Laser cutting has become a common and essential technology for laser cut stainless steel processing across various industries, including metal furniture, lighting, automotive manufacturing, kitchenware production, and more. However, not all manufacturers fully harness the potential of laser cut stainless steel technology. Defects like burrs, irregular cut edges, or unwanted discoloration can often occur during the cutting process, diminishing the quality and aesthetic appeal of the finished product.
If you are facing these challenges, don’t worry. This guide will provide you with valuable insights into how to perfect stainless-steel cutting with KRRASS laser cutting machines to achieve precise, high-quality results.
Table of Contents
Set Up Your KRRASS Laser Cutting Machine
Before powering up the machine, ensure that all electrical connections are stable and meet the machine’s power requirements. Inspect the machine for any obstructions that could interfere with the movement of the axes, and ensure the entire system is intact and free of any debris or dust.
Clean the Protective Lens
The laser cutting process requires clean lenses to function optimally. Before starting, ensure the protective lenses are free from water, oil, residue, or any discoloration such as black or yellow stains. Note that protective lenses can fog up in colder conditions or due to auxiliary gas use, so it's essential to regularly inspect and clean the lenses to maintain cutting accuracy.
Choose the Correct Nozzle
The nozzle type and size should be selected based on the thickness of the material being cut. Below is a general guideline for selecting the correct nozzle for stainless steel cutting:
Material | Thickness (mm) | Nozzle Type | Nozzle Diameter (Φ) |
Stainless Steel | 1 | Single layer | Φ1.0 |
2-3 | Φ1.5 | ||
3-5 | Φ2.0 | ||
5+ | Φ3.0 or larger |
In addition to the nozzle type and size, regular maintenance is critical. Make sure to install the nozzle carefully, ensuring that it is not damaged, and clean it often to prevent residue buildup. If the nozzle becomes deformed or clogged, it can significantly affect the cut quality.
Verify the Pilot Light Status
Ensure that the pilot light is properly illuminated and round, with no black spots present.
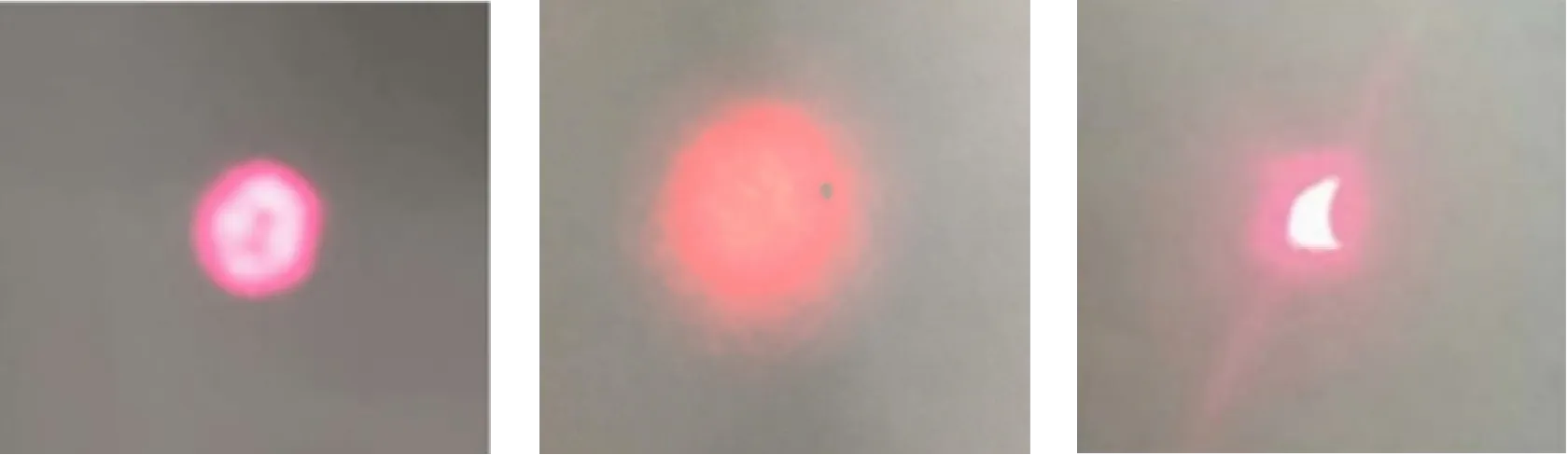
If black spots are seen, inspect the focusing protective lens. If the black spots persist even after cleaning, the internal lens or collimating protective lens may be damaged. In such cases, it is advisable to contact a qualified technician for repairs.
