life in smaller shops via resale. Electric machines might likewise hold good resale value if they stay in demand, though rapid tech advances could potentially make an older electric less appealing if new models are significantly better. However, given the current pace, an electric press brake bought today should remain quite competitive for a long time, since bending fundamentally doesn’t change and a 1-micron accuracy machine will be just as useful in 15 years if kept. Planning the full lifecycle (including end-of-life options) is part of maximizing the value of the investment.
Conclusion: Choosing the Right Press Brake for Your Needs
In the end, “Which is better, hydraulic or electric?” comes down to your specific production requirements, budget, and strategic priorities. Hydraulic press brakes offer time-proven reliability, higher tonnage abilities, and typically lower upfront cost – they are often the best choice for heavy fabrication, large parts, or when budget is tight, and the machine will be moderately used. Electric press brakes deliver superior energy efficiency, precision, and a cleaner, quieter operation, making them ideal for precision manufacturing and long-term cost savings, especially in lower tonnage applications.
For a procurement professional, it’s crucial to consider all the factors in this outline: performance needs, total cost of ownership, operator experience, and future growth. Some may even conclude that a hybrid approach (using hydraulic machines for some jobs and electric for others) maximizes benefits. By understanding the pros and cons of each type – from speed and accuracy to maintenance and ROI – you can align your press brake investment with your company’s production goals and values. The best press brake is the one that most effectively and efficiently meets your requirements, and armed with these insights, you can confidently choose between hydraulic and electric options to drive your manufacturing operations forward.