Laser cutting is a fundamental application technology in the laser processing industry and one of the most widely used methods for metal processing. Due to its significant advantages, such as high precision, speed, simplicity in operation, and automation, laser cutting has become the preferred choice in various industries, including automotive manufacturing, aerospace, shipbuilding, railway equipment, industrial automation, national defense, building materials, and more. To maximize these benefits and avoid common cutting defects, laser cutting quality improvement solutions are essential for enhancing cutting performance and keeping high-quality standards.
Laser cutting plays a pivotal role in maximizing productivity and reducing costs, which helps manufacturers not only improve efficiency but also build trust with their clients. When manufacturers look to employ laser cutting for producing metal parts—either for their own production or on behalf of clients—achieving high cutting speeds, stable operation, and cost-effective performance are of utmost importance. However, in real-world applications, operators often face specific quality defects that hinder the full potential of the cutting process, which in turn affects the results they can deliver.
At KRRASS, who have spent years solving technical problems for laser cutting machine users, we’ve compiled a list of 10 common laser metal cutting quality defects, along with their causes and proven solutions. Understanding and addressing these defects ensures manufacturers can achieve best cutting performance and keep high-quality standards. Here’s a detailed breakdown of these common issues and how you can overcome them with the right technology, such as the latest fiber laser cutting machines.
Laser Cutting Quality Improvement Solutions Case Study:
1. Uneven Cutting Quality at One Side of the Edge
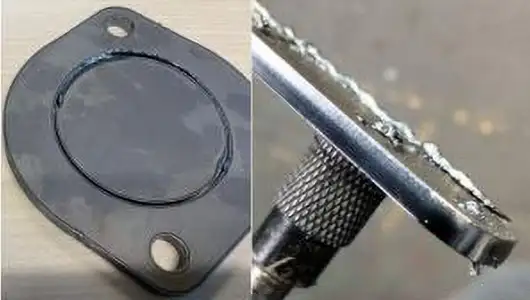
Cause: Misalignment of the laser beam to the lens, blockage or irregularity in the nozzle, improper laser path cleanliness, or the laser head being non-vertical compared to the material.
Solution: Regularly check and center the laser beam, inspect and clean the nozzle, ensure the laser head is properly aligned, and keep lens cleanliness for best cutting performance.
2. Kerf Too Wide
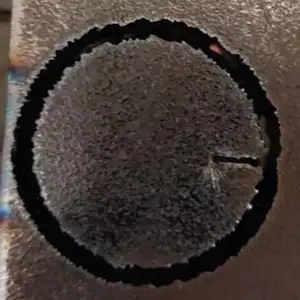
Cause: Excessive gas pressure, focus height being too high, too much laser power, or poor material quality.
Solution: Reduce gas pressure incrementally by 0.1 bar, lower the focus height by 0.2mm at a time, reduce the laser power, and ensure the material surface is free from contaminants for cleaner cuts.
3. Burnt Corners
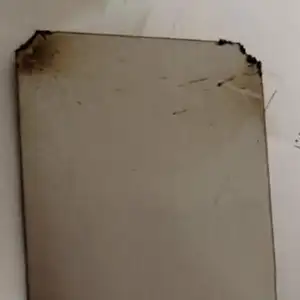
Cause: Overheating at the corners during the cutting process.
Solution: Implement a power curve or cooling points to better regulate the energy distribution and minimize overheating in critical areas of the cut.
4. Rough Sections Only on the Lower Edge
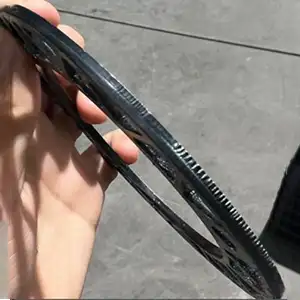
Cause: High gas pressure or insufficient focus height.
Solution: Lower the gas pressure and adjust the focus height to a best level for smoother, cleaner cuts on both the top and bottom of the material.
5. Excessively Rough Striations at the Cutting Edge
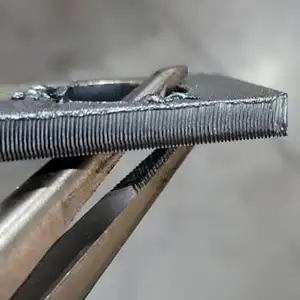
Cause: High gas pressure, excessive focus height, slow cutting speed, or a dirty/damaged lens.