Ensure Coaxial Alignment of the Laser Light and Nozzle
Correct alignment between the laser beam and the nozzle is crucial for achieving precise cuts. Follow these steps to ensure alignment:
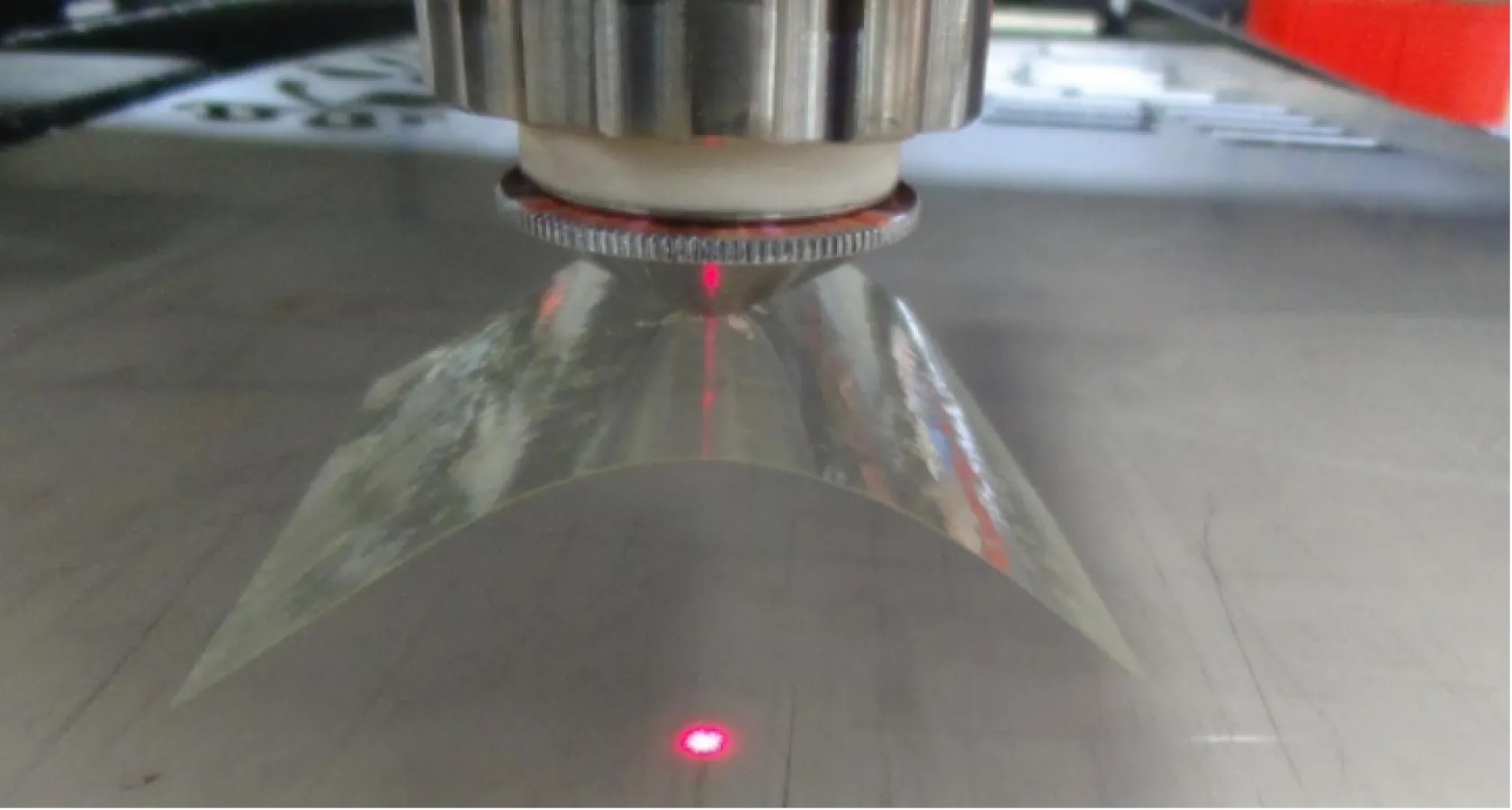
- Use the cutting software (Example: CypCutE) to position the laser head and beam appropriately.
- Attach a piece of Scotch tape to the nozzle’s end face.
- Set the laser power, typically around 80-100W, and activate the laser to create a small mark on the tape.
- Remove the tape and verify if the laser spot aligns with the center of the nozzle. If not, adjust the focus by turning the knob on top of the laser head to achieve coaxial alignment. Repeat the process until the spot is perfectly centered.
