Sheet metal fabrication is a versatile and essential manufacturing process that involves converting flat sheet metals, typically ranging in thickness from 0.15 mm to 10 mm, into finished parts, components, or structures of various shapes and sizes. This process is used to create a wide variety of products, including enclosures, chassis, brackets, stamped features, curls, and even intricate decorative patterns. Whether for industrial applications, prototyping, or decorative items, sheet metal fabrication plays a crucial role in numerous industries, including automotive, electronics, aerospace, and construction.
How Does Sheet Metal Fabrication Work?
Sheet metal fabrication typically involves three major steps: material removal (cutting), deforming (forming), and assembly. These processes are often executed in a sequential manner to transform the raw sheet metal into a final product that meets the specific requirements of the design.
1. Material Removal: Cutting the Sheet Metal
Material removal is the first stage of the sheet metal fabrication process. This involves cutting the raw metal sheet into specific shapes using various cutting techniques. Precision cutting methods ensure that parts are fabricated to the exact dimensions needed for assembly.
Laser Cutting
Laser cutting is one of the most precise and widely used cutting techniques in sheet metal fabrication. It involves focusing a high-density laser beam on the sheet metal, which melts, vaporizes, or burns through the material to create intricate cuts. Laser cutting offers several advantages:
- CO2 Lasers: Highly efficient, suitable for cutting thin materials like aluminum and stainless steel, as well as for engraving and boring.
- Nd Lasers: Known for their high energy but low repetition efficiency, ideal for engraving, welding, and boring.
- Nd:YAG Lasers: Offer the highest power output, enabling the cutting of thicker materials, though they are more expensive to run compared to CO2 lasers.
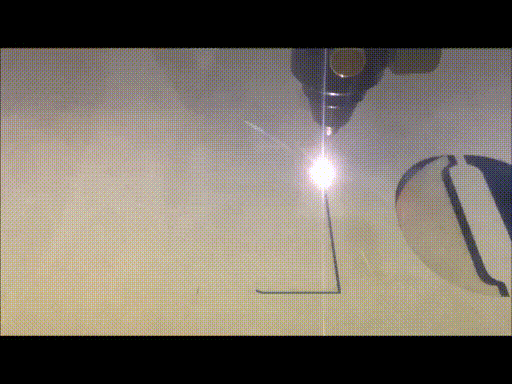
Laser cutting works best on materials such as aluminum, steel, copper, and stainless steel, with typical cutting thickness limits of 15 mm for aluminum and 6 mm for steel.
Waterjet Cutting
Waterjet cutting is a highly versatile and precise method that uses a stream of high-pressure water (sometimes mixed with abrasives) to cut through a variety of materials. Unlike other cutting methods, waterjet cutting doesn’t generate heat, which means there is no heat-affected zone (HAZ), preserving the material's integrity. This method is known for its accuracy and is often used in applications requiring tight tolerances (typically between 0.05 mm and 0.1 mm).
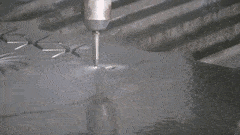
Waterjet cutting can be used on a wide range of materials, from metals such as aluminum, steel, and copper, to softer materials like rubber, foam, and plastics. It is particularly useful when cutting intricate shapes or materials that are sensitive to heat.
Plasma Cutting
Plasma cutting uses a high-temperature plasma arc to melt and cut through electrically conductive materials like steel, aluminum, and copper. The plasma arc is formed by ionizing a gas (such as nitrogen, oxygen, or air) and directing it through a nozzle to cut through the material. While plasma cutting is not as precise as laser or waterjet cutting, it is an excellent choice for cutting thicker materials quickly and efficiently. Plasma cutting is especially useful for metals that are 6 mm to 300 mm thick, depending on the material.
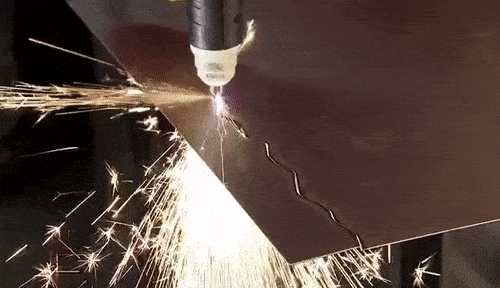
While plasma cutting offers speed and cost-efficiency, it does have limitations in terms of precision, particularly when compared to laser and waterjet cutting. However, it stays one of the most popular choices for industrial applications due to its speed and affordability.
