The operation of a fiber laser cutting machine involves a variety of cutting processes, with micro-joints playing a critical role in ensuring the stability and precision of each cut. Micro-joint technology is designed to address issues related to workpiece support, stability, and potential deformation during the laser cutting process. By using innovative micro-joint functions, we can minimize issues such as material warping, collision risks, and unnecessary downtime, significantly improving the overall performance of the laser cutting system.
Table of Contents
Cutting Challenges and Nano Joint Solutions
When using a fiber laser cutting machine, workpieces are typically supported by knife blade tables or similar supporting structures. However, certain challenges may arise during the cutting process. Specifically, some cutting parts may not be small enough to fall through the gaps of the support blades, while others may not be large enough to be securely supported. These scenarios can lead to imbalances in the workpieces, causing them to tilt or shift. If the parts lose their balance, the high-speed movement of the laser head may result in collisions with the workpiece, leading to potential damage or, at best, machine stoppages.
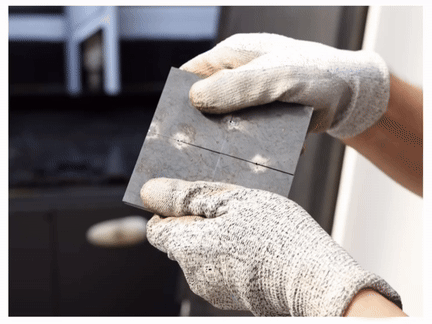
To address these issues, KRRASS introduces a series of micro-joint solutions designed to effectively prevent imbalances and collisions, thereby enhancing the overall cutting efficiency, accuracy, and safety of the operation. We offer three distinct types of micro-joint options: Simple Micro-Joint, High-Speed Micro-Joint, and Traceless Nano Joint. Each type has been customized for different cutting requirements, offering varied benefits in terms of speed, surface quality, and material efficiency.
1. Simple Micro-Joint
The Simple Micro-Joint is an easy-to-use micro-joint function that disconnects the cutting contour at several points, ensuring the parts stay attached to the surrounding material after the cutting process. This simple technique prevents smaller parts from falling off the material and ensures that the workpieces stay properly supported throughout the operation.
Advantages:
- User-friendly: The simple micro-joint is straightforward to implement in programming and offers a reliable solution for most workpieces.
- Versatile: Suitable for a wide range of materials and cutting applications.
Disadvantages:
- Reduced Cutting Speed: Adding micro-joints may slightly slow down the cutting process, as the machine needs to execute added movements to implement the joints.
- Surface Quality: The cut edges may show visible laser piercing marks, making this choice less suitable for applications requiring high-quality surface finishes.
2. High-Speed Micro-Joint
The High-Speed Micro-Joint is an enhanced version of the Simple Micro-Joint, specifically designed for cutting thin sheets. Unlike the Simple Micro-Joint, this method allows the laser to temporarily stop at the micro-joint point, while the cutting head continues to move at full speed without any interruption. Once the laser reaches the micro-joint breakpoint, the laser output automatically stops and resumes once the head has moved past the joint.
Advantages:
- Uninterrupted Speed: The high-speed micro-joint does not affect the overall cutting speed, as the laser head continues to move without slowing down, ensuring efficient cutting.
- Ideal for Thin Sheets: This method is particularly effective for cutting thinner materials, as it does not interfere with the cutting speed.
Disadvantages:
- Limited Material Thickness: This technique is not suitable for cutting thicker plates, as the laser is turned off and on during the process, and thicker materials may require pre-piercing to ease cutting.
3. Traceless Nano Joint
The Traceless Nano Joint is the most advanced micro-joint technology. Unlike traditional methods, the Traceless Nano Joint uses a laser to cut through the material without completely penetrating the sheet. This method does not require the laser to pause or slow down at the joint, ensuring continuous operation without interruption. The cutting process is both faster and more efficient, making it a highly cost-effective solution.
Features and Advantages:
- Improved Cutting Efficiency: With no need to pause or re-punch the material at the joint, the Traceless Nano Joint allows for faster and more continuous cutting, resulting in reduced time and energy consumption.
- Enhanced Material Utilization: The small size of the joints allows for tighter nesting in the layout, which maximizes the usage of material and reduces waste.
- Smooth and Traceless Surface: The surface at the joint is left smooth and without visible marks, making it easier for post-processing and polishing. This is particularly beneficial for customers with high surface quality demands.
- No Need for Piercing: The process cuts the need for piercing during cutting, which reduces added material usage and enhances cost savings.
Additional Benefits:
- Cost and Time Efficiency: By reducing the need for pausing and re-piercing, the Traceless Nano Joint minimizes downtime, electricity consumption, and material costs.
- Better Nesting Software Integration: The use of Traceless Nano Joints makes the laser cutting process compatible with advanced nesting software, easing more efficient layout planning and material usage.
Notice:
- System Requirements: To fully use the Traceless Nano Joint function, a System bus is needed. Currently, all KRRASS laser cutting machines are equipped with a bus-type system, ensuring that our customers can take full advantage of this innovative technology.
Conclusion
KRRASS provides innovative solutions for the fiber laser cutting industry, and our innovative micro-joint technologies, including the Traceless Nano Joint, offer clear advantages in terms of efficiency, material use, and surface quality. For customers looking to achieve high precision, reduced downtime, and cost savings, the Traceless Nano Joint is the ideal choice.
If you are interested in learning more about how our advanced laser cutting solutions can help your operations, don’t hesitate to contact KRRASS for detailed information and personalized support.