Input Suitable Cutting Parameters
Ensure that the cutting parameters entered the software match the material thickness and cutting requirements. If the settings are incorrect, adjust them promptly. This includes selecting the best cutting speed, laser power, and frequency.
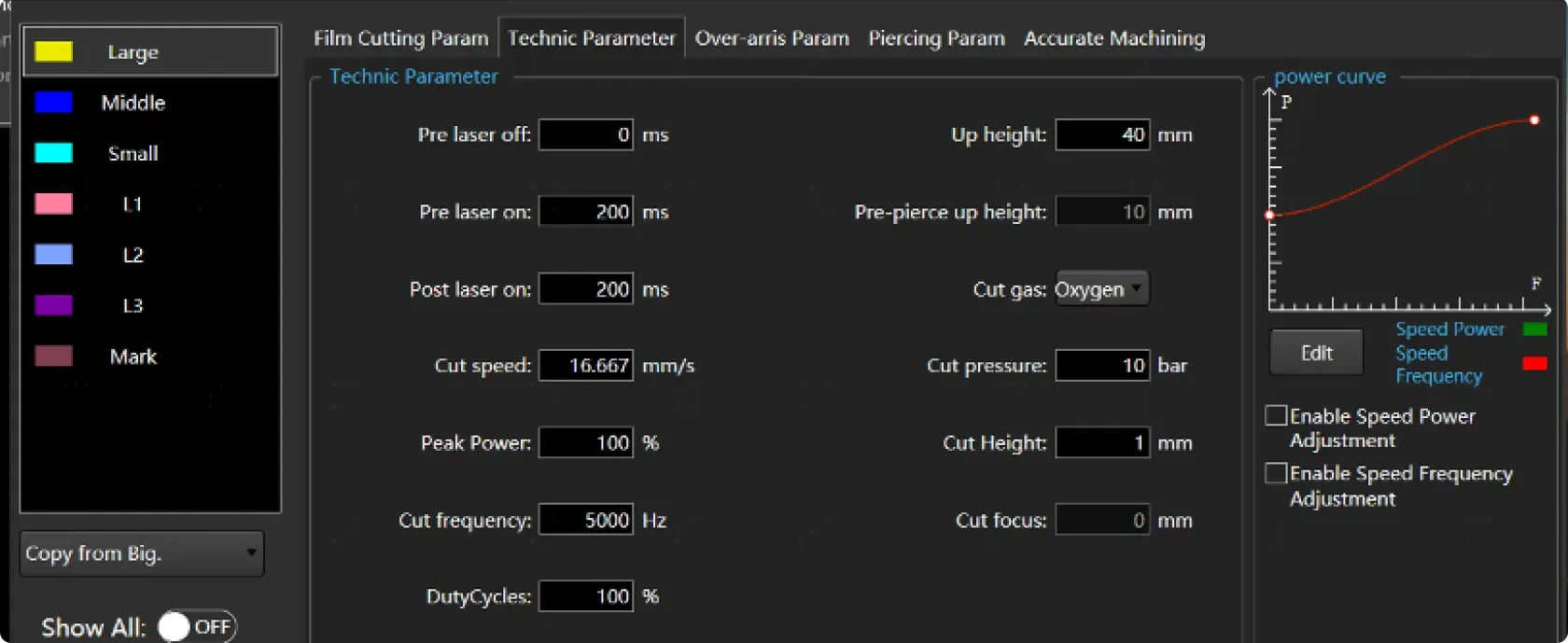
Find and Correct Inappropriate Cutting Speed
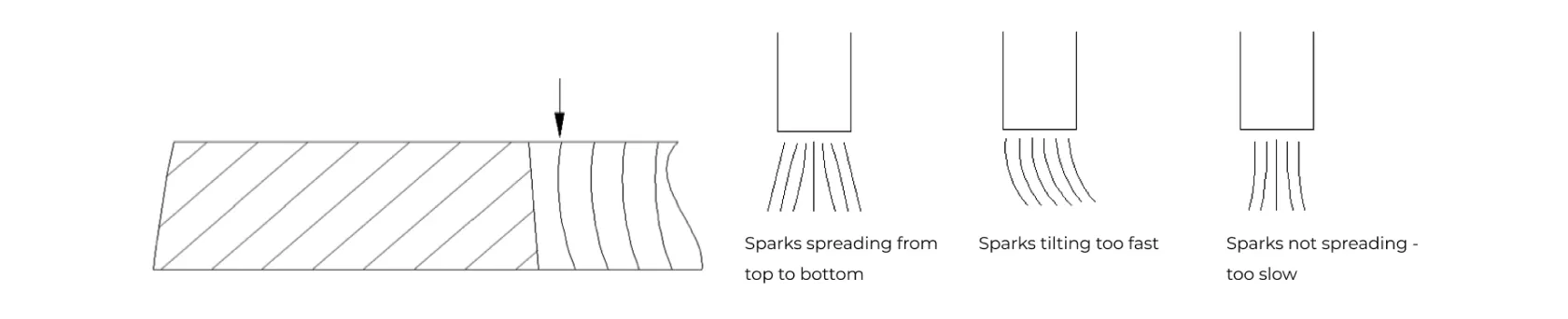
After inputting the cutting speed, see the sparks generated during cutting. The correct speed produces smooth cuts with minimal slag. Here's how to identify proper speed:
- Stable sparks: Ideal cutting speed.