2. Deforming: Shaping the Metal
Once the material has been cut to size, the next step is shaping the metal into the desired form. Deforming, or metal forming, involves the controlled application of force to bend, stretch, or stamp the material into specific shapes. This is a critical step in sheet metal fabrication, as it allows manufacturers to create complex and precise geometries.
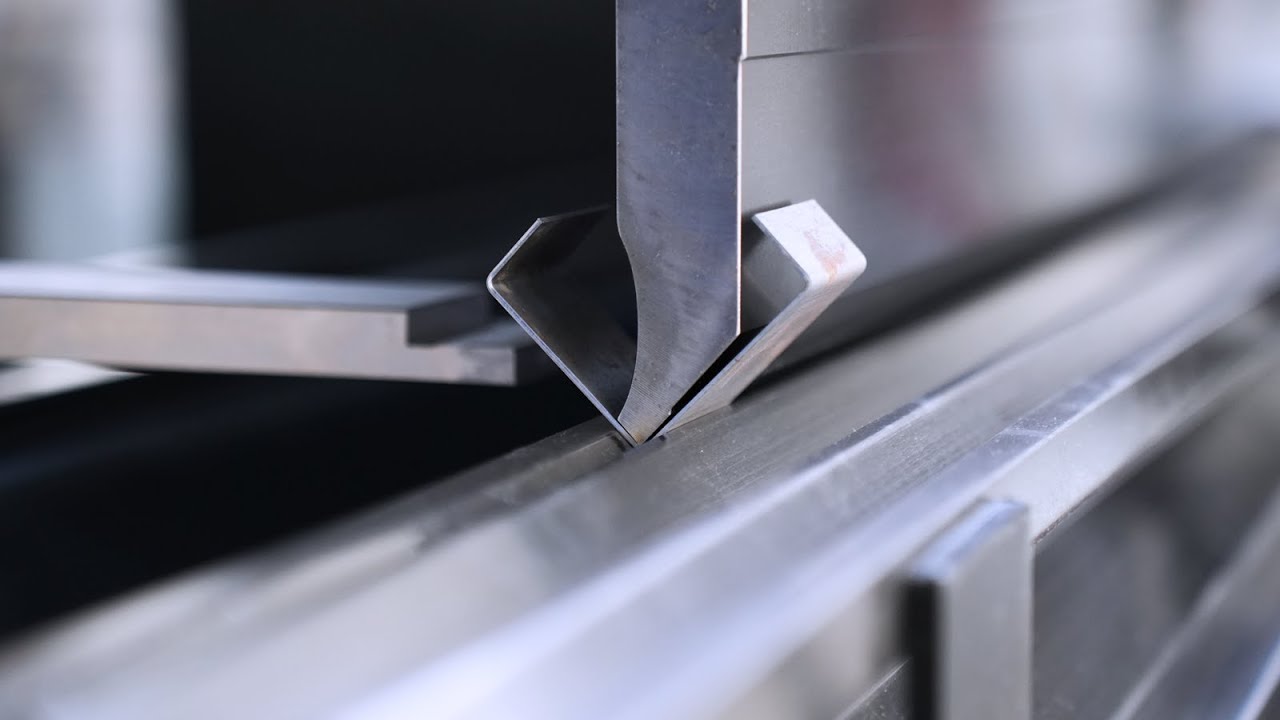
Key deforming processes include:
- Bending: The metal is bent using tools such as press brakes to create angles and curves.
- Stamping: This involves the use of dies to form parts by pressing the metal into specific shapes.
- Stretching: Metal sheets are stretched to create larger areas or thinner gauges, which is particularly useful for forming complex shapes without compromising material strength.
- Forming: The material is shaped into a specific design using a die or mold.
Deforming processes are conducted using specialized machines, such as hydraulic presses, stamping presses, and laser cutters, to ensure precise and consistent results.
3. Assembling: Joining Metal Parts
Once individual components are fabricated, they need to be assembled to create the final product. This stage of sheet metal fabrication involves various joining techniques, including welding, brazing, riveting, and adhesive bonding.