Solution: Lower the gas pressure, adjust the focus height for better precision, increase the cutting speed to perfect material flow, and inspect the lens for cleanliness or damage to ensure sharp and precise cuts.
6. Soft Slag Residue on the Lower Surface
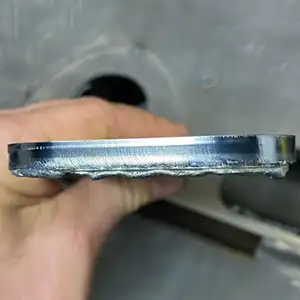
Cause: Cutting speed being too fast, focus height being too high, or gas pressure being too high.
Solution: Slow down the cutting speed, adjust the focus height for better cut quality, and lower the gas pressure to prevent slag formation on the underside of the material.
7. Coating Peel-Off at the Lower Edge
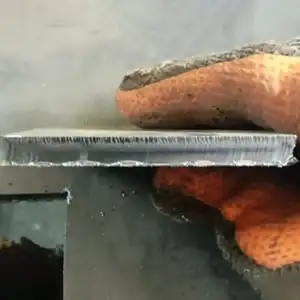
Cause: High gas pressure, insufficient focus height, or overly fast cutting speed.
Solution: Reduce both gas pressure and cutting speed, while increasing the focus height to keep a stable cutting environment that preserves coatings on the material.
8. Hard Slag at the Lower Surface of Stainless Steel

Cause: Excessive focus height, low gas pressure, or improper cutting height.
Solution: Lower the focus height, increase the gas pressure for better material flow, and adjust the cutting height to achieve a smoother and more precise cut with minimal slag.
9. Abnormal Edge Color
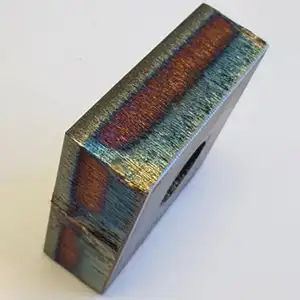
Cause: The nitrogen gas used for cutting is not pure.
Solution: Switch to a higher purity nitrogen gas supply to avoid contamination and achieve cleaner, more consistent edge coloring.
10. Abnormal Defects at the Starting Cutting Point
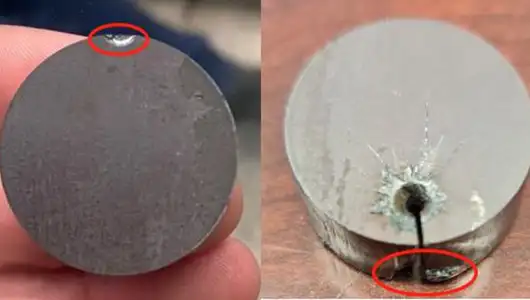
Cause: Incorrect settings for laser on/off delay or improper cutting lead-in.
Solution: Change the lead-in path to avoid defects and adjust the laser on/off delay settings to ensure a smoother, defect-free start to the cut.
Conclusion: Achieving Efficient and High-Quality Laser Cutting
For manufacturers in the metal fabrication and manufacturing industries, it is crucial to avoid common defects that can disrupt the laser cutting process and ultimately impact productivity. With the right equipment, regular maintenance, and fine-tuning, these defects can be minimized or completely avoided. One key to achieving this is selecting a stable, high-quality, and efficient laser cutting machine from a trusted manufacturer.
Fiber laser cutting machines, with their exceptional precision, fast cutting speeds, and improved performance, are ideal for addressing these issues. At [Your Company Name], we specialize in providing innovative fiber laser technology that ensures best cutting performance, reliability, and long-term savings. Our machines are designed to minimize the occurrence of common defects, offering manufacturers a cost-effective and high-quality solution that boosts both efficiency and customer satisfaction.
With our fiber laser cutting machines, you can ensure your production processes stay smooth, defect-free, and profitable. Ready to take your laser cutting to the next level? Contact us today to learn more about our advanced solutions and how we can help you achieve the best possible results in your metal cutting operations.