- Upward-tilting sparks: Speed is too fast.
- Condensed sparks: Speed is too slow.
Adjust the Cut Height
The height between the nozzle and the workpiece should be carefully set between 0.5mm and 1.5mm.

If the nozzle is too close to the workpiece, it could cause damage. If the distance is too large, the cutting gas will spread out, leaving residue on the cut surface, which could degrade the quality of the cut.
Locate the Correct Focus
Some KRRASS machines feature automatic focus adjustment, ensuring stable and precise focus during cutting. If your machine lacks this feature, measure the zero-focus point and adjust it, as necessary. Stainless steel cutting typically requires a negative focus, meaning the focus point is slightly below the work surface.
Use the Appropriate Laser Power
Adjust the laser power according to the material’s thickness. Both too high and too low power levels can lead to poor cutting quality. If the power is too low, the material may not be cut through effectively, while excessive power may cause melting at the cut edge and result in a wide kerf. Aim to find a balanced power setting that ensures clean, precise cuts.
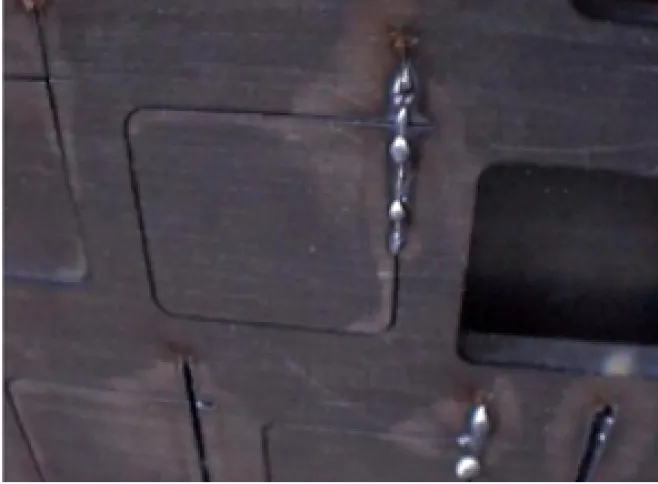
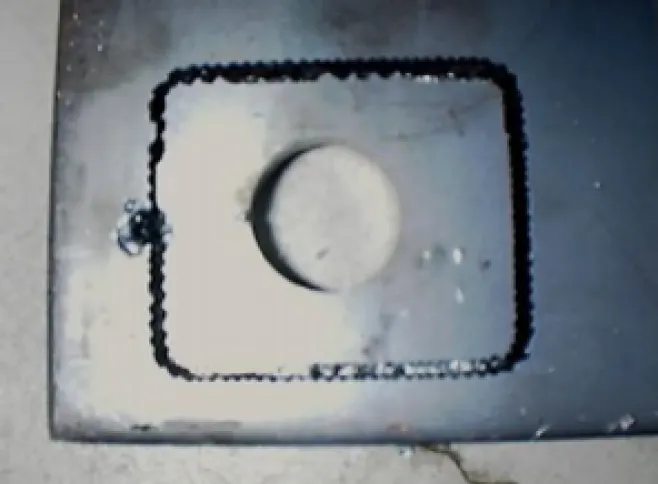
Note: These two samples are carbon steel plates, and stainless steel plates exhibit the same effects if the laser power is too small or too large.
Find the Optimal Cutting Frequency (for Thicker Materials)
For thicker stainless-steel sheets, adjust the cutting frequency within the range of 5000Hz to 200Hz. As the frequency decreases, the cut quality improves, resulting in smoother edges and better layering conditions. Ensure the pulse frequency is well-matched with the single pulse energy for the best results.
Use High-Quality Auxiliary Gas
The choice of auxiliary gas is pivotal in stainless steel cutting. Nitrogen (with a purity of 99.995%) is the preferred gas for cutting stainless steel, as it prevents oxidation on the cut edges, reducing or cutting the need for post-processing. For thicker materials, oxygen with a purity of 99.999% can be used to improve cutting efficiency.