- Welding: The process of joining two or more metal parts by melting them together using heat. Common welding methods include MIG (Metal Inert Gas) welding, TIG (Tungsten Inert Gas) welding, and spot welding.
- Brazing: This process uses a filler metal to join two metal parts at a lower temperature than welding, making it suitable for heat-sensitive components.
- Riveting: Mechanical fasteners, or rivets, are used to hold metal parts together. This is particularly useful for thick metals where welding might not be possible.
- Adhesive bonding: In some cases, strong industrial adhesives may be used to bond metal parts together, offering a cleaner finish and reducing the need for heat-based methods.
Materials for Sheet Metal Fabrication
The materials chosen for sheet metal fabrication play a significant role in deciding the product’s performance and cost. The most used materials include:
- Aluminum and its alloys: Lightweight, corrosion-resistant, and easy to form, aluminum is ideal for applications requiring a strong yet lightweight material.
- Steel: Known for its strength and versatility, steel is used in a wide range of applications, including construction, automotive, and machinery.
- Stainless steel: Highly resistant to corrosion, stainless steel is commonly used in industries like food processing, medical equipment, and architecture.
- Copper and its alloys: Excellent for electrical applications due to its high conductivity, copper is also used in plumbing, roofing, and decorative elements.
Each material is selected based on the specific requirements of the part being manufactured, such as strength, weight, corrosion resistance, and cost.
Aluminium | Copper | Stainless steel | Steel |
---|---|---|---|
DIN 3.3523 | EN AW5052 | DIN 2.0065 | EN CW004A | 1.4319 | Mild steel |
DIN 3.3211 | EN AW6061 | DIN 2.0265 | EN CW505L | 1.4301 | Low-carbon steel |
DIN 3.3535 | EN AW5754 | DIN EN 13601 | EN CW009A | 1.4404 |
Post-Processing Operations
After the metal fabrication process, various post-processing operations may be needed to improve the finished part's appearance, functionality, or durability. These operations include:
- Bead Blasting: A surface finishing technique used to smooth or texture metal surfaces.
- Anodizing: A process that adds a protective oxide layer to aluminum parts, enhancing their corrosion resistance and providing a decorative finish.
- Powder Coating and Painting: These processes provide an added layer of protection and aesthetic appeal, improving the part's resistance to weathering, corrosion, and wear.
- Heat Treatment: Often used after welding or forming, heat treatment helps relieve residual stresses, improve hardness, and strengthen materials.
Benefits of Sheet Metal Fabrication
Sheet metal fabrication offers numerous advantages for manufacturers and end users, including:
- Durability: The resulting parts are strong and dependable, ensuring long-lasting performance.
- Scalability: Whether you're creating a single prototype or large production runs, sheet metal fabrication is highly scalable, offering flexibility in production volumes.
- Material Variety: With a wide range of metals available, you can select the best material to meet the specific performance requirements of your product.
- Cost Efficiency: The process is highly cost-effective, especially when using automated technologies for cutting, bending, and assembling parts.
- Speed: The use of CNC technologies accelerates the production process, reducing lead times and allowing for rapid prototyping and mass production.
Industries That Use Sheet Metal Fabrication
Sheet metal fabrication serves a broad array of industries, including:
- Machine Building: For manufacturing mechanical components and machinery.
- Automotive: For body panels, chassis components, and exhaust systems.
- Electronics: For creating enclosures, heat sinks, and connectors.
- Medical: For the fabrication of medical devices and equipment.
- Construction: For structural components, roofing, and ventilation systems.
- Aerospace: For manufacturing lightweight, high-strength parts for planes.
- Furniture: For designing modern, industrial-style furniture and accessories.
- Robotics: To produce parts used in robotic arms, actuators, and other automation systems.
Conclusion
At KRRASS, we specialize in providing innovative metal forming equipment designed to help manufacturers achieve high-precision results across a variety of industries. Our ultramodern machines, including CNC laser cutters, plasma cutters, waterjet cutters, and advanced forming equipment, enable businesses to produce high-quality, durable, and cost-effective metal parts. Additionally, we offer a range of support and guidance to ensure you get the most out of our equipment.
To learn more about how KRRASS can help elevate your metal forming processes, visit our website and explore our product offerings today.