Recommended Cutting Parameters for Different Laser Powers
For 3kW Laser Power:
Thickness (mm) | Cut Gas | Cut Speed (m/min) | Taper (mm) | Ra (μm) |
1 | N2 | 30-58 | 0 | 1.2 |
Air | 35-50 | 0 | 1.2 | |
3 | N2 | 6-14 | 0.03-0.06 | 1.7 |
Air | 10-15 | 0.03-0.10 | 3.0-5.0 | |
10 | N2 | 0.6-0.8 | 0.25-0.4 | 8.8-10.7 |
Air | 0.6-1.0 | 0.25-0.4 | 8.8-10.7 |
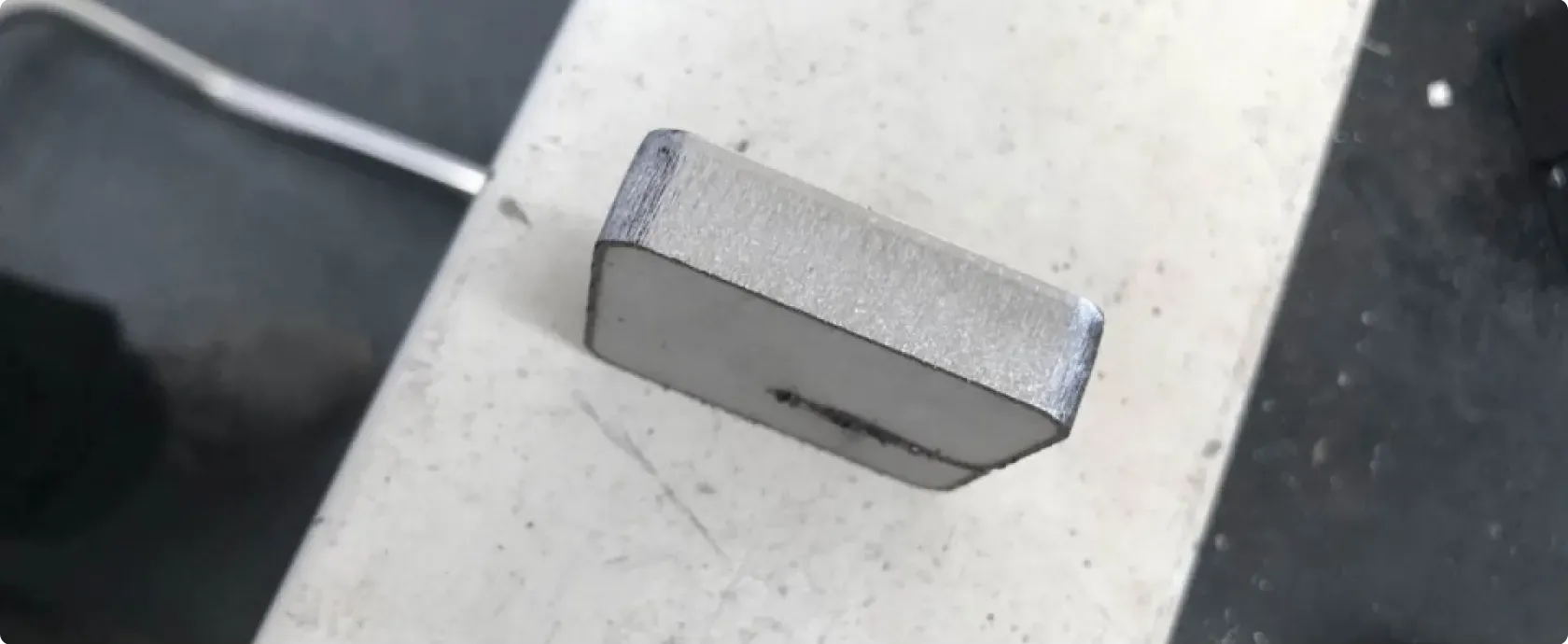
For 6kW Laser Power:
Thickness (mm) | Cut Gas | Cut Speed (m/min) | Taper (mm) | Ra (μm) |
1 | N2 | 42-52 | 0 | 1.2 |
Air | 42-52 | 0 | 1.2 | |
12 | N2 | 0.8-1.5 | 0.3-0.6 | 11.8-16 |
Air | 1.2-2.0 | 0.3-0.6 | 11.8-16 | |
20 | N2 | 0.3-0.5 | 0.5-0.7 | * |
Air | 0.3-0.5 | 0.5-0.7 | * |
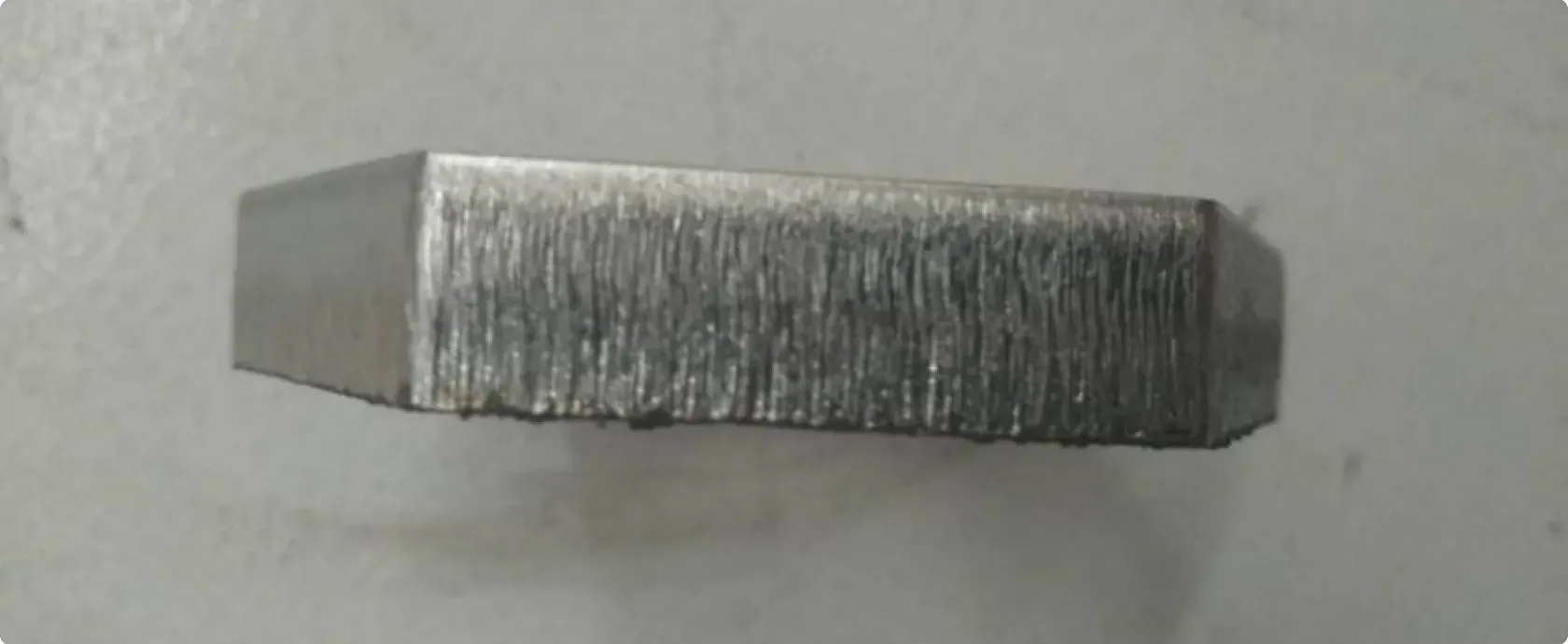
For 12kW Laser Power:
Thickness (mm) | Cut Gas | Cut Speed (m/min) | Taper (mm) | Ra (μm) |
1 | N2 | 45-60 | 0 | 1.2 |
Air | 45-70 | 0 | 1.2 | |
20 | N2 | 0.7-1.5 | 0.5-0.7 | * |
Air | 0.8-1.5 | 0.5-0.7 | * | |
30 | N2 | 0.2-0.5 | 0.5-0.8 | * |
Air | 0.3-0.6 | 0.5-0.8 | * |
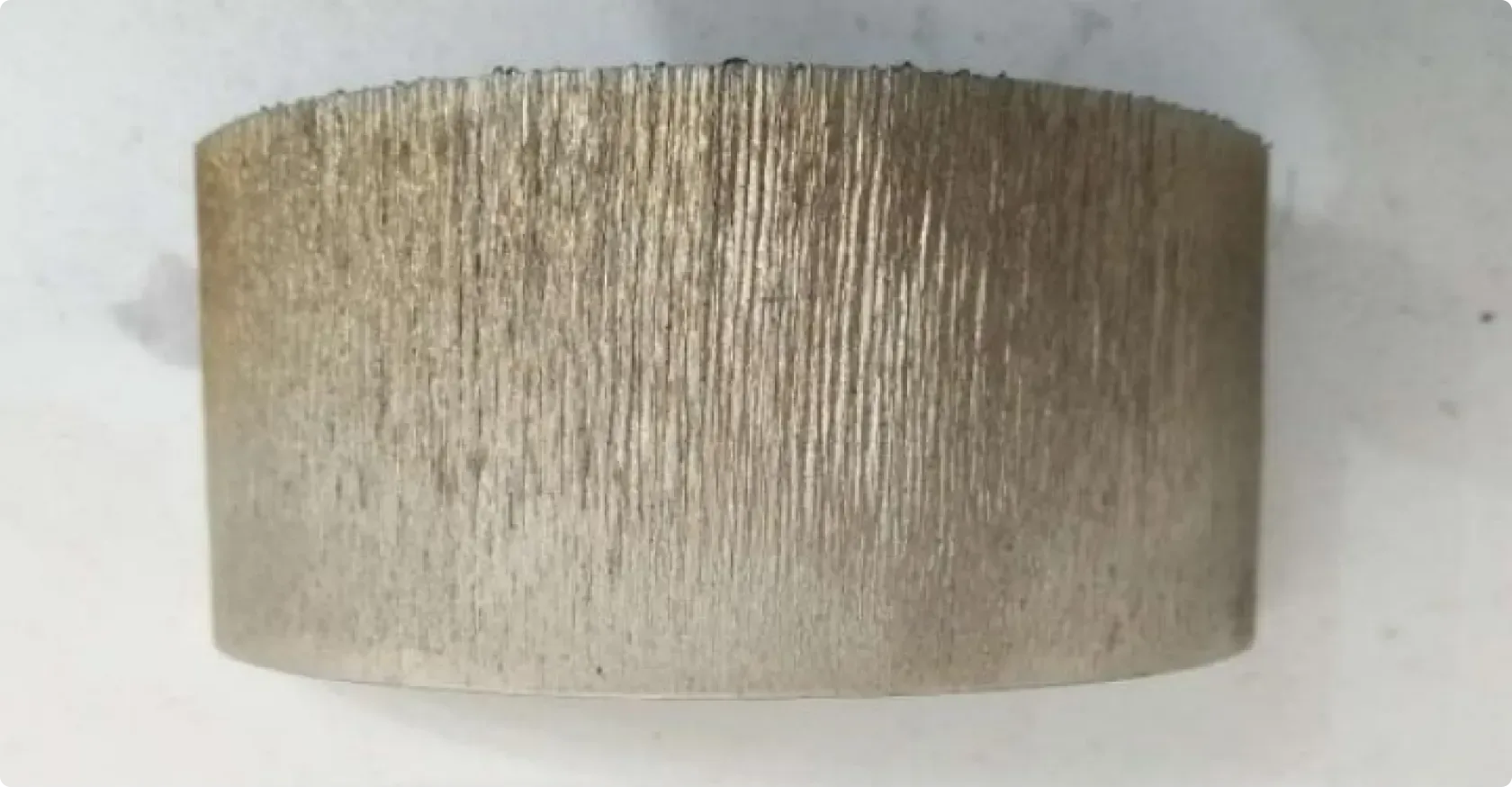
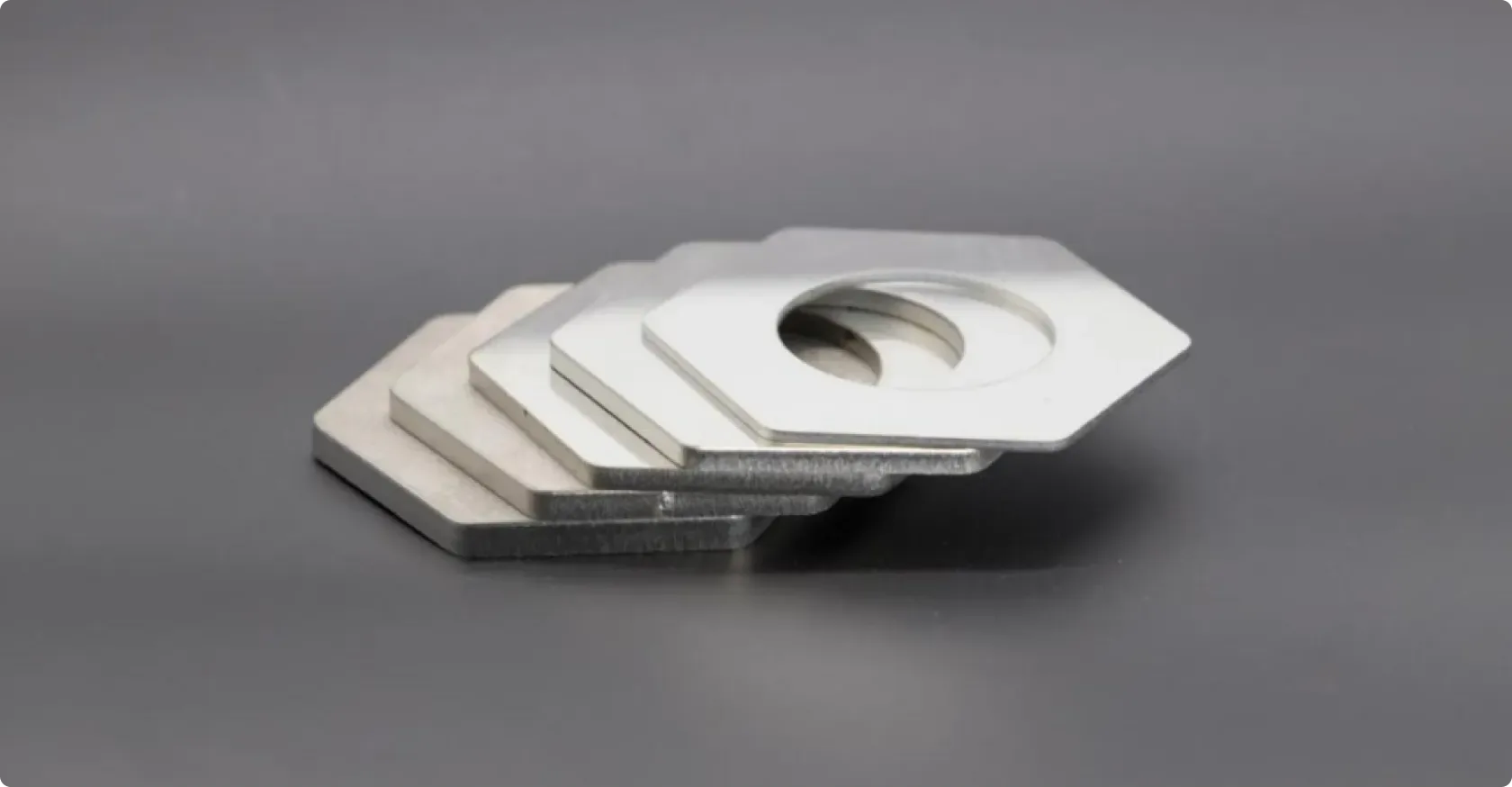
Common Stainless Steel Laser Cutting Defects and Solutions
Despite following proper procedures, laser cutting defects may still occur. Below is a chart summarizing common issues along with their potential causes and recommended solutions:
Laser Cutting Defect | Possible Cause | Solution |
Small, Regular Drip-Shaped Burrs![]() | Focus set too low, Cut speed too high | Increase the focus height, Decrease cutting speed |
Long Irregular Filamentous Burrs on Both Sides & Surface Color Changes on Large Plates![]() | Cutting speed too low, Focus set too high, Insufficient pressure, Material overheated | Increase cutting speed, Decrease focus, Increase pressure, Allow material to cool |
Long Irregular Burrs Appearing Only on One Side![]() | Laser beam not coaxial with the nozzle, Focus set too high, Insufficient pressure, Cutting speed too low | Adjust the laser beam alignment, Lower the focus, Increase gas pressure, Increase cutting speed |
Yellowed Cut Edges | Nitrogen has oxygen impurities | Use higher-purity nitrogen with less oxygen contamination |
Beam Divergence from Laser Head | Acceleration too high, Focus set too low, Molten material not adequately removed | Lower acceleration, Increase focus, Ensure proper material ejection |
Rough Cut Edges | Nozzle damaged, Lenses are contaminated or dirty | Replace the nozzle, Clean or replace the lenses |
Material Ejected from the Top![]() | Laser power too low, Cutting speed too high, Gas pressure too high | Increase laser power, Reduce cutting speed, Lower gas pressure |
Choosing the Right Laser Cutting Machine
Achieving best cutting results also requires selecting the right tool. KRRASS high-performance laser cutting machines can deliver exceptional cutting precision and efficiency, enabling you to achieve superior results with minimal effort.
By following the best practices outlined in this guide and equipping your facility with KRRASS's advanced laser cutting machines, you can significantly improve your stainless-steel cutting processes and product quality.
Should you need any aid, the KRRASS 24/7 Online Service Team is ready to provide support and technical guidance to help you perfect your laser cutting operations. Contact us today for more information and to receive the best solutions tailored to your